Health and Safety – Working in hazardous environment
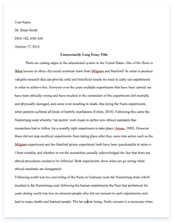
- Pages: 14
- Word count: 3338
- Category: Environment Health Policy Protection Safety Work
A limited time offer! Get a custom sample essay written according to your requirements urgent 3h delivery guaranteed
Order NowDo the protective clothing and equipment give the workers enough protection? Is there a chemical hazard? Do we have to use chemical-resistant clothes or gloves? Is there an electric shock hazard? If yes, what level?
Is there a fall hazard?
Personal Protection Equipment (PPE) in confined space
PPE is generally regarded as the last line of protection to avoid accidents. It also requires an appropriate managerial control system. However, PPE may be the first line of protection in the potentially hazardous environment and isolated position to enter a confined space.Each confined space may represent different hazards and levels of risk to health and safety. The last resort of PPE should be based on a risk assessment In terms of general rule the following guidance is recommended. Basic confined space PPE should include:
Full body protection (Overalls with suitable pockets for radio) Head protection (comfortable helmets with chinstraps)
Hand protection (hard-wearing, durable gloves)
Eye protection (protective glasses, goggles)
Ear protection (ear plugs or ear defenders – worn subject to communication system) Foot protection (steel toecaps (200 joules), oil resistant, steel midsoles) Gas meter – multi-gas meter for measuring of HC, H2S, CO, O2 is recommended Lighting (hand held with lanyard and appropriate beam width) Welding in Confined Spaces
To carry out welding and grinding in a confined space we have to follow all confined space entry and welding safety guidelines.Welding can be very dangerous in a confined space. Without suitable air ventilation, welding can become an admissible atmosphere into a poisonous one very quickly. When welding in a confined space, atmospheric/air monitoring should be carried out before anyone enters the space and periodically during the entry to ensure that the welding is not creating a toxic atmosphere. Justification of the level of protective personal equipment during welding, grinding in confined space.(What we need and why we need.) Justification PPE Reason to use
Required Not required â Welding helmet Always needed. (Using welding helmet during welding is always required. Eye injury can occur from the intense light, UV radiation that a welding arc can produce. Injury from a welder’s arc commonly is known as flash burn, welder’s flash, or arc eye. Eye injury can also occur from hot slag that can fly off from the weld during cooling.) â Respirator However the welding fume is not currently assigned a hazard classification respiratory protection is needed when ventilation is not sufficient to remove welding fumes or when there is risk of oxygen deficiency. Welding fumes also produce gases, which can contain carbon monoxide, fluorine, hydrogen fluoride, nitrogen oxide and ozone. â Ear protection Required to wear if the daily noise exposure level at 85dB or over when the employers are required to take certain steps to reduce the harmful effects of noise on hearing. â Flame resistant clothing In most welding applications, it is critical to have all exposed skin covered during the welding exposure to prevent burns to the skin. â Welding gloves Heavy, flame-resistant gloves (from materials such as leather) should always be worn to protect your hands and wrists from burns, cuts and scratches.
As long as they are dry and in good condition, they will offer some insulation against electric shock. (TIG/MIG etc..)â Safety shoes Always required. High top boots with steel toecaps fully laced to prevent sparks from entering into the boots or falling heavy objects. Use fire-resistant boot protectors or spats strapped around the pant legs and boot tops, to prevent sparks from bouncing in the top of the boots. â Safety glasses Even when wearing a welding helmet with side shields, or goggles, should always be worn to protect your eyes from flying particles (grinding). â High visible jacket High-visibility safety apparel (HVSA) is needed when there is low light and poor visibility, especially if someone works in confined space. This fact increases the safety at work. â Harness and retrieval lines Always required in confined space. Harnesses are used to belay the wearer in areas where there exists a danger of falls from a height and to arrest falls. â Gas meter Recommended. If welding it is required. Multi-gas detector – Air monitoring. Gas, fume or vapour can arise from welding or by use of volatile and flammable solvents from paints and adhesives etc. It may be necessary to mechanically ventilate the confined space. â Lighting Recommended.
