Process Industry with Focus on Steel
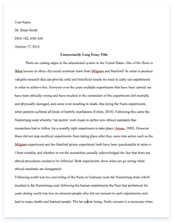
A limited time offer! Get a custom sample essay written according to your requirements urgent 3h delivery guaranteed
Order Now1. Introduction
This research addresses application of lean manufacturing concepts to the continuous production/process sector with a focus on the steel industry. After World War II Japanese manufactures, particularly in the automotive industry, were faced with the dilemma of shortages of material, financial and human resources.Eiji Toyoda and Taiichi Ohno at the Toyota Motor Company on Japan pioneered the concept of Toyota Production System, or what is known as “Lean Manufacturing. “The basic idea behind the system is eliminating waste. Waste is defined as anything that does not add value to the end product from the customer’s perspective. The primary objective of lean manufacturing is to assist manufacturers who have a desire to improve their company’s operations and become more competitive through the implementation of different lean manufacturing tools and techniques.
Quickly following the success of lean manufacturing in Japan other companies and industries. The term “lean” as Womack and jones defined it denotes a system that utilizes less in terms of all inputs to create the same outputs as those created by a traditional mass production system, while contributing increased varieties for the end customer. Lean is to manufacture only what is needed by the customer, when it is needed and in the quantities ordered. The manufacture of Goods is done in a way that minimizes the time taken to deliver the finished goods, the amount of labour required and the floor space required, and it’s done with the highest quality and unusual, at the low cost.
2. History of Lean
Although there are instances of rigorous process thinking in manufacturing all the way back to the Arsenal in Venice in the 1450s, the first person to truly integrate an entire production process was Henry Ford. At Highland Park, MI, in 1913 he married consistently interchangeable parts with standard work and moving conveyance to create what he called flow production. The public grasped this in the dramatic form of the moving assembly line, but from the standpoint of the manufacturing engineer the breakthroughs actually went much further. Ford lined up fabrication steps in process sequence wherever possible using special-purpose machines and go/no-go gauges to fabricate and assemble the components going into the vehicle within a few minutes, and deliver perfectly fitting components directly to line-side. This was a truly revolutionary break from the shop practices of the American System that consisted of general-purpose machines grouped by process, which made parts that eventually found their way into finished products after a good bit of tinkering (fitting) in subassembly and final assembly. The problem with Ford’s system was not the flow: He was able to turn the inventories of the entire company every few days. Rather it was his inability to provide variety.
The Model T was not just limited to one colour. It was also limited to one specification so that all Model T chassis were essentially identical up through the end of production in 1926. (The customer did have a choice of four or five body styles, a drop-on feature from outside suppliers added at the very end of the production line.) Indeed, it appears that practically every machine in the Ford Motor Company worked on a single part number, and there were essentially no changeovers. When the world wanted variety, including model cycles shorter than the 19 years for the Model T, Ford seemed to lose his way. Other automakers responded to the need for many models, each with many options, but with production systems whose design and fabrication steps regressed toward process areas with much longer throughput times. Over time they populated their fabrication shops with larger and larger machines that ran faster and faster, apparently lowering costs per process step, but continually increasing throughput times and inventories except in the rare case—like engine machining lines—where all of the process steps could be linked and automated.
Even worse, the time lags between process steps and the complex part routings required ever more sophisticated information management systems culminating in computerized Materials Requirements Planning (MRP) systems. As Kiichiro Toyoda, Taiichi Ohno, and others at Toyota looked at this situation in the 1930s, and more intensely just after World War II, it occurred to them that a series of simple innovations might make it more possible to provide both continuity in process flow and a wide variety in product offerings. They therefore revisited Ford’s original thinking, and invented the Toyota Production System. This system in essence shifted the focus of the manufacturing engineer from individual machines and their utilization, to the flow of the product through the total process.
Toyota concluded that by right-sizing machines for the actual volume needed, introducing self-monitoring machines to ensure quality, lining the machines up in process sequence, pioneering quick setups so each machine could make small volumes of many part numbers, and having each process step notify the previous step of its current needs for materials, it would be possible to obtain low cost, high variety, high quality, and very rapid throughput times to respond to changing customer desires. Also, information management could be made much simpler and more accurate. The thought process of lean was thoroughly described in the book The Machine That Changed the World (1990) by James P. Womack, Daniel Roos, and Daniel T. Jones. In a subsequent volume, Lean Thinking (1996), James P. Womack and Daniel T. Jones distilled these lean principles even further to five: * Specify the value desired by the customer
Identify the value stream for each product providing that value and challenge all of the wasted steps. Currently necessary to provide it * Make the product flow continuously through the remaining value-added steps * Introduce pull between all steps where continuous flow is possible * Manage toward perfection so that the number of steps and the amount of time and information needed to serve the customer continually falls.
