Kalabasa lollipop
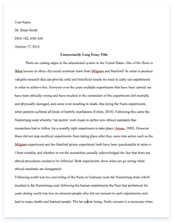
A limited time offer! Get a custom sample essay written according to your requirements urgent 3h delivery guaranteed
Order Now
CHAPTER I
INTRODUCTION
Description of the Project
Kalabasalollipop is the newest lollipop that we have made for this year and available for everybody who want to have experience from our lollipop. Squash are widely grown for commercial use, and are used both in food and recreation. Lollipop is one of the most favorite candy of children and which is attract to many children especially if it has a vitamin contain which is from the squash, we decided to innovate or take a unique flavor which is not already in the market. This lollipop is not for children only it is also available for teenager and for the parents it can tell by its bright color that it’s going to be good for you. Not only squash loaded with vitamin A and antioxidant carotenoids, particularly alpha and beta-carotenes, it’s a good source of vitamins C, K, and E, and lots of minerals, including magnesium, potassium, and iron.  It is one of the very low calorie vegetables. 100 g fruit provides just 26 calories and contains no saturated fats or cholesterol; however, it is rich in dietary fiber, anti-oxidants, minerals, vitamins. The vegetable is one of the food items recommended by dieticians in cholesterol controlling and weight reduction programs. Squash is one of those vegetables that is almost emblematic of fall – it makes us think of harvest, of holidays, of frost, of lengthening nights and the oncoming winter. And yet, the only way it usually gets to the table is in a store-bought pie, or perhaps a can of pie filling that goes in a pie we made ourselves. But squash can be so much more — and since squash keeps for 6 months whole or for years in a can, it can be a year-round addition to our diet.
Brief History
Squash is believed to have originated in the ancient Americas. These early squash were not the traditional round orange upright Jack-O-Lantern fruit we think of today when you hear the word squash. When the air gets a little brisk and the leaves are turning orange, you can almost be certain there will be pumpkins and winter squashes in abundance in North America. They used the sweet flesh in numerous ways: roasted, baked, parched, boiled and dried. They ate squash seeds and also used them as a medicine. The blossoms were added to stews. Dried squash could be stored and ground into flour.
Squash is the one of the vegetables which is commonly use here in the Philippines as main dish we use this in pakbet, ginataangkalabasa, halayangkalabasa, and etc,.Nowadays, Filipinos are being exposed to a lot of information about health issues, cooking shows, new lifestyle, and other trends that will benefit them for their daily living. The kalabasa lollipop is the newest lollipop in the market it contains lots of vitamins which the parents love as alternative vitamins to their children. Even the lollipop is already existing in the market we have to make sure that our lollipop have a good quality and it contain a lots of vitamins which is good to our body and to patronized of many people as their preferred candy.
The Importance of Project
The feasibility helps us how to determine the viability of a business venture in a specific area or sector of business. This is the process that will identify any possible problems that might occur between the acceptance of the product with the consumer and how profitable the business venture might be. A Feasibility study is very important for a business. It makes an analysis of all the aspects of a business. The external factors influencing it and also the internal factors. It also analyzes all the costs associated with the project and how the material would be sourced. On the other hand, it will also make an estimate of how much sales are to be expected and what profits would the project make. If the results of the feasibility study are favorable, it is logical to proceed with it. Whereas on the other hand, if the results are not favorable, no businessman will take a risk on it. Just because a business has a great and needed product for a region, does not necessarily make it a good business opportunity. Not all ideas that make sense are great business opportunities. Like selling water in a desert, since there is a shortage of water, it sounds like a great idea. But since there is very little water present, there is not a population that sustains a living there and sales would not exceed the cost of importing the water to the arid region, this is not a good and viable business venture. What can be learned from a feasibility study can better help a business and a project manager deciding if the business venture will be profitable. In the study, the logistics of the business should be determined.
Business personality
Name of the Company
The proponents decided to go with name K-Pop Food Company with an aim specializing in making a lollipop made of squash. The name of the company which is K-Pop is a pun of the word Kalabasa and Lollipop. The name of the product that will be offer is Kalabasa Lollipop. Product logo
Figure 1
Company Logo
Figure 2
Location
The location of the proposed business is in the City of Mandaluyong, addressed at 222 Shaw Boulevard Corner A. Bonifacio St., Barangay HagdangBatoItaas, City of Mandaluyong. The purpose of the business is to get the buying behavior and to introduce a unique flavored lollipop for the children and the general public who wish to avail the product.The location of the office and facilities of the business is surrounded by many barangays. The City of Mandaluyong is one of the cities and municipalities that comprise Metro Manila in the Philippines. Located at the approximate geographical centre of Metro Manila, it is bordered on the west by the country’s capital, Manila, to the north by San Juan City, to the east by Quezon City and Pasig City, and by Makati City to the south. It is “Metro Manila’s Heart”, and the “Shopping Mall Capital of the Philippines” thus the proponents chose to put the company location at this City. Map Site
Ownership
Table 1
Proponents Names and Addresses
Name
Address
Flores, Catherine V.
G1 3F California Garden Square DM Guevarra St. Mandaluyong City Potenciando, Glory Mae V.
122 7th St. Punta, Sta. Ana Manila
Tolosa, Albert R.
29 Pinatubo St. Brgy. Ilaya, Mandaluyong City
Villanueva, Mistica V.
Blk32 Lt7 Monterra Homes Subd. Bucandala V, Imus Cavite
Ygar, Mendy M.
5C-28 Women’s Club St. Galas Quezon City
The table above shows the name of proponents of the proposed business and their addresses. The proposed venture named as “K-Pop Food Company” will be a Partnership form of organization. The operation of the business will be adopted according to the Partnership Code of the Philippines, and the business will be registered in the Securities and Exchange Commission, Department of Trade and Industry, Bureau of Internal Revenue, and other government agencies necessary to the establishment of the legal personality of the proposed project. A partnership is a strategic alliance or relationship between two or more people. Successful partnerships are often based on trust, equality, and mutual understanding and obligations. Partnerships can be formal, where each party’s roles and obligations are spelled out in a written agreement, or informal, where the roles and obligations are assumed or agreed to verbally. The reason why partnership is chosen by the researchers as the form of organization because it can reduce costs and improve customer service. They can save money through the sharing of facilities, personnel, and office equipment. Partnerships can also be used for cooperative projects such as restoration or maintenance of historic facilities. They may also include services such as complete operation of a visitor’s center.
Objectives
The aim of the business is that it will manufacture nutritious kalabasa lollipop that consumers will soon patronize. It also aims to have a competitive edge among other candy manufacturers that are existing in the market. The objective of the study is to determine if the manufacturing of
kalabasa lollipop will sell out to consumers. For the long range objectives of this project, the researchers visualized the firm of expanding its distribution channel and be known in the world of business.
Capitalization
The figures below show the total project cost, detailed organization cost and detailed working capital of the proposed business.
K-POP COMPANY
Initial Project Cost
Initial Cash Outlay
Pre-Operating Expenses
Legal Requirements
DTI 800.00
BIR 900.00
SEC (1/5 of 1% of the capital) 5,000.00
Mayor’s Permit
(BFAD, Sanitary Permit, Fire Insp.) 7,800.00
Allowance 500.0015,000.00
Connection of
Electricity 3,000.00
Water 1,000.00
Communication1,500.00
Advertising 20,000.0040,500.00
Machineries &Equipment, and Kitchen Tools104,000.00
Furniture & Fixtures 37,650.00
Rental Deposit 20,000.00
Delivery Equipment200,000.00
Store Supplies 6,000.00
Office Supplies 2,500.00
Working Capital (for one week)
Salaries 9,560.00
Materials 19,500.00
Some Operating Expenses 5,000.00
Total444,710.00
Initial Cash on Hand1,055,290.00
Sources of Financing
The investments of the proponents will come from their very supportive family and upon their own resourcefulness. Ms. Flores and Mr. Tolosa’s contributions will come from their bank savings. Ms. Potenciando’s contributions will come from her own savings. Ms. Villanueva and Ms.Ygar’s capital will come from the income of their family business.
Gantt Chart of Activities
CHAPTER II
MARKETING ASPECT
The proposed business belongs to the food manufacturing business. The company will offer a product known as kalabasa lollipop, which has a unique flavor compare to other existing candies. The proponents chose this particular side of the industry because of the basic assumption that there is always a necessity or demand for food. The proposed business will introduce kalabasa lollipop that are cheaper, and of higher quality. The more important consideration in marketing kalabasa lollipop is the growing health-consciousness among Filipinos, especially the growing children. Squash are essentially part of a “healthy” cluster of food ingredients common to Filipino diet staples. And with the enhancement of squash flavor lollipop, a simple candy will be more made even tastier.The proposed business will provide an alternative solution to those children who do not eat squash. It does not only satisfy their enjoyment but also this product will benefit the children because this simple candy contains an extraordinary nutrients such as carotenoids and flavonoids which can provide protection from cancer. Many candy products has been growing nowadays without even thinking the welfare of their consumers especially the children whose from the start were not aware of what will be the result of eating such. That is why we came up to this proposed idea of making a kalabasa lollipop to ensure the satisfaction of our consumer.
Target Market
The target market of the product will be the children. However, the proposed business will not only limit its market to the children because regardless the age, candy is a necessity. The proposed business is also for the children to get nutrients even in candies. Consumers from other locations can also buy the product from groceries, supermarkets, and retailers that wish to distribute or sell the product to other individuals.
Demand Analysis
Companies use market demand analysis to understand how much consumer demand exists for a product or service. This analysis helps companies to determine if they can successfully enter a market and generate profits. As an essential part of project formulation and appraisal, market and demand analysis is vital so that capacity and facility location can be planned and implemented in line with the market requirements.
Historical Demand
To estimate the demand the proponents made use of target market’s historical and projected population as basis.
The table below shows the historical population in past five years of Mandaluyong City.
Table 1
Historical Population of Mandaluyong City
YEAR
POPULATION
2008
317,719
2009
323,209
2010
328,699
2011
334,189
2012
339,679
The above table shows the increase in the population of Mandaluyong every year by 1.67%, since NSO has only year 2010 that has 328,699 population updated data, the group considered its growth rate which is 1.67% to get the increase on the succeeding years. In order to project the population for 20011 to 2012, the group considered the annual growth rate which is 1.67%. Source: National Statistic Office,Republic of the Philippines.
The table below shows the Estimated Projected Population of Mandaluyong City. Table 2
Estimated Projected Population
YEAR
Average Annual Increase
POPULATION
2013
1.67%
345,169
2014
1.67%
350,659
2015
1.67%
356,149
2016
1.67%
361,639
2017
1.67%
367,129
2018
1.67%
372,619
The above table show the estimated projected population based on the annual
population growth rate which is 1.67%. This figures came from multiplying the average annual increase to the 2012 population and then add it on the data 339,679 to get 2013 population. Same process was done to the year 2014 up to 2018.
The table below shows the projected demand based on projected population and survey questions answered by respondents.
Table 3
Projected Demand
Year
Population
Projected Demand
2013
345,169
202, 960
2014
350,659
206, 188
2015
356,149
209,416
2016
361,639
212,644
2017
367,129
215, 872
2018
372,619
219, 100
Source: Answered survey of the respondents, IlayaBarangka Integrated School
Mandaluyong City The demand indicated in the table above was based on the assumption demand equal to the population multiplied by the percentage of respondents who are “Willing to taste squash-flavoured lollipop” then the percentage of respondents who have “Not heard of taste squash-flavoured lollipop, since it is not yet existing in the market ”. Projected demand was estimated by multiplying the projected population by 70% as the people who “have not heard” of which 84% are “willing to try”.
Where:
*Current population345,169
*Percentage of respondents
Who are “willing to taste squash- flavoured lollipop”.84% *Percentage of respondents who “have not
heard of squash-flavoured lollipop”.70%
Supply Analysis
A detailed review of the inputs and outputs of a process that is employed to assess how the available quantity of a product is affected by changes in demand, input factors and production techniques. Supply analysis is often used to make key policy decisions by manufacturing business managers since it gives them insight into how shifts in production are likely to influence market supply.
