Toyota Production
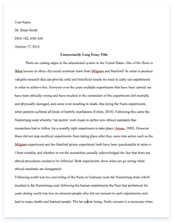
- Pages: 4
- Word count: 822
- Category:
A limited time offer! Get a custom sample essay written according to your requirements urgent 3h delivery guaranteed
Order NowDoug Friesen is the manager of assembly, for Toyota’s Georgetown, plant. The plant has been experiencing some production problems lately. Too many cars are sitting in the clinic and overflow parking area with numerous seat defects. As Doug, I would focus my ettorts on the root cause ot the problem, 1. why are defected cars slttlng In the cllnlc and overflow areas? seats have numerous defects 2. Why are the seats defected? Numerous issues, from the data and from talking with assembly teams. Why is KFS having issues? The Toyota Production system provides for eliminating waste. Waste can be identified in all manufacturing process.
Quality rises along with Productivity when people learn to identify and eliminate waste. That is because a big part of eliminating waste consists of preventing defects. Defective products entail waste of human resources, equlpment and materials. sy Identltylng waste and ellmlnatlng It, companies can reduce costs. KFS should be contacted to Idenufy exactly why the seats are having problems. TMM and KFS should work closely together to complete a process evaluation to narrow down the possible sources of the defects. TMM also deviated from the Toyota Production System (TPS). The seat problem was not handled correctly.
The TPS calls for building quality into the production process (Jidoka) and strongly condemns any deviation trom value-additions. The seat detects were not being corrected Immediately once they had been detected, they were sent to the clinic and overflow parking area. This violates the TPS, and builds waste into the product and the manufacturing line. By allowing the defective seats to go into the system as defects TMM broke its own rules causing many wastes in the manufacturing process.
In case of the defective seats, the reasons for the exceptions were: a) The final assembly eople already knew ot the problem. ) It was possible to tinisn building the car without seat assemblies c) It was felt that stopping the line was too expensive given how long it took to obtain the replacement seat. In TMM, TPS principles would make any production problems instantly self- evident and stop producing whenever problems were detected. The most important teature ot the Toyota Production System is the way it links all production activity to real demand. Everything that happens In the system happens In the name of  system.
The seat set was the most expensive of all the purchased parts.. TMMs sole seat supplier was Kentucky Framed Seat. KFS), which teamed up well with TMMs operations until TMM increased seat styles. The hook breakage problem reported by one of the group leaders might also be an issue with the assembly process. The processes needing improvement should be identified and more data should be gathered about the problems by interviewing the personnel in details. The data should then be analyzed in order to fgure out the gaps between the standards and the current outputs. Summary: Doug Friesen should address the problem by focusing on the reasons for allowing uch deviations from TMM’s normal way of handling problems.
He should also look at the communication and organization between KFS and the plant. One issue that he should look at is why these cars were sitting in the clinic and overflow lot for so long. KFS was making special deliveries of new seats to replace the defective seats, but there were still cars with defective seats sitting in overflow lot. The other seat issues that Mr. Friesen should look into are the problems caused by breaking of the hook, and the delivery of the wrong seat by KFS. With this said there seems to be multiple problems that need resolution.
First, The ariations in seat sets and wrong delivery of seat at the wrong time may indicate that the production line needs to more level loaded so that KFS may keep up with demand. A capacity analysis may be helpful in identifying if more manufacturing resources are needed to satisfy demand of the assembly line. Second, there may be an engineering design issue in the breaking of the hook, it may be prudent toget the design department to reviewed the breakage. His attention should be focused on finding the root of the problem. He should go down and watch the team who installs the seats into the cars and see if he sees any problems there.
He should also discuss with those employees and see what they think could be done. He should also consider going over to KFS and watching their production lines to see if he can notice any significant problems. Perhaps KFS is being overworked with the new increase in seat variations and finding another supplier or perhaps expanding their own plant to build seats on their own like other companies. Doug should focus his efforts to find the root of the problem and determine if the solution is feasible. Time needs to be invested to investigate the problem and have the companies work together to figure out the problem and solution.