Case Study: Avion, Inc.
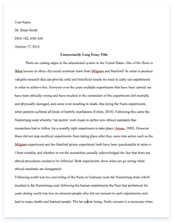
- Pages: 5
- Word count: 1028
- Category: Case Study Customer Management
A limited time offer! Get a custom sample essay written according to your requirements urgent 3h delivery guaranteed
Order Now1. What parts of the supply chain are most closely involved with the situation in this case? What is the responsibility of each part in order to maintain a smooth flow of material? It is no doubt that the ultimate problem rising in the case is miscommunication. Communication is utmost vital for both parties – purchasers and suppliers- to interact effectively, hence, to conduct business smoothly. On the other hand, it is also a lack of competency of Avion, Inc.’s procurement managers as they were unaware of such obvious changes in volume and delivery time required for operation though they deal with the flow of material on a day-to-day basis.
They could not identify the problem, but also did not even bother initiating inquiries with Foster Technology sooner. To maintain a smooth flow of material, every aspects of value chain, including inbound, outbound logistics, operations, marketing and sales, and customer services must be fulfilled. In the case of Avion, Inc., the volume of goods shipped and its delivery lead time are far beyond the actual ability and capacity that Foster Technology could handle. The inbound logistics was hence affected, slowing down operations and outbound logistics, causing frustrated customers.
2. What initially appears to be the problem? What really is the problem(s) in this case? Delayed shipment initially appears to be the problem causing the whole mess of the supply chain. Avion, Inc’s procurement managers quickly blamed it on their supplier. However, the root of the problem is from the inconsistence from the buyer in terms of initial and actual ordering. Follow up is the unresponsiveness of the buyer regardless of multiple attempts were made by the suppliers regarding the rising problem.
3. How easy is it to switch suppliers? What could complicate a firm’s ability to switch to a new supplier? It is easy to switch suppliers; however, it would take a lot of time, money, and effort. Also, Avion, Inc. had already had pending projects with Foster Technology; hence, immediate supplier termination could complicate the whole system, causing incomplete deals.
4. What does it mean to get to the root cause of a problem?
To get the root cause of a problem is to investigate thoroughly or to dig the problem deeply to find out the utmost causation of the problem so that it can be resolved accordingly. It is crucial to figure out the root cause of problem, whether it is a part/ a function/ a party or whatever that could not fulfill its responsibility and why that happens in first place. The right way to do is to trace back to every single layer of the problem, constantly wonder “Why?” to filter the surface to discover the hidden root cause of problem.
5. What does it mean to be a good customer? Why does a buying firm want to be perceived by a supplier as a good customer? Provide specific examples of what a firm must do to be a good supply chain customer. A good customer is the one who maintains good manner, is trustworthy, and has a good relationship with the supplier. A buying firm wants to be perceived by a supplier as a good customer so that the supplier would be dedicated to complete his tasks excellently, provide high quality of materials, be willing to share his technology, or even offer favors like exclusivities or discounts. All terms, agreements and guidelines between two parties should be spelt out explicitly to avoid unwanted occurrences. For example, Avion, Inc. should not alter its supplier right after the problem arose without searching for root cause of the problem.
6. Explain the role of performance measurement in managing supply chain activities. Performance measurement is truly important in managing supply chain activities to ensure a non-disruptive growth of the company. It provides the metrics to monitor the progress, to assess the effectiveness and efficiency of the on running process, to evaluate how well the firms handle its business in terms of speed, inventories, sales, customer satisfaction, etc. Weaknesses would be easily spotted and fixed quickly when arise.
7. Why can changes within a supply chain disrupt the normal flow of goods and services within a supply chain? Changes within a supply chain can disrupt the normal flow of goods and services within a supply chain. Nowadays firms are interdependent, creating a dynamic supply chain. If one failed to perform its task, other components in value chain would also get affected. Anything from miscommunication, political instability, “acts of God”, technical problems, terrorism, just to name a few, can jeopardize the continuity of supply chain.
8. Why might Avion want to reduce the lead times on its purchased materials and components? Avion might want to reduce the lead times on its purchased materials and components so it will have more time for production, so as to fulfill more orders from the customers in a shorter time manner. This leads to a more efficient supply chain helping the company to gain competitive advantage so it can enjoy more profit down the road.
9. Why do firms single source contracts?
There are several reasons why firms single source contracts. It might be the required materials in need are so unique that firms cannot find anywhere else. It could also due to the special relationships between buyers and suppliers. Or it could be the premium price or quality being offered by the suppliers that it rules out other competitors.
10. Develop an action plan for Avion that addresses the issues presented in this case. Be prepared to explain fully your recommendations. Avion, Inc. should adhere to initial project regarding volume and delivery time. If it wants to either increase volume or decrease the lead time, it should consider the maximum ability and capacity Foster Technology could handle. Avion’s procurement managers are liable for being well aware of quantity of shipping goods and well coordinate with materials management team. If there is any arising change, the production team needs to inform both above departments to address the issue appropriately. In this case, the performance measurement is needed to monitor and evaluate the process timely.