Inventory System Documentation
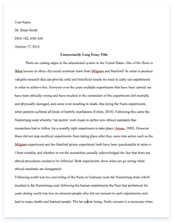
A limited time offer! Get a custom sample essay written according to your requirements urgent 3h delivery guaranteed
Order NowEfficient, fast, and effective inventory management are important factors of a store owner’s establishment. Store owners are tasked to make consistent, reliable, and timely decisions considering obstacles like uncertainty, pressure, and lack of information. It is often that store owners do not have enough time or information to make a perfect decision but they are forced to solve problems using resources within their control. Effective inventory control requires store owners to ensure inventories of the right items in the correct quantities. When the store overstocks, money is wasted since procuring, storing, and accounting for unneeded items require time, space, and money which could have been used on more critical assets. Likewise, when under-stocking occurs the store will more likely to only partly meet their mission or possibly not meet the mission at all. Also, a weak inventory control system is more prone to errors and fraud. These are some of the problems of Janilyn B. Ong Chung, Q.V. Store owner, the research client.
The Q.V. Store is a “sari-sari” store in a small compound somewhere in Arevalo, Iloilo City. Originally Sto Niño Store, it changed its name in 2007, after changing management and ownership, the Q.V. Store is known for its fast and reliable products and also for its location, making it convenient not only for the neighboring houses but for Villa Rosa’s, a beach resort right in front of the establishment, customers as well. It is a family-owned business passed from generation to generation. The store has 2 separate stock rooms for more space within the main building. Three refrigerators inside the main building are also used where beverages are stored and cooled. The second stockroom maintains the supply cases for the beverages for the three refrigerators through a manual inventory system. This research will aim to recommend an enhanced inventory control system to be used by the store’s supplies. Statement of the Problem
The study will enhance the existing inventory control system for Q.V. Store’s stocks for a better inventory management and to eliminate/reduce risks of errors and fraud. It will seek to answer what enhancement and design the store can adopt for a more effective and efficient inventory system. Specifically, it endeavors to answer the following questions: 1.What are the current policies and procedures of Q.V. Store to account for their Stocks inventory? 2.What are the strengths and weaknesses of the current inventory control system? 3.What appropriate measures should be adopted to minimize risks from the weaknesses and threats? 4.What inventory management and accounting concepts, principles, and techniques should be applied to the enhanced inventory control system? Objectives of the Study
The main goal of the study is to evaluate the current stocks inventory control system of Q.V. Store and come up with an enhanced inventory control system for the store’s stocks for a better inventory management and eliminate/reduce risks of errors and fraud. It will seek to give an enhancement and design the stocks could adopt for a more effective and efficient inventory system. Specifically, the study aimed to:
1.determine the current policies and procedures of Q.V. Store to account for their stocks inventory; 2.verify strengths and weaknesses of the current inventory control system; 3.provide appropriate measures to be adopted to minimize risks from the weaknesses and threats; and, 4.Identify inventory management and accounting concepts, principles, and techniques should be applied to the enhanced inventory control system. Significance of the Study
For Q.V. Store, the result of the study can provide the management a view of their current stocks inventory control system. Q.V. Store can adopt the recommendations to be done by the researchers to improve the efficiency and effectiveness of their stocks inventory control system. For other similar “sari-sari” stores, the study can provide insights and basis for other establishments and similar businesses to improve their system. For educators and students, the study can provide topics for classroom discussions and serve as reference for inventory management. For future researchers, this research can provide basis and references for future studies related to inventories. The researchers, being the main participants, will gain knowledge and experience to improve their skills. This research is a major requirement to complete the Documentation Finals Project in Introduction in Software Engineering. Scope and Limitations of the Study
The study intends to evaluate the current stocks inventory control system of Q.V. Store. It will focus primarily on the stocks inventory and not on the inventory of the store as a whole. It will cover products and supplies maintained in the stocks and will not involve inventory of equipments and other supplies maintained by the other departments of the store. The results of the study will be based on interviews, observation, cooperation, and answers given by the people involved in the Stocks Inventory Control of Q.V. Store, that include the store owner and other authorized personnel. Facts, concepts and related theories will be the basis of recommendation of the researchers. The study will be done at #2 Brgy Sto Niño Norte, Arevalo, Iloilo City during the Academic Year 2011. CHAPTER II
REVIEW OF LITERATURE
Inventory can be the largest investment a store can make. Dealing with inventory can be intricate unless the store has a good inventory control system. The purpose of this system is to maximize efficiency and effectiveness. Efficiency is to minimize inventory costs and effectiveness is to meet the customer demands. Inventory control involves maintaining adequate stock of supplies, as well as storing those products in a safe and secure manner. It also means keeping track of the purchasing and distribution of the goods. Good inventory control allows the store to have enough supplies on hand to fill customer demands and orders, without having so much stock that the supplies would reach its expiration date before they can be used. Inventory Acquisition
Purchasing is not just a routine function to keep inventories on the shelf. However, since stores literally spend a lot to acquire supplies and other goods, purchasing is actually a substantial investment process. According to the research of Desselle and Zgarrick (2008), the objective of purchasing is to obtain the right products in the right quantity at the right price at the right time from the right vendor. Right quantity means having just enough products on hand to cover consumer demand at any given time. In order to estimate the minimum quantity needed to meet the demand, the purchasing agent must know how many items on hand, when to order, and how much to order. Most businesses place an order for replenishment of inventory when the inventory level is already at low point.
