Cement industry in bangladesh
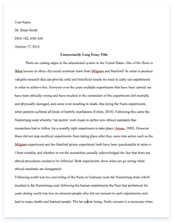
- Pages: 12
- Word count: 2799
- Category: Industry
A limited time offer! Get a custom sample essay written according to your requirements urgent 3h delivery guaranteed
Order NowCement
Cement is a binder, a substance that sets and hardens independently, and can bind other materials together. The word “cement” traces to the Romans, who used the term opus caementicium to describe masonry resembling modern concrete that was made from crushed rock with burnt lime as binder. The volcanic ash and pulverized brick additives that were added to the burnt lime to obtain a hydraulic binder were later referred to as cementum, cimentum, cäment, and cement. Cements used in construction can be characterized as being either hydraulic or non-hydraulic. Hydraulic cements (e.g., Portland cement) harden because of hydration, a chemical reaction between the anhydrous cement powder and water. Thus, they can harden underwater or when constantly exposed to wet weather. The chemical reaction results in hydrates that are not very water-soluble and so are quite durable in water. Non-hydraulic cements do not harden underwater; for example, slaked limes harden by reaction with atmospheric carbon dioxide. The most important uses of cement are as an ingredient in the production of mortar in masonry, and of concrete, a combination of cement and an aggregate to form a strong building material..
Bangladesh cement industry is the 40th largest market in the world. Currently capacity of the industry is about 20 mn tones (MT). Top 13 players are alone controlling over 78% of the total industry capacity. However, the balance capacity still remains quite fragmented. Per capita consumption remains poor when compared with the world average; only 65 kg (FY2009) while our neighboring countries, India and Pakistan, have per capita consumption of 135kg and 130kg respectively. This underlines tremendous scope for growth in the Bangladesh cement industry in the long term. Cement, being a bulk commodity, is a freight intensive industry and transporting it over long distances can prove to be uneconomical. For that reason, industry is regional in nature. It’s also seasonal in nature, during Monsoon industry suffers from low demand. Four major costs are associated with the production of cement as provided:
The pricing of cement of various players in the industry are very close to one another. The factories which would be using captive power (which is cheaper and more reliable than grid power) and backed by uninterrupted clinker supply at competitive price, are likely to be more cost efficient to emerge as the market leader. Currently, the standard price of one bag of cement produced by the multinational cement companies ranges within BDT 370 to BDT 390 per bag. On the other hand, price of one bag of cement produced by the local companies‟ ranges within the price bracket of BDT 340 to BDT 365.
The common technology which is widely used in our industry from the year 2003 is Portland Composite Cement (PCC) which is made following European Standard Methods (ESM). Earlier, Ordinary Portland Cement (OPC) had been used which was made following the American Standard Method (ASM). PCC gives equal strength and durability like OPC. The basic difference between them is in the manufacturing technology. Only 65%-80% of clinker is required to produce PCC while 95% of clinker is required to produce OPC. So, worldwide PCC has become popular which requires less clinker.
Currently, Heidelberg, Holcim and Lafarge are the leaders among multinational cement Manufacturers and Shah and Meghna are the leading domestic manufacturers. Shah cement is the Market leader with close to 14.20% of the market share, followed by Heidelberg with about 9.30% of the market share. During the 2010, many small local manufacturers like Premier, Seven Circle, Crown, Fresh and King cement increased their sales drastically riding on their benefits of economies of scale, backward linkage and aggressive marketing effort.
In Bangladesh, cement consumers are categorized as follows:
1. Individual home makers (25%)
2. Real estate developers (35%)
3. Govt. organizations, i.e., LGED, RHW etc. (40%)
Cement consumption (kg) per capital
Cement consumption has steadily been rising. It is expected that cement
companies will enjoy a good growth of margin over the next 3 years. Because, in next couple of years when large capacities are expected to come on-stream, pass through of input cost will be easier and clinker (main raw material of cement) price is expected to remain stable at $53-$58. Currently, multinational cement companies are facing intensive competition with local companies. Local manufacturers have been pursuing more innovative and aggressive business strategy compared to multinationals. Local manufacturers seek to seize large market by reaching mass people through economies of scale while multinationals cater the needs of specific group of customers by charging high price through superior brand value and quality. In addition, another basic trend in cement industry is smaller companies are shutting down and the bigger companies are becoming bigger. Leading cement manufacturers are now going for expansion. It is expected that if the ongoing expansion plans complete within FY2011, the total production capacity of the industry will rise by 61%. Cement industry expects the consumption to rise by 25% (it will be much higher if Government projects come on stream). Though it seems that the industry will run overcapacity but as mentioned earlier, industry is dependent on only 13 companies‟ production. So it reveals that the cement industry will fall short of supply if the demand increases in line with the big infrastructural projects of Government as expected in future and this symbolizes the huge growth potential of our cement industry.
