Coloplast Case Study
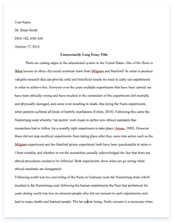
- Pages: 4
- Word count: 871
- Category: Case Study Knowledge Language
A limited time offer! Get a custom sample essay written according to your requirements urgent 3h delivery guaranteed
Order NowColoplast, an international company that specializes in developing, manufacturing, and marketing medical devices, implemented an off-shoring strategy in order to stay viable, competitive and keep in focus the dynamic market needs. Implementing this strategy has brought some issues that were unexpected for Coloplast. One of the issues was with the organizational structure. Coloplast’s off shoring involved moving operations to Hungary. They would be operating with Danish and Hungarian production plants, where production processes were not the same. Misunderstandings and miscommunication arose amongst employees and created managerial and operational challenges.
Another issue that arose was knowledge management and this became a problem since there was very limited documentation on inconsistencies in equipment operation as well as no proper standardization of systems in place. The solution to these problems is to implement company wide processes that help standardize both Hungarian and Danish plants. Employee motivation and communication is another issue and this is attributable to the resistance to change which many employees face. Coloplast didn’t look at these issues with offshoring as their costs were rising locally and they needed to mitigate that cost. Another solution is Coloplast expanding to China where labour is even cheaper than Hungary.
Issue Identification
One of the issues faced was that of the interdependent relationship between the Danish and the Hungarians. There were operational assumptions and activities. Nobody factored in how significant the language barrier would be. It proved to be a significant enough factor that it warranted unexpected time and money to rectify the problems Coloplast faced. There was a lack of knowledge transfer from the Danish operators to the Hungarian operators and this resulted in operational inefficiencies. The other issue involved the human resource aspects such as limiting attrition rates, limiting social hardship, and transferring knowledge effectively.
Environmental and Root Cause Analysis
Although Coloplast saw the need to offshore or outsource, their decision was based on them trying to focus on their core business and to increase efficiency, the prime motive was to cut costs. They chose to offshore as this entailed lower cost and availability of skilling workers. They did not want to rely on third parties, and third parties lack Ithe in house knowledge needed for Coloplast’s operation. Coloplast was seriously considering relocating to a low cost location for some time. They were in danger of certain factors such as reimbursement, policy changes, price pressures due to wholesaler concentration, and powerful insurance companies. Their establishment in Hungary was due to the significant savings in production costs, which were 20 percent less than Danish levels.
After they had factored in wage increases, Coloplast was convinced this offshore move would be financially advantageous in the long run. Building costs were 50% less in Hungary than Denmark. Cost considerations were an issue, but logistical considerations were weighed to be more important. Large regional differences existed within Hungary in terms of wage and infrastructure. Coloplast was located on the attractive side of Hungary and other major companies were close by, which played a part in their decision to off shore. Although the relocation of operations involved mature product lines, the decentralized structure still made documenting planning and production systems difficult. The operations at the Danish site were not standardized, thus making it harder to offshore to Hungary, where they had their own operations.
Alternatives or Options
Expand in Europe. Many locations were scouted before Hungary was implemented, and there are several Eastern Bloc countries with low wage, and production costs. However, there is more risk in operating in one of these countries as the geopolitical implications in these countries can cause cost savings to be eroded.
Recommendation and Implementation
Relocate to china. Now that Coloplast has realized it’s deficiencies in their process with the offshoring to Hungary, they can mitigate these for the future in their relocation to China. The whole initial decision to offshore in the first place was to reduce cost. Hungary was less costly than Denmark, and China is less costly than Hungary. It makes business sense to relocate to China production wise as the wages are significantly lower than the Danish and Hungarians. There are organizational challenges in this implementation in that the geographical distance between Denmark and Hungary can amplify many of the scenarios that arose from their offshoring to Hungary. Their knowledge transfer must be coordinated well in advance with any offshore implementation. They must establish well set corporate guidelines on how to relocate and manage production sites in advance of any physical offshoring move. They must learn from the mistakes identified with their previous project. They must also apply the best practices from Hungary and include the idiosyncrasies of the Chinese business environment.
Monitor and Control
Pilot production phase
– R&D, design and marketing
Ram-up phase
– resources of in building and fine-tuning
machinery
Volume production phases
Range care
Function for plant conjunction
primary support functions
– quality, engineering, maintenance, planning and logistics.
Secondary support functions
– information technology
(IT), facility management and accounting
Competitor Environment
Firm’s resources Cont
Managerial resources
save 66% if Coloplast Hungary buy directly from Hungarian
producer
Knowledge
– tackle operational inconsistencies in the machinery
Adhesives technology
– important resource of manufacturing
Production planning systems
each production units has its own unique production planning systems.
Programmable logic controllers (PLCs)
control and manage automatic production machines
Human resources