This low point is predetermined by the management using the reorder point (ROP) system. A reorder point is simply a level of inventory that is designated as the signal to replenish. Whenever the inventory level reaches the reorder point, a replenishment order is placed. It is set such that the inventory level will reach zero at about the time the replenishment order is expected to arrive. Generally, the quantity to reorder depends on the level of demand and other factors such as market availability, storage space available, and shelf life considerations (Mercado, 2007). Formula for computing the reorder point is: ROP = (Demand per time period x Lead Time) + Safety Stock
Lead time is the period between placing an order and receiving delivery. When lead time and demand are not certain, the firm must carry out extra units of inventory, called safety stock, as protection against possible stock-outs (Siegel and Shim, 2006). Minner (2000) defined safety stock as the expected inventory just before the next order arrives. Using this technique of reordering requires a system that can track the inventory level at any given time. This can be accomplished using a perpetual accounting record or a visual method. Desselle and Zgarrick (2008) explain that too much inventory ties up store’s money without having adequate return on investment. On the other hand, having too little inventory may result in lost sales and profits when the product is not available for purchase. Not having enough products available also may result in the loss of customers in the future.
The management therefore must know the right amount of inventory to order while maintaining the right amount of stock. To determine this, the purchasing agent must identify the economic order quantity (EOQ). EOQ is the optimum amount of goods to order each time to minimize total inventory costs (Shim and Siegel, 2000). It describes the level of inventory and reorder quantity at which the combined costs of purchasing and carrying inventory are at a minimum. Purchasing or ordering costs include costs of placing the order and received goods while carrying or holding costs include the storage, handling, property tax, and insurance costs, as well as the required return rate on the inventory investment (Siegel, Shim, and Hartman, 1997). The classical formula for EOQ model is Where:
D = annual demand in units;
O = unit ordering cost;
H = annual holding or carrying cost per unit
Inventory Protection and Storage
Proper storage of inventory is vital. Improper storage can cause a product to ruin, resulting in a loss of inventory and money. According to Bizmanualz, Inc. (2008), storage refers to protecting inventory from both damage and shrinkage or theft. Damage control includes insuring and keeping inventory clean and properly sheltered. According to Yadav (2008), proper environmental control (i.e., proper temperature, light, humidity, conditions of sanitation, ventilation, and segregation) must be maintained wherever beverages and supplies are stored. Proper control is required such as expiry dates of supplies, especially food and drugs or medicinal supplies, stored must be considered. With regards to safety, proper consideration should be given to the safe storage of hazardous items, e.g. Rugby, Detergents, Cleaning Chemicals etc. Control over shrinkage is directed at human error (data entry, POS error, receiving errors, etc.) and customer or employee theft. Human error is a continual possibility. Successful business systems acknowledge this fact and incorporate preventative and detective controls to mitigate the anticipated human error.
Preventative controls include written POS procedures, supervisory control, use of logs, cash-up reports and other checklists. Detective controls include cycle inventory counts, exception reports, and gross margin analyses. Improper inventory also produce a higher risk of theft and fraud. Customer theft protection involves many elements from security to customer return policies. Businesses should focus on high-peso merchandise that can be easily hidden and carried out of the store. Also, employee theft protection must be given proper attention. Employee theft protection involves two important ingredients: maintaining a high level of security and eliminating the easy opportunities for theft. A high level of security is maintained when cycle count exceptions are followed, supplies are stored properly and shelved quickly, and unresolved damage claims, customer returns and returns to vendors are not allowed to build up. Eliminating easy opportunities for theft involves structural security as well as numerous written employee procedures.
