How to Do Production Planning and Control
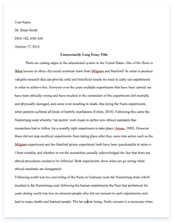
- Pages: 15
- Word count: 3552
- Category: Industry
A limited time offer! Get a custom sample essay written according to your requirements urgent 3h delivery guaranteed
Order NowObjectives
β’ The ultimate objective of production planning and control, is to contribute to the profits of the enterprise. β’ this is accomplished by keeping the customers satisfied through the meeting of delivery schedules. β’ Specific objectives of production planning and control are to establish routes and schedules for work that will ensure the optimum utilization of materials, workers, and machines β’ and to provide the means for ensuring the operation of the plant in accordance with these plans.
Components of PP
β’ SOP: Sales and operations planning β’ DRP: Distribution Requirements Planning β’ MRP: Materials Requirement Planning
DRP
β’ The objectives of Distribution Resource Planning (DRP) in the SAP R/3 System are: β’ To improve customer service levels by anticipating customer demand at distribution centers and providing finished products at the correct location when customer needs arise. β’ To provide an accurate requirements plan for manufacturing. β’ To optimize the distribution of available stock in the distribution network using the deployment function. β’ Deployment lets you take action when a requirements shortage or surplus is calculated as a result of DRP runs. Deployment uses algorithms for “fair share” distribution when demand exceeds supply and “push,” “pull,” or “pull/push” distribution when supply exceeds demand.
Sales & Operations Planning
β’ Sales & Operations Planning (SOP) is a flexible forecasting and planning tool with which sales, production, and other supply chain targets can be set on the basis of historical, existing, and estimated future data. β’ Rough-cut planning can also be carried out to determine the amounts of the capacities and other resources required to meet these targets. β’ Use SOP to streamline and consolidate your companyβs sales and production operations. β’ SOP is particularly suitable for long- and medium-term planning.
MRP
β’ The main function of material requirements planning is to guarantee material availability, that is, it is used to procure or produce the requirement quantities on time both for internal purposes and for sales and distribution. β’ This process involves the monitoring of stocks and, in particular, the automatic creation of procurement proposals for purchasing and production.
Production Planning
β’ The function of Demand Management is to determine requirement quantities and delivery dates for finished products assemblies. β’ Customer requirements are created in sales order management. β’ To create a demand program, Demand Management uses planned independent requirements and customer requirements.
KANBAN Production control method
β’ A system of continuous supply of components, parts and supplies, such that workers have what they need, where they need it, when they need it. β’ This is called a “pull” type of production system. The number of items that are made depends on the customer demand
Production Process
β’ β’ Production Proposal: This may come from MRP, Sales Order, manual or any number of ways Capacity: This is optional. Capacity will check to ensure you have enough manufacturing capacity to meet the production requirements need to make a product Release and schedule: These may two completely independent functions. You may want to schedule independently to maximize capacity or minimize cost then release the orders. Shop floor documents : These go along with the order on the floor. Many organizational use completely electronic shop floor control documents. Good issue (raw materials) These are consumed in the manufacturing process Completion confirmation: The product is now finished and often times just sitting at the end of the production line waiting to be put away. Goods receipt of finished product: Putting away of the product Order settlement: How much did it cost. Now, we can review the variances against expectations.
PP module
β’ PP modules are use mainly in the Manufacturing industry. β’ This component allow you to create BOM, routing, work center, plan orders, production order and confirmation. β’ It is tightly integrated with modules such as MM and SD thru the use of MRP which is also part of PP
Flow of Production Planning
Customer order management Demand management
I/P MRP BOM
Purchase requisition
Planned order
Define work center
Routing
Goods issue
Release order
Order confirmation
Order settlement
Flow of PP
β’ Demand generation thru demand management calculates the quantities to produce and the time for the final assembly β’ data from demand management is transferred to MRP. The data from demand mgt can come from Customer Sales Order (firm) or Planned Order (forecast).
β’ MRP checks for the availability of material at various stages of BOM. β In case material is not available MRP generates planned order and Purchase requisition for production of components in house and procurement from vendor respectively.
β’ The planned orders are converted into production order by the planner and the purchase requisition are converted into purchase order by the purchaser.
