Caterpillar Case Study
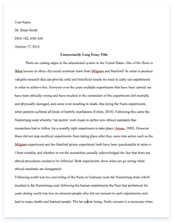
- Pages: 2
- Word count: 343
- Category: Case Study Globalisation Industry
A limited time offer! Get a custom sample essay written according to your requirements urgent 3h delivery guaranteed
Order Now1. If you are Mr. Folley, looking over the devastation at the Oxford plant, what do you do to keep Caterpillar’s worldwide production running?
To keep production running, Mr. Folley needs to quickly “re-route” the supply chain from his facility and disperse those demands to other locations. Because the Oxford plant is the only one owned by Caterpillar that produces these couplings, he needs to find outside sources that can produce the couplings to Caterpillar’s standard and get them contracted and trained so they can get couplings to the manufacturing plants and keep production running while Caterpillar rebuilds the Oxford plant. While other plants are gearing up to produce the couplings, Caterpillar needs to begin “cross-distributing” whatever couplings are on hand between manufacturing plants. Due to JIT practices there is most likely not many couplings available so contracting the outside sources needs to happen fast.
Mr. Folley needs to begin cleanup of the plant and reconstruction now. He needs to assess the amount of damage to the metal-stamping machines and develop an accurate estimate of how long it will take before Caterpillar can begin producing its own couplings again.
2. Given the inherent risk in JIT and the trauma that the companies have experienced, why has JIT survived?
But what makes JIT such a high risk supply method is that it can cause devastating losses if production halts. The trade-off is that JIT is such a lean method of supply that it not only reduces cost to the company by eliminating inventory to store and maintain, but it also saves by minimizing waste caused by overproduction. JIT create a more simple practice of quality control. JIT forces a company to focus on production and as a result creates a more efficient and better quality throughput in a production line. It allows a more fluid approach to production which minimizes the costs of redesign (whether it be a product or a process).
3. What do these experiences, and the continuing popularity of JIT, tell you about just-in-time?