A well-lit storage space, restricted areas, and installation of security cameras are example of structural security features. Written procedures that reduce opportunities for theft include limiting storage access only to designated personnel, mandating all authorized personnel to exit and enter only through the front door, preventing employee from ringing up a sale for him/her or family members, monitoring customer returns, and proper cash drawer and petty cash usage. Coltman and Jagels (2003) provide the following control practices that should be used for product storage: 1.Immediately after goods have been delivered and all receiving checks performed, they should be moved to storage areas or sent directly to the departments that requested them. Proper storage facilities should be used. 2.Storage areas should be locked when the storekeeper is not present. Access to storerooms should be limited to the storekeeper and other authorized personnel. 3.Storekeepers should not maintain or have access to formal inventory records, nor should employees who maintain those records have access to storerooms except to take inventories.
4.Inventory counts of stored products should be taken periodically by the store owner and compared to perpetual inventory cards (if used). A perpetual inventory card is maintained for each separate item in stock. It has recorded on it, for each item, quantities received in and quantities issued from the storeroom to provide a running balance of what should be in inventory. 5.The best procedure for taking inventory is to make two accounting employees responsible. One completes the actual physical count; the other compares this with the perpetual inventory card figure and then records the actual count on an inventory sheet. 6.If there are any significant differences that cannot be reconciled between the inventory count and what should be in inventory according to perpetual inventory cards, the differences should be investigated to determine the cause. 7.To aid in inventory count, preprinted inventory sheets that list items in the same order as they are located on storeroom shelves should be used. Inventory Obsolescence and Disposal
According to Bragg (2006), there is inevitably a certain amount of inventory that will not be used, due to excessive purchasing of materials beyond a company’s needs or customers not buying certain items. In the store’s perspective, inventory (specifically school and office supplies, medicines etc.) becomes obsolete because of its limited shelf life. Obsolete inventory can constitute a large portion of the total inventory, so it is suggested to consider giving controls in this area. Bragg further explains that the primary risks associated with obsolete inventory are that the inventory will not be promptly recognized as obsolete, that inventory will be improperly designated as obsolete, and that dispositioned inventory will be accidentally reordered. He also provided some controls dealing with these risks. Regularly complete an obsolete inventory review. The best way to ensure that obsolescence is recognized promptly is to conduct a regularly scheduled obsolescence review of the entire inventory, typically using an obsolescence report.
Move obsolete inventory to segregated area. It is much easier to review and leave as-is obsolete inventory if it is congregated in a single area rather than scattered throughout the warehouse. Match obsolescence authorization to tagged obsolete inventory. It is possible that store room employees will deliberately tag inventory as being obsolete, so they can remove it from the stocks or acquire it at a low price from the company. To avoid this problem, periodically compare the obsolete inventory review procedure to tagged obsolete inventory, to ensure that only authorized items are tagged. Any other items marked as obsolete should immediately be brought to the attention of the warehouse manager and internal audit manager as being a possible case of fraud.
Moini (2004) also provided some controls in disposing expired stock. He explains that expired, deteriorated, contaminated, or other non-reusable products should be removed immediately from usable store stock and disposed of. Expired products should be placed into containers labeled with “expired – DO NOT USE” or any similar understood warning. Disposal requirements for most drugs that have expiration date are listed in the package inserts. Expired products and their disposal should be documented regardless of whether they are put into recycle bags for collection or disposed of in any other way. Inventory Measurement and Tracking System
There are two ways to measure the inventory and cost of goods sold.
The first one is Periodic System. This method has historically been the one used by stores because it requires much less record keeping, as opined by Carroll in 2006. It is based on costing out physical counts at both beginning and ending periods. The cost of goods sold is calculated by adding purchases to the beginning inventory and subtracting the ending inventory (Toomey, 2000).
The major disadvantage of this method is the requirement of conducting a complete physical inventory count to obtain a calculation of the inventory cost. With this, calculation of the inventory will be costly and time-consuming. Accuracy may also be an issue in this procedure.
The second one is the Perpetual System. In perpetual system, detailed records of each inventory purchase and sale are maintained. This system provides a current record of inventory on hand and cost of goods sold to date (Robles and Empleo, 2007). This method keeps the accounts current and accurate because the balances are updated constantly. It continually accumulates all incoming and outgoing transaction quantities of an inventory item so that, at any time, there is a record of the current balance on hand (Mercado, 2007). Carroll (2006) provides the following advantages of the perpetual system: 1. It provides the cost of goods sold without a physical inventory. Consequently, financial statements can be generated easily and inexpensively at any time during the year. 2. It provides information that managers can use to control inventory levels. Individual inventory accounts show frequency of sales for each stock keeping unit (SKU). Managers can use this to determine optimal purchase quantities and maximum and minimum inventory levels for SKUs. 3. It provides a basis for measuring shrinkage. Shrinkage refers to the amount of inventory that is lost, broken, or stolen.
