Wireless Control for Industrial Instruments
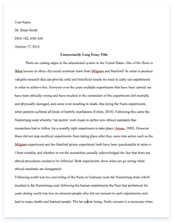
- Pages: 8
- Word count: 1876
- Category: Control Technology
A limited time offer! Get a custom sample essay written according to your requirements urgent 3h delivery guaranteed
Order NowJigar Daki Dhaivat Vasoya J.M.Rathod A.B.Bambhaniya EL Student EL Student AP, EL Department AP, ET Department B.V.M. engineering college B.V.M. engineering college B.V.M. engineering college B.V.M. engineering college V.V. nagar, India V.V. nagar, India V.V. nagar, India. V.V. nagar, India [email protected] [email protected] [email protected] [email protected],in
Abstract-It is a microcontroller based wireless equipment controller that can switch on or switch off devices at a desire time interval set by the user in transmitter. This system is a combination of software and hardware. We have used AT89C51 microcontroller kit for interfacing our system. This paper is about controlling various AC devices using remote control which is working on Radio frequency. Let us take example if we can connect the bulb at the output then we can switch on or off of bulb at a desire time interval using the remote. Status of various devices is displayed on LCD. In this paper we are using RF transmission because with the help of IR transmitter there is a problem of directivity and range of working, that problem is eliminated with RF transmission. RF has better directivity and frequency range.
Index Terms: Microcontroller, LCD, Reception, Transmission, Wireless.
1. INTRODUCTION
Block diagram of wireless control system is given as below.[pic] Figure 1.Block mittam of Transmitter
The device can be control from a distance of up to 30 meters from the transmitter. In the transmitter an LCD module is used to show the device number and preset control time for the device (00 to 99 seconds) .Concepts of wireless RF communication and automation with AT89C51 microcontroller are used here. Our operating range of frequency is at UHF band. It is about 434 MHz.
A. Transmitter
Above figure shows Transmitter and Receiver section. Four pushbutton switches (s1 through s4) are used as inputs to select the devices and set the time-out in the transmitter section.
These are designated as up, down, enter , run , keys respectively. The time-out data is transferred over the RF wireless link to the receiver section.
The 8 bit AT89C51 MICROCONTROLLER is the main controlling part of the transmitter section.[1].It is connected to the LCD module , input switches and encoder IC (HT12E) .The device control program is stored in the memory of the microcontroller to control the devices as per the time-out settings done through input switches s1 through s4.
A two line, 16 character LCD module shows the status of the main program that is running inside the microcontroller.
The HT12E is an 18 pin DIP package encoder IC that encodes 4 bit data and sends it to TRX-434 RF transmitter module.[2].
The TRX-434 RF transmitter module uses a digital modulation technique called amplitude – shift keying (ASK) or on-off keying. in this technique, whenever logic ‘1’ is to be sent , it is modulated with carrier signal (434 MHz). This modulated signal is then transmitted through the antenna. The waveform in figure depict the ASK concept [3].
B. Receiver
[pic]
Figure 2. Block Diagram of Receiver
The 12V DC supply , used along with a 5V regulator , can be provided by a 12V battery or power adaptor. The RX-434 radio receiver module receives the ASK signal from RX-434.The HT12D decoder demodulates the received address and data Bits. IC CD4519 is a quadruple two-input multiplexer that selects the appropriate data bits to control the devices.
The ULN 2003 relay driver seven NPN darlington pairs that feature high-voltage outputs with common-cathode clamp diode for switching the inductive loads. The collector-current rating of a single darlington pair is 500mA.
TABLE Ι. RF MODULE SPECIFICATION
|PARAMETER |VALUE | |Frequency of operation |434 MHz | |Modulation |ASK | |Range |5V (Rx) | |Power supply |3V TO 12 V (TRX) |
2. CIRCUIT DESCRIPTION OF TRANSMITTER
Figure 3. here shows the circuit diagram of Transmitter circuit. The Microcontroller reads the input data from switches S1 through S4 at its port 2 pins 21 to 24 and displays it on LCD. Port 3 provides read data to Encoder IC HT12E at pins 10 through 13. The Microcontroller is programmed to control input and output data.
The AT89C51 is a low-power, high-performance CMOS 8-bit microcomputer with 4Kbytes of Flash programmable and erasable read only memory (PEROM). The deviceis manufactured using Atmel’s high-density nonvolatile memory technology and is compatible with the industry-standard MCS-51 instruction set and pin out.[1].
[pic]
Figure 3.Circuit Diagram of Transmitter
The on-chip Flash allows the program memory to be reprogrammed in-system or by a conventional nonvolatile memory programmer. By combining a versatile 8-bit CPU with Flash on a monolithic chip, the Atmel AT89C51 is a powerful microcomputer which provides a highly-flexible and cost-effective solution to many embedded control applications.
When the input switches S1 through S4 are open, Logic 0 is constantly fed to the respective port pins of microcontroller. When any one of the switch is pressed, Logic 1 is fed to the respective port pins of the Microcontroller.
The device control program stored in the memory of Microcontroller activates and executes as per the function defined in the program for respective input switches.
