Otto’s Consulting Report
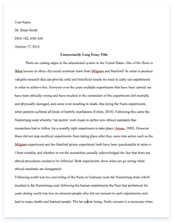
- Pages: 9
- Word count: 2152
- Category:
A limited time offer! Get a custom sample essay written according to your requirements urgent 3h delivery guaranteed
Order NowHansen Consulting proudly presents the following statistical information for Otto’s Auto parts. Statistics is a branch of mathematics that makes it possible for you to gain an edge over your competitors by providing a method for collection of data, and a way to summarize and quantify it to represent real world observations from which predictions can be made. Statistics also includes stochastic modeling, which is a powerful tool that incorporates random variables to predict future outcomes. For decades insurance companies have successfully profited from using stochastic modeling for making predictions of unknown entities. Stochastic models can be run hundreds or even thousands of times to show the likelihood of which outcomes are likely to occur, based on different managerial decisions, and what their expected ranges are in the long run. We will discuss stochastic modeling in further detail later.
We have prepared an in depth report for your consideration. Our report includes a tool crib staffing analysis, an inventory simulation for the manufacture of your catalytic converters, an employee profile concerning age and gender, profit-ability analysis for handheld computers, and an accuracy test of your current personal screening tests. Some of the challenges you are currently faced with in the “Tool Crib” at your Pierre manufacturing facility are similar to the problems Chrysler dealt with when Lee Iacocca asked Hansen Consulting to help put them on the path to profitability in 1979. For your consideration, we have analyzed your tool crib system using the patented Wedel Queuing Analysis Software, to assist you in determining the optimal number of employees to run your Pierre tool crib.
TOOL CRIB STAFFING ANALYSIS
The Patented Wedel Queuing software is derived from queuing theory, where predictions can be made for fabrication & assembly worker time spent waiting in line, and their arrival times, in relation to a varying number of tool crib servers (workers). In essence, queuing theory provides the tools necessary to analyze and understand the relationship between congestion and service delays caused from waiting in line. Our queuing analysis for the tool crib demonstrates the balance between server idle time (tool crib workers), versus customer costs (total time for fabrication & assembly workers to check out tools or to return tools). As server idle time increases, customer costs decreases, and the total cost also decreases until the optimal number of servers is reached. After the optimal number of servers is reached, the total cost begins to increase. Based on our analysis, the expected optimal cost saving balance is achieved when there are 8 workers manning the tool crib. We have included the costs for having 6 – 10 servers, in the table located below, to demonstrate cost comparisons for your consideration.
TOOL CRIB COSTS
SERVERS| SERVERIDLE TIME| SERVER COST (cost/hour)| CUSTOMER COST (cost/hour)| TOTAL COST (cost/hour)| 6| 11.1%| $168| $361| $529|
7| 23.8%| $196| $217| $413|
8| 33.3%| $224| $189| $412|
9| 40.7%| $252| $179| $431|
10| 46.7%| $280| $176| $456|
INVENTORY SIMULATION
Simulation is a method of creating a model system to imitate the operation of a real system over time. To create a model system, random numbers are chosen to mimic future unknowns, such as delivery times for orders, and project completion times, or product demand. Simulation models have been used to predict expected numbers of passengers for commuter airlines flights, or construction completion dates for track home developers, and for estimating optimal inventory levels at pharmacies, to name a few examples. Simulations become powerful tools for predicting expected outcomes when they are run hundreds or even thousands of times to reveal a “long run average”. For example: if you simulate the flipping of a coin 300 times, the long run average will be close to 50% heads and 50% tails. Likewise, if you simulate only 10 flips of a coin the outcome could vary greatly from the true long run average. The long run average, or law of large numbers, makes it possible for owners and managers to better visualize how optimal strategies can be formulated in order to lower their costs and increase their systems’ performance and effectiveness.
We recently ran a 500-week simulation to determine the optimal order quantity and reorder point for the titanium covers your company purchases and holds, for use in the internal assembly of your catalytic converters. In creating your titanium cover simulation we used random variables to simulate different titanium part demand values and supplier lead times for your manufacturing facility and analyzed the affect they had on your inventory, holding costs, shortage costs, and ordering costs for each week. Our analysis shows that your optimal strategy for order quantity to be 1,000 units, and your optimal reorder point to be 800 units. A 500-week simulation plot for your optimal strategy was generated (located on the next page) to demonstrate that the long run average begins to reveal itself at ~270 weeks. As the plot starts to “flatten out” near ~270 weeks, the long run average shows that your optimal strategy’s expected value is estimated at ~$307.
500 –Week Simulation Plot for Optimal Strategy
Employee profile – Gender
An employee profile was created using descriptive statistics and statistical estimation. Descriptive statistics is a procedure used to summarize and/or describe data, collected from a population or a sample, to make it easier to visualize patterns and interpret data. Descriptive statistics only provides information about the group the data was taken from. Whereas, statistical estimation is used to extend the results from the sample to a larger group in order to make estimates about the population from which the samples were taken. One useful way of summarizing data is through the use of graphs and charts. We created a pie chart (located on the next page) to illustrate an estimated percentage of the workforce that are male and the percentage that are female from a random sampling of 36 factory employees selected by your personnel department for our statistical study.