Shrinkage is estimated by comparing the inventory level recorded in the inventory account with that found by a physical inventory. The difference between these two levels represents shrinkage. Bragg (2004) pointed out that the perpetual inventory system is highly recommended because it avoids expensive periodic inventory counts, which also tend not to yield accurate results. Also, it allows the purchasing staff to have greater confidence in determining the inventory on hand for purchasing planning purposes. Accountants can complete period-end financial statements more quickly, without having to guess at ending inventory levels. Inventory Valuation
Determination of inventory cost is the major aspect of financial reporting. Whether the periodic or the perpetual system is used, it is necessary to use a specific method for the assignment of costs to the ending inventory as well as to the cost of goods sold. Assignment of costs can be complex because goods are usually purchased at different costs during the accounting period. Thus, there must be a consistent procedure in assigning costs which is called the cost-flow assumption (Eisen, 2007). There are three cost-flow assumptions that can be used. The first one is the First-In, First-Out (FIFO) Method. This is based on the assumption that the first units brought are the first units sold. The oldest cost assigned to the inventory is the cost assigned to the goods first sold. Consequently, the most recent cost is assigned to the ending inventory. Although business organizations are free to choose among a number of inventory methods, many adopt FIFO simply because there is a tendency to dispose of goods in the order of their acquisition (Eisen, 2007).
This method, though not as accurate as specifically identifying the item being sold, would give a close approximation of value. The second one is the Last-In, Last-Out (LIFO) Method. This method assumes that the most recent cost of goods acquired should be charged at the most recent sales made. Thus, the assignment of the cost to the ending inventory represents the cost of all earlier purchases, without regard to the order in which the goods are actually sold, since it is assumed that the goods are all the same and readily interchangeable (Eisen, 2007). The third one is the Weighted Average Cost Method. This method yields a cost that is representative of the cost of the product over the entire accounting period. The weighted average cost of a unit of inventory is determined and all units are assigned this cost. The average cost is weighted by the number of units purchased at each cost (Carroll, 2006). Eisen further notes that in accounting periods where costs remain relatively constant, the FIFO method is probably the most appropriate. If it is important that replacement costs relate as closely as possible to the cost of the goods sold, the LIFO method is better. The weighted average method is a third option, even though it does not necessarily bring about the matching of costs and revenue. Its simplicity may have a cost-saving effect.
Principles of Internal Control
To meet the purpose of an inventory control system, the management must apply internal controls in its business. A broad definition of internal control was given by Trenerry (1999): “A system of controls and checks instituted by the various levels of management that are independent and interdependent and are integrated into the financial and non-financial activities and operations of a business to ensure that the business operations are conducted efficiently and effectively and operating results for all aspects of the business are reliably reported to ensure management decision-making is well based and that all relevant laws and regulations are complied with.” The objectives of internal control are to provide reasonable assurance that: (1) assets are safeguarded and used for business purposes; (2) business information is accurate; and, (3) employees and managers comply with laws and regulations (Warren, Reeve, and Duchac, 2008). Coltman and Jagels (2003) discuss some basic principles that provide a solid foundation for a good internal control. Some of them are the following: Establish preventative procedures.
Internal control procedures should be established so that they minimize and/or prevent theft. This is much more effective than suffering losses from theft or fraud and having a system that detects the culprits only after the event. Establish management supervision. Complete absence of any controls will yield some employees to temptation and become dishonest. If management does not care, why should the employees? Monitor control systems. Any system of control must also be monitored to ensure that it is continuing to provide the desired information. The system must therefore be flexible enough to be changed to suit different needs. Establish responsibilities and prepare written procedures. Once the designated person is established, that person must be given a list of receiving procedures, preferably in writing, so if errors or discrepancies arise, that person can be held accountable. Maintain adequate records. Another important consideration for good internal control is to have good written records.
Without good records, employees will be less concerned about doing a good job. Separate record keeping and control of assets. One of the most important principles of good internal control is to separate the functions of recording information about assets and the actual control of the assets. Limit access to assets. The number of employees who have access to assets such as cash and inventory should be limited. The larger the number of employees with access, the greater is the potential for loss from theft or fraud. Divide the responsibility for related transactions. Responsibility for related transactions should be separated so the work of one person is verified by the work of another. This is not to suggest duplication of work—that would be costly—but to have two tasks that must be carried out for control reasons done by two separate employees. This procedure keeps one person from having too much control over assets and may prevent their theft. Set standards and evaluate results.