Considering the „Life cycle of the industry‟, currently cement industry of Bangladesh is in the growth stage. Sales of cement are increasing due to growing demand for cement in both the local and foreign markets. The industry realized about 30% and 21% growth in 2009 and 2010 respectively after suppressed demand from previous years. Industry expected demand growth is 20%-25% for the next three years based on the assumptions below.
1. Government would be able to materialize its important ADP.
2. According to the UN Population Fund (UNFPA) report 2010, 28% people of our country live in urban areas where the population growth is 3.2 per thousand.
Urbanization and demand for accommodation are increasing day by day. Thus it is expected that the real sector will grow steadily with the household users‟ increasing cement consumption pattern.
3. Private sector may get interested to invest in real estate for getting tax advantages of their undisclosed funds
4. Good number of large infrastructure construction projects (Padma Bridge, Flyovers, and highways) is on the pipeline.
5. There is no “Substitute” for Cement. Steel can be used in construction but in limited extent due to its high cost. On the flip side, some caution has to be maintained due to the current demand- supply gap leading to over capacity and falling margins and prices. Also, given the close linkages between them, the effect of a slowdown in real estate growth or hike in interest rates globally or price increase of imported raw materials should also be considered.
ACRONYMS AND ABBREVIATIONS
ASM = American Standard Method
BCMA= Bangladesh Cement Manufacturing Association
CNF = Cost & Freight
ESM = European Standard Methods
OPC = Ordinary Portland Cement
PCC = Portland Composite Cement
UNFPA = UN Population Fund
Cement Industry Overview
Development of cement industry in Bangladesh dates back to the early-fifties but its growth in real sense started only about a decade. The country has been experiencing an upsurge in cement Consumption for the last five years. Government gave permission for establishing cement industries in Bangladesh in FY1995. Initially the cement industry took place without the proper analysis of the demand and supply of cement in the. Within the span of the
two to three years, industry attained expanded capacity of the product with stable growth rate of consumption.
There were mainly four dominant players in the cement industry in the year 1998 that produced their own cement to meet the demand of their customers. These companies were:
Meghna Cement (owned by Bashundhara group)
Eastern Cement (currently known as Seven Horse)
Chatok Cement
Chittagong Cement (taken over by Heidelberg where the local brand is called Ruby)
After a decade, currently 123 companies are listed as cement manufacturers in the country. Among them 63 have actual production capacity while 32 are in operation. The current installed capacity of the industry is 20.0 mn MT. This installed capacity has been calculated under two conditions below:
1. All factories are in operation
2. Production is at its peak season
Though the installed capacity is 20.0 mn MT, currently the actual capacity is about 13.96 mn MT due to supply constraints for power and clinkers.
Overview of cement industry
Industry Demand & Production scenario
Producers and consumer of the industry:
Major producer of the industry:
The largest 13 cement manufacturers hold 78% of the market share. Heidelberg, Holcim and Lafarge are the leaders among multinational cement manufacturers and Shah and Meghna are the leading domestic manufacturers. Shah cement is the market leader with close to 14.20% of the market share, closely followed by Heidelberg with about 9.30% of the market share. During the 2010, manyVsmall local manufacturers like Premier, Seven Circle, Crown, Fresh and King cement increased their sales drastically riding on their benefits of economies of scale, backward linkage and aggressive marketing Effort.
Market share of major cement companies
Current and upcoming capacity of running cement industry of Bangladesh Running industry present capacity probable capacity total capacity
Industry outlook in FY2012 2010 2012
Total installed capacity (mn MT)
Actual capacity (mn MT)
Total Demand (mn MT)
Major consumer of this industry:
In Bangladesh, the main cement consumers are:
1. Individual home makers
2. Real estate developers
3. Govt. organizations, i.e., LGED, RHW etc.
Real estate developers and Govt. projects are the dominant users of cement. During 2007-2008 public sector construction works were slowed down under caretaker government. Unwillingness to disclose the source of income contributed to the downward trend in real estate sector, i.e., building of apartments, flats etc. during that time period.
Major user group of cement
Individuals 25%
Real state developers 35%
Government project 40%
EXPORT OF CEMENT: SIZE OF EXPORT IS 260 K MT/YEAR
Cement industry started export from FY2007. Currently, companies exporting cement to north- Eastern states of India are as below:
Shah Cement
Holcim Bangladesh Limited
Seven Circle
Unique Cement
MI Cement
Confidence Cement
Premier Cement
Aramit
All these companies are exporting in very low quantity to the neighboring countries (India and Myanmar) which are easily accessible through water transportation such as ships and mother vessels. Transportation cost is major concern to export cement. Thus exporting this product to countries which are reachable through connecting water bodies is much more feasible in terms of cost and accessibility. High duty charge is one of the main stumbling-block of cement export. Cement manufacturers in our country produce cement by importing clinker from China and Indonesia (mainly) at a high rate of shipping cost and duties which make the present cost structure impracticable to tap the export potentials for cement. If the government make the duty structure more industry-friendly by exempting some duties on exportable cement and granting cash incentives, cement exporting to SriLanka, Nepal, Bhutan and the Middle Eastern (ME) countries will be feasible in future.