β’ Production in charge converts the planned order to production order and carries out the production activities once the order is released for production. β’ Production is carried out as per the operation steps provided in the routing. β’ Work centers are also mentioned with each operation in the routings where these operations are to be carried out. β’ Once the production is completed production confirmation is done and goods movement (delivery created) takes place
β’ Capacity planning is yet another part of PP which planes the capacities for various work centers. β’ MPS is another tool which is used to plan out the master products. β If MPS is to be run the inputs are provided from demand management to MPS.
β’ The out put from MPS is then feed into MRP.
Repetitive manufacturing
β’ Repetitive manufacturing is period based planning and not based on orders.
β’ Normally same products will be manufactured over longer period of time. β’ not manufactured in individually defined lots. β’ Instead, a total quantity is produced over a certain period at a certain rate. β’ Products will not change frequently.
Discrete Manufacturing
β’ A typical characteristic of discrete manufacturing is the frequent switching from one manufactured product to another. β’ The products are typically manufactured in individually defined lots, the sequence of work centers through production varying for each one of these. β’ Costs are calculated on the basis of orders and individual lots.
β’ Discrete manufacturing typically involves varying the sequence of work centers through which the products can pass during production. β’ The order of work centers is determined in routings, which can often be very complex. β’ There can be waiting times between the individual work centers. β’ Also, semi-finished products are frequently placed in interim storage prior to further processing.
β’ Repetitive Manufacturing involves a relatively constant flow on production lines. β’ Semi-finished products are usually processed further immediately without being put in interim storage. β’ Routings tend to be relatively simple
β’ In discrete manufacturing, component materials are staged with specific reference to the individual production lots. Completion confirmations for the various steps and processes document the work progress and enable finetune controlling. β’ In Repetitive Manufacturing, components are often staged at the production line without reference to a particular order. Completion confirmations are less detailed, and the recording of actual data is simplified.
Production Planning & Execution
Forecasting
β’ Based on SIS and CO-PA β’ Foundation for a reliable SOP β’ Forecasting models
are available β Seasonal β Trend β Can be manual or automatically selected
SOP
β’ Forecasting results in SOP. β’ Flexible forecasting and planning tool β’ Sources of SOP β Sales, marketing, manufacturing, accounting β HR, purchasing
β’ Three steps in SOP
β Sales plan β Production plan β Rough cut capacity plan
Demand management
β’ Link between SOP and MPS/MRP β’ Result of DM is called the demand program. β’ It is generated from planned independent requirements and customer independent requirements. β’ Planned Independent Requirements are planned production or sales quantities that are based on some sort of forecast procedure (e.g. Material Forecast or S&OP procedure). These numbers are used in MRP to calculate procurement and/or production quantities for a material.
Demand Management
β’ The function of Demand Management is to determine requirement quantities and delivery dates for finished products assemblies. β’ Customer requirements are created in sales order management. β’ To create a demand program, Demand Management uses planned independent requirements and customer requirements. β’ To create the demand program, you must define the planning strategy for a product. β’ Planning strategies represent the methods of production for planning and manufacturing or procuring a product.
Planning Strategy
β’ To create demand program, planning strategies needs to be defined for a product β’ Planning strategies represent the methods of production for planning and manufacturing or procuring a product. β’ Using these strategies, one can decide if production is triggered β by sales orders (make-to-order production), β or if it is not triggered by sales orders (make-to-stock production).
β’ One can have sales orders and stock orders in the demand program. β’ If the production time is long in relation to the standard market delivery time, one can produce the product or certain assemblies before there are sales orders. In this case, sales quantities are planned, for example, with the aid of a sales forecast.
Made To Stock (MTS) Cycle
β’ The Made to stock scenario will start from Demand Management here we can create Planed independent requirements manually or by using data from SOP. β’ After MRP run system will create planned orders which we can convert to Production order β’ As the Stocks produced there off are not customer stock or the stock is not attached to any specific customer. β’ Further confirmations are done and issues of material are carried out to the production order. β’ Finally the production is put in to stock (GR).
Made to order (MTO)
β’ In the Made to order production, sales order produced are converted in to production order during MRP run. β’ The production orders created have a specific quantity, specific Basic start date and a specific Basic Finish Date, a set of operations and a set of component attached from the BOM. β’ In course of production the quantities produced in the operation for an order should be confirmed so that the current status of work is available in real time situation. β’ The components required for production are issued to the production order through goods issue by a movement type 261 and the issue is always made to the reservations or to the order, thereby clearing the reservations. β’ Issues of unplanned components are made as new items issue and not as order issue. β’ The quantities, for an order which are produced completely are the put in to stock i.e. a Goods Receipt is done.