Table 4
Projected Supply of Competitors
Year
Star Pops
Frooty Pops
Total
2013
71,056
64,627
135,683
2014
72,243
65,707
137,950
2015
73,450
66,805
140,255
2016
74,677
67,921
142,598
2017
75,925
69,056
144,981
2018
77,193
70,210
147,403
The above table shows the projected supply of the two considered direct competitors of kalabasa lollipop which are the Universal Robina Corporation Star pops and Columbia’s Frooty Pops.
Note: *The competitors projected supplies are sale of packs annually*
The proponents projected the supply of competitors by getting the estimated annual sale of bottles to each of the competitors’ merchandiser. For the Universal Robina Corporation Star pops its annual sale of packs is 68,740 for the year 2011 that includes three other different stores that they are supplying. For Columbia’s Frooty Pops, its annual sale of packs is 62,520 for the year 2011 that includes two other different stores that they are supplying. To get the projected supply of each competitors for succeeding
years, the group considered the population growth rate which is 1.67%.The year 2011 sale and multiplied by 1.67%. The increase in the supply is based on the percentage increase in the population growth. Both competitors are supplying to other different stores that are located in Mandaluyong City.
Demand-Supply Analysis
Table 5
Demand and Supply Analysis
Year
Demand
Supply
Unfilled Demand
Projected Sales
Market Share
2013
202, 960
135,683
67,277
54,000
26.64%
2014
206,188
137,950
68,238
57,600
27.94%
2015
209,416
140,255
69,161
61,200
29.22%
2016
212,644
142,598
70,046
64,800
30.47%
2017
215,872
144,981
70,891
68,400
31.69%
2018
219,100
147,403
71,697
72,000
32.86%
The table above shows the Demand and Supply Analysis
*Assumption: Maximum of 200 packs of Kalabasa Lollipop per day.
The projected sales were based on the capacity of the business to supply the number of demand. Since the business has a maximum capacity to produce 200 packs of kalabasa lollipop, a day multiplied by the number of working days a year which is 360, the maximum projected sales for a year is 72,000 packs of kalabasalollipo. Since the business is new in the market, the proponents assumed to supply only 75% of the maximum projected sales for the first year, 80% on the second year, 85% on the third year, 90% on the fourth year, 95% on the fifth and 100% on the last year. The unfilled demand was computed
from the difference between demand and supply. The Market Share was computed by dividing the annual projected sales over the total demand multiplied by 100
Marketing Program
Product
The Kalabasa Lollipop has a unique taste and its flavor is more pronounced and enhanced. It will then add to a local traditional food of lollipop that the children are most likely where squash is a main ingredient. The brand Kalabasa Lollipop was chosen by the proponents for the proposed product since the product is kalabasa lollipop, it is very simple word yet capturing and can be easily remembered by connecting it to squash and lollipop. It is important to considered the packaging and labeling design of the product to ensure that the product will be appealing, capturing and benefits its consumers. The package design of a certain product greatly affects its marketability. There are a lot of means to package a product: plastic containers, and wrappers, paper wraps, and so on. Packaging serves as the protection of its content from spoilage, exposure to other elements like bacteria, molds, dirt and other matters that can affect the quality of the product. Another purpose of packaging is for the storage of its content, especially for the sake of the consumers, on how they will store the product for future consumption. Since the proposed business will be into the manufacturing of squash lollipop, it is important to consider how the product will maintain its freshness and quality for a longer period of time.
Price
Kalabasa that are in the market nowadays are affordable. Consumers still have demand for vitamins that they get from lollipop made from squash. Producing kalabasa lollipop can have a big advantage on the price compared to its competitors. The price is a little bit higher than its competitor because of its added flavor which is squash. After conducting interview and price checking of the raw materials, equipment, labor, water, etc., the proponents were able to compute the market price of the product. In the projection of the annual cost of raw materials, the group considered a 200% mark-up and 2% average inflation rate, which will directly increase the price of the
product every year. To deal with the difficulty on how the product is availed, the group came up with a decision that the basis in availing the product is by pack, each pack of kalabasa lollipop has a standard size of 250 grams per pack.
Table 7
K-POP Market Price
Product
Market Price
Product Cost
Mark-Up
K-POP
P 35.00
P 17.50
200%
The table above shows the computed price of kalabasa lollipop.
The market price was computed by multiplying the product cost by 200% mark-up. The Product Cost was computed as follows:
Table 8
Product Cost
Unit
Quantity
Unit Price
Amount
Squash
grams
4
P 0.3125
P 1.25
Sugar
grams
12.5
P 0.06
P 7.50
Cream of Tartar
tsp
3
P 0.75
P 2.25
Lollipop Stick
pc.
20
P 0.1625
P 3.25
Wrapper
pc.
20
P 0.1625
P 3.25
Total
P 17.50
Table 9
Competitors’ Price
Frooty Pops
Starpops
Distributor
Columbia’s
Universal Robina Corp.
Price
P 25.00
P 25.00
Net weight
188g/pack
210g/pack
The table above shows the Competitors’ Price
The table below shows the projection in the increase in price and sales of the proposed business based on the assumption of 2% increase in price and the percentage capacity of candies to produce the product per year and for succeeding years.
Table 10
Projected Sale 2013
Product
Price per pack
Average daily sales
Average Monthly Sales
Average Annual Sales
Total Sales w/ Vat
Kalabasa Lollipop
P 35.00
200
4,000.00
48,000
1,680,000
The table above shows the total projected sale for the first year operation of the proposed business, since the business assumed to supply 80% of its maximum capacity to produce kalabasa lollipop, the total projected sales will be P 1,680,000.00. The total sales was computed by multiplying the price per pack of kalabasa lollipop to its average annual sales. Table 11
Projected Sale 2014
Product
Price per pack
Average daily sales
Average Monthly Sales
Average Annual Sales
Total Sales w/ Vat
Kalabasa Lollipop
P35.70
212.50
4,250.00
51,000.00
P1,820,700
The table above shows the total projected sale for the second year operation of the proposed business, since the business is in the second year it assumed to supply 85% of its maximum capacity to produce kalabasa lollipop ,the total projected sale will be P 1,820,700.00. The increase in price was based on the assumption of 2% increase in price annually. Table 12
Projected Sale 2015
Product
Price per pack
Average daily sales
Average Monthly Sales
Average Annual Sales
Total Sales w/ Vat
SUNMATO
P 36.41
225
4,500
54,000
P1,966,140
The table above shows the total projected sale for the third year operation of the proposed business, since the business is in the third year it assumed to supply 90% of its maximum capacity to produce kalabasa lollipop. The total projected sale will be P 1,966,140. The increase in price was based on the assumption of 2% increase in price annually. Table 13
Projected Sale 2016
Product
Price per pack
Average daily sales
Average Monthly Sales
Average Annual Sales
Total Sales w/ Vat
Kalabasa Lollipop
P 37.14
237.50
4,750
57,000
P2,116,980
The table above shows the total projected sales for the fourth year operation of the proposed business, since the business is in the fourth year it assumed to supply 95% of its maximum capacity to produce kalasaba lollipop. The total projected sale will be P2, 116,980. The increase in price was based on the assumption of 2% increase in price annually. Table 14
Projected Sale 2017
Product
Price per pack
Average daily sales
Average Monthly Sales
Average Annual Sales
Total Sales w/ Vat
Kalabasa Lollipop
P 37.88
250
5,000
60,000
P2,272,800
The table above shows the total projected sale for the fifth year operation of the proposed business, since the business is in the fifth year it is assumed to supply its maximum capacity which is 100% or 200 packs of kalabasa lollipop. The total projected sales will be P 2,272,800. The increase in price was based on the assumption of 2% increase in price annually.
Place
Channels of distribution
Location for setting up a lollipop manufacturing plant has imperial implications on fixed costs, operational costs and procedures. In food manufacturing industry, it is important to identify what business establishment, will serve as a link from the producer to the end users. There are many ways to distribute a certain product to consumers, it can be through the retailers, groceries, supermarkets, or even by direct selling the product to the consumers. The channels of distribution will serve as path in which the product is taken from the time it was produced to the point that it will be purchased. In addition, a location should be chosen from where business operations like production and distribution can be performed quickly with low operational cost. In distributing the product, it will be more convenient for the business to deliver the product to retailers such as grocery stores, supermarkets, and specialty stores. The location of the business is an advantage for the reason that it is located in the City of Mandaluyong, Acacia Lane, which is accessible to most cities and other municipalities in the Metro Manila area.
Distribution Process
Consumers or end users can buy the product from retailers, such as grocery stores and specialty stores, in which the business will deliver the products to this establishments. Consumers within the vicinity of the location can also buy directly in the location of the business. The distribution process will start from the business location where the product will undergo the manufacturing process, and to be delivered to the establishments who wish to sell the product.
Promotion
Marketing and promotional activities will be critical in the success of any newly introduced kalabasa lollipop brand; however, it takes years to establish brand equity which is highly dependent on electronic media and a continuous and persistent follow-up media campaign. Television and Radio have the most in depth penetration in the consumer market and companies
usually use these two electronic mediums for the promotion of their products; however these are also high cost options for product promotion and a new business entrepreneur will be constrained to afford this cost. The product will have an interesting packaging that includes recipes with the product as the main featured ingredient. The business is at its initial stage of the operation and it is working under a limited budget but the partners are aware of the importance advertising and promotion plays in business that is why we allotted a considerable amount of money to these activities.
CHAPTER III
TECHNICAL ASPECT
Product Description
The proposed business will be in line with food manufacturing wherein the company will locally produce Kalabasa Lollipop. Lollipop is one of the most favorite candy of children and which may attract children especially if it has a vitamin contain which is from the squash, the proponents decided to innovate or take a unique flavor which is not available in the market. The proposed business will provide an alternative solution to those children who do not eat squash. It does not only satisfy their enjoyment but also this product will benefit the children because this simple candy contains extraordinary nutrients such as carotenoids and flavonoids which can provide protection from cancer. Properties of the Product
Kalabasa Lollipop is made up of mashed squash that will provide an alternative solution to those children who do not eat squash. It does not only satisfy their enjoyment but also this product will benefit the children because this simple candy contains extraordinary nutrients such as carotenoids and flavonoids which can provide protection from cancer.
Compared to other existing lollipops, kalabasa lollipop is a brilliant source of vitamin C and a very good source of magnesium, vitamin A. It is also abundant in potassium, providing 345.60 milligrams per serving. Potassium is a key electrolyte in the balance of fluids and also provides muscle energy. Process
Manufacturing Process Flowchart
The flowchart will show the process of manufacturing KALABASA LOLLIPOP. Manufacturing Process Flowchart
Description of the Process
The product will definitely be all natural, organic, and additive free. The following will be the ingredients in the production of Kalabasa Lollipop: Mashed squash
Sugar
Cream of tartar
Water
The following are the procedures to be follow.
1. Hand-picked and wash squash.
After the squash has been delivered, it should be hand-picked to ensure that the squash that will be used in producing kalabasa lollipop are not damage. The chosen squash should be washed properly. 2. Peelingand slicing of the squash.
After peeling the squash, slice it into pieces so that it can be easily mashed after boiling. 3. Placing the squash into a crockpot and simmer it until it gets soft. The sliced squash should be put into a crockpot with water and then simmer it for a couple of minutes until it gets soft and ready to mash. 4. Set the table and prepare the things and the ingredients needed. All the things and ingredients needed must put on a clean table for orderliness. 5. Combine the ingredients, wait until it cooks and put it into the molds. Combine the sugar, mashed squash, milk and water in a crockpot over medium-high heat. Stir until the sugar dissolves, then brush down the sides of the pan with a wet pastry brush. . Allow to boil, without stirring, until candy gets the desired texture. When caramelized, remove from heat. Prepare the molds by spraying them with nonstick cooking spray and inserting lollipop sticks into the molds. 6. Cooling and removing from molds.