Steady growth margins:
In next couple of years when large capacities are expected to come on-stream, pass through of input cost will be easier. Moreover, clinker (main raw material of cement) price is expected to remain stable at $53-$58. Therefore, it’s been expected that cement companies will enjoy a good growth
of margin over the next 3 years.
Current scenario of the industry:
Dominance by local companies
Currently, multinational cement companies are facing intensive competition with local companies. Lafarge, Cemex, Holcim and Heidelberg are among the top ten cement companies in the world, but together they make up only around 27% of the Bangladesh market. Scancement of Heidelberg Group is the biggest among the foreign companies, but its market share is Around 9.3% despite it has been in Bangladesh for nearly a decade. Holcim’s market share is around 6.4% despite it bought three plants in quick succession more than half a decade back as it planned to emerge as the top player in the country. Lafarge and Cemex, the world’s first and the second largest cement companies have been struggling to survive in the industry. Local companies are grabbing the top slot of the industry by operating in economy of scale and with deft marketing strategy.
For example, Shah Cement, a subsidiary of the country’s biggest conglomerate Abul Khaer Group is now in the top of the industry beating Heidelberg and Holcim by deploying a fleet of trucks in the main growth areas and building the best marketing network in the country. Local companies are investing in backward linkages (captive power plants), have built big plants to reduce cost of production and have a fleet of trucks to carry the products right to the doorsteps of consumers. Quality-wise also, the local companies have made rapid strides. Multinationals bear high overhead costs regarding salary, infrastructure, quality control etc. On the other hand, local companies are more focused to keep the overhead costs low. Multinationals are only concentrating in providing high quality products. But local companies are concentrating in offering quality product with additional benefits like home delivery system, rebate, gifts etc. Local manufacturers have been pursuing more innovative and aggressive business strategy compared to multinationals. Local manufacturers seek to seize large market by reaching mass people through economies of scale while multinationals cater the needs of specific group of customers by charging high price through superior brand value and quality.
Industry Survivors: Large Companies
During last five years almost 32 cement companies have been shut down due to inadequacy of raw materials. Its too difficult to the small manufacturers to survive in the industry due to the shortage of raw materials since small companies face difficulties to arrange the raw materials in competitive price. Currently, the basic trend in cement industry is smaller companies are shutting down and the bigger companies are becoming bigger. Only 10-15 companies are holding 80% of market share.
Future outlook of cement industry of Bangladesh
Considering the „Life cycle of the industry‟, currently cement industry of Bangladesh is in the growth stage. Sales of cement are increasing due to an enormous demand for cement in both the local and foreign markets. The industry realized about 30% and 21% growth in 2009 and 2010 respectively after suppressed demand from previous years.
Industry expected demand growth is 20%-25% for the next three years based on the assumptions below.
1. Government would be able to materialize its important ADP of building big infrastructure projects.
2. According to the UN Population Fund (UNFPA) report 2010, 28% people of our country live in urban areas where the population growth is 3.2 per thousand. Urbanization and demand for accommodation is increasing day by day. Thus it is expected that the real sector will grow steadily with the household users‟ increasing cement consumption pattern.
3. Private sector may get interested to invest in real estate for getting tax advantages of their undeclared funds
4. Good number of large infrastructure construction projects (Padma Bridge, Flyovers, and highways) is on the pipeline.
5. There is no “Substitute” for Cement. Steel can be used in construction but
in limited extent due to its high cost.
On the flip side, some caution has to be maintained due to the current demand- supply gap leading to over capacity and falling margins and prices. Also, given the close linkages between them, the effect of a slowdown in real estate growth or hike in interest rates globally or price increase of imported raw materials should also be considered.
CONCLUDING REMARK
The cement industry is likely to maintain its current growth momentum and continue growing at around 20% to 25% in the medium to long term. Government initiatives in the infrastructure sector and the housing sector are likely to be the main growth drivers. Our cement consumption per year was only 65kg in FY2009 whereas, in India its 135 kg and in Pakistan its 130kg. So there is a lot of opportunity to grow in this industry. If the import duty structure of various cement products, e.g. finished cement, semi-finished cement and basic raw materials for cement (25%, 12% and 7% respectively) continues i.e. import duties is on favor of the local manufacturers and the construction sector remains booming with smooth power supply than nothing to be surprised that cement industry will be the most evolving industry in the next three to five years. The importance of the housing sector in cement demand can be gauged from the fact that it consumes almost 60%-65% of the country’s cement. If housing sector growth wanes, it would impact the growth in consumption of cement, leading to demand supply mismatch.