MPS
β’ Master production scheduling (MPS) is a form of MRP that concentrates planning on the parts or products that have the great influence on company profits or which dominate the entire production process by taking critical resources. β’ These items are marked as βAβ parts (MPS items) and are planned with extra attention. T β’ hese items are selected for a separate MPS run that takes place before the MRP run. β’ The MPS run is conducted without a BOM explosion so that the MRP controller can ensure that the Master schedule items (MSI) are correctly planned before the detailed MRP run takes place.
β’ MPS operates within only one level of the BOM, While MRP can be utilized throughout all levels of a materialβs BOM. β’ If a MPS is run on a material, the necessary orders are planned at that level. β’ Dependent requirements (if any) are placed on the next BOM level down, and then the process stops
Material Requirements Planning (MRP
β’ A set of techniques that uses bill of material data, inventory data, and the master production schedule to calculate requirements for materials. β’ It makes recommendations to release replenishment orders for material. β’ it is time-phased, it makes recommendations to reschedule open orders when due dates and need dates are not in phase. Time-phased MRP begins with the items listed on the MPS and determines β’ (1) the quantity of all components and materials required to fabricate those items and β’ (2) the date that the components and material are required. Timephased MRP is accomplished by exploding the bill of material, adjusting for inventory quantities on hand or on order, and offsetting the net requirements by the appropriate lead times.
β’ Planned Independent Requirements (PIR)
β Planned Independent Requirements are planned production or sales quantities that are based on some sort of forecast procedure (e.g. Material Forecast). These numbers are used in MRP to calculate procurement and/or production quantities for a material.
β’ (Planned) dependent requirements
β Dependent requirements is demand that is dependent on another material. E.g. components of a bill of material are often planned on the basis of the demand for the material of which it is a part.
Example
β’ A company plan to sell 200 bikes in the month of January 2009 based on sales in the same month of 2008. These 200 bikes is a Planned Independent
Requirement for 01/2009. β’ Since every bike is produced using two pedals the 200 bikes you plan to sell in January 2009 results in 400 pedals you need to procure. These 400 pedals is a planned dependent requirement for 01/2009. β’ On the basis of these numbers MRP can calculate including current stock levels how much bikes and pedals you actually need to produce/procure.
Material Requirements Planning
β’ MRP is carried out using current and future sales figures. The planned and the exact requirement quantities trigger the net requirements calculation. β’ The requirement elements of this calculation include sales orders, planned independent requirements, material reservations, dependent requirements received from BOM explosion, and so on. β’ The net requirements calculation can give the exact requirements for each day. β’ As you require exact requirement quantities for MRP, this means that you can work with particularly low safety stocks.
MRP-5 logical steps
β’ β’ β’ β’ β’ Net requirements calculation Lot size calculation Procurement type Scheduling BOM Explosion
Net requirements calculation
β’ In MRP, requirement quantities are maintained in the system as: β planned independent requirements, customer requirements, dependent requirements, material reservations as well as forecast requirements. β’ The system checks every exact requirement and every forecast requirement to determine whether they are covered by available warehouse stock and/or receipts (purchase orders, firmed order proposals, production orders, and so on).
β’ Available stock is calculated as follows: Plant stock (-)Safety Stock + Receipts (purchase orders, firmed order proposals, production orders) – Requirement quantities (e.g. independent and customer requirements, material reservations, forecast requirements for unplanned additional requirements)
Available stock β’ A shortage occurs if available stock is negative, β’ that is, the requirement quantities are greater than expected receipts and
stock.. β’ The system specifies the date of the issue (for example, customer requirement, planned independent requirement, reservation, forecast requirement) as the requirements date.
Lot Sizing
β’ Lot-sizing procedures serve to calculate the procurement quantities, that is, the purchase order and production quantities. β’ Static β In static lot-sizing procedures, the procurement quantity is calculated exclusively by means of the quantity specifications entered in the material master.
β’ Periodic
β In period lot-sizing procedures, the system groups several requirements within a time interval together to form a lot.
β’ Optimum
β In static and period lot-sizing procedures, the costs resulting from stock keeping (from the setup procedures or from purchasing) are not taken into consideration. β The aim of optimum lot-sizing procedures, on the other hand, is to group shortages together in such a way that costs are minimized. β These costs include lot size independent costs (setup or order costs) and storage costs.
