Chaparral Steel
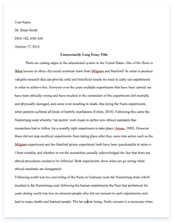
- Pages: 10
- Word count: 2259
- Category:
A limited time offer! Get a custom sample essay written according to your requirements urgent 3h delivery guaranteed
Order NowQuestion 1
Consider the company’s operations during the years from 1975 to 1979, and answer the following questions: a. How has the above complex approach actually worked, over these four years? What was the outlook (as of the case date) for further progress in this matter? In 1975 Chaparral Steel commissioned minimill and started production. Minimills are different from traditional integrated steel plants. In minimill an Electric Arc Furnace (EAF) is used for steel making purpose and in downstream long product is made using rolling mill. The advantage of minimill is it requires less capital investment and a good solution when only long products needed to be produced. In case of Chaparral they invested $40 million in minimill as against $200 million requires for an integrated steel plant. The input to minimill is scrap or Direct Reduced Iron (DRI) and electricity is used to melt the scrap in EAF. So in countries like USA where scrap is available readily and electricity cost is relatively cheap compared to coking coal required for blast furnace minimill is even cheaper.
While set up of minimill can be considered a deliberate strategy Chaparral Steel continues modest investment in new equipments and procedures as and when needed so the emerging ideas from shop floors are facilitated. So it is a mix of both deliberate and emergent strategy. To get new ideas and make emerging strategy successful Chaparral has introduced profit sharing plan. Profit sharing contributed to additional 10-15% on average hourly wage of $16. As it empowered employees and followed participatory management employees were happy and there was no union thus further boosting profitability. Chaparral also sends employees for continuous training and development.
They send their employees to other steel plants and equipment manufacturers to know about procedures better which by turn fuelled development of emerging strategies. Chaparral Steel set up the minimill with finishing mill capacity at 500000 tpy which was twice the capacity of melt shop which was only 250000 tpy. That meant it will have to operate melt shop at above capacity to feed the rolling mill. The idea behind going for low capacity melt shop is that chance of breakdown is more in rolling mill compared to melt shop.
Also Chaparral foresaw that improvement can be done in melt shop to increase its capacity. Inside melt shop there was a capacity mismatch EAF was rated at 250000 tpy but was being operated at 370000 tpy. This capacity mismatch put further pressure on casting where they installed a 4 strand billet caster for casting the molten steel. b. Draw a simple flow diagram showing the three stages of production in Chaparral’s mini-mill (inclusive of the inter-stage, simultaneous operation of the two ladles—for tapping of the molten liquid, lifting it to the caster, and finally lowering the empty ladle to the ground for the next heat).
In the following diagram the sequence of operation is presented. Scrap collection from Scrap yard
Scrap bucket is transferred to EAF bay and emptied into EAF
Electrodes are lowered and power connection is established
Scraps are melted and second charge is added till heat is complete
Once heat is complete molten metal is tapped into Ladle 1 from EAF Ladle is transferred to Ladle furnace for secondary steelmaking operation Once metal reaches critical temperature Ladle 1 is lifted by crane and placed in ladle turret over tundish Ladle 1 feeds hot metal to the tundish which in turn feeds molds for casting While Ladle 1 is feeding the tundish ladle 2 is used to tap liquid metal and put it through secondary steelmaking Ladle 2 is then transferred and placed in other arm of turret Once Ladle 1 finishes hot metal feeding turret arm is rotated and Ladle 2 starts feeding the molds Ladle 1 is transferred back to EAF. In this fashion caster is fed continuously and continuous casting is achieved Scrap collection from Scrap yard
Scrap bucket is transferred to EAF bay and emptied into EAF
Electrodes are lowered and power connection is established
Scraps are melted and second charge is added till heat is complete
Once heat is complete molten metal is tapped into Ladle 1 from EAF Ladle is transferred to Ladle furnace for secondary steelmaking operation Once metal reaches critical temperature Ladle 1 is lifted by crane and placed in ladle turret over tundish Ladle 1 feeds hot metal to the tundish which in turn feeds molds for casting While Ladle 1 is feeding the tundish ladle 2 is used to tap liquid metal and put it through secondary steelmaking Ladle 2 is then transferred and placed in other arm of turret Once Ladle 1 finishes hot metal feeding turret arm is rotated and Ladle 2 starts feeding the molds Ladle 1 is transferred back to EAF. In this fashion caster is fed continuously and continuous casting is achieved
c. Draw a ‘multi-activity chart’ (or bar chart), showing for a cycle of one whole ‘heat’ (of about 100 tons), the operation of the furnace, the caster and the rolling mill (along with roles played by the crews attending to the furnace and to the ladle, for the transfer of molten metal), enabling the existing mill (in 1979, before the proposed capacity expansion) to operate at its designed capacity. Multi activity chart is drawn as below taking following assumptions
* Three charges are required for EAF
* Assuming 100 ton EAF and four strand caster and casting rate 16 ton per hour total cast time is calculated as approximately 90 minutes (=100/16*4) * Other time are taken from internet source (Steel university website) Time (minute)| Cumulative Time| EAF Operator| Crane operator| LF operator| CCM Operator| 3| 3| Loading First Scrap Bucket| | | |
2| 5| Lowering of electrodes| | | |
8| 13| Melting| | | |
2| 15| Lifting Electrodes | | | |
3| 18| Loading Second Scrap Bucket| | | |
2| 20| Lowering of electrodes| | | |
8| 28| Melting| | | |
2| 30| Lifting Electrodes | | | |
3| 33| Loading Third Scrap Bucket| | | |
2| 35| Lowering of electrodes| | | |
8| 43| Melting| | | |
2| 45| C/O injection for foaming slag| | | |
3| 48| Tapping into Ladle| | | |
3| 51| | Transporting Ladle to LF| | |
8| 59| | | LF for secondary metalluargy | |
3| 62| | Transport Ladle to ladle turret| | |
2| 64| | | | Rotate turret|
0| 64| | | | position dummy bar |
1| 65| | | | Open Ladle Slide gate|
1| 66| | | | open tundish slide gate|
0| 66| | | | Start Mould oscillation|
90| 156| | | | Casting|
2| 158| | Remove Ladle from turret| | |