Non-sparking tools and specially protected lighting are essential where flammable or potentially explosive atmospheres are likely. In certain confined spaces (eg inside metal tanks) suitable precautions to prevent electric shock include use of extra low voltage equipment (typically less than 25 V) and, where necessary, residual current devices. â Portable ladder A safe means of access to and within the confined space, such as fixed ladders. Ladder should only be used where a risk assessment demonstrates that the use of more suitable work equipment is not justified because of the low risk, and short duration of use or existing features on site that cannot be altered. â Radio Required. If a phone is not immediately available, radio communications shall be used. Workers have to be able to communicate with each other and with attendants on the outside of the space. Communication may be voice, radio, hand signals or life lines, etc., or a combination of, as long as it enables the employees to monitor each other and to alert entrants of the need to evacuate the space. P 1.2 – Task 2.
Evaluation of permit-to-work
What is Permit-To-Work System?
A formally described process to control work which is recognized as potentially hazardous. It is a flow of information between administration management, supervisors, and workers who carry out the job which can be hazardous. The facility giving the workgroup a written permit to work within a particular located area and time schedule using the appropriate equipment. Essential features: Clear identification of those who may authorise particular jobs Clear identification of the types of work we consider hazardous Standardised identification of the task, the Risk Assessment process, the permitted task duration and also any simultaneous work activity Training and instruction in the issue, use and closure of permits Monitoring and auditing to ensure that the system is working as intended When are P.T.W. systems applicable?
PTW have to be considered if we want to carry out any work which may have
substantial adverse effect on the safety of the environment or the personnel. It is very necessary that anyone begins a hazardous work is aware of the local provisions describing how and when PTW is to be applied at a particular location. Permit to work in confined spaceWhen we issue a PTW for confined space we have to make sure of: What are the potential hazards in this particular confined space? Are the workers qualified /trained to undertake any work?
Has it been separated from all connected pipework?
Has it been drained, purged?
Has it been locked out and electrically isolated?
Has the confined space been locked off mechanically?
What is the min/max temperature during work in the confined space? (If the temperature is significantly hot in a confined space that might be a risk of a stroke or we may have a heat-collapse from prolonged exposure to high temperatures. The risk can be avoided or reduced by the wearing an appropriate PPE or choosing appropriate ventilation.) Additional ventilation required?
What is the air consistency in the confined space?
On-going gas/oxygen detector at hand? (The atmosphere should be monitored using atmosphere testing equipment to evaluate any hazardous atmospheres that may occur so the appropriate permit entry conditions come to term for that space. Testing for residual hydrocarbon gas and oxygen content.) Emergency breathing apparatus required?
Does the entrance have the required size to enter in case of emergency? Is access to evacuate from the confined space acceptable?
Is the portable oxygen breathing machine available to use in emergency situation? Is safety harness and any other emergency equipment available? Is the first aider (preferably supervisor/manager) at point of entry? Permit to work working at height
Is the person who carries out the work qualified/trained?
Appropriate working at height permits posted?
Are the entry and emergency exit safe to use?
Is the working area surrounded with barricades?
Is there a means of contact in emergency?
Are there handrails and roofing ladder involved?
Are there harness or/and scaffolding involved?
If yes guard rails required?
Is there a safe mean of weather conditions?
Any hazard from gas or vapour?
Any overhead on-going work?
Safe working load. Is the roof surface itself fragile?
Is PPE required?
Work at height operations is closely supervised? Name of supervisor: Is there a rescue plan?
Is there a safe work method statement issued?
Permit to work – hot workWhat hot work permit basically does is accesses an alert system to everyone in the area as well as providing guidance to the individual doing the hot work. The permit has three sections: A checklist for precautions and safe preparation
A section for accountability
And a warning sign with a space for an emergency information Usually three people will be involved with the permit the hot work supervisor, the person who is doing the hot work and the fire watch. The basic concept of the permit is:
We want to identify weather itâs safe to do work in the area. If itâs not safe what steps we need to take to make it safe. Once we made the area safe by performing the steps itemised on the permit then we can move forward with selecting a fire watch. Following these steps can help you prevent that small fire that’s going to happen from becoming a major disaster. Hot work accidents usually occur when workers welding cutting, grinding near flammable vapour. (Eg Case Study: â2010 hot work accident at DuPont Buffaloâ) In order to start the hot work we should either disconnect or cover the some alarm detector for the time we carry out the hot work process. Is there a danger from the transferred heat?
Area has to be cleared of flammable material.
Removing all flammable liquids or gases.
Welding, cutting or grinding work covered/protected with non-flammable material Gas supply has to be closed or isolated or/and protect piping Are the flash back arrestors in working order? (gas cylinders) Gas cylinders used and stored in the upright position?
Are the fire extinguishers in good working order?
Other specifications regarding the particular area.