One of the requirements of a good internal control system is not only to control the obvious visible items, such as cash or inventory, but also to have a reporting system that indicates whether all aspects of the business are operating properly. Once procedures have been established and the various employees have been given detailed written guidelines about how to perform tasks, standards of performance should be established. Create an audit trail. Most good internal control systems are based on having an audit trail that documents each transaction from the time that it was initiated through source documents and defined procedures through to the final recording of the transaction in the operation’s general ledger. A good audit trail allows each transaction, where necessary, to be tracked again from start to finish. Supervise the system and conduct reviews. One of management’s major responsibilities in internal control is constant supervision and review of the system. This supervision and review is necessary because the system becomes obsolete as business conditions change. Also, without continuous supervision the control system can collapse. Definition of Terms
Cost-flow assumption – is the beginning point used to determine the value of the ending inventory and the cost assigned to the cost of goods sold (Eisen, 2007).
Economic Order Quantity (EOQ) – it is the optimum amount of goods to be ordered each time the inventory level drops at the pre-determined reorder point.
First-In, First-Out (FIFO) Method – it is a cost-flow assumption generally
use by business entities in assigning cost to their inventories. This method assumes that the first units brought are the first units sold.
Internal control – it is a system of procedures and forms established in a business to safeguard its assets and help ensure the accuracy of the information provided by its accounting system.
Inventory – it is an asset acquired and maintained by an entity which are held for sale or as supplies in the business operations.
Inventory control system – it is a set of policies and controls that monitors level of inventory and determines what levels should be maintained, when stock should be replenished, and how large orders should be.
Lead time – it is the period between placing an order and receiving delivery used in the computation for economic order quantity (EOQ).
Last-In, Last-Out (LIFO) Method – this method assumes that the most recent cost of goods acquired should be charged at the most recent sales made
Periodic system – it is an inventory tracking system that determines inventory levels only at fixed points in time through the use of physical inventory counts (Bragg, 2004).
Perpetual system – it is an inventory tracking system that determines inventory levels on an ongoing basis by making incremental adjustments to inventory records based on individual production transactions (Bragg, 2004).
Safety stock – it is the buffers or reserve stock kept on hand to protect against stock outs caused by delayed deliveries or increased demand.
Reorder Point (ROP) – it is the designated inventory level at which it is appropriate to replenish stock (Siegel, Shim, and Hartman, 1997). It is set such that the inventory level will reach zero at about the time the replenishment is expected to arrive.
Weighted average method – it is a cost-flow assumption that yields a cost that is representative of the cost of the product over the entire accounting period. The average cost is weighted by the number of units purchased at each cost (Carroll, 2006). Synthesis
This chapter discussed the related literatures about the inventory control system. The discussion started with the purpose of an inventory system and its scope. Functions of an inventory system, which are inventory acquisition, inventory protection and storage, and inventory obsolescence and disposal are also discussed. In the inventory acquisition section, the chapter provides some key points basically used in purchasing such as the reorder point (ROP) system and the economic order quantity (EOQ) model. In inventory protection and storage, controls against damage and shrinkage (due to human error or customer or employee theft) are provided. Meanwhile, in inventory obsolescence and disposal, control measures for obsolete stock are discussed in both accounting and stocks perspectives. Accounting concepts are included in the discussion of inventory measurement and tracking system and inventory valuation.
Two systems of inventory measurement, which are the periodic and perpetual system, are used to determine the number of units. Cost-flow assumptions, which are used in determining the value of inventory, have three different methods namely, FIFO, LIFO, and weighted average method. These methods provide certain advantages depending on the type of business. The concept of internal control is also included in this chapter. Some basic internal controls provided in this chapter will aid in the efficiency and effectiveness of an inventory control system. These reviews will serve as guideline in the study of enhancement of the stocks inventory control system for Q.V. Store. Theoretical Framework
The theoretical framework that will be used in this study is the Input-Process-Output Model. In the IPO model, a process is viewed as a series of boxes (processing elements) connected by inputs and outputs. Information of material objects flow through a series of tasks or activities based on a set of rules or decision points. Flow charts and process diagrams are often used to represent the process. What goes in is the input; what causes the change is the process; and what comes out is the output (Harris and Taylor, 1997). Figure 1 illustrates the basic IPO model:
Figure 1. Basic IPO Model
The IPO model will provide the general structure and guide for the direction of the study. Substituting the variables of this study on the IPO model, the researchers came up with the conceptual framework. Conceptual Framework
Handling stocks in every organization is an important issue in every business. A well-structured inventory system would give the organization proper control of their stocks. This study will be using the input-process-output diagram to come up with an enhanced stocks inventory control system for Q.V. Store. Input. The first variable is the current stocks inventory control system of Q.V. Store as provided based on interviews and observations by the researchers. It will include policies and procedures provided by the management currently implemented for purchasing, receiving, storage, issuing and reporting of inventory. Process. After identifying the inputs, the current stocks inventory control system of Q.V. Store will be evaluated using the SWOT analysis.
