Nissan Case Study
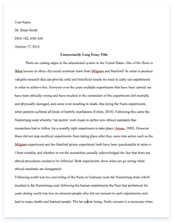
- Pages: 3
- Word count: 646
- Category: Case Study Service
A limited time offer! Get a custom sample essay written according to your requirements urgent 3h delivery guaranteed
Order Now1. The quality problems in this case include total quality management, statistical process control, timing, managing the supply chain, and capacity planning. Total quality management would have addressed the problems in a broader since in giving employees and managers goals to strive for and follow. This would allow the managers to have plans and a guide in how to fully satisfy customers, as well as motivating their workers to complete task efficiently. Statistical process control would provide an objective tool to make decisions concerning how well as process is performing. In this case, the process in place at Cranston Nissan was not working, because the customer was never given their car on time and in ideal condition. The operations manager should have noticed the quality of their process was lacking and therefore needed much improvement. Timing was a poor quality that Cranston lacked. From receiving the car to communicating the appropriate time frame to the customer and the customer receiving the car.
The customer was told many times that his car was not ready when it was supposed to be. It kept have to be pushed back a day and then another and then another. Because of the unmanaged supply chain, timing was kept being extended. With each repair and new person who was supposed to fix it, there was a new problem. The quality of the worker output was bad. When it was only supposed to be rust repairs, problems with the security arose, with the speedometer, and even the rear view mirror was detached. The quality of work was very poor and the management if the workers was poor. On September 5th, poor capacity planning is evident. The workshop had too much to do and wasn’t giving this customer the time they deserved. This is another contributing factor to why the timing is bad. The workers could have been working on each job quickly not taking the necessary time each job is really needed to produce the best quality outcome. They work on more, but have low quality service. 2. The lack of an efficient operations manager and service manager. They are not worrying about the quality of their service, but instead are looking to make more money. The need to be expedient was overpowering the true need for quality and customer satisfaction.
However, in this case, the customer was not given expedient service, instead his repairs were being pushed back. Perhaps because of the bad management of the supply chain, the manager was too embarrassed to give the customer the car or tried to cover up the mishaps. It seems as though total quality management was happening here, because all aspects of production are faulty. 3. What needs to be done immediately is the full and necessary repairs for this customer, free of charge. He had to deal with his car being treated wrongfully by the workshop and he hadn’t even driven the car since he turned it in. Customer satisfaction needs to be addressed immediately. A course on customer service would also be beneficial. There is a need for more watchful oversight of the workers and each step in the supply chain, because there are more problems arising because of carelessness. The manager should take time to see each division and see how they work and where there is a need for improvement. If a worker is not following procedure frequently and too careless, then they need to not be apart of the company. There should be monthly, if not bi-weekly reports sent into higher management on the progress of the new policy. In the long term, all the new policies that are implemented are going to be showing their results and frequent check-ins would no longer be as frequent. There will be more customer satisfaction, and new technologies and improvements can be implemented and learned, increasing quality.