IKEA Transport Efficiency Redesign
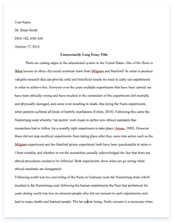
A limited time offer! Get a custom sample essay written according to your requirements urgent 3h delivery guaranteed
Order NowIKEA is one of the company that engages in retail. As a large company IKEA wants to make their company grow more and more and become better everyday. In order to expand and develop their company, IKEA also faces some problems :
1. Packaging design makes unnecessary costs
In this part, means that many of their low value products use excessive space on load units due to packaging design. Their packaging design results in poor efficiency in both the transportation and warehouse operations, and thereby creates unnecessary costs. For examples : for large products such as pillows, mattresses, sofas, and others which are filled with air and therefore take up a lot of unnecessary space during transportation andstorage. Another example of a product that has traditionally included a lot of air in its packaging is the Glimma tea candle. The original packaging for the candles is a bag containing 100 candles weighing in total 1.4kg. IKEA has been looking into ways of eliminating as much air as possible from their product packages.
2. Transportation costs form a large part of the total cost of many of the products In this part, it can be shown that it’s important to make the company to minimize transportation, handling and warehouse costs wherever possible. As we can see in the packaging problem stated that it takes a lot of unnecessary space during transportation and storage. This means that if we take a lot of unnecessary space during transportation, it will makes more transport that will be used. So more transportation means more cost.
3. Transportation affects the environment
The excessive packaging space used during transportation can affects the environment as well. Using too much transportation can increased pollution. As we know, pollution can lead us to global warming and global warming can put our Earth into dangerous situation.
4. Keeping the suppliers involved
Even though IKEA may find a solution in their packaging problems, there is a possibility where the products, made by the suppliers doesn’t match the package. Therefore, IKEA will need their suppliers cooperation.
Objectives
1. To find a way of redesigning the package of products
IKEA needs to reduce the excessive space in the packaging caused by the air filled in the package. By doing this, they can increase the real product volume in each package.
2. To fully utilize the transportation means
IKEA would like to reduce the number of transportation used by fully maximizing the load units in each truck/container. By doing this, IKEA can cut cost and take part in improving the environment.
3. To get cooperation from suppliers
Redesigning the package can possibly change the design of the product itself. IKEA would like to avoid further cost caused by this redesigning package solution. So both IKEA and the suppliers need to cooperate in implementing this solution.
4. To depict how IKEA can make their continous improvement in order to lower costs and increase economical, social, and environmental efficiency
We can know how IKEA find new ways of integrating their various suppliers in the supply chain to be able to improve efficiency and lower costs. Not every companywould be able to integrate suppliers in this manner, but companies of IKEA’s size are more likely to be able to negotiate agreements with their suppliers such as thecluster solution. We can learn more about how IKEA manage all of their project, how they solve their problems, what ways they took to fulfill their project requirements and at the end it can makes great improvements in efficiency and cost efficiency. And we can also understand how important to consider whether the benefits of the investments are indeed greater than the costs.
Research Methodology
The methods used by IKEA in doing this packaging research are: 1. Survey methodology
Since this research is done by the internal of IKEA, so they really know what the problems is and the current conditions in the company. They just have to ask or interview several directly related staffs in the production department and executives opinion. 2. Analysis methodology
The staffs trying to figure the suitable solution for this packaging problems by consulting several experts, benchmarking other companies who might have the same problems, and suggestions from internals. 3. Design methodology
In order to lower logistics costs and increase efficiency in its transportation and warehousing operations, IKEA tried so hard to find the right way to reduce unnecessary air in the product packaging. IKEA did some researches to find the most effective and efficient way to reduce the air from the product packaging. One way that they did is by holding the internal competition, called “Air Hunting Competition” focused on removing as much air as possible from packaging and thereby increasing true product volume during transportation and storage. One product that was being identified for the packaging development is Glimma tea candle. After several times struggling in trials & errors method, IKEA finally found the right way to reduce the air from the packaging, which is to increase the number of candles per package and place the candles in such a pattern to increase the density of the product package, so that it can also remove the air.
After find the right way to remove the air, the density of each package increased causing the increase number of the weight for each package too. Therefore, IKEA needs to do one more research to find the most effective way to ship the products, because the weight of a container with full load will be approximately 22,000 kg, which exceeds the maximum weight allowed for a vehicle. After doing some research by interviewing some experts and do the trials & errors method again, IKEA has finally found a way to solve it, which is by balancing the load on the trucks by using the lightweight products such as matresses and folded sofa, to fill up the left over space. And then, to achieve this balancing, products need to be consolidated from different suppliers and travel together to a common destination. Finally, IKEA has found a way which is using a so-called “cluster supplier” method, where a major supplier of IKEA takes responsibility for storing goods from the other suppliers for later consolidation with its own goods when orders are depatched to central distribution centers and warehouses in different countries.
Research Outcomes
After IKEA doing the research to solve the high transportation cost problem, the research produces several solutions to solve the problem, which are: * Packaging Redesign
Based on the analysis done from the research, the best solution to minimize the transportation cost is by redesigning the packaging of the products. As mentioned on the problem section, the low value products use excessive space of the warehouse and the trucks used to distribute them because they are filled up with excessive air inside the package. Therefore, in order to minimize the air inside the package, packaging redesign is required to solve that problem. Based on the research, it is also found that the best way to redesign the package is by creating certain patterns in arranging the products into one package, so it will increase the density of the product package and eliminate the air inside it. By doing this, more products will be able to fit in one package and reduce the spaces required in the warehouse and in the trucks. Less truck will be required to distribute the products and this solution will definitely reduce the transportation cost. * Product Loading Management
Second solution gained from the research is to do product loading management. The size and weight of the products which are being loaded into a truck were usually not being considered. That action leads to the condition where the total weight of products which are being loaded into one truck is usually not maximized to the capacity of the truck. Another condition which is usually happened because of that action is the condition where the total weight of products in a truck has reached the maximum capacity of truck, but there are still some spaces left in the truck. In the end, more trucks will be needed and it will increase the transportation cost. The research shows that doing product loading management will be the perfect solution to optimize the weight and space of the products which are being loaded into the truck. The product loading management will be done by combining the light products with the heavy ones, also combining the big products with the small ones. * Cluster Supplier
The analysis of the research also provides the solution of using cluster supplier to minimize the transportation cost. So, a major supplier will take the responsibility of storing goods from certain suppliers and distribute the products by grouping the products which have the common destination to travel together.
By performing those solutions which are developed based on the research, the high transportation cost problem will be resolved and the transportation process will be more effective and efficient. There are also some valuable lessons that they gain as additional benefits from the solutions, such as small, simple, ordinary solutions can sometimes become a great deal, advantage to a company, it is important to involve suppliers in early development of solutions that might be related to them and to integrate several suppliers to gain further process efficiency and cost efficiency.