After the strengths and weaknesses of the current system are identified, the enhancement of the current stocks inventory control system of Q.V. STORE will follow. During this phase, management and accounting theories, concepts, and techniques will be followed to enhance the current system. Also, the organizational requirements of Q.V. STORE will be taken into consideration for the enhancement. Before the final output, feedback from the management will be taken for comments and suggestions to be added for the final output. Output. The output will be the result of the careful analysis and discussion of the researchers and the client’s management. The output will be an enhanced stocks inventory system for Q.V. STORE to be recommended for the client.
Figure 2 shows the conceptual framework of the study using the input-process-output diagram.
INPUT
PROCESS
OUTPUT
Figure 2. Conceptual framework
CHAPTER III
RESEARCH METHODOLOGY
The purpose of this chapter is to explain the methods and procedures to be followed in the research project. This chapter will review the research questions of the study, the research design used to carry out the study, the tools used to gather data, the research respondents, and the procedures to be used for conducting the study. It will also include an overview of how to treat research data gathered by the researchers. Research Design
The study will use an action type of research to assess the current stocks inventory control system of Q.V. STORE. The researchers will be using a descriptive methodology to describe the issues and topics in the stocks inventory system of Q.V. STORE. Research Locale
The study will be conducted at Q.V. STORE located #2 Brgy Sto Niño Norte, Arevalo, Iloilo City. The stocks inventory control system of the establishment will be the focus of the study because of the store’s need for a better, more efficient and effective system to be adopted for more security and control. Research Respondents
The researchers will gather the information through the following respondents: the establishment’s owner and attendants of Q.V. STORE. These personnel will provide imperative aid to complete the study. Research Gathering Tools
The researchers will conduct personal interviews with the chosen respondents to inquire about the implemented policies and procedures of Q.V. STORE. Questionnaires will also be at hand to seek further information about their inventory control procedures. These questionnaires will have close-ended questions and/or “yes or no” questions. Moreover, the researchers will carry out non-participant observations and walk-through observations to verify the results of the interview and questionnaires. Secondary data, which will be taken from related literatures, will be used to support the enhancement of the current inventory system. Data Gathering Procedure
To start with the process, the researchers will provide a letter of request asking for their permission to conduct the study. After the approval, personal interviews and walk-through observation will be scheduled and questionnaires will be prepared. The respondents will be given enough time to answer the questionnaires. During the interview, there will be a thorough discussion with the respondents of their inventory control management. The walk-through observation will be conducted on the same day of interview. Researchers will have a closer look of how the organization’s policies and procedures are performed and complied. A non-participant observation to be done separately from the walk-through observation will verify the undertaken walk-through observation and interviews.
Treatment of Data
The researchers will use qualitative analysis of the information gathered from the interview, and questionnaires. The analysis will be graphed into a flowchart to show the results and to give a clear view of Q.V. STORE’s current inventory control system. Results of the observations will also be taken into consideration. From the results of the qualitative analysis, data will be processed using the SWOT analysis to identify strengths and weaknesses. The review of literature will be used to improve the current system of Q.V. STORE. RESEARCH INSTRUMENTS
Questionnaire
This questionnaire will be used in gathering the primary data needed in conducting the study. The questions are based on inventory controls.
Inventory Acquisition
Are inventories maintained at a level as to avoid consistent stock-outs, or spoilage/obsolescence? Are reorder points established for key stock items?
Is responsibility for purchasing and invoice approval assigned to provide division of duties?
Inventory Protection and Storage
Does the facility have a proper environmental control (i.e., proper temperature, light, humidity, conditions of sanitation, ventilation, and segregation)? Are inventories arranged so that the earliest received will be issued first? Is there physical control over inventory stock?
Is the person responsible for inventory someone other than the records bookkeeper?
Inventory Obsolescence and Disposal
Are damaged and obsolete goods physically segregated?
Inventory Measurement and Tracking System
Are periodic physical inventories taken?
Are perpetual or periodic inventory records maintained to reflect value and quantities of inventories? Are stock item activity reports maintained for each stock item?
Inventory Valuation
Has an acceptable inventory valuation method been adopted?
Other Controls
Are all inventory transactions evidenced by the proper supporting documentation, i.e., purchase orders, requisitions, adjustment memos, physical counts, etc.? Are effective control procedures established to ensure that inventories are used properly and for authorized purposes?