Spoon the candy into the mold cavities, making sure to cover the back of the stick. Allow cooling completely and remove once hardened.
7. Packaging
A plastic pack will be used as a packaging of the kalabasa lollipop. The vacuum sealer will ensure that all the air content will be removed from the pack, and it will maintain the quality of the lollipop. 8. Distribution
Before delivering the finished lollipops, it should be inspected to avoid any damage.
Production Processes and Controls
K- Pop Company will carry out production processes and control from receiving the raw materials and supplies to the extent of the machines &equipments and kitchen tools to be use in producing Kalabasa lolliop to ensure that the product will be process and produce with qualityand control measures. All operations in the receiving, inspecting, transporting, segregating, preparing, manufacturing, packaging, and storing of food should be conducted in accordance with adequate sanitation principles. There shall be appropriate quality control operations procedures to ensure that food is suitable for human consumption and that food-packaging materials are safe and suitable. All reasonable precautions should be taken to ensure that production processes do not contribute contamination from any source. All food that has become contaminated to the extent that it is adulterated within the meaning of the act shall be rejected, or if permissible, treated or reprocessed to eliminate the contamination. To prevent problems, which could affect consumer safety or satisfaction, each line must be under control. Hazard and root cause analyses must be used to specify control measures: Critical Control Points (CCPs) for food safety and Control Points (CPs) for consistency. Raw Materials and Other Ingredients
There shall be procedures and work instructions for the sanitary handling of raw materials and other ingredients. Raw materials and other ingredients shall be inspected and either segregated or otherwise properly handled to ascertain that they are clean and suitable for processing into food. Raw materials shall be stored under conditions that will protect against contamination and minimize deterioration. Containers and carriers of raw materials shall be inspected on receipt to ensure that their condition has
not contributed to the contamination or deterioration of food. Raw materials and other ingredients shall either not contain levels of microorganisms that may produce food poisoning or other disease in humans, or they shall be pasteurized or otherwise treated during manufacturing operations so that they no longer contain levels that would cause the product to be adulterated within the meaning of the act. Compliance with this requirement shall be verified by any effective means, including purchasing raw materials and other ingredients under a supplier’s guarantee or certification. Rework items shall be held in bulk, or in containers designed and constructed so as to protect against contamination and shall be held in a manner that will prevent the food from becoming contaminated within the meaning of the act. Material scheduled for reprocessing shall be identified as such. Manufacturing Operations
Procedures and work instructions shall be established for the sanitary handling and maintenance of machines & equipment and kitchen tools for manufacturing operations. Machines & equipment and kitchen tools and finished food containers shall be maintained in a sanitary condition through appropriate cleaning and sanitizing. Where appropriate, machines & equipment shall be taken apart for thorough cleaning. Food that can support the rapid growth of undesirable microorganisms, particularly those of public health significance, shall be handled in a specified manner that prevents the food from becoming contaminated within the meaning of the act. Work-in-process shall be handled in a manner that protects against contamination. Finished food should not be handled together with raw materials, other ingredients, or refuse in a receiving, loading, or shipping area if that handling could result in contaminated food. Food transported by conveyor shall be protected against contamination. Sieves, traps, magnets, electronic metal detectors, and other suitable means should be used to protect against the inclusion of metal or other extraneous material in food. Glass, foreign matter should likewise be prevented from contaminating food by exclusion of the use of breakable glass as processing machines & equipment, sampling containers, laboratory glassware, etc. in production areas. If use of breakable glass in production areas cannot be avoided, as in the case where packaging material is glass, there should be a procedure on how to deal with broken glass in
food. Food, raw materials, and other ingredients that are adulterated/ contaminated within the meaning of the act shall be disposed of in a manner that protects against the contamination of other food. Adulterated/ Contaminated food opted to be reconditioned shall be reprocessed using a method proven to be effective and shall be tested as non-adulterated or non- contaminated within the meaning of the act, before being incorporated into other food. Physical protection of food from contaminants that may drip, drain, or be drawn into the food during operations like washing, peeling, trimming, etc. shall be done properly to protect food against contamination. Protection may be provided also by adequate cleaning and sanitizing of all food-contact surfaces, and by using time and temperature controls at and between each manufacturing step. Filling, assembling, packaging, repacking and other operations shall be performed in a manner that protects food against contamination by any effective means. Food such as, but not limited to, acid and acidified food, that relies principally on the control of pH for preventing the growth of undesirable microorganisms shall be monitored and maintained at a pH of 4.6 or below. Ice used in contact with food shall be made from potable water and shall be manufactured, stored and handled in accordance with good manufacturing practice. Steam used in contact with food must be of food grade quality. Make-up water shall be potable and comply with current food legislation standards. Food-manufacturing areas and machines & equipment used for manufacturing human food should not be used to manufacture nonhuman food grade animal feed or inedible products, unless there is no reasonable possibility for the contamination of the human food. All food manufacturing establishments using one or several critical allergens as ingredients shall take all reasonable precautions to avoid cross contact of products that do not normally contain these allergens and that do not normally carry a specific mention in the ingredient statement.
MACHINES, EQUIPMENT, AND KITCHEN TOOLS
Machines andequipment and kitchen tools directly utilized for food manufacture shall be designed and constructed using materials that can be easily and adequately cleaned and maintained. Machinery and other workplace equipment can be dangerous if not used properly. Anyone using equipment in the workplace needs to be thoroughly trained in its operation and kept up to
date. Designs and Specifications
The following are the machines, equipment, and kitchen tools that will be used in the production of Kalabasa Lollipop. Machines, Equipment and Kitchen Tools
Vegetable strainer – use for draining the washed squash.
Knife – used for slicing the squash.
Wooden ladle – used for stirring the mixture.
Mash squash machine – use to mash the squash.
Non-stick crockpot – it is where all the ingredients are being mixed.
Lollipop moulds and sticks – use to shape the desired lollipop.
Kitchen weighing scale – use for weighing kalabasa lollipop in packing process.
Gas stove – use for boiling the squash and cooking the candy mixture.
Digital weighing scale – use in checking the weight of the delivered orders of squash.
Sugar thermometer – use for checking the temperature of the candy mixture.
Vacuum sealer – use in packing kalabasa lollipop to remove air content inside the pack.
Vegetable peeler – use for peeling the squash.
Cutting board – use for cutting and slicing the squash.
Stainless table – where all the ingredients will be put.
Figure 5
Cost of Machines, Equipment, and Kitchen Tools
The machines, equipment, and kitchen tools described in the previous pages shall be used for processing Kalabasa Lollipop. Below shows the list of each and quantity needed for the production and their respective unit price. Table 15
Production Machines, Equipment, and Kitchen Tools, Quantity and Unit Price Machines, Equipment and Kitchen Tools
Quantity
Unit Price (Php)
Total Cost (Php)
Vegetable strainer
3
150.00
450.00
Knife
3
100.00
300.00
Wooden ladle
5
100.00
500.00
Mash squash machine
3
6,950.00
20,850.00
Non-stick crockpot
5
500.00
2,500.00
Lollipop moulds
20 sets
130.00
2,600.00
Lollipop sticks
5 packs
200.00
1,000.00
Lollipop wrapping kit
5 packs
150.00
750.00
Kitchen weighing scale
2
850.00
1,700.00
Gas stove
1
3,500.00
3,500.00
Digital weighing scale
1
3,250.00
3,250.00
Sugar thermometer
2
800.00
1,600.00
Vacuum sealer
1
2,500.00
5,000.00
Vegetable peeler
15
60.00
900.00
Cutting board
6
250.00
1,500.00
Stainless table
3
2,000.00
6,000.00
Centralized Computer Network (4 users)
1
20,000.00
20,000.00
A/C unit
2
20,000.00
20,000.00
Computer Printer
2
3,000.00
6,000.00
Cash Register
1
4,00.00
4,000.00
Fire Extinguisher
1
800.00
800.00
LPG
1
800.00
800.00
Total Costs of Machines, Equipment and Kitchen Tools
104,000.00
Life Span and Depreciation Costs of Machines, Equipment and Kitchen Tools
The machines, equipment and kitchen tools use for the production of Kalabasa Lollipop are estimated to have five (5) usable/productive years. The business used the formula below in determining the estimated annual depreciation of the equipment and utensils.
Depreciation cost = Cost of machines and equipment
Estimated life span (in years)
The following table will show the life span and estimated annual depreciation of each.
Table 16
Production Machines, Equipment, and Kitchen Tools with Corresponding Estimated Annual Depreciation Costs
Machines, Equipment and Kitchen Tools
Quantity
Unit Price (Php)
Total Cost (Php)
Estimated lifespan (years)
Depreciation (Php)
Vegetable strainer
3
150.00
450.00
5
90.00
Knife
3
100.00
300.00
5
60.00
Wooden ladle
5
100.00
500.00
5
100.00
Mash squash machine
3
6,950.00
20,850.00
5
4,170.00
Non-stick crockpot
5
500.00
2,500.00
5
500.00
Lollipop moulds
20 sets
130.00
2,600.00
5
520.00
Lollipop sticks
5 packs
200.00
1,000.00
5
200.00
Lollipop wrapping kit
5 packs
150.00
750.00
5
150.00
Kitchen weighing scale
2
850.00
1,700.00
5
340.00
Gas stove
1
3,500.00
3,500.00
5
700.00
Digital weighing scale
1
3,250.00
3,250.00
5
650.00
Sugar thermometer
2
800.00
1,600.00
5
320.00
Vacuum sealer
1
2,500.00
5,000.00
5
1,000.00
Vegetable peeler
15
60.00
900.00
5
180.00
Cutting board
6
250.00
1,500.00
5
300.00
Stainless table
3
2,000.00
6,000.00
5
1,200.00
Centralized Computer Network (4 users)
1
20,000.00
20,000.00
5
4,000.00
A/C unit
2
20,000.00
20,000.00
5
4,000.00
Computer Printer
2
3,000.00
6,000.00
5
1,200.00
Cash Register
1
4,00.00
4,000.00
5
800.00
Fire Extinguisher
1
800.00
800.00
5
160.00
LPG
1
800.00
800.00
5
160.00
Total Depreciation Costs of Machines, Equipment and Kitchen Tools 20,800.00
The above table shows the Production Machines, Equipment, and Kitchen Tools with Corresponding Estimated Annual Depreciation Costs Furniture and Fixtures
In producing Kalabasa Lollipop, the Administrative department of K-POP Food Company will not function without the facilities that are important in the business. The following table will show the list, quantity and unit price of each furniture and fixtures that will be needed by the business. Table 17
List of Furniture and Fixtures Quantity and Prices
Furniture & Fixtures
Quantity
Unit Price (Php)
Total Cost (Php)
Locker
1
4,000.00
4,000.00
Sofa (4 seaters)
2
5,000.00
10,000.00
Office Table
5
1,700.00
8,500.00
Office Chair
5
1,700.00
8,500.00
Monobloc Chair
12
300.00
3,600.00
Monobloc Table
3
200.00
600.00
Bulletin Board
1
250.00
250.00
Filing Cabinet
1
2,200.00
2,200.00
Total Costs of Furniture & Fixtures
37,650.00
The table above shows the List of Furniture and Fixtures Quantity and Prices
The following table shows the depreciation costs of furniture & fixtures of the business. The formula use in getting the estimated annual depreciation is the same with the formula use for the machines, equipment and kitchen tools for producing Kalabasa Lollipop. Table 18
Furniture & Fixtures with corresponding Estimated Annual Depreciation Costs Furniture & Fixtures
Quantity
Unit Price (Php)
Total Cost (Php)
Estimated life span (years)
Annual Depreciation (Php)
Locker
1
4,000.00
4,000.00
5
800.00
Sofa (4seaters)
2
5,000.00
10,000.00
5
2,000.00
Office Table
5
1,700.00
8,500.00
5
1,700.00
Office Chair
5
1,700.00
8,500.00
5
1,700.00
Monobloc Chair
12
3000.00
3,600.00
5
720.00
Monobloc Table
3
200.00
600.00
5
120.00
Bulletin Board
1
250.00
250.00
5
50.00
Filing Cabinet
1
2,200.00
2,200.00
5
440.00
Total Depreciation Costs of Furniture & Fixtures per year
7,530.00
The above table shows the Furniture & Fixtures with corresponding Estimated Annual Depreciation Costs.
