Seligram Case Study Argumentative
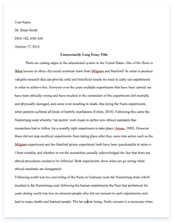
- Pages: 5
- Word count: 1024
- Category: Accounting Case Study
A limited time offer! Get a custom sample essay written according to your requirements urgent 3h delivery guaranteed
Order NowThere are mainly three factors leading to the failure of the existing system at ETO. First, there has been a steady decline in direct labor hours per lots and fewer test lots. Such a decline is mainly due to an increased dependence on vendor certificate, which is a key component of JIT delivery. Number of tests being done by ETO reduces because the suppliers did the testing by themselves. Second, there is a shift from simple inspection services to broader-based test technology. Although ETO provides engineering supports on complex parts, outside testing services are even cheaper, esp. on large lots when only elementary testing is required. Lastly, the existing testing equipment is getting out-dated and is unable to cope with the pace with new developments in high-technology components. Also, the very expensive highly automated equipment is required to test the new high-technology components. That equipment provides longer test cycles and more test data per part. Such an increased automation would reduce direct labor needed to absorb depreciation costs for ETO.
Charges for testing go up due to an increase in burden rates. Therefore, ETO notices that the number and frequency of complaints from the customers are amplified.
Question 2
The Reported Cost of 5 Components under the Existing System
ProductDLBurden=DL*Burden RateAllocated Overhead
ICA$917$917*1.452246.65
ICB20512051*1.455024.95
Capacitor10941094*1.452680.3
Amplifier525525*1.451286.25
Diode519519*1.451271.55
Total:12509.7
The Reported Costs of the 5 Components under the System proposed by the Accounting Manager (Two-Cost Pool)
ProductDirect Labor $DL $ RateMachine HourMachine Hour RateAllocated Overhead
IC A9171100.418.514802580.4
IC B 20512461.24032005661.2
Capaciter10941312.87.56001912.8
Amplifier52563054001030
Diode519622.8129601582.8
Total12767.2
Reported costs of the five components described in the system proposed by the consultant
ProductDL DL rate * 0.2Main Test * 63.34Mech. Test * 112.63TOTAL
IC A917183.4538.391126.32765.09
IC B2051410.2886.762928.396276.34
CAP.1094218.8190.02506.8532009.673
AMP.525105253.36112.63995.99
DIO.519103.8443.38563.151629.33
Total13676.423
As for the comparison of the 3 methods used, the first method, the existing one, would relatively bias against jobs with high direct labor cost but low machine hours. But for the second method, the one proposed by the accounting manager, penalizes jobs with relatively more main machine hours than mechanical machine hours. The third method, the one proposed by the consultant, is relatively the best among the three as it divides direct labor cost from the machine cost(Main-Test Room and Mechanical Test Room), which makes more sense and more fair, yielding a more accurate estimate. The downside of it, thou, is that this method would increase the total cost
As for recommendation, we would suggest the company to allocate their cost according to the real usage of the material. With the cost being driven by the consumption of the resources, the production capacity is likely to be at it’s fullest as it utilizes the resources more efficiently. It also has a higher chance of calculating the true cost of a product which would lead to better management decision.
Question 3:
Under the existing system, whether the manufacturing division of Seligram should be required to purchase their testing from ETO depends on the simplicity/ complexity of the inspection services. Since “low technology” outside laboratories is often cheaper, especially on large lots, the division should be required to purchase the testing from outside services. On the other side, since “complex parts” require sophisticated engineering resources in which ETO has its competitive advantage in doing that. Therefore, ETO could provide cheaper, rapid and cost-effective engineering services, the divisions should purchase their testing from ETO. Moreover, the existing accounting system may benefit these “complex parts” by allocating comparatively low manufacturing overhead of ETO to those complex parts.
Under the new cost accounting systems, the divisions should purchase their testing for both low and high technology parts from ETO. Implementing two- and three-burden-pool systems utilize separate burden centers for accounting could allocate the burden costs based on machine hours and rate per direct labor dollar. Both of the new systems are more reasonable and relevant than the existing one in terms of burden costs on machine and direct labor. Although the allocating cost for the “complex parts” would have a comparatively higher burden of overhead allocation than that of the original accounting system, this higher percentage of allocation would truly reflect their cost of inspection. Therefore, it would allow managers to make better decision since the allocation of overhead cost is more reasonable and relevant.
Question 4
If we include the new machine in the main test, the new Main test’s burden rate:
= [Original burden + (First year Depreciation cost + Engineering requirements + Estimated overhead)] / (original machine hour + new machine utilization)
= 2103116+(500000+75000+250000) = 2928116
= 2928116 / (33201+400) = 87.14
The cost allocation would be as follows:
@DLDL Rate * 0.2 Main Test * 87.14Mech Test * 112.63Total
ICA917183.4740.691126.32967.39
ICB2051410.21219.962928.386609.54
CAP.1094218.8261.42506.8532081.073
AMP.525105348.56112.631091.19
DIO.519103.8609.98563.151795.93
Total @ @ @ @14545.123
The above method simply multiplies the original main test machine hours by the new main test burden rate. However, not all the jobs would use this new machine. Besides, the “machine hours” of the main room assigned to the above products would be different from those of the new machines. Thus, this method over simplified the situation by allocating the cost according to the original machine hours.
To tackle this issue, we could treat the new machine as a separate cost center. In this scenario, we would only utilize 10% of the new machine. Therefore, the total 1st year hours of the new machine utilization would be equal to 4000hrs*10%. The burden rate assigned to the products would be calculated as follows:
(First year Depreciation cost + Engineering requirements + Estimated overhead)/total hours*utilization percentage
$825,000 / (4000hr*10%) = $2062.5 per hour
The new machine’s burden rate would be allocated according to the jobs which actually use it. In other words, we only allocate the cost of machine to the relevant jobs. As a result, the cost allocation would be based on the relevant activities and could be more reliable.