CHAPTER IV
RECOMMENDATIONS
From the information given from the previous chapter, it was observed that there were a limited number of employees in Q.V. STORE. Also, it was observed that these employees have limited knowledge in accounting. The researchers propose a simple yet effective inventory control system to be adopted by the stocks. The researchers recommend the following policies and procedures for the enhancement of stocks inventory control system: Purchasing
ROP system and EOQ model. The researchers suggest the management to establish ROP for each items classified under the ABC analysis and also the implementation of EOQ model in purchasing inventory. This is to resolve the issue of overstocking and/or understocking of inventory that leads to inventory loss or customer dissatisfaction. Once established, the management must update this regularly. Pre-numbered Purchase Orders (PO). Due to the limited number of employees, the pharmacist could be the one to prepare the PO to be approved by the manager. Purchases must be in sequential order. The researchers also recommend the management to require the following information in each PO:
1.Complete description of each item (i.e., brand name, common name, and other specifications)
2.Quantity required
3.Date required
4.Recommended vendor or source
5.Shipping requirements
Criteria for selecting vendor/supplier. To minimize the problems occurring in purchasing goods, the researchers advocate the following criteria in selecting their suppliers: 1.Have you ever reviewed existing purchasing procedures to see if they meet your needs? 2.Do you have specific policies and procedures regarding who is authorized to purchase goods or services? Receive salespersons’ calls? Place requisitions? Process records? 3.Have you ever discussed your purchasing function with other stores or with professional businesses to obtain suggestions or techniques? 4.Have you ever visited or investigated your existing or potential vendors to verify that they can meet your requirements in terms of price, quality, quantity, and service? 5.Does your volume of purchasing for any particular item warrant you’re dealing directly with its manufacturer? 6.Do your vendors have regular and competent sales personnel? 7.Have you had problems with suppliers in regard to shortages? Backdoor selling? Delivery delays? Unsolicited favors and gifts? Receiving
Reject deliveries not having purchase order support. The receiving manager should reject all supplier deliveries for which there is no authorizing purchase order, or for which there is not a sufficient authorized quantity to cover the unit quantity of the delivery. Inspect and count the goods received. Once goods are received, the attendant should inspect the goods to see if requirements are complied with and count the goods to see if goods ordered are actually received. Blind Copy Purchase Order. The manager should provide the attendant with a blind copy of purchase order. This blind copy provides the list goods ordered excluding the quantity. The attendant needs to fill up the blanks and submit back to the manager. This is another control for securing the inventory count. Receiving Report. The receiving staff must prepare a receiving report to document the receipt of goods. Storage
ABC analysis. The researchers propose that the stocks use the ABC analysis for their inventory classification. This will determine the importance of items and the level of control placed on the items. This gives a close control to fast moving and items with high value. Class A items or the items with the highest value should be given more level of importance. To follow this theory, the researchers propose that the management conduct a semi- monthly physical count for Class A items. Class B items should be physically counted monthly. While Class C items being given the lowest importance should be counted every three months. A thorough explanation of the ABC analysis is included in Chapter 2. Stock rotation. This is an important inventory management principle that encourages the use of products before they expire and helps prevent the use of expired products.
Under this method, expiration date of newly ordered products should be compared with that of the existing stock. Products that have already expired should be removed. Products that will expire in the near future should be highlighted and placed in the front of the shelf or bin. Segregate items subject for disposal. Obsolete inventory should be segregated from the current stock. Those items that requires disposal should be transferred to another room. The manager may decide to return the goods to original supplier. Restrict access to stockrooms. The management should determine as to which employee can have access to the stockroom. In the researcher’s subject, it is the listed authorized personnel. Other employees should be prohibited in entering the stockrooms. Regular check of the facilities. It is important that the facilities, especially the stockrooms, are checked regularly for any possible cause of inventory loss like fire or water leaks. It should be ensured that all are in proper condition. Issuing
Stock cards. The researchers advocate the use of stock cards to keep record of transactions for each item. This card shows the receipt and issuance of the item including the quantity and cost. This is to complement the implementation of perpetual inventory system. Perpetual inventory system. This requires continuous recording of every transaction that relates to inventory. This would minimize errors in determining the number of inventory at hand. Reporting
Inventory valuation. The management should determine the valuation of inventory to prevent misreporting. Without this, inventory may either be understated or overstated. Researchers suggest the use of FIFO method. Elaborate discussion of this method is included in Chapter 2. The researchers also provided a flow chart which illustrates the recommended duties of each staff and the flow of the inventory system of Q.V. STORE which is shown below.
