Cost Accounting and the Lean Production Philosophy
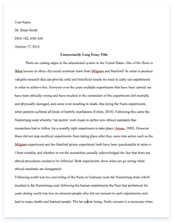
- Pages: 4
- Word count: 912
- Category: Accounting Philosophy
A limited time offer! Get a custom sample essay written according to your requirements urgent 3h delivery guaranteed
Order NowAs Dr. Stephanie White prepares to cope with the a steep reduction in the budgetary allocation to the Uptown Clinic she must carefully determine which areas to cut while striving to maintain current levels of service. This essay will offer advice Dr. White on preparing for budget cuts. It will also discuss the lean production philosophy and how this compares with typical production. This essay will also describe the differences between managerial accounting and cost accounting.
There are many strategies that Dr. White could employed to adequately mitigate the negative impact of reduced budgetary allocations to the Uptown Clinic. Before addressing where possible cuts could be made, she must remain cognizant of two important factors; budgetary cuts are likely to extend into the foreseeable future and demand for the clinic’s services are likely to increase. Any cuts must take these two factors into consideration. One of the most important things that Dr. White can do to prepare reduced budgets is to understand why the cuts are required. Is the clinic is financial trouble and unable to meet its payroll, overhead and other monetary obligations? Is there an operating deficit that makes the operation of the clinic unsustainable in its current configuration? Armed with this information Dr. White would be better prepared to determine the type or nature of the reductions to be made. These reductions may come in two forms. Across the board cuts reduce to portion of the budgetary allocation made to made section/department of the clinic.
Targeted cuts on the other hand, seek to identify specific areas where cuts made be required (www.tgci.com) Once the nature of the reductions to be made have been determined, Dr. White can continue to prepare to these reductions by studying the impact these reductions are likely to have to have on the clinic’s ability to maintain the services it provides in its current configuration. For example, the attached excel spreadsheet suggests that, despite staff reductions, it is possible to maintain the current level of services provided by the Community Mental Health Services and Outpatient Mental Health Treatment if the resources and functions of these two departments are effectively combined. Guided by this information, Dr. White could further prepare for a reduction in budgetary allocation by undertaking the difficult task of communicating her projections and potential changes to the staff of the Uptown Clinic. While it is logical to assume that all members of staff will be concerned about the possibility of losing their jobs, Dr. White must seek to prevent a mass, hurried exit by communicating in a frank, honest and empathetic manner (www.tgci.com).
Managerial accounting and cost accounting are different but they are both integral to the managerial and decision making needs of an organization. Managerial Accounting is a tool that drives production and goal-setting decisions of an organization. It does not only analyze and interpret accounting information but it also seeks to objectively evaluate the performance of various sectors or departments of a company as well as those tasked with the management of these departments. It is Management Accounting that determines the direction of an organization as well as the products and services it wishes to provide (mycampus.aiu-online.com). Cost accounting on the other hand, seeks to accumulate and maintain accounting data relevant to a manufacturing environment whether is it a specific process or a specific job within the manufacturing process. It is designed to determine the cost for each unit of product as well as the cost of every individual job. Cost accounting is essential is the establishment of competitive selling prices for the goods and services a company offer (mycampus.aiu-online.com).
Lean production is a management philosophy that was initially pioneered and mastered by the automobile manufacturer Toyota in the 1990’s. This philosophy is now generally accepted as the ideal business model of the 21st century and replaces the mass production philosophy of the previous century. On the website www.1000advices.com Mr. Vadim Kotelnikov, Inventor of inspirational Business e-Coaching states that the lean production philosophy “is about doing more with less: less time, inventory, space, labor, and money. “Lean manufacturing”, a shorthand for a commitment to eliminating waste, simplifying procedures and speeding up production (www.1000advices.com). At its very core, this philosophy employs a systematic approach to the elimination of waste in seven key areas. These areas could be summarized as eliminating overproduction and producing only what customers’ need; eliminating unnecessary delay, down or idle time; streamlining inventory processes to eliminate unnecessary purchasing and storing of raw materials; prevent over-processing by removing any unnecessary steps in processes or procedures; streamlining the motion/movement of people and equipment; eliminating transportation delays and unnecessary material handling and reducing defective products and the cost to repair/replace them (www.1000advices.com).
As is obvious by now, there are clear differences between typical production process and the lean production model. Suited for the mass production strategy of the last century, the manufacturing cycle of the typical production process primarily engages in cost accounting whether periodic or ongoing. The cost accounting data gathered is used the cost of each unit of good or service produced. Lean production goes well beyond cost accounting boundaries to highlight the saving made from the elimination of wasteful activities at every stage in the production process. Perhaps, it is this particular management philosophy that Dr. White must adapt in order to successfully manage the challenges that will inevitably result from reduced budgetary allocations (www.goalsys.com).
References
http://www.1000advices.com/guru/processes_lean_production_vk.html http://www.goalsys.com/books/documents/TOCandLeanPaper-rev.1.pdf https://mycampus.aiu-online.com/courses/ACCT310/u1/hub1/hub.html http://www.tgci.com/magazine/Strategic%20Budget%20Cutting.pdf