Bottling Company Case Study
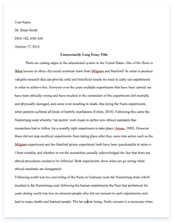
- Pages: 2
- Word count: 397
- Category: Case Study Company Manager
A limited time offer! Get a custom sample essay written according to your requirements urgent 3h delivery guaranteed
Order NowConfidence Interval for the ounces in the bottle. With a mean score of 14.87, a standard deviation of 0.55033, and a desired confidence level of 95%, the confidence interval is + 0.25. There is a 95% certainty that the true population of the mean falls within the range of 14.66 to 15.16.
For the hypothesis test the calculation has to verify if the claim that a bottle contains less than sixteen (16) ounces that was advertised. The logic of this test is that there was a complaint that the bottle of the brand soda produced by the company contains less than the advertised sixteen (16) ounces that is produced. Now order to verify this claim the employee will pull thirty (30) bottles off the line at random from all shifts at the bottle plant. Employees are required to measure the amount of soda there is in each bottle.
With this study there can be two hypothesis one could be the alternative hypothesis that would be the bottles of the brand of soda produced contains less than the advertised sixteen (16) ounces of product. The other hypothesis is a null hypothesis were the bottle of the brand of soda produced do not contain less than the advertised sixteen (16) ounces of product. 95% Confidence Interval= (14.66, 15.16)
Completing the calculation we are confident that the true population mean is between 14.66 and 15.16. Margin error= (15.16-14.66)=0.5/2=0.25
T Statistic= -11.246
P-Value= 2.15273
Based on the P-Value there are evidence against the null hypothesis in favor of the alternative.
The conclusion is that there are less than sixteen (16) ounces in some of the bottles of soda. Some of these causes could come from mechanical defect with the equipment, employees failing to notice or inspect the bottles before packaging, or the product evaporates or goes flat after a period of time as pasted. As a manager, I would recommend that there be a maintenance check on all equipment. Also employees will monitored on how thorough each product has been inspected before it leaving the assembly line to be packaged. I would lastly, I will let the consumers know that there can be a possibility that the product may have experienced evaporation and gone flat depending on how long it stayed on the shelf unopened. I would insure them that the problems has been address and is being looked at.