BUILDINGS
Designs and Specifications
The office and production facilities is on the 1st floor of the building. The first floor will be used mainly for the production purposes of the business and it is divided into five 5 areas. The first area will be the place where the public can be entertained, and where they can directly buy the product. The Production Supervisor’s office is also located in this area in which it has a clear view towards the production area. Right beside the Production’s Supervisors office will be the huddle room. Conferences, meetings, conversations with VIPs, wholesalers, retailers, job applicants, and other important individuals, will be held in this room. The second area in the first floor is the production area. This is where the production process will take place, and it is where the employees lockers and baths are located. An air-lock is provided for lesser exposure of the room. The third is the delivery area, where all raw materials that will be used will be unloaded. The security guard’s room is also located in this area, for the checking of what will be brought inside the facility. The stockroom is also located in this area that it can directly see the raw materials that will be used. The fourth area will be the breakout area. This area will serve as the eating place for the employees, and all the individuals that are involved in the business including the partners themselves. Coffee breaks
can also be held in this area. The fifth area in this facility is the drying area. This is where the kalabasa will be mashed. The mashing area has a clear view from the production area.
Store Layout
Costs of Building
The proposed business decided to rent a space that will be the main office and production area as well. The said space has an old building that is suitable for the production of Kalabasa Lollipop and fits the features and areas that the plan layout and dimension contains. It is agreed between the partners and the space owner a P 12,500.00 (twelve thousand five hundred pesos) monthly rental with 2 months deposit which cost P 25,000.00 (twenty five thousand pesos). It is also agreed that the rent can be paid at the end or at the beginning of each year, which is annual payment and it will cost for P 150,000.00 (one hundred fifty thousand pesos). *The renovation cost of the building will not be shoulder by the partnership, instead the space owner will be the responsible for the renovation of the building with accordance to the preference of the proponents.
Utilities
The operation of the proposed business will not be possible without the other services that other businesses offer. The services needed for the business are the power services, telecommunications, and water. For the power services, it will be provided by Manila Electric Company, or also known as MERALCO. Telephone line and Broadband Internet connection will come from PLDT., and the water supply shall be provided by Manila Water Company. The following are the services for power, water and telecommunication with their corresponding costs of installation and service provider.
List of Utilities and Service provider with corresponding Installation Cost Utilities
Service Provider
Cost of Installation (Php)
Water
Manila Water Co.
1,000.00
Electricity
MERALCO
3,000.00
Communication
PLDT
1,500.00
Total
5,500.00
The table above shows the List of Utilities and Service provider with corresponding Installation Cost.
PLANT LOCATION
Address and Map
The offices and production facilities of the proposed business is located at222 Shaw Boulevard Corner A. Bonifacio St., Barangay HagdangBatoItaas, City of Mandaluyong.The location of the office and facilities of the business is surrounded by many barangays.
The following shows the site map of the business’s location.
Map Site
The following figure will be perspective view of the proposed business. The business name K-POP Food Company and logo will appear at the front of the building. There will also be space for customer’s vehicles. Perspective View of K-POP Food Company
Transportation Facilities
The proposed business will purchased a second hand delivery vehicle to use for purchasing raw materials, supplies needed and delivery of Kalabasa Lollipop. The following table will show the purchased cost of this transportation facility and its estimated annual depreciation cost. Table 20
Transportation Facility Cost with corresponding Estimated Annual Depreciation Cost Transportation Facility
Quantity
Cost (Php)
Estimated life span (year)
Annual Depreciation Cost (Php)
Delivery Vehicle
1
200,000.00
5
40,000.00
Total Estimated Depreciation Cost of Delivery Vehicle
40,000.00
The above table shows the Transportation Facility Cost with corresponding Estimated Annual Depreciation Cost
Accessibility to Suppliers and Market
The location of the proposed business is very accessible to the target markets and for the suppliers as well. Since Mandaluyong City is located right at the center of Metro Manila, it is called “Metro Manila’s Heart”. Mandaluyong City is bordered on the west by the country’s capital, Manila, to the north by San Juan City, to the east by Quezon City and Pasig City, and Makati City to the south. K-Pop Food Company is a few meters away from the Mandaluyong City Hall and Divine Mercy Church and also to different schools like Jose Rizal University and Good Shepherd Christian School where the parents or guardians of the children can visit K-Pop Food Company and purchase Kalabasa Lollipop. The business will also supply to the selected supermarkets and retailers around the city so that the customers will be able to purchase Kalabasa Lollipop to their nearest supermarket for more convenience.
RAW MATERIALS AVAILABILITY
Raw Materials, Supplies, and Their Sources
The different raw materials needed for the production of KALABASA LOLLIPOP will be for the ingredients of kalabasa lollipop and for the packaging.
For the kalabasa lollipop, the raw materials or ingredients for its production process are native squash which would be bought per basket, for P300.00, where the net weight of one box is 20 (twenty) kilograms. It is readily available from vegetables dealers from Pampanga to “AlingPuring” at Kalentong wet market which will be the supplier of the business. Kalabasa has a year-round availability so there will be no shortage for its need in the production process. However, during peak supply months, the price of kalabasa goes down, and if the supply is low and the demand is high, the price per basket rises. The other ingredients are sugar, which will be purchased by kilogram or per sack. The raw materials for the packaging will be the plastic seal made for automatic bunch machine . The plastic seal for the automatic bunch sealing can be purchased from many manufacturers or distributors which will be purchased at P1.00 per plastic.
In purchasing all the raw materials needed for the product, the business will ensure that all materials meet the required standards for food manufacturing industry. The partners will ensure that the suppliers and K-pop will have a good business relationship as well as partnership.
Another are the office supplies that needed by the business to perform, plan and record all the transactions of the business. The estimated budget on these stuffs would be P2, 500.00 which includes bond papers, envelops pencils and ball pens, timecards, record books, folders and others.
And lastly, to keep the cleanliness and maintenance of the business, cleaning materials are necessary. P12, 000.00 will be the estimated budget for these materials.
PRODUCTION FORECAST
K-POP Food Company aims to produce and distribute a minimum of 250 packs of Kalabasa Lollipop per day. The operation of the business is five (5) days a week, the production of Kalabasa Lollipop will be 1250 packs (5 days x 250 packs/day) in a week. For the monthly production, the business can supply 5000 packs (4 weeks in a month x 1250 packs/week). And in a year, the business can produce 60000 packs of Kalabasa Lollipop (12 months in a year x
5000 packs/month). Since the business is new in the market, the proponents assumed to supply only 80% of the maximum projected production in the first year. In the following years, it is presumed that the ability to supply the number of demand will increase 5% yearly, hence, 85%, 90%, 95%, the respectively. In other words, at the first year, only 48,000 packs will be supplied for the customers, 51,000 packs for second year, 54,000 packs for third year, 57,000 packs for its fourth year and 60,000 packs for the fifth year.
Chapter IV
ORGANIZATION AND MANAGEMENT ASPECT
FORM OF BUSINESS ORGANIZATION
First thing to consider in starting a business is the form of business to be use. It is hard to enter a business if you cannot identify what form of business is going to use.Determining the form of organization is very important before doing any kind of business, including acquiring property and equipment, hiring employees, leasing space, borrowing money or acquiring capital, having a license or franchise, and so on. The proposed business which is “K-Pop Food Company” chose the partnership as its form of business organization. The operation of the business will be adopted according to the Partnership Code of the Philippines, and the business will be registered in the Securities and Exchange Commission, Department of Trade and Industry, Bureau of Internal Revenue, and other government agencies necessary to the establishment of the legal personality of the proposed project. The form of business organization which is partnership will be used since there will be five (5) parties involve in starting to the business. The contribution of each partner will be an equal amount which serves as initial capital of the proposed business.
The table below shows the contribution of each partner.
Table 21
Contribution table
Name of Parners
Nationality
Type of Partner
Contribution
Catherine V. Flores
Filipino
General Partner
Php300,000
Glory Mae V. Potenciando
Filipino
General Partner
Php300,000
Albert R. Tolosa
Filipino
General Partner
Php300,000
Mistica V. Villanueva
Filipino
General Partner
Php300,000
Mendy M. Ygar
Filipino
General Partner
Php300,000
The Table above shows the Contribution Table of each partner. Partnership is easier to administer compare to corporation and it is less expensive to set up. In partnership, each partner, is a general partner. A general partner is personally liable in to the business up to its personal property. Before explaining why partnership is the form of business for the proposed business, it is important to explain what partnership is. Partnership is a business organization in which two or more individuals manage and operate the business. Both owners are equally and personally liable for the debts from the business.The reason why Partnership is chosen as the form of organization because it is inexpensive and simple to form and maintain. All parties should adopt a written Partnership Agreement or called as the Articles of Partnership. The preferred type of partnership is the General
Partnership. In this type of partnership, each partner is jointly and generally liable for the debts of the business. This means that one partner can be held responsible for all the debts and obligations incurred in the name of the business by another partner. The partner can also be held responsible for any wrongful act or omission by other partner’s activity in the ordinary course of the company’s business, in which might be an advantage that will motivate a partner to act right and do his share in an appropriate manner, or it can be a serious disadvantage. The main advantage of the partnership, lies in the working relationships between the partners rather that in the structure of the organization. The success of the partnership are within the partners’ talents that they will share for the benefit of the business, being comfortable in sharing the decision making for the good of all the parties, and for all the individuals who will be involved in the organization. Organization Structure
The typical hierarchical arrangement of lines of authority, communications, rights and duties of an organization. Organizational structure determines how the roles, power and responsibilities are assigned, controlled, and coordinated, and how information flows between the different levels of management. The following figure will show the organizational structure of K-pop Food Company.
K-Pop Food Company
Figure 6
PERSONNEL AND LABOR REQUIREMENTS
Another important factor to consider in starting a business is he number of individuals need for the operation of the business. The shortages or excess of personnel can affect the production and profitability of the business. The proposed business needs a number of personnel for the production and organization of the business operation.
The number of personnel needed is on the list below.
Table 22
List of Personnel of K-Pop Food Company
Position
Number of Personnel
Manager
1
Sales and Markeing Officer
1
Finance Officer
1
Bookkeeper
1
Production Supervisor
1
Production Staff
1
Cashier
1
Delivery Staff
1
The proponents themselves will act as the top management level. The Manager will be Mendy M. Ygar, Sales and Marketing Officer Mistica V. Villanueva, Catherine V. Flores is the Finance Officer, the Production Head/Supervisor is Glory Mae V. Potenciando, and Albert R. Tolosa will be the Bookkeeper. K-Pop will only hire and train two (2) production staff, a cashier, a delivery staff. There will be a need for one (1) security guard for one shift, twelve hours security of the office and production facility. The security guard needed will come from a security agency.