Safe Isolation in general terms
The isolation of a mechanically and/or electrically operated equipment is required if the system if it can be operated otherwise inadvertently. In case of confined space if any poisonous gas or vapour can enter in a confined space we have to make sure that all pipework had been isolated before we start the process. In all cases a check-back is required to make sure that the isolation was effective. In terms of safe isolation the isolation requires:
Barriers ( to prevent system approach either mechanical, electrical or chemical) Lock off (electrical isolation)
Blanking plate (mechanical, chemical isolation)
Tag (if the system is locked off the system should allow you to go back and identify who had locked it off (name), when, and e why clear identification Shut off valve ( mechanical )
Check off (is the system really down?) ( electrical isolation) Safe isolation requires some sort of system approach and right equipment, diagram to follow the safe isolation procedure. Safety isolation procedure requires a trained person who is authorised and trained to carry out the isolation and the correct organisation.Locks and âDangerâ tags in general terms If someone works on and isolated plant their own lock and Danger tag should be fitted or can be used other management-approved system that gives the same level of safety. ⢠All danger and lock-off tags must be signed⢠All danger and lock-off tags must be dated⢠Locks has to be attached by an appropriate tag to identify who had locked out the plant.⢠The locks and tags cannot be removed by outsider or unauthorised worker but by the person who fitted them or by an authorised supervisor with the signature on the tag. Isolation in terms of mechanical system
Hot-work equipment (eg. welder) is secured.
Fixed gas/oil supply piping has been isolated and locked.
Check for fire or spark source left alive.
Any gas, air or steam or must be locked down by draining down or blocking. Detectors such as heat or smoke have to be in operation. (Tagging might be required) If any pipes, tanks contains hazardous gas, fluid etc. they have to be isolated and vented. Taking actions to prevent hazardous vapour and/or sparks from release from unsealed ends. Consider the potential for conduction of heat.
Isolation in terms of chemical system
Closing manually and automatic operated valves which provide the chemical supply either it is gas or some liquid Removing power from motors if there is a pump system
Set-up pressure relief
Set-up cooling systems
Set-up ventilation
Purging
Blanking, lock-off
Tagging
Isolation in terms of electrical system
Identify all power sources and isolate them. In the case of electrical equipment, âwhole current isolationâ such as the main isolator should be used instead of âcontrol isolationâ by way of the stop button on a control panel. Any energised equipment to be worked on must be isolated/discharged to ensure the energy is removed or controlled to prevent incidents. This may include ensuring inertia in mechanical parts, parts likely to move by gravity, electrical capacitors, accumulators, springs and pressurized fluids.
Verify that the isolation is effective eg. determine that the equipment is âDeadâ ensure any guards are in place and engage the start mechanism of the plant. A qualified worker shall use the appropriate test equipment to test the circuit elements and electrical parts of equipment. Work must be completed in accordance with the provision of the energy isolation permit. Where electrical isolation is affected at a removable or rack out circuit breaker or combined fuse, switch, if practicable it must be racked out or removed, then locked open and danger tagged. Lock or otherwise secure all isolating points using padlocks, multi-padlock hasps and danger tags.
Using the HSE daily noise level calculator by our case study the average daily noise exposure of 89dB By Control of Noise at Work Regulations 2005 if the noise levels exceed 85dB(A) (Upper Exposure Action Value) then it is dangerous to the hearing and can cause irreversible damage. Over 85 dB average noise level wearing of hearing protection is compulsory in order to take an action to reduce the high level of noise.What can be done to reduce this average daily noise level? Order or purchase new machines with lower noise level
Move the affected work area or the source of noise out of âsightâ. Using divider or sound barrier between the source of noise and the work area/employee. Maintain the equipment if that solves the problem.
Using appropriate PPE
By determining the suitable PPE if we know the daily noise exposure is 89 dB using the protector factor table below:
By this spread sheet we have to select an era protector with and SNR (Single Number Rating) of 20 or less. In order to reduce the average noise level I have chosen the 3M ClearE-A-R SNR 20 earplugs from the 3M catalog with the SNR value of 20. Using the calculator I have green 79 dB.
The last SNR value that still gives green result is the E-A-R Classic Earplugs SNR 28 dB earplug. It still gives appropriate protection and it isnât overprotect. If I chose an earplug with SNR of 29 ( eg. E-A-R Classic Corded Earplugs SNR 29 dB) or over the earplug overprotects and the calculator gives red field.