Data inputs AD8 through AD11 (pins 10 through 13) of HT12E are connected to the microcontroller. Pins 1 to 8(A0 to A7) of the IC are address inputs. Shorting the address pins using switches to either VCC or GND enables different address selection for data transmission. Here we have connected to 5V. Since address pins are connected to 5V the address is set to 255d (in decimal). If you were to connect all the address would be 000d . Thus there are 256 possible address available. So you can set up switches to control one or more of the encoder address pins.
Pin 14 is a transmit-enabled (TE) input pin. The encoder will send data only when pin 14 is connected to ground. Whenever a button is pressed, logic 0 is sent to this pin through the microcontroller, thus activating it and enabling transmission.
Pin 17 is the data-out (D-out) pin that sends a serial stream of pulses containing the address and data. It is connected to the data input pin of the TRX RF module.
3. CIRCUIT DESCRIPTION OF RECEIVER
[pic]
Figure 4.Circuit Diagram of Receiver
The time-out control is set using input keys S1 through S4 to turn on/off the devices at predetermined time. The default time for all the devices is’00’ seconds. So using ‘up’ key you can increment time by one second, and using ‘down’ key you can decrement time by 0ne second down. At the same time, the LCD module shows the current status of increments and decrements.
When the time out for a device is set, press ENTER key so that the program controls the transfer to the next device for time out settings. In the same way, the remaining three time out settings must be done before pressing RUN key. When RUN key is pressed, it executes the device control program subroutine in the Microcontroller and the program automatically collects the time out information entered by the user and sends the processed data to the Encoder IC HT12E. the encoder IC sends the data to Din(pin 2) of the RF transmitter module. The data is transmitted by the TRX 434 module to the receiver section through the antenna.
Figure 4. shows the receiver circuit. The RF receiver (RX-434) module can receive the signal transmitted by the transmitter from a distance up-to 1 to 1.5km.. The range can be increased up to 30 meters using a good antenna.
Dout pin of RX-434 RF Module is connected to Din pin of Decoder IC HT12D (IC 4). Din pin of IC4 receiver address and data bits serially from the RF Module. Decoder IC4 separate data and address from the received information. It accepts data only if the received address matches with address assigned to Encoder IC1 (HT12E). we have used ‘1111’ as the permanent address for communication. Pins 1 through 8 of IC4 are address pins and therefore 256 possible address are available. The address on the Encoder and Decoder ICs must match for the data to be valid.
The HT12D decoder receives serial address and data from the Encoder continuously with its local addresses. If no error or unmatched codes are found, the input data codes are decoded and transferred to the output pins. VT pin (valid transmission) goes high to indicate a valid transmission. The HT12D provides four latch type data pins whose data remains unchanged until new data is received.
Data pins D8 through D11(pins 10 through 13) of the decoder send 4 bit data to CD4519 multiplexer. The latched output data from multiplexer CD4519 is fed to Relay Driver IC ULN2003, to control upto 4 devices through relays. VT pin is connected to LED4 through IC6 to indicate the status of device.
4. WORKING FUNCTION
[pic]
Figure 5.Working model of Transmitter
[pic]
Figure 6.Working model of Receiver
When the system is switch on ,the startup message “press any key” appears on the LCD screen , when key is pressed by the user ,the LCD displays the message” to set time out press enter”, pressing enter key display the following message on the LCD with a cursor blinking near the 1st device “D1_T”:
D1_T=D2_T=
D3_T=D4_T=
Use up and down key to set the time for the controlling device. set time for each device on a LCD screen look like this.
D1_T=10D2_T=20
D3_T=30D4_T=40
Now press enter key followed by run key. a device control subroutine execute and send the data to the RF module, which transmit the data through antenna.
You can set maximum of 90 second as the control time for the device. If u set it to 00 a particular device is turned on for infinite time.S
CONCLUSION
The system is a small, simple, cost effective and good for wireless control of equipment. Using the radio frequency we can on or off devices .We can control home appliances and various industrial instrumentation. If we use infrared, then infrared signal cannot pass through wall. So if we want to control our device outside the wall cannot do it, the only way is that to use some RF remote control .The circuit (transmitter and receiver) use few component and ordinary .it’s easy to build because we don’t have to tune coil or variable capacitor.
ACKNOWLEDGEMENT
The Authors would like to thanks Dr F S Umrigar,Principal and Prof U S Depopurlar,H.O.D. Electronics Department of Birla Vishvakarma Mahavidyalaya Engineering Collage for their support.
REFERENCE
[1]. Muhammad A Mazidi , Janice Mazidi , Rolim
Mc Kinaly , The 8051
[2]. George Kennedy , Electronics Communication ,
Tata Mc Graw Hill
[3]. Bernard Skalar, pabitra Kumar Ray, Digital
Communication, Second Edition, Pearson
Education.
[4]. G.K. Dubey, S.R. Doradla, A.Joshi, R.M.K.
Sinha, Power Electronics, New Age.
[5]. Digital and analog communication by B.P. Lathi
.Zhi Ding(international 4th Edition), OXFORD
university press.
[6] www.efy.mag.com