d. Explain, using the above chart or a sketch, how the Japanese procedure of ‘sequence casting’ would have served to provide, for Chaparral, a new alternative for additional future increases in the caster capacity? Sequence casting can be used to increase the capacity. In sequence casting a ladle turret is used with two arms to hold two ladles. In first instance when one ladle is feeding the moulds another ladle is prepared with molten metal from EAF. The same is taken to other arm of ladle turret and placed there. So when the first ladle completes feeding of molten metal turret is rotated and second ladle start feeding the strands through the tundish. The empty ladle is removed to the ladle preheating ward. In this way continuous casting can be achieved till tundish refractory is not depleted. Once tundish refractory is depleted another tundish is placed through tundish car above the strands. The tundish is taken to the tundish preheating and lining ward to reline it with refractory and another tundish is placed in tundish car. Question 2
Discuss in detail the possible explanation of how Chaparral’s ‘initial capacity decisions’ as above, and its subsequent actions at the levels of the various individual operations (in particular, at the furnace and the caster) in the shops might have together contributed to the impressive results actually realized during these four years. Chaparral installed the minimill with melt shop capacity half of the rolling mill capacity. So there was need to increase the capacity of melt shop to feed downstream rolling mill.
This realization led to the innovative strategies taken to operate EAF at 370000 tpy instead of at rated 250000 tpy. This has been made possible as the rebuild the furnace with $11 million expense and installed new technology. Along with that they streamlined operating procedure to save time in operation at melt shop. Chaparral management tracked the performance of its workers with other benchmarks available. They operated at 2.7 labour hour per ton which is same as its closest minimill competitor Nucor. Chaparral further continued improvements to decrease labour hour to 2 labour hours per ton.
Question 3
Why do you think the company might not have tried such innovative strategies, which it employed for its furnace and caster, for also increasing its rolling mill’s capacity? Chaparral installed its rolling mill at double the capacity of melt shop. So there was no need to increase the efficiency of rolling mill. It was theoretically able to process more cast steel than the capacity of melt shop. Rolling mill capacity was more to keep it as a buffer against possible breakdown. Also if there is any need to change product mix then rolling stands are to be set up leading to idle capacity time. So capacity of rolling mill was higher than melt shop. In case chaparral Steel decided to introduce more variety of products they might need to consider increasing the efficiency as more set up time will be required. Another reason is that operation of rolling mill is fully automated so there is no further scope of saving time without increasing capital expenditure.
Question 4
What was Chaparral’s strategy with regard to its ‘product scope’ (which took into account not only the product profitability, but possible loss of productivity through short runs)? Was it dynamic in scope? How did it change over the first four years? Explain. Chaparral steel was producing long products through its minimill which are used for construction purpose mainly. Now in construction different kind of bars are required. Like ordinary rebar to “I” shaped beam, “H” shaped pile etc. The same rolling mill can be used to produce different sizes and shapes upon changing rolling stands. The dimension of rolling stand grooves determine the shape it produces on the other hand the power of stand determines maximum size. If bars are to be smaller in size then it is to be rolled more using more number of stands or increasing the roll pass. Now steel plant is run continuously and once set up is done for a particular shape a substantial quantity is to be produced.
For example in each heat 70 billets of 1.5 ton were produced. So in total 105 ton cast steel is produced. It takes about 1 hour and 40 minutes to cast each heat. So it is obvious that the company needs to accept large order for a particular shape to compensate for set up time it needs. There is a dichotomy in product scope to be reconciled here. Dichotomy arises because at one hand supplying small orders mean loss of valuable plant time in setting up for small numbers and on the other hand not accepting order means loss of business. In order to reconcile this dichotomy Chaparral Steel aggregates order from different customers. Its decision to enter new geography also helps in getting new customer. As the market size increases Chaparral could effectively combine different orders for a particular shaped product and achieved economies of scale. So it reconciles the product scope dichotomy as well.
Question 5
What was the thinking behind its strategy of also winning orders in newer geographical markets (i.e., in its secondary market areas) rather than increasing the market shares in the existing geographical markets (in its primary market areas)? When a company tries to increase its growth then it has essentially four options as depicted in figure. As the product is steel it cannot enter into related new products as that will involve significant capital expenditure. So it needs to explore new geography, penetrate the same market, or acquire new company. Acquiring new company again involves significant expenditure so only feasible option left with the company are either to penetrate same market or explore new geography. Penetrating the same market means more competition with existing competitors which requires investment in promotion thus reducing profit margin. On the other hand If Chaparral can go to other market only cost that is required is cost for transportation and one time set up of downstream supply chain comprising of distribution centres etc.
Figure 1 Growth Strategy options for a Company
So it can be said that Chaparral has reconciled a dichotomy on market by expanding into new geography. The dichotomy was to not to cannibalize existing market by starting a price war versus selling more steel. By exploring new geography Chaparral has been able to increase its top line at the same time did not hurt its bottom line by not increasing cost related to market penetration and cannibalization of existing market. As the fact goes Chaparral was operating in four US states- Texas, Oklahoma, Louisiana, and Arkansas. Later it made a foray into other 10 states by 1977 and expanded to 20 states by 1979.