In conclusion by this case study we have to choose earplugs between SNR value of 15 and 28. Choosing lower than 15 may not give us enough protection or choosing earplug with higher value of 28 will overprotect us which can be catastrophic. Over-protection can cause difficulties with hearing warning signals and communication with others. D1 – Use critical reflection to evaluate own work and justify valid conclusions.Additional working at heights case study âOSHA Violation: Worker stands on column using sledgehammerâYoutube video: http://www.youtube.com/watch?v=Syv-x5_gU3k Content of the video:A worker wants to carry out a job by using a sledgehammer. He uses 15ft ladder to stand atop a column and use a sledgehammer to hit a big rivet. He has no fall protection at all. Watching this video I would like to point out the deficiency of communication, training and management. Lack of training:
We can see that the person who is working at height is not to be competently trained in the work to be done. He is not aware of the risks involved and he is not following the required safe work procedures which include the use of proper personal protective equipment. If he had known or been trained than he either didnât go without using fall protection or refused to carry out the dangerous task without providing him with the appropriate safety equipment such as safety harness. Lack of communication:
A buddy system should be encouraged in your company so that workers can help to remind and encourage each other on the safe work practices even in the absence of a supervisor. The supervisor or manager should have ensured the worker health and safety and provide employers and contractors with information regarding hazards. Incompetent management:
The management should decide to disregard unsafe practices such as not wearing the individual fall arrest system when required. Workers may be led to believe that it is acceptable to engage in such practices. Over time, these unsafe practices may be unofficially incorporated into the work procedures, making it a norm. This will increase the risk faced by workers working at height. The supervision of work is also important and should be carried out by an appointed and qualified supervisor. Without proper supervision, workers may violate rules and regulations or adopt unsafe practices and put themselves at risk. When they made this video they either didnât have supervision on in the work area or if they had he also had not been fully trained. If the supervisor had had the appropriate training he either wasnât in the area or if he was he should not have let the worker to carry out this dangerous task. From Working at heights regulation:
⢠Employers must ensure the health and safety of their workers, inform workers of potential hazards, and remedy hazardous workplace conditions and practices. ⢠Supervisors must ensure the health and safety of all workers under their direct supervision and inform those workers of hazards. ⢠Workers must follow established safe work procedures, use any required personal protective clothing and equipment, and report hazards to their supervisor or employer. Seeing this video in my opinion the company and the management abused/breached the following points form The Work as Heights Regulations 2005: Regulation 4. /1b Organisation and planning
4/1b Every employer shall ensure that work at height is appropriately supervised. Here either it was a great absence of the operation being supervised or was a clear evidence of the lack of the knowledge of Health and Safety Regulations nor training. Regulation 6. /3,5 Avoidance of risks from work at height6/3 Where work is carried out at height, every employer shall take suitable and sufficient measures to prevent, so far as is reasonably practicable, any person falling a distance liable to cause personal injury. 6/5 Every employer shall so far as is reasonably practicable, provide sufficient work equipment to minimise the consequences of a fall. Employers must comply with the Health and Safety at Work Act 1974 and extensive subordinate legislation. If health and safety rules are broken, employers face severe penalties, with potentially unlimited fines. The worst transgressions can even result in imprisonment.
Information Resources:
PLANT ISOLATION, SAFETY TAG AND LOCKOUT PROCEDUREShttp://policy.cqu.edu.au/Policy/policy_file.do?policyid=150Handbook
of electrical safetyhttp://www.slideshare.net/safithri/14-handbook-of-electrical-safetyPermit to work procedurehttp://www.bris.ac.uk/Depts/Bursar/BuildingServices/permit/ptwproced.pdfPERMIT TO WORK AND RESTRICTED ACCESS GUIDELINEShttp://staff.uow.edu.au/content/groups/public/@web/@ohs/documents/doc/uow048592.pdfHOT WORK â PERMIT TO WORKhttp://www.ardsshoppingcentre.com/contractor/hotworks.pdfOSHA â Control of hazardous energy (Lokout/Tagout)https://www.osha.gov/SLTC/controlhazardousenergy/University of Cambridge â Confined space Permit to Workhttp://www.ch.cam.ac.uk/sites/ch/files/users/meg27/DSO053M%20Confined%20Space%20PTW%20Final%200813.pdfHSE information sheet Emergency isolation of process plant in the chemical industryhttp://www.hse.gov.uk/pubns/chis2.pdfSTFC â Safety, Health and Environmenthttp://www.stfc.ac.uk/SHE/Codes/STFC/20771.aspxThe Work at Height Regulations 2005http://www.legislation.gov.uk/uksi/2005/735/regulation/6/made