JOB DESCRIPTION
1. Manager – The general manager is responsible for the general operation of the business. Manager serves us the Hunan Resource Department of the business. He is liable for the selecting, hiring and training the employees needed by the business. He is responsible for the management and supervision of the business. The General Manager shall be a member of the Partnership, a
graduate of management or allied courses, can communicate effectively, a team player, and have adequate skills in human relations. He shall reports directly to the Partnership during its regular meetings. 2. Sales and Marketing Officer -The Sales and marketing Officer shall be liable for directing the sales and marketing operations of K-Pop Food Company. The Marketing Officer oversees the company’s marketing campaigns both internally and externally and plays a key part in communicating the organizations marketing message.The Sales and Marketing Officer shall be a member of the Partnership, a graduate of marketing or allied courses, a team player, and have adequate skills in human relations. He shall reports regularly to the General Manager and to the Partnership during its regular meetings. 3. Finance Manager- The finance manager shall be liable on the financial aspects and operation of the Company. He is also liable on keeping all the records of the company’s accounts and all other things concerning the financial aspect needed by the company. He shall be a member of the Partnership, a graduate of accountancy or allied courses with sufficient background in financial management, a team player, and have adequate skills in human relations. The Financial Officer reports regularly to the General Manager and to the Partnership during its regular meetings. 4. Bookkeeper- The Bookkeeper shall be responsible for the processing of the accounts payable, verifying invoices, data entry, run checks and file accounts payable reports, obtain signatures, verify and correct all accounts payable entries, be responsible for mailing, process check requests by verifying invoices, regular and miscellaneous cash receipts. Together with the Financial Officer and the Cashier, work on issues related to payroll, sub-ledger maintenance, and general ledger entries and monthly reports. The Bookkeeper shall also perform specific duties assigned by the Financial Officer or as directed by the Partnership. The Bookkeeper should be a graduate of Accountancy, a team player, and have adequate skills in human relations, and should be trustworthy. He shall reports directly to the Financial Officer and to the Partnership during its regular meetings. 5. Production Supervisor- The production supervisorsupervises employees in the Production Department. Is responsible for the overall direction, coordination, and evaluation of this unit. Carries out supervisory responsibilities in accordance with the organization’s policies and
applicable laws. Responsibilities include interviewing, hiring, and training employees; planning, assigning, and directing work; appraising performance; rewarding and disciplining employees; addressing complaints and resolving problems.To perform this job successfully, an individual must be able to perform each essential duty satisfactorily. The requirements listed below are representative of the knowledge, skill and/or ability required. Reasonable accommodations may be made to enable individuals with disabilities to perform the essential functions. 6. Production Staff – The Production Staff shall be responsible in the production procedure of the product. Production staff is professional who work on a production line in a manufacturing environment and perform a variety of duties to ensure production goals are met for an organization.They shall also be responsible in maintaining the cleanliness of the production facility. The Production Staff should be able to work under minimum supervision. The Production Staff reports directly to the Production Supervisor. 7. Delivery Staff- The delivery staff shall be responsible in the delivery of the goods to the wholesalers, retailers and end consumers. He shall be responsible on the safe and timely delivery of goods or products. He is also responsible on checking the delivery vehicle is in good order. The delivery staff should have professional driver’s license and should be trustworthy.He shall reports directly to the Sales and Marketing Officer. 8. Cashier – The Cashier will be responsible for the transaction and exchange of money or credit with customers. Payments received by the Delivery Helper should be directly delivered to the Cashier. The Cashier should possess good mathematical skills, should be neat in appearance, and should deal pleasantly to customers. The Cashier reports directly to the Bookkeeper. *The Partners will attend Trainings and Seminars regardingproduction, food processing, and supervisory and other related topics on the said business. *A Security Guard will be needed and will be acquired from a security agency. Tasks that will be assigned to him are to assure that all individuals are safe inside the facility’s premises, to check and count all materials that will be delivered, finished products that will be delivered. JOB SPECIFICATION
Since the proponents will be the top management of the company, it is
assumed that they possesses all the characteristics and requirements needed for their position in the company. The following table will provide the positions and requirements for the personnel of K-Pop Food Company. Table 23
Job Specification of Sunny Treats
Position
Requirements
Manager
Male
At least twenty-five (25) years old
Graduate of any business course, preferably with master’s degree At least two (2) years experience in food manufacturing desired Computer literate
Must be result-oriented and creative
Must have strong interpersonal, communication, and analytical skills Marketing Officer
Female
At least twenty-five (25) years old
Graduate of any business, fine arts, or mass communication courses Computer literate
Must be result-oriented and creative
Must have strong interpersonal, communication, and analytical skills Must have knowledge in performing marketing and managerial tasks Design experience is an advantage
Finance Officer
Female
At least twenty-five (25) years old
Graduate of any business course, preferably finance or accountancy Computer literate
Must have a knowledge in basic accounting
Must have strong, interpersonal, communication, and analytical skills Must have knowledge in performing marketing and managerial tasks Bookkeeper
Female
At least twenty-one (21) years old
Graduate of Accountancy or Finance
Computer literate
Must have a knowledge in basic accounting
Must have strong, interpersonal, communication, and analytical skills Can work under minimum supervision
Must be diligent and trustworthy
With good moral character
Production Officer
Female
At least twenty-two (22) years old
Graduate of any four (4) year course, preferably business, food technology, hotel and restaurant management, culinary arts, or industrial engineering Computer literate
Must have strong, interpersonal, communication, and analytical skills Must have knowledge in performing marketing and managerial tasks Production Staff
Male or female
At least eighteen (18) years old
High school graduate or college level
Can work under minimum supervision
Willing to be trained
Hardworking and physically fit
Must be diligent and trustworthy
With good moral character
Cashier
Female
At least eighteen (18) years old
High school graduate or college level
Computer literate
Should be able to do repetitious work accurately
Needs basic mathematical skills
Should be neat in appearance
Should be able to deal tactfully and pleasantly with customers Delivery Driver
Male
At least twenty-one (21) years old
At least high school graduate
Must have professional driver’s license
Hardworking and physically fit
Must be diligent and trustworthy
With good moral character
Salary Structure, Incentives and Benefits
The salaries and wages that will be received by the employees will conform to the standard wage that is imposed by the Department of Labor and Employment (National Wages and Productivity Commission). (See Annexes for Rate Table) K-Pop Food Company employees will be paid twice a month. There are two pay periods in each month – the first pay period is from the 1st through the 15th and the second pay period is from the 16th through the last day of the month. Because it needs sufficient time to prepare, process, and distribute the payroll. Pay will be received within four calendar days after the pay period ends. Advances and loans against future pay are not allowed. Should an employee fail to claim his salary on the prescribed day, he may claim it from the Manager. Aside from the basic salary and wage of the employees, they will also receive mandated and other benefits indicated in the Compensation Table. (See Annexes for Compensation Table) 13th Month Pay
Every year, an employee is entitled to a 13th month pay, which is equivalent to 1/12 of his/her annual salary. This is released not later than December 24. Should an employee resign or be terminated within the year, he/she is entitled to a prorated 13th month pay. All employers are required to pay their rank and file employees regardless of the nature of their employment and irrespective of the method by which their wages are paid provided they worked for at least one (1) month during the calendar year.
Holiday Pay
Every worker shall be paid his/her regular daily wage during regular holiday. Holiday includes: New Year’s Day, Maundy Thursday, Good Friday, the ninth of April, the first of May, the twelfth of June, the fourth of July, the thirtieth of November, the twenty-fifth and thirtieth of December and the day designated by law for holding a general election. Premium Pay
Additional compensation for work performed within eight (8) hours on non-working days, such as rest days and special days. 1. For work performed
on rest days or on special days – plus 30% of the daily rate of 100% or a total of 130%. 2. For work performed on a rest day which is also a special day – plus 50% of the daily rate of 100% or a total of 150%. 3. For work performed on a regular holiday which is also the employee’s rest day – plus 30% of the regular holiday rate of 200%. Overtime Pay
Work may be performed beyond eight (8) hours a day provided that the employee is paid for the overtime work, an additional compensation equivalent to his regular wage plus at least thirty percent (30%) thereof. Work performed beyond eight hours on a holiday or rest day shall be paid an additional compensation equivalent to the rate of the first eight hours on a holiday or rest day plus at least thirty percent (30%) thereof. *The General Manager, Finance Officer, Marketing and Sales Officer, Production Officer and Production Supervisor are not entitled for Overtime Pay since they are part of the Partnership. Night Shift Pay
An additional 10% of the regular hourly wage will be paid for hours worked between 10:00 p.m. and 6:00 am. Service Incentive Leave
For every employee who has rendered at least one year of service shall be entitled to a yearly service incentive leave of five days with pay. Free Annual Medical Examination
K-Pop Food Company will provide free annual medical exam to be done at the accredited clinic. This is to comply with DOLE regulations and also to make sure that health and safety concerns of employees are addressed effectively. Annual Vacation
An employee will be entitled to an annual Service incentive leave of five (5) days every year after they have worked for the company for a full year.
Social Security System
SSS Policy – “It is the policy of the State to establish, develop, promote and perfect a sound and viable tax-exempt social security system suitable to the needs of the people throughout the Philippines which shall promote social justice and provide meaningful protection to members and their families against the hazards of disability, sickness, maternity, old age,
death and other contingencies resulting in loss of income or financial burden. Toward this end, the State shall endeavor to extend social security protection to workers and their beneficiaries.” *Source : www.sss.gov.ph (Section 2, RA 8282) SSS Benefits
Social security contribution required to include both the employer and employee’s share. 1. Sickness Benefits
2. Maternity Benefits
3. Disability Benefit
4. Retirement Benefit
5. Death and Funeral Benefit
6. Salary Loan
7. Housing Loan
8. Stocks Investment Loan Program
9. Livelihood Financing Program
(See Annexes for SSS Contribution Schedule)
PHILHEALTH(Philippine Health Insurance Corporation)
PhilHealth is attached to the Department of Health  providing affordable health social health insurance coverage for all Filipinos. Insuring the sustainable national health insurance program for all. This social insurance program shall serve as the means for the healthy to help pay for the care of the sick and for those who can afford medical care to subsidize those who cannot. The PhilHealth program provides benefits for hospital room and board allowance, allowance for medicine, laboratory examinations, X-ray, surgeon’s fee, operating room fee, anesthesiologist’s fee, and medical and practitioner’s fee. However, the allowance would not necessarily cover the total expense incurred. (See Annexes for PhilHealth Premium Table) *Source : www.philhealth.gov.ph
Home Development Mutual Fund
More popularly known as Pag-ibig Fund, was an answer to the need for a national savings program and an affordable shelter financing for the Filipino worker. PAG-IBIG offers its members benefits like housing loan program, livelihood program, Savings and Multi-loan program. The maximum monthly compensation used in computing the employee contributions is
currently set at P5,000. This means that the maximum member contribution and employer counterpart per month are both currently P100. (See Annexes for the Contribution Table) *Source : www.pagibigfund.gov.ph
ADMINISTRATIVE POLICIES, RULES AND REGULATIONS (DICIPLINE GUIDELINES AND PROCEDURE)  Relate to the operational aspects of the substantive work of the K-POP. They cover the role of the Council, Committees and all subsidiary bodies. They concern the organization of meetings, including the participation of non-member economies and the adoption and implementation of the Acts (legal instruments) of the Organization.
Quality, Cleanliness, and Value
K-POP Food Company has a commitment to provide customers high quality products, served quickly with a smile, in a clean and pleasant environment at an affordable price. Driven by a philosophy of Quality, Service, Cleanliness and Value for Money, the kalabasa lollipop is so priced that consumers can easily afford it, while at the same time ensuring that quality is not compromised. K-POP strives to maintain its local quality standards in every single one of its outlets. Dealing directly with the farmers, k-pop ensures that every ingredient is of the best quality. Strong supply chain efficiencies, cold chain delivery, minimum storage times, standard recipes. Work Days and Hours
Regular workdays are from Monday to Friday from 8:00 am to 5:00 pm. Those who are on regular day duty are entitled to two 15 minute break (one in the morning and the other in the afternoon) and a lunch break from 12:00 noon to 1:00 pm. Employees who are authorized to render overtime work are entitled to overtime pay as follows: 1. Overtime pay at the rate of regular base plus 30% is paid for all work performed in excess of eight hours on ordinary days within the work week. 2. Premium pay at the rate of regular base plus 50% is paid for all work done on Saturdays, Sundays and, for work close on legal holidays with pay; the employees shall be paid at the rate of regular base pay plus 150%.