Figure 4. Flowchart of duties and flow of inventory system of Q.V. Store
SUMMARY
The study aimed to investigate the current stocks inventory control system of Q.V. STORE. Weaknesses were identified through careful examination of the system. Management and all other people involved were interviewed and given a set of questions to give the researchers a clear view of their system. Non-participant observations were also made to verify the data gathered from the interview and questionnaires. The inventory control system of Q.V. STORE was composed of five stages namely, Purchasing, Receiving, Storage, Issuing, and Reporting. In Purchasing, request for replenishment was sent when there was a little buffer inventory left. The management does not use ROP system and EOQ model as part of their purchasing procedures. The manager would simply make a call to their suppliers; no Purchase Order (PO) form was prepared to document the purchase.
In Receiving, the pharmacist would inspect and count the goods delivered. No Receiving Report (RR) was prepared and physical count was not supervised. The goods received would be brought to the stocks or stockroom. There were no existing logbooks as to record the receipt and issuance of goods. Also, there was no proper valuation of inventory. Hence, reporting of their inventory is not reliable. From the gathered data, the researchers assessed that the current stocks inventory control system of Q.V. STORE is relatively weak and lacks control for security. It was also observed that employees in Q.V. STORE had relatively low knowledge about accounting which convinced the researchers to create a simple and easy to learn enhanced inventory system for the stocks.
CONCLUSION
Inventory management is crucial for most companies, but it is especially crucial for small businesses like Q.V. STORE because when compared with large companies, they usually have limited resources and bargaining power, which have negative effects on the way the inventory can be managed. This thesis is trying to propose an enhanced inventory control system for a small organization like Q.V. STORE. Establishing policies and procedures is the major step in starting an inventory control. These policies and procedures must be implemented and the management must see to it that everyone in the organization complies with it. A good inventory system does not need several employees to implement segregation of duties and avoid conflict of interests. Proper documentation and supervision of transactions should be given more focus.
References
Askew, G., & Stoner, Marilyn, S. (2001). Assisting in the pharmacy. Florence, Kentucky: Cengage Learning.
Bizmaualz, Inc. (2008). Accounting and bookkeeping procedures for internal control. St. Louis, MO: Author.
Bragg, S. M. (2004). GAAP implementation guide. Hoboken, New Jersey: John
Wiley & Sons, Inc.
Bragg, S. M. (2005). Inventory accounting: A comprehensive guide. Hoboken, New Jersey: John Wiley & Sons, Inc.
Bragg, S. M. (2006). Accounting control best practices. Hoboken, New Jersey: John Wiley & Sons, Inc.
Carroll, N. V. (2006). Financial management for pharmacists: A decision-making approach (3rd ed.). Boca Raton, Florida: Lippincott Williams & Wilkins.
Coltman, M. M., & Jagels, M. G. Hospitality management accounting (8th ed.). Hoboken, New Jersey: John Wiley & Sons, Inc.
Desselle, S. P., & Zgarrick, D. P. (2008). Pharmacy management: Essentials for all practice settings (2nd ed.). New York: McGraw-Hill Companies.
Duchac, J, Reeve, J. M., & Warren, C. S. (2008). Financial and managerial accounting (10th ed.). Florence, Kentucky: Cengage Learning.
Eisen, P. J. (2007). Accounting (5th ed.). New York: Barron’s Educational Series.
Empleo, P. M., & Robles, N, S. (2007). Intermediate Accounting (Vol. 1). Mandaluyong City: Millenium Books, Inc.
Hartman, S., Shim, J. K., & Siegel, J. G. (1997). Schaum’s quick guide to business formulas: 201 decision-making tools for business, finance, and accounting students. New York: McGraw-Hill Companies.
Mercado, E. C. (2007). Hands-on inventory management. Boca Raton, Florida: Auerbach.
Minner, S. (2000). Strategic safety stocks in supply chains. New York:
Springer.
Moini, J. (2004). The pharmacy technician: A comprehensive approach. Florence, Kentucky: Cengage Learning.
Peterson, A. M. (2004). Managing pharmacy practice: principles, strategies, and systems (Vol. 18). USA: CRC Press
Shim, J. K., & Siegel, J. G. (2000). Financial management (2nd ed.). Hauppauge, New York: Barron’s Educational Series.
Toomey, J. W. (2000). Inventory management: principles, concepts and techniques. New York: Springer.
Trenerry, A. (1999). Principles of internal control. Sydney, Australia: UNSW Press.
Yadav, A. V. (2008). Hospital and clinical pharmacy (15th ed.). Tamil Nadu: Pragati Books Pvt. Ltd.