Material Handling Equipment Final
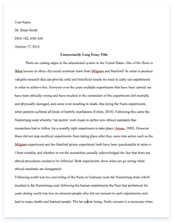
- Pages: 3
- Word count: 523
- Category: Commercial Social Movements Transportation
A limited time offer! Get a custom sample essay written according to your requirements urgent 3h delivery guaranteed
Order NowMaterial handling refers to efficient short-distance movement of goods that usually takes place within the confines of a building such as a plant or a warehouse or between a building and a transportation agency. Material handling equipment is equipment that relate to the movement, storage, control and protection of materials, goods and products throughout the process of manufacturing, distribution, consumption and disposal.
Material handling equipment is used to increase output, control costs, and maximize productivity.
Objectives / Roles
Handling
Receiving
In-storage Handling
Shipping
Material Handling
Principles
1. Planning Principle
2. Standardization Principle
3. Work Principle
4. Ergonomic Principle
5. Unit Load
6. Space Utilization Principle
7. System Principle
8. Automation Principle
9. Environmental Principle
10. Life Cycle Cost Principle
Importance of Material Handling
Equipment
(i) Improve efficiency of a production system by ensuring the right quantity of materials delivered at the right place at the right time most economically.
(ii) Cut down indirect labour cost.
(iii) Reduce damage of materials during storage and movement. (iv) Maximise space utilization by proper storage of materials and thereby reduce storage and handling cost. (v) Minimise accident during materials handling.
(vi) Reduce overall cost by improving materials handling.
(vii) Improve customer services by supplying materials in a manner convenient for handlings. (viii) Increase efficiency and saleability of plant and equipment with integral materials handling features.
Scope of Material
Handling
1. Manufacturing
2. Processing
3. Construction
4. Mining
5. Power
6. Machine Tools
7. Truck building
8. Railroad car builders
9. Barge and Ship building
10. Aircraft
Types
1. Storage and handling equipment
2. Engineered systems
3. Industrial trucks
4. Bulk material handling
5. On-Rails Transfer Cart
6. Conveyors
7. Cantilevered Crane Loading Platform
Belt conveyor
Belt conveyors are capable of handling a wide range of bulk materials
Chain conveyor
A chain conveyor is a type of conveyor system for moving material through production lines.Motor driven chain that drags material along a metal side base.
Flexible Conveyor
Flexible conveyors can be worked around obstacles and keep production lines flowing.
Cranes, Elevators and Hoists
These are overhead devices used for moving varying loads intermittently between points within an area. Cranes –A crane is a type of machine, generally equipped with a hoist, wire ropes or chains, and sheaves, that can be used both to lift and lower materials and to move them horizontally.
Elevators
Elevators –Types of cranes that lift materials –usually between floors or buildings
HOISTS
Ratchet lever hoist
Pulley chain hoist
Construction hoist
Mine hoist
INDUSTRIAL TRUCKSÂ FORKLIFT TRUCK
Counterbalance Trucks
3 Wheel counterbalanceTrucks
Reach Trucks
PALLET TRUCK
1. HAND PALLET TRUCKS
2. POWERED PALLET TRUCKS
Industrial Robot
An industrial robot is defined as an automatically controlled, reprogrammable, multipurpose manipulator programmable in three or more axes. The field of robotics may be more practically defined as the study, design and use of robot systems for manufacturing.
Conclusion
Handling material is a daily function in the workplace. All too often it is a task taken for granted, with little knowledge of or attention to the consequences if done incorrectly.
Operators must be authorized.
Operators must undergo skills Trainings.
Handlers and operators must be trained in safety and health.
Equipment must be regularly inspected and maintained.
Storage areas should have at least two exits.
Should be properly illuminated and ventilated.
Reduce Labour Cost.