Open Communication Policy
The proponents considers K-POP as a progressive and well-meaning company, but everyone may, from time to time, have business related problems or concerns. Discussion among managers and staff over work related issues are encouraged and welcomed. Inquirer Philippine News is located on a prominent part of the work area. These boards are used to post announcements or notices regarding safety, working conditions, benefits and other matters relating to employment. Opinion Survey would be held twice a year and will require the participation of employees. This will help the company in terms of discovering opportunities to meet the needs of the employees.
Health and Safety Policy
K-POP Food Company is committed to providing and maintaining a safe and healthy workplace for all staff, and to providing the information, training and supervision needed to achieve this. The company will take responsibility for health and safety procedures, however, employees need to be aware of their responsibilities and comply with the business’ health and safety policy. Each employee is encouraged to play a vital and responsible role in maintaining a safe and healthy workplace through: Being involved in the workplace health and safety system.
Sticking to correct procedures and equipment.
Wearing protective clothing and equipment as and when required. Reporting any pain or discomfort as soon as possible.
Ensuring all accidents and incidents are reported.
Helping new employees, trainees and visitors to the workplace understand the right safety procedures and why they exist. Telling your manager immediately of any health and safety concerns. Keeping the work place tidy to minimize the risk of any trips and falls. Your participation is much appreciated.
Basic Responsibilities and Work Policies
Because the company is in food handling business, employees are required to practice to wash hands every hour and prior to their duty, after using the comfort room and/or handling any cleaning tool or when hands have been exposed to contamination. Because a timecard is a personal record, the employee alone should punch his/her timecard. Tampering or punching another
employee’s timecard is prohibited. The company telephone is for business purposes only. However, emergency calls will be allowed. To avoid disturbing operations, calls for production staffs will be noted down by the receiving manager. Return calls can be made during break times or off duty upon the approval of management. Business transactions not related to the company are prohibited within company premises. Unauthorized transactions should be reported to management. Before any staff can report to work again after any illness, a medical certificate from the accredited clinic will be required and cannot work until this is provided. Beeper and cell phones are not allowed while on duty.
In order to keep records up to date, Management should be notified whenever there is a change in employee: Name (thru marriage or otherwise)
Address
Contact number
Marital Status
Person to notify in case of accident/illness
Attendance Policy
It is every employee’s responsibility to work on time, without proper approval from management, late and absences will be considered unexcused. Late, absences, and over breaks will be treated the same. These offenses will be subject to disciplinary action. If a staff incurs an attendance violation, he/she will receive a progressive disciplinary action. After each disciplinary action, the employee involved will be given 2 months to improve his/her attendance. Should the same violation is committed again progressive disciplinary action will be issued starting with a verbal warning. The progressive disciplinary action a staff may receive is as follows: 1st offenseverbal warning
2nd offensewritten warning
3rd offensesuspension of 2 scheduled working days
4th offense5 days suspension from work or termination
Schedule and Work Hours
A regularly scheduled administrative workweek must be established for every
full-time employee unless the employee works a first 40-hour of duty, is paid annual premium pay for standby duty, works a flexible or compressed work schedule, or is intermittent. When an assignment to a new assign of duty is necessary, an employee must be given as much advance notice as possible. Unless there is a bargaining unit agreement that states otherwise, it is standard practice that schedules be established by 6 p.m. Friday of the week prior to the one in which the time will be worked. A schedule may need to be established earlier depending on the hour a majority of the employees depart the workplace. Absent a bargaining unit agreement, published policy, posted schedule or notification that says otherwise, an employee’s schedule is deemed set for the following week at that time.Time clocks will be installed to assure accurate recording of working time for pay purposes. Should an employee can’t make it to the scheduled shift, the manager should be informed at least 2 days in advance so a replacement could be arranged. It is expected that the approved sudden changes be marked as follows: Excused Absent (EA)
Excused Late (EL)
Certain cases wherein the crew did not inform or get the approval of the management, the involve staff would be marked late or no show. *All habitual tardiness or absence with or without excuse may result in disciplinary action.
Food Safety Policy
Nothing is more important than delivering safe food to the clients. As a business, K-POP is committed to food safety. It is everybody’s responsibility to maintain and enforce all safety and standard procedures in the business. Any violation of procedures, which will jeopardize the safety of any food item, will be dealt with accordingly. Neatness
All employees are required to maintain the highest standards relating to personal hygiene including bathing daily, use of deodorant and moderate use of cosmetics. Production staff would be required to wear a clean white polo shirt, pants and an apron which would be provided by the company. Only one pair of stud earrings is allowed to be worn. Men are not allowed to wear
earrings. Necklace can also be worn but should be hidden under the uniform. Employees should style their hair so that it does not exceed a moderate length. All employees are required to keep their forehead clear. For the men, full ear should show. The hair must not overlap the collar, and should be styled not to exceed the reasonable height from the scalp, if not a hairnet must be worn. Ladies’ hair should be neatly styled, away from the face. Use a clip or matching colored ribbon to tie the long hair. *For sanitation purposes, a hair net must be worn to cover the entire hair from the forehead down to the nape. A neat, clean appearance is required; a mustache is not allowed to be worn. Likewise, it is essential that the stubbles be shaved as soon as noticeable. Sideburns are permitted; however, it should be styled to extend below the ear lobe and should be groomed to avoid being over grown. Men should always wear clean, black, closed, non-skid shoes with white socks. Women should wear clean, black, closed, non-hazardous, non skid shoes with plain white or plain flesh colored stockings or white socks. For men and women, open toed sandals, canvass shoes or other rubber shoes cannot be worn. All employees should have clean hands and short fingernails at all times. Employees are not allowed to wear nail polish. The company, since it is in the food business emphasizes the importance of hygiene and sanitation. Failure to comply with the above mentioned policies will merit disciplinary action. No Solicitation Policy
Solicitation for funds, membership, or individual commitment to outside organization, or distribution of any literature for any purpose, or attempts to sell merchandise or services, by outside non-employee persons is prohibited on company premises. Solicitation by employees for funds, memberships or individual commitments to outside organization or causes, or attempts to sell non company product is also prohibited. Distribution of non-approved, non-company product on company premises by employees is not permitted. The premises must be kept clean and free of litter at all times. Sexual Harassment Policy
Definition – Sexual harassment is any unwanted sexual attention that is explicitly or implicitly made as a condition for favorable decisions affecting one’s employment, or that which creates an intimidating, hostile
or offensive environment in the workplace. K-POP prohibits sexual harassment of any type. Sexual harassment is prohibited because it is intimidating, an abuse of power and is inconsistent with the policies, practices and management philosophy. Sexual harassment is defined as unwelcome sexual advances, request for sexual favors, and other verbal or physical conduct of a sexual nature. Sexual harassment is sexual conduct that interferes with another person’s work performance or creates an intimidating, hostile or offensive work environment. The company shall enforce the provisions of the Anti-Sexual Harassment Law and the accompanying policy guidelines which are noted in separate publication. Any employee who feels subjected to discrimination or harassment should immediately report it to a member of the management team. Such reports will be investigated thoroughly. If the report has merit, disciplinary action will be taken against the offender. Rules of Conduct
As a condition of employment and a all times during employee’s employment with K-POP food company, the undersigned employee will abide by the following rules of conduct. 1. All information submitted on any employment application and/or given to employer to gain employment, including information given on any resume, questionnaire, and medical history or during any pre-employment interview shall be true, accurate and not misleading. 2. Employees shall maintain all Company matter, secrets confidential but not limited to trade secrets, company records, customer information, intellectual property, and other tangible matters not known to the general public. 3. Employees are expected to behave properly in the work place and in all official and social gatherings (like company parties, outings and meetings) of the company whether on or off duty. Reporting to these occasions under the influence of alcohol and prohibited drugs are strictly prohibited. 4. Smoking on unauthorized places is strictly prohibited.
5. Clients should be treated with utmost respect and courtesy and failure to do so shall be given disciplinary action. 6. Employees are not allowed to leave the job without permission or conduct personal affairs without authorization while working. Example is: leaving the station and talking to
visiting friends or relatives without authority of the managers. 7. Giving away products or other properties of the company without the payment or the appropriate authority of the management. 8. Employees are required to obey instructions and perform work as required or assigned. Any insubordination or failure to obey lawful instructions with regard to work and behavior will result to disciplinary action. 9. Employees should respect the person, rights and properties of co-workers. Acts of or even attempts to cause physical and/or psychological harm, injury, damage, loss, and situations to endanger safety and well-being of the above stated person will be subjected to disciplinary action. 10. Employees are expected observe all security rules.
Security Policy
To further protect the company premises and employees, the following guidelines have been set: All personnel (on duty or not) shall have their bags and parcels inspected by the guard on duty before going in and when coming out. Be advise to allow time prior to schedule or after duty to prevent being late. The delivery door, fire exits and corral doors are not for entry or exit except for delivery purposes or emergencies. No one is allowed to use these doors as a passageway for personal use. Absence without Leave (AWOL)
AWOL is a situation where in a staff did not return for work after 4 days of absence and fails to inform the management on the status of his/her employment. A formal letter from the Management will be sent to the employee. Seven days after receipt of letter and no contact has been made by the concerned staff to the management explaining the AWOL, it will be assumed by the company that the employee voluntarily terminated his/her employment at this time. Resignation and Rehire
Employees of good standing, both in floor operations and conduct, may reapply with the company again if he/she wishes to do so. The decision to rehire will be made by the General Manager.
FORMS AND DOCUMENTS DESIGN
Security and Exchange Commission (SEC) – the partnership should be registered its name with SEC in order to have juridical entity. Department of Trade and Industry (DTI) – the partnership should be registered with DTI after SEC registration. Mayor’s Permit – after SEC and DTI registration, the partnership should registered at the municipal hall to have a permit to conduct the business in the proposed location. This permit also includes the following certificates; Barangay Clearance/Business Locational Clearance
Sanitary Permit/BFAD
Fire Certificate
Bureau of Internal Revenue (BIR) – the partnership should also registered in the BIR and to be able to transact with its customers having a tax identification number, registered its books, official receipts, sales invoices, purchase order slips, and delivery slip/receipts. **See Annexes for the Forms, Permits, Certificates and Documents.
CHAPTER V
FINANCIAL ASPECT
The financial aspect of the business shows the projected financial statement, supporting data, and assumptions to help determine the feasibility and vitality of the project. Establishing the cost-effectiveness of the proposed project, i.e. if the benefits do not outweigh the costs then it is not worth going ahead. Before beginning a business, it is important to know how much money is going to be needed to run it. Financial aspect interprets the qualitative analysis done in the marketing study. Every business owner should know every financial aspect of the company. Mismanaging money is dangerous and a complete waste that can be easily avoided with a clear and organized financial plan. Building a financial plan after everything has been done to outline the business keeps the goals of the proposed business from being compromised. The financial aspect of this feasibility study contains the following: Basic Assumptions:
The projection of sales is based from the projected market share. Product price increase annually by 2%.
Purchases are all on cash basis.
Material costs per unit, utilities expenses, supplies expenses, and advertising expenses are assumed to increase by 5% yearly due to inflation rate and some unseen factors. Profits or losses are to be distributed equally among the partners at the end of the year. Partners will have maximum allowable withdrawals leaving an amount not less than the vat premium. (See note number 7) Half of the utilities expenses are charged to production.
Purchases of office supplies, store supplies (cleaning materials), and advertising materials will be done on the first month of the year and assumed none will be left unused. There will be no increase in salaries and wages, allowances, and premium contribution for the next 5 years. Remittances should be as follows
Monthly Payments
SSS –within 30 days from the date of employment
Phil Health -within 30 days from the date of employment
PAG-IBIG -25th day of the next month
Quarterly
VAT and Income Tax –within 25 days following the close taxable quarter 90% of the total cash will be deposited in the bank and 10% will be left as petty cash.