From the given set of sample data, we calculated that there is a 95% probability that the estimated proportion of the males from the population of 800 factory workers, is between 45% and 77%. This calculation was derived from statistical estimation, and in this case it simply gives you an estimated range of values that is likely to include an unknown population segment (percentage of males). To put it another way, if we conducted 100 different random samplings of 36 workers, 95 of those sampling’s would produce a percentage of the male workers that would fall between 45% and 77%, while the other 5 samplings would be either higher or lower than our calculated values.
Employee profile – age
Descriptive statistics was used to summarize the data collected pertaining to age among the 36 employees that were sampled. The average age (sample mean) among the employees sampled was determined to be 40 years. The median, or halfway point in the series of ages sampled, is 37 years of age. The age that occurred most frequently, called the mode, was 31 years. The measure of the average years dispersed of the sample data from its mean, commonly called the standard deviation, is 14 years. The range of the summarized data is 47 years, which is the difference between the age of the oldest employee and the age of the youngest employee within the sample. There is a 95% probability that the estimated average age is between 33.3 years and 46.7 years. A histogram (located below) was created to show how frequently an age occurs within ~7.8 year intervals located at the bottom of the graph. The height of each bar shows the sum of the number of employees (frequency) that are at that age. The highest frequency measured is 9 employees aged at 34.6 years, while the lowest frequency of employees is shown to be 1 worker aged at 19 years.
Age Range of Employees
HANDHELD COMPUTERS
Next we determined if handheld computers could increase your profits by decreasing the amount of time your factory workers spend manually recording work order information. Handheld computers come at an average cost of 30 cents per hour to acquire and maintain. Therefore, handheld computers must decrease production cost by an average of more than 30 cents an hour for the average factory worker, in order to increase your profits. Your company currently gives each factory worker a performance rating based on speed, quality, and accuracy. From our original sample of 36 factory workers, we used descriptive statistics to determine the group’s average performance rating without computers to be 86 points.
Next, we trained and equipped each of them with a handheld computer, and recorded their new performance ratings for a month and found that the group’s average rating increased to 91 points, an average increase of 5 points. For every average increase of one point, your factory saves 10 cents a point. The break-even point for the additional cost for acquiring and maintaining the handheld computers is therefore determined to be 3 points, which equals 30 cents an hour.
Armed with this data for performance change, we then used hypothesis testing. Hypothesis testing is used to determine what can be proven about a population based upon the sample evidence. In your case, we used this method to prove if computers can increase profits in your factory. By using the breakeven point of 3 points as the baseline for our hypothesis, we determined that the average 5-point increase in performance seen in our sample group would increase your overall profits if handheld computers were given to all factory workers. We estimate that there is a 95% probability that your factory worker performance ratings will increase by a minimum of 3.8 points up to maximum 6.2 points. We calculated the p-value to be .0005. The p-value is a reliable indicator of whether or not our estimate is correct. A p-value equal to or less than .05 is considered to be a significant predictor for your job performance rating values. To put it another way, a p-value of .0005 means that there is a .05% chance that our profitability prediction for using handheld computers is incorrect.
PERSONAL SCREENING TESTS
We were asked to determine the accuracy of using general aptitude (GA) and manual dexterity (MD) tests as screening devices for potential employees. We reviewed the data collected from your sample group of 36 factory workers that showed the performance ratings for each worker and compared them to their point values for GA and MD. This process of comparing is a statistical technique called regression analysis. Regression analysis is a tool used to predict the value of a dependent variable, such as performance, in order to estimate the effect of one or more independent variables (GA, MD), has on the dependent variable. Put another way, does an increase of GA or MD, or GA and MD combined, increase the performance ratings of your employees? The regression showed that there is a positive correlation between both GA, and MD.
A positive correlation means that a relationship exists between two variables, such that, when one variable increases or decreases, the other variable increases or decreases, respectively. As worker GA and MD increased, so did their performance rating. This relationship can be presented in the form of what is called a regression equation. The regression equation produced from our analysis can be used to predict the future performance of potential employees and is as follows:
Y = 48 + .255 (GA) – .069(MD), Where Y = performance.
The average factory employee has a GA score of 203, and an average MD score of 132. In determining the performance values for the average factory worker, these values were plugged into the regression equation as follows:
Performance = 48 + .255 (203) – .069(132) = 91 (rounded to the nearest one)
It is our opinion that any potential employee may not be a suitable candidate for hire if they score a performance rating lower than an 91.
We received and reviewed the test results for your applicant Stan Stills. Stan had a GA score of 158, and a MD score of 162. When these figures were plugged into our regression equation his performance estimate was determined to be 77. We have calculated that Stan has a 95% probability that his performance estimate is between 66 and 83. Even though Stan Stills’ current employer, Professor T. Wedel, gave a glowing recommendation for his brother-in-law, we recommend that you base your decision on his poor performance estimate of 77 and not hire him. As statisticians like to say, “the law of large numbers does not lie”.
Everyone here at Hansen Consulting thanks you for the opportunity to serve you in your statistical business decision-making needs, and we look forward to working with you in the future.