Additive Manufacturing
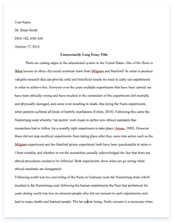
- Pages: 7
- Word count: 1579
- Category: College Example
A limited time offer! Get a custom sample essay written according to your requirements urgent 3h delivery guaranteed
Order NowAdditive manufacturing is method for producing three dimensional objects irrespective of their shape or geometry. Normally, manufacturing method involves processes like cutting shearing and forming. But additive manufacturing involves a different way of joining the materials together to form the object.
Aspects over Conventional Manufacturing
Additive manufacturing has ability of greater design. This means complex assemblies can be printed in one process which makes the manufacturing process simple. Many of the constraints using traditional manufacturing are reduced.
Usually tooling is a great barrier in production processes because of their high cost. But in additive manufacturing tooling requirement can be fully eliminated.
Additive manufacturing can be done in anyplace. The data file of the object to be printed can be sent digitally and can also be manufactured in homes. This reduces the transport requirement.
Traditional manufacturing process always has some geometrical limitations and is a time-consuming process. But additive manufacturing is a fast process and complex parts are also easily made.
Machines are very compact and the resources required are very less compared to conventional manufacturing machine. Skilled labour is a mandatory requirement in conventional manufacturing, which is eliminated in additive manufacturing.
Customizing is another advantageous option in additive manufacturing. Parts can be modified according to the personal requirements. E.g.: Medical sector
Overproduction of parts can be stopped due to manufacture of exact demand requirement. This improves the efficient usage of the material.
The risk and cost of manufacturing can be minimized in additive manufacturing methods. A major benefit of additive manufacturing process is the reduction of development time (from concept to final product) of the object.
There are two materials used in additive manufacturing process the powder and the support material. Both materials can be mostly recycled and reused improving material efficiency.
Additive manufacturing is environmental beneficiary because it can be done anywhere, reducing the emission of gases due to transport.
Now a days 3D printing machines are widely used and they are cost effective but the injection moulding machines are still expensive.
- Categories of Additive Manufacturing
- There are seven categories in additive manufacturing. They are
- VAT PhotopolymerisationMaterial Jetting
- Material Extrusion
- Powder Bed Fusion
- Sheet Lamination
- Directed Energy Deposition
- Binder Jetting
VAT PhotopolymerisationVAT photopolymerisation is an additive manufacturing technique which uses UV rays to cure and harden the resin. A vat of liquid polymer is the resin used in this process. The object is manufactured layer by layer. The UV rays fall over the resin and hardens it. Once the resin is hardened the platform is lowered further to harden the resin to manufacture the rest of the part.
During the process, material has no support because it uses liquid resin to form the part. If it is a powder based method, the unbound powder acts as the support material. In case of VAT photopolymerization, support structure is always needed.
Fig 1: VAT Polymerization process
Material Jetting
Material jetting works in a similar way to a 2D ink jet printer. Two materials are used in this process i.e.) Build material and support material. These materials are jetted onto the build platform continuously or by drop on demand approach.
When these materials are jetted on the build platform, they are solidified and the part is made layer by layer. The nozzle moves horizontally across the build platform and the material is deposited from it. Then UV (Ultra Violet) rays are used to cure the deposited material and harden them. The number of materials to be used in this method is confined because they are deposited in drops. So, highly viscous materials which can form drops easily are commonly used (Polymers and waxes).
Fig 2: Material Jetting Process
Material Extrusion
Material extrusion is one of the most commonly used additive manufacturing technique. The well-known process in this technique is Fused deposition modelling(FDM). The spooled material is extruded through a heated nozzle which is mounted on a movable arm. The material is deposited layer by layer and the platform moves vertically to add more material to form the object. The material solidifies as it cools. Variety of plastics can be used in this process.
Material extrusion process is fast and inexpensive. There is always a problem of hardening the part. So, constant pressure and temperature must be maintained to get good quality parts.
Fig 3: Material Extrusion Process
Powder Bed Fusion
The Powder Bed Fusion process includes the following commonly used printing techniques: Direct metal laser sintering (DMLS), Electron beam melting (EBM), Selective heat sintering (SHS), Selective laser melting (SLM), Selective laser sintering (SLS), and laser engineered net shaping(LENS) . Laser beam or electron beam is used in this process to fuse the powder material together and the object is formed. There is no support material needed for this process because the powder acts as the support material.