K-POP COMPANY
Initial Project Cost
Initial Cash Outlay
Pre-Operating Expenses
Legal Requirements
DTI 800.00
BIR 900.00
SEC (1/5 of 1% of the capital) 5,000.00
Mayor’s Permit
(BFAD, Sanitary Permit, Fire Insp.) 7,800.00
Allowance 500.0015,000.00
Connection of
Electricity3,000.00
Water 1,000.00
Communication1,500.00
Advertising20,000.00 40,500.00
Machineries &Equipment, and Kitchen Tools104,000.00
Furniture & Fixtures 37,650.00
Rental Deposit 20,000.00
Delivery Equipment 200,000.00
Store Supplies 6,000.00
Office Supplies 2,500.00
Working Capital (for one week)
Salaries 9,560.00
Materials 19,500.00
Some Operating Expenses 5,000.00
Total 444,710.00
Initial Cash on Hand 1,055,290.00
Capital/Mode of Financing
Contributor
Contribution
Catherine V. Flores
300,000.00
Glory Mae V. Potenciando
300,000.00
Albert R. Tolosa
300,000.00
Mistica V. Villanueva
300,000.00
Mendy M. Ygar
300,000.00
Sources of Financing
The investments of the proponents will come from their very supportive family and upon their own resourcefulness. Ms. Flores and Mr. Tolosa’s contributions will come from their bank savings. Ms. Potenciando’s contributions will come from her own savings. Ms. Villanueva and Ms.Ygar’s capital will come from the income of their family business.
PROJECTED INCOME STATEMENT
K-POP FOOD COMPANY
Projected Income Statement
Year 1
Year 2
Year 3
Year 4
Year 5
Revenues from Sales
Volume of Sales
48000
51000
54000
57000
60000
Selling Price Per Unit
35.00
35.70
36.41
37.14
37.88
Total Projected Sales
1,680,000.00
1,820,700.00
1,966,140.00
2,116,980.00
2,272,800.00
Less: Cost of Sales
Direct Materials
48,000.00
50,400.00
52,920.00
55,566.00
58,344.30
Direct Labor
58,720.00
76,608.00
86,400.00
80,438.40
84,460.32
Overhead
33,000.00
72,450.00
76,072.50
79,876.13
83,870.00
Total Cost of Sales
139,720.00
199,458.00
215,392.50
215,880.53
226,674.62
Gross Profit
1,540,280.00
1,621,242.00
1,750,747.50
1,901,099.47
2,046,129.38
Less: Operating Expenses
Selling Expenses
Pre-operating Expenses
33,000.00
–
–
–
–
Advertising Expense
–
21,000.00
22,050.00
23,152.00
24,310.00
Salaries & Wages
373,440.00
373,440.00
373,440.00
373,440.00
373,440.00
SSS, PhilHealth, PAG-IBIG
36,134.40
36,134.40
36,134.40
36,134.40
36,134.40
13th Month Pay
38,240.00
38,240.00
38,240.00
38,240.00
38,240.00
Store Supplies
6,000.00
6,300.00
6,615.00
6,945.75
7,293.04
Rent
120,000.00
120,000.00
120,000.00
120,000.00
120,000.00
Administrative Expenses
–
–
–
–
–
Allowances
15,000.00
15,000.00
15,000.00
15,000.00
15,000.00
Office Supplies
2,500.00
2,625.00
2,756.00
2,894.00
3,039.00
Utilities Expense
66,000.00
69,300.00
72,765.00
76,403.25
80,223.41
Permit & Licenses
–
7,000.00
7,000.00
7,000.00
7,000.00
Depreciation
68,330.00
68,330.00
68,330.00
68,330.00
68,330.00
Total Operating Expenses
758,644.40
757,369.40
762,330.40
767,539.40
773,009.85
Less: Input Tax
91,037.33
90,884.33
91,479.65
92,104.73
92,771.98
Net Operating Expenses
667,607.07
666,485.07
670,850.75
675,434.67
680,237.87
Net Income Before Tax
872,672.93
954756.93
1,079,896.75
1,225,664.80
1,365,891.51
Less: 35% Provision for Tax
305,435.53
334,164.93
377,963.86
428,982.68
478,062.03
Net Income After Tax
567,238.00
620,592.00
701,933.00
796,683.00
887,830.00
PROJECTED CASHFLOW STATEMENT
K-POP FOOD COMPANY
CASH FLOW STATEMENT
Year 1
Year 2
Year 3
Year 4
Year 5
Operating Activities
Cash-in
Net Income
567,238.00
620,592.00
701,933.00
796,683.00
887,830.00
Amount Withheld
Income Tax Payable
305,416.00
332,054.00
375,748.00
426,656.00
475,616.00
VAT Payable
110,560.00
126,778.00
143,594.00
161,027.00
179,024.00
Depreciation
68,330.00
68,330.00
68,330.00
68,330.00
68,330.00
SSS, PhilH., PAG-IBIG
3,052.00
3,052.00
3,052.00
3,052.00
3,052.00
Total
1054596.00
1150806.00
1292657.00
1455748.00
1613852.00
Investing Activities
Rental Deposit
120,000.00
–
–
–
–
Machi. & Equip., & Kit. Tools
104,000.00
–
–
–
–
Furniture & Fixtures
37,650.00
–
–
–
–
Delivery Equipment
200,000.00
–
–
–
–
Cash Inflow (Outflow)
461,650.00
–
–
–
–
Financing Activities
Partners Contribution
1,500,000.00
–
–
–
–
Less: Withdrawal
-300,000.00
-500,000.00
-600,000.00
-700,000.00
-800,000.00
Net
1,200,000.00
500,000.00
600,000.00
700,000.00
800,000.00
Net Cash Inflow (Outflow)
1792946.00
650806.00
692657.00
755748.00
813852.00
Cash Balance, Dec. 31, beg
–
1792909.00
2443715.00
3136372.00
3892120.00
Cash Balance, Dec. 31, end
1,792,909.00
2443715.00
3136372.00
3892120.00
4,705,972.00
PROJECTED BALANCE SHEET
K-POP FOOD COMPANY
INITIAL BALANCE SHEET
Year 1
Year 2
Year 3
Year 4
Year 5
ASSET
Current Asset
Cash on Hand/in Bank
1,792,909.00
2,443,715.00
3,136,372.00
3,892,120.00
4,705,972.00
Fixed Assets
Machi & Equip., & Kit. Tools
104,000.00
104,000.00
104,000.00
104,000.00
104,000.00
Furniture & Fixtures
37,650.00
37,650.00
37,650.00
37,650.00
37,650.00
Delivery Equipment
200,000.00
200,000.00
200,000.00
200,000.00
200,000.00
Total
341,650.00
341,650.00
341,650.00
341,650.00
341,650.00
Less: Acc. Depreciation
68,330.00
136,660.00
204,990.00
273,320.00
341,650.00
Total Fixed Assets
273,320.00
204,990.00
136,660.00
68,330.00
0.00
Other Assets
Deposit – Rental
120,000.00
120,000.00
120,000.00
120,000.00
120,000.00
TOTAL ASSETS
2,186,229.00
2,768,705.00
3,393,032.00
4,080,450.00
4,825,972.00
LIABILITIES & PARTNERS EQUITY
Current Liabilities
Income Tax Payable
305,416.00
332,054.00
375,748.00
426,656.00
475,616.00
VAT Payable
110,523.00
126,741.00
143,557.00
160,990.00
178,987.00
SSS,PhilHealth, PAG-IBIG
3,052.00
3,052.00
3,052.00
3,052.00
3,052.00
Total
418,991.00
461,847.00
522,357.00
590,698.00
657,655.00
Partners’ Equity
Partners Equity – beg.
1,500,000.00
1648113.00
2,091,099
2,583,767
3,138,142
Add: Net Income
567,238.00
620,592.00
701,933.00
796,683.00
887,830.00
Total
2,067,238.00
2,268,705.00
2,793,032.00
3,380,450.00
4,025,972.00
Less: Withdrawal
300,000.00
500,000.00
600,000.00
700,000.00
800,000.00
Total
1,767,238.00
1,768,705.00
2,193,032.00
2,680,450.00
3,225,972.00
TOTAL LIABILITIES & PARTNERS EQUITY
2,186,229.00
2,768,705.00
3,393,032.00
4,080,450.00
4,825,972.00
NOTES
Note 1: Summary of Raw Materials per Unit
Year 1
Year 2
Year 3
Year 4
Year 5
1 pack of KalabasaLollipop
17.50
18.38
19.30
20.27
21.28
NOTE: Materials costs per unit assumed to increase by 5% yearly.
Note 2:Utilities
Monthly
Year 1
Year 2
Year 3
Year 4
Year 5
Electricity
3,000.00
36,000.00
37,800.00
39,960.00
41,944.50
44,041.73
Water
1,000.00
12,000.00
12,600.00
13,230.00
13,891.50
14,586.08
Communication
1,500.00
18,000.00
18,900.00
19,845.00
20,837.25
21,879.11
Fuel & Oil
2,500.00
30,000.00
31,500.00
33,075.00
34,729.00
36,465.00
TOTALS
8,000.00
96,000.00
100,800.00
106,110.00
111,402.30
116,971.90
Note:Half of the utilities are charged to production as overhead and assumes to increase by 5% yearly.
Note 3:Supplies
Year 1
Year 2
Year 3
Year 4
Year 5
Store Supplies
6,000.00
10,500.00
11,025.00
11,576.00
12,155.00
Office Supplies
2,500.00
2,625.00
2,756.00
2,894.00
3,039.00
NOTE:Supplies are assumed to increase by 5% yearly.
Note 4:Advertisement
Year 1
Year 2
Year 3
Year 4
Year 5
Advertising Expense
20,000.00
21,500.00
22,050.00
23,152.00
24,310.00
NOTE:Advertising expenses are assumed to increase by 5% yearly.
Note 5:Depreciation
Total
Estimated Life
Annual
Property, Plant & Equipment
Cost
(years)
Depreciation
Production Equipment
104,000.00
5
20,800.00
Furniture & Fixtures
37,650.00
5
7,530.00
Delivery Vehicle
200,000.00
5
40,000.00
Total
341,650.00
68,330.00
Year 1
Year 2
Year 3
Year 4
Year 5
Accumulated
Depreciation
68,330.00
71,747.00
75,335.00
79,102.00
83,058.00
STAFFS
Daily rate with COLA (367+22)
Weekly Wage (5days)
Monthly Wage (4wks)
MONTHLY Remittances
Annual Wage (12mos)
ANNUALLY Remittances
SSS Premium
SSS EC
Phil Health Prem.
Pag-ibig Fund
SSS Premium
SSS EC
Phil Health Prem.
Pag-ibig Fund
Production Staff
2.00
778.00
3,890.00
15,560.00
1,130.60
20.00
175.00
200.00
186720.00
13,567.20
240.00
2,100.00
2,400.00
Cashier
1.00
389.00
1,945.00
7,780.00
565.30
10.00
87.50
100.00
93360.00
6,783.60
120.00
1,050.00
1,200.00
Delivery driver
1.00
389.00
1,945.00
7,780.00
565.30
10.00
87.50
100.00
93360.00
6,783.60
120.00
1,050.00
1,200.00
1,556.00
7,780.00
31,120.00
2,261.20
40.00
350.00
400.00
373440.00
27,134.40
480.00
4,200.00
4,800.00
EMPLOYEE
Compensation Table
STAFFS
Daily rate with COLA (456+22)
Weekly Wage (5days)
Monthly Wage (4wks)
MONTHLY Remittances
NET MONTHLY WAGE
Annual Wage (12mos)
ANNUALLY Remittances
NET ANNUALLY WAGE
SSS Premium
Phil Health Prem.
Pag-ibig Fund
SSS Premium
Phil Health Prem.