The term “lean” is used because Japanese business methods used less human effort, capital investment, floor space, materials, and time in all aspects of operations. The resulting competition among U.S. and Japanese automakers over the last 25 years has led to the adoption of these principles within all U.S. manufacturing businesses Lean Today
As these words are written, Toyota, the leading lean exemplar in the world, stands poised to become the largest automaker in the world in terms of overall sales. Its dominant success in everything from rising sales and market shares in every global market, not to mention a clear lead in hybrid technology, stands as the strongest proof of the power of lean enterprise. This continued success has over the past two decades created an enormous demand for greater knowledge about lean thinking. There are literally hundreds of books and papers, not to mention thousands of media articles exploring the subject, and numerous other resources available to this growing audience.
3. PROBLEM STATEMENT
Major businesses in the United States have been trying to adopt new business initiative in order to stay alive in the new competitive market place. Lean manufacturing is one of these initiatives that focuses on cost reduction by eliminating non – value added activities. These tools and techniques of lean manufacturing have been widely used in the discrete industry starting with the introduction of the original Toyota production system. Tools include just in time, cellular manufacturing, total productive maintenance, single – minute exchanges of dies and production smoothing have been widely used in discrete parts manufacturing sectors such as automotive, electronics and appliance manufacturing. Applications of lean manufacturing to the continuous process industry have been far fewer. In part, it has been argued that this is because such industries are inherently are more efficient and present relatively less need for such improvement activities.
Managers have also been hesitant to adopt lean manufacturing tools and techniques to the continuous process industry because of reasons such as high volume and low variety products, large inflexible machines and the long set up times that characterize the process industry. As an example, it is difficult to use the cellular manufacturing concept in a process facility due to the fact that equipment is large and not easy to move. While it seems that some lean manufacturing tools are difficult to adapt in the process industry, others are not. For example Cook and Rogowski (1996) and Billesbach (1994) used just – in – time concepts at a process facility and both reported good results. This research is driven by the fact that while researches and practitioners have widely used lean manufacturing tools in the discrete industry, nobody has systematically investigated how to apply lean tools and techniques to a continuous process facility due the differences exhibited between the two manufacturing environments. In order to compete in today’s global competitive market the continuous process industry also needs to look for more ways to gain a competitive edge.
The objective is to systematically demonstrate how lean manufacturing tools when used appropriately can help the process industry to:
1. better product quality,
2. better overall financial and operational procedures.
3. eliminate waste
4. have better inventory control,
The goal of this research is to investigate how the tools of lean manufacturing can be adapted from the discrete to the continuous manufacturing environment and to evaluate their benefits at a specific industrial concern. The research hypothesizes that there are big opportunities for improvement in the process industries if lean tools are utilized. Although the process and discrete industry share several common characteristics, there are also areas where they are very different. Both manufacturing settings have overlap, but at the extreme, each has its unique characteristics. The objective is to look at commonalities between discrete and continuous manufacturing where lean techniques from the discrete side are directly applicable, and to also examine ways to do so in other areas where this may not be quite so straightforward.
In this research the steel industry will be used to represent the continuous process industry, and much of the work will be carried out at an actual steel manufacturing facility 4. Research Objective
5 .RESEARCH APPROACH
The initial step in this research is to systematically study and define the history of the lean manufacturing concept and its different tools and techniques. It will then examine where most of the lean tools and techniques have been used .This will be followed by a literature review of the process industry and a study of the findings regarding applications of lean concepts to continuous manufacturing and the steel industry in particular. The next step is to develop taxonomy of the continuous process industry with respect to its product /process characteristics and the relative balance of discrete and continuous operations. This taxonomy is used to contrast the process industry and to characterise the process industry distinguishable groups. Next, this taxonomy is used to examine and identify specific lean manufacturing tools and techniques that could be applicable. To study the effect of lean tools at a process sector the steel industry is used to illustrate the procedures of implementing lean tools at a process facility. First value stream mapping is used to map the current state for ABS.this is used to identify sources of waste and then identify lean tools to try to reduce this waste. The future state map is then developed for a system with lean tools applied to it.