- In Selective laser sintering(SLS) laser beam is used to sinter the powdered material together and form a solid object.
- In Selective laser melting(SLM) the material is fully melted by passing laser beam and they are bound together.
- Direct metal laser sintering(DMLS) is the same process as Selective laser sintering(SLS) but metal powder is used instead of plastic powder.
- In Electron beam melting(EBM) vacuum is required and powdered layers are fused together by passing an electron beam.
- Selective heat sintering(SHS) is different from other Powder fusion processes. It uses a heated thermal print head to bind the powder material together.
Fig 4: Powder Bed Fusion Process
Sheet Lamination
There are two types of techniques in this process namely Ultrasonic additive manufacturing(UAM) and Laminated object manufacturing(LOM). Commonly used material for this process is sheet metal (copper, aluminium, stainless steel, titanium).
In Ultrasonic additive manufacturing(UAM) the sheet metal is cut and assembled like ribbons and they are welded together by ultrasonic welding. There will be often some unbound metal formed in this process and they are removed by additional CNC machining processes.
In Laminated object manufacturing(LOM) commonly used material is paper and plastic. A sheet of material (paper or plastic) is fed and the laser cuts the material. A heating roller fuses the material together which are cut and arranged layer by layer.
Fig 5: Sheet lamination Process
Directed Energy Deposition
Directed energy deposition is a process in which the objects are formed by melting the material. The material can be either wire or powder (polymers, ceramics, mostly metals). The material can be deposited at any angle because the nozzle is mounted on a four or five axis arm and laser or electron beam is passed to melt the material.
Besides manufacturing the parts, the main purpose of this process is to repair and coat existing parts. Although it also has some drawbacks like high cost of the equipment and lack of accuracy.
Fig 6: Direct Energy Deposition Process
Binder Jetting IntroductionBinder jetting process is another additive manufacturing process and is similar to traditional paper printing method. The binder material acts like ink when it moves over the layer of powder and forms the final product. This process is considered as the best 3D printing process because it can produce solid layers and can print very large objects i.e.) room sized architectural objects.
Fig 7: Binder jetting process
Binder Jetting Process
- The powder material is distributed over the powder bed using the powder roller.
- The inkjet printhead consists a number of nozzles and it drops binder adhesive material on the top of the powder.
- This adhesive material fuses the powder together to form the solid object.
- Another layer is formed by lowering the build platform. The roller moves to and fro to spread the next layer of powder.
- The powder which is unbounded prevails in the box surrounding the object. This unbounded powder acts as the supporting material.
- This technique is reiterated till the entire 3D object is made.
Uniqueness of Binder jetting over other AM process
Many of the manufacturing techniques build parts through welding or melting process, laser or melted material to fuse the material together. So, a build plate will be required for these processes to maintain the stability of the part. This eventually leads to usage of more material also increasing the manufacturing time for these processes. In Binder Jetting process the parts are supported by the loose powder (left out powder without binding) in the job box. Thus, eliminates the requirement for a build plate.
Spreading speeds for Binder Jetting continue to significantly outperform other processes. Binder Jetting can print large parts and is often more cost-effective than other additive manufacturing methods. Another unique character of Binder Jetting process is that it does not handle heat during the manufacturing process. Other manufacturing technique use heat source which can cause stress in the formed part. These stresses must be eliminated using another post processing operations.
Advantages
3D parts can be made in different colours.
Binder Jetting works with almost any material that is available in powder formBinder Jetting works with almost any material that is available in powder formBinder
Jetting works with almost any material that is available in powder formBinder jetting works with almost every material available in powder form . Mostly metal, polymers and ceramics.
Binder jetting is faster compared to other additive manufacturing processes.
Variety of binder material and powder combinations is possible in this process. Hence,3D objects with different mechanical properties can be made.
Disadvantages
- Due to high speed process, surface finishing process is mostly required.
- This is a binding process and the material is glued together making the objects fragile.
References
- Dhanesh Avinash Dhanawade, Bhatwadekar S.G., “A Review on Types of Powder Bed Fusion Process In Additive Manufacturing Technology” Mechanical department, Sanjay Ghodawat University, Kolhapur, India
- EXone Digital Part materialization, ‘What is binder jetting?’
- Additively AG 2018, ‘Binder Jetting(BJ)’
- Additively AG 2018, ‘Stereolithography(SL)’
- Additively AG 2018, ‘Material Jetting(MJ)’
- Additively AG 2018, ‘Fused Deposition Modelling(FDM)’