Pag-ibig Fund
Production Staff
2.00
778.00
3,890.00
15,560.00
533.40
175.00
200.00
14651.60
186720.00
13,567.20
2100.00
2400.00
168652.8
Cashier
1.00
389.00
1,945.00
7,780.00
266.70
87.50
100.00
7325.80
93360.00
6,783.60
1050.00
1200.00
84326.4
Delivery driver
1.00
389.00
1,945.00
7,780.00
266.70
87.50
100.00
7325.80
93360.00
6,783.60
1050.00
1200.00
84326.4
1,556.00
7,780.00
31,120.00
1,066.80
350.00
400.00
29303.20
373440.00
27,134.40
4200.00
4800.00
337305.6
*assume that there is no increase on salary rate and premium contribution for the next five years
Note 6:Compensation Table
Note 7:
VAT Schedule
Year 1
Year 2
Year 3
Year 4
Year 5
Output Tax
201,600.00
218,484.00
235,936.80
254,037.60
272,736.00
Less: Input Tax
91,040.93
91,706.93
92,343.23
93,011.26
93,712.85
Total VAT Payable
110,559.07
126,777.07
143,593.57
161,026.34
179,023.15
Less: Year End Payable
68,544.00
73,244.00
77,929.00
82,590.00
87,205.00
205,632.00
219,730.00
233,785.00
247,770.00
261,615.00
Total
–
68,544.00
73,244.00
77,929.00
82,590.00
Add: Prem. Pay.
205,632.00
288,247.00
307,029.00
325,699.00
344,205.00
Payment Remitted
NOTE:
Output Taxes are VAT on gross sales.
Input Taxes includes VAT on purchases and some operating expenses.
Note 8:
SSS, PhilHealth, PAG-IBIG Payment
Year 1
Year 2
Year 3
Year 4
Year 5
Premium current
36,615.00
36,615.00
36,615.00
36,615.00
36,615.00
Less: End Year Payable
3,052.00
3,052.00
3,052.00
3,052.00
3,052.00
Total
33,563.00
33,563.00
33,563.00
33,563.00
33,563.00
Add: Premium Payable, end
–
3,052.00
3,052.00
3,052.00
3,052.00
Payment Remitted
33,563.00
36,615.00
36,615.00
36,615.00
36,615.00
FINANCIAL ANALYSES
PROJECTED RETURN ON INVESTMENT
Return on Investment (ROI) = (Net Income / Investment)*100
It determines the rate of return on investment of the business. As an owner or shareholder, this is one of the most important ratios, as it shows the hard facts about the business. Year 1
Year 2
Year 3
Year 4
Year 5
567,238
620,592
701,933
796,683
887,830
1,500,000
1,500,000
1,500,000
1,500,000
1,500,000
=0.38
or 38%
=0.41
or 41%
=0.47
or 47%
=0.53
or 53%
=0.59
or 59%
PROJECTED PAYBACK PERIOD
The payback period is another method to evaluate an investment project. It is the length of time that it takes for project to recoup its initial cost out of the cash receipt that it generates.
Method used: Uneven Cash Flow Payback Period Method
Investment of P1.5 million and is expected to generate 300 million in Year 1, 400 million in Year 2, 500 million in year 3, 600 million in Year 4 and 600 million in Year 5.
Cumulative Cash Flow
Year
Cash Flow
0
(1,500,000)
(1,500,000)
1
300,000
(1,200,000)
2
400,000
(800,000)
3
500,000
(300,000)
4
600,000
300,000
5
600,000
900,000
Payback Period
= 2 + (500,000 Ă· 800,000)
= 2 + 0.625
=2.63years
PRICE
While break-even revenue and units sold are calculated for making financial and management decisions, break-even pricing is calculated to assist in helping market the product. Break-even pricing is important for producer-owners of businesses because they need to know how to price a product as compared with pricing a commodity.
Year 1
Year 2
Year 3
Year 4
Year 5
Selling Price Per Unit =
Materials Cost Per Unit + 200% Markup
35
35.7
36.41
37.14
37.88
Unit Variable Cost=
Total Cost of Sales/ Volume of Sales
2.91
3.91
3.99
3.79
3.78
Contribution Margin Per Unit=
Unit Selling Price – Variable Cost
MC Per Unit
32.09
31.79
32.42
33.35
34.1
Contribution Margin Percentage=
CM per Unit/ Selling Price
MC %
0.91685714
0.89047619
0.89041472
0.89795369
0.90021119
Fixed Cost (FC)
675270
667995
672956
678165
683635.45
BEP Sales Volume=
FC/MC Per Unit
21,043.00
21012.73986
20757.43368
20334.78261
20047.96041
BEP Peso Sales=
FC/ MC %
736505.1441
750154.8132
755778.1614
755233.825
759426.7431
BEP Price
Variable Cost Per Unit + (FC / BEP Sales)
35
35.7
36.41
37.14
37.88
Fixed Cost
Pre-operating Expenses
39,000.00
–
–
–
–
Advertising Expense
–
21,000.00
22,050.00
23,152.00
24,310.00
Salaries & Wages
373,440.00
373,440.00
373,440.00
373,440.00
373,440.00
Store Supplies
6,000.00
6,300.00
6,615.00
6,945.75
7,293.04
Rent
120,000.00
120,000.00
120,000.00
120,000.00
120,000.00
Office Supplies
2,500.00
2,625.00
2,756.00
2,894.00
3,039.00
Utilities Expense
66,000.00
69,300.00
72,765.00
76,403.25
80,223.41
Permit & Licenses
–
7,000.00
7,000.00
7,000.00
7,000.00
Depreciation
68,330.00
68,330.00
68,330.00
68,330.00
68,330.00
Total
675,270.00
667,995.00
672,956.00
678,165.00
683,635.45
FINANCIAL RATIO ANALYSIS
I. Liquidity
These are the ratios that will measure the firm’s ability to meet the cash needs as it arises. Current Ratio = Current Assets / Current Liabilities
The ratio between all current assets and all current liabilities, it is a way of expressing liability.
Year 1
Year 2
Year 3
Year 4
Year 5
1,792,909
2,443,715
3,136,372
3,892,120
4,705,972
418,991
461,847
522,357
590,698
657,655
4.28
5.3
6.00
6.54
7.16
II. Safety
This is the indicator of the business’s vulnerability to risk. These ratios are often used by creditors to determine the firm’s ability to repay loans. Debt to Equity Ratio = Total Liabilities / Total Equity
This shows the ratio between capital investment of the owners and the funds provided by the lenders.
Year 1
Year 2
Year 3
Year 4
Year 5
418,991
461,847
522,357
590,698
657,655
1,767,238.00
1,768,705.00
2,193,032.00
2,680,450.00
3,225,972.00
0.24
0.26
0.24
0.22
0.20
Debt Ratio = Total Liabilities / Total Assets
It indicates on what proportion the firm’s assets is being financed through debt. Year 1
Year 2
Year 3
Year 4
Year 5
418,991
461,847
522,357
590,698
657,655
2,186,229
2,768,705
3,393,032
4,080,450
4,825,972
0.19
0.17
0.15
0.14
0.14
III. Profitability
In this part, the ratios will measure the ability of the business to make profit.
Gross Profit Margin = Gross Profit / Net Sales
It indicates how much profit is earned on the products without the consideration of selling and administration cost.
Year 1
Year 2
Year 3
Year 4
Year 5
1,540,280.00
1,621,242.00
1,750,747.50
1,901,099.47
2,046,129.38
1,680,000
1,820,700
1,966,140
2,116,980
2,272,800
0.92
0.89
0.89
0.90
0.90
Return on Investment (ROI) = Net Income / Investment
It determines the rate of return on investment of the business. As an owner or shareholder, this is one of the most important ratios, as it shows the hard facts about the business.
Year 1
Year 2
Year 3
Year 4
Year 5
567,230
620,592
701,933
796,683
887,830
1,500,000
1,500,000
1,500,000
1,500,000
1,500,000
0.38
0.41
0.47
0.53
0.59
Return on Assets (ROA) = Net income / Assets
It is considered as a measurement on how effective the assets are being used to generate returns Year 1
Year 2
Year 3
Year 4
Year 5
567,230
620,592
701,933
796,683
887,830
2,186,229
2,768,705
3,393,032
4,080,450
4,825,972
0.26
0.22
0.21
0.20
0.18
Return on Equity (ROE) = Net Income / Ave. Total Equity
It determines the rate of return in the investment in the business. Year 1
Year 2
Year 3
Year 4
Year 5
567,230
620,592
701,933
796,683
887,830
8,627,194
8,627,194
8,627,194
8,627,194
8,627,194
0.066
0.072
0.081
0.092
0.102
Conclusion:
The group concludes that this project is financially feasible. As per return on investment, the business has an expected ROI of 38% for the first year. Payback period is expected at less than three years from the start of operation or 2.63 years. Breakeven volume for the first year of operation is 21,676 units which is less than the projected sales of 48,000 units.
CHAPTER VI
SOCIO-ECONOMIC ASPECTS
In starting a new business venture the primary goal is to earn or to gain a profit, but in this proposed business the proponents are very much concerned about the positive impact it will bring to the community especially to the
valuable consumers.
Government Revenues
The socio economic is one of the main concerns of K-Pop Food Company. Government revenue is revenue received by a government. It is an important tool of the fiscal policy of the government and is the opposite factor of government spending. Revenues earned by the Government are received from sources such as Taxes levied on the incomes and wealth accumulation of individuals and corporations and on the goods and services produced, exported and imported from the country.
Foreign Exchange Savings or Generations
Since Philippines are rich in its natural resources, the proponents come up with the thought of producing a lollipop flavored with squash. Since a kalabasa lollipop is new to hear and be first introducing to the market, the new product will add to the variety of product that the Filipino people will patronize.
Producing locally will help the Philippine economy to lessen such expenses when it comes to importation. The proponents need not to import raw materials for squash can be found in almost every part of the Philippines.
Development of Industries
The proposed business must not only focus on the profit the business will gain but also to the responsibilities it should carry socially in terms to the government and community. Business must not only assure the continues flow in economic goods and kind from the process of production to consumption but likewise must equally concern itself with a demand of a fast changing society in terms of improving the quality of life particularly with regards to employee development and education, improving product quality and better utilization of existing resources.
A. Benefits to Consumers, Suppliers, Employees and Partners
Benefits to Consumers
The very reason why many businesses exist is probably because of consumers’
needs and demands. Without the consumers I don’t think business would go a long way. Consumers must be rest assured that what the consumer wanted with the product the same way the proponents wanted it to be for the satisfaction of every person involved. Benefit to Suppliers
Suppliers are the sources of raw materials. The proponents must build a harmonious relationship where each of the parties involve benefits from each other or what is called the win-win relationship so that when in need of any supplies, it will not be hard to whom the proponents will get to purchase because at any time needed there will be a supplier to count on.
Benefits to Employees
The proposed project will be a great help to the employee of the business because it can create a never-ending opportunity for those unemployed and the profit it will generate can sustain employee’s daily living and can provide a better future for their families.
Benefit to Partners
As the business gaining profit the partners’ income also increases. In managing a business partners entrepreneurial skills and knowledge will be showcased as well as how well the partners can manage a business. Partners can also create an opportunity for growth and development in every individual endeavor. B. Social and Environmental Rate of Return
A healthy living is the advocacy of this proposed business. The business seeks to provide healthy foods to promote a healthy lifestyle especially to children not eating the very nutritious squash. The proponents made sure that the product had undergone due process for safety purposes and to maintain its cleanliness. The proponents also ensure that the proposed business follows strict rulings when it comes in disposing of waste materials, conserving energy and instilling values to its employees for the business to stay longer in the food industry.
PRODUCTS
Research Documents
AP Notes
Resource Center
STUDY TOOLS
iOS App
Android App
Citation Generator
COMPANY
About StudyMode
Blog
Contact
Help
Jobs
Internships
FOLLOW
Facebook
Twitter
Google+
RSS
©2016 StudyMode.com Legal Site Map Advertise