β’ If you order often, you will have low storage costs but high order costs due to the high number of orders. If you only seldom place orders then you will find that your order costs remain very low, but your storage costs will be very high since warehouse stock must be large enough to cover requirements for a much longer period.
Procurement Type
β’ External
β Purchase requisition β Purchase order β Schedule line
β’ Internal
β Planned order β Production order β Process order
Scheduling
β’ During the net requirements calculation, the system determined the shortage quantities and material shortage dates. β’ During the procurement quantity calculation, the system calculated the procurement quantities necessary for covering requirements. β’ During scheduling, the system determines start and finish dates for the procurement elements of materials that are produced in-house and for materials that are procured externally.
BOM Explosion
β’ The BOM is exploded and the dependent requirements are determined within MRP during the planning run, after the system has performed the procurement quantity calculation, lot-size calculation and scheduling. β’ The bill of material is exploded for every new procurement proposal for an assembly during the planning run. β Dependent requirements, which mean the required quantities, are determined for all the assemblies and components needed to produce the product.
Consumption-Based Planning
β’ Consumption-based planning procedures use past consumption data (historical data) to calculate future requirements with the help of the material forecast or static planning procedures. β’ Consumption-based planning procedures have no reference to the master plan. β’ This means that the net requirements calculation is not triggered by an independent or a dependent requirement. Instead, the net requirements calculation is triggered when stock levels fall below a reorder point or by forecast requirements calculated from past consumption data. β’ The advantage of this type of planning is that it is easy to use and you do not require extensive data.
β’ The aim of material requirements planning is to tailor available capacities and receipts on time to suit requirements quantities. MRP or consumption-based planning is used for this. A special form of MRP is master production scheduling. β’ Material requirements planning is carried out using current and future sales figures. The planned and the exact requirements quantities trigger the net requirements calculation. β’ In Master production scheduling , finished products and important assemblies, so called master schedule items, are planned separately and with extra attention. Only the master schedule items are planned in this planning run. The system creates dependent requirements for the BOM level directly below the planning level.
β’ Consumption-Based Planning uses past consumption data historical data) to calculate future requirements with the help of the material forecast or statistical planning procedures. The net requirements calculation is not hereby triggered by an independent or dependent requirement, but is triggered either when stock levels fall below a reorder point or by forecast requirements.
Orders
β’ Planned order
β A request created in the planning run for a material in the future β Converts to either production order or purchase order
β’ Production order
β A request to internally produce a specific product at a specific time
β’ Purchase order
β A request to a vendor for a material at a specific time
Manufacturing Execution Process
Production order Capacity Planning Schedule and release Shop floor documents Goods issue Order confirmation Goods receipt Order settlement
Production order
β’ Used to control production operations and associated costs β’ They define β Material produced β In what qty, in which location, at what timeline, labor involved, resources used β How to settle costs
Schedule
β’ Calculates production dates and capacity requirements for all operations in an order β Determines routing β Work center
Release
β’ Header level
β All operations are released for processing
β’ Operation level
β Individual operations within an order are released
Availability check
β’ Automatic check to see whether the components, PRT or capacities in an order are available β’ Generates an availability log
Schedule & Release
β’ Once order is released, it is ready for execution β’ Print shop floor documents (????) β’ Execute goods movements β’ Accept confirmations against the order
Shop floor documents
β’ Operation based lists
β Time slots, confirmation slips
β’ Component based lists
β Material withdrawal slips
β’ PRT Lists
β Drawings, blueprints
β’ Multi-purpose lists
β Operation control tickets
Confirmations
β’ Monitor and track the progression of an order through its production cycle β’ Operation level β’ Order level β’ Data that needs confirmation include: β β β β β β β quantities, Activity data-machine time Dates Employee Work center Goods movement PRT usage
Production Resources and Tools (PRT)
β’ Unlike machines and fixed assets, production resources and tools (PRTs) are movable (not stationary) operating resources that are required to perform an activity and can be used repeatedly. β’ For example, PRTs include documents, engineering drawings, jigs and fixtures, and measurement instruments. β’ You can assign production resources/tools to internal and external activities. You use the assignment to determine: β The quantity β The operating time β The dates of the PRTs required to carry out the activity.
Backflushing
β’ It is an automatic accounting (Goods issues) of material consumed for production, at the time of confirmation. β’ Eg. When a 4 wheeler automobile is rolled out from assy line, 4 wheels & Tyres are deemed to be consumed and issued to production order automatically by way of backflushing by the system. β’ Backflush is used for material which are a must and having fixed relationship