Stirling Cycle Refrigerator
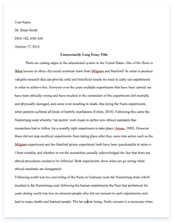
- Pages: 13
- Word count: 3216
- Category: Chemistry
A limited time offer! Get a custom sample essay written according to your requirements urgent 3h delivery guaranteed
Order NowThermodynamic cycle can be divided into two that are power cycle and refrigeration cycle. The cycle that produce net amount of works is called power cycle. The power cycle that can remain it working fluid in gaseous phase is called gas power cycle. There are many types of cycle in gas power cycle such as Otto cycle, Diesel cycle, Bryton cycle, Stirling cycle and Ericson cycle. The Otto cycle is known as ideal cycle for spark-ignition cycle while the Diesel cycle is known as compression-ignition internal combustion engine. The Bryton cycle is known as ideal cycle for the modern-gas turbine engineand can be categorize as one of the gas power cycle. The Bryton cycle itself has four internal reversible processes. The next cycle is Stirling cycle. This Stirling cycle involves an isothermal heat-addition process and isothermal heat-rejection process. .
In reversed of heat engine, it has refrigeration system. Refrigeration system is the transfer system for heat from low temperature region to higher temperature region. The device that produces refrigeration is called refrigerator, heat pump and air-conditioning. The cycle they operate is called refrigeration cycle. The refrigerator and heat pump operate on the same cycle but different with their objective. The objective of refrigerator is to maintain the refrigerated space at low temperature. Discharging this heat to a higher-temperature medium is merely a necessary part of the operation. But the objective of heat pump is to maintain heated space at high temperature by absorbing the heat from a low temperature source and then supplying that heat to high temperature medium such as house.
The refrigeration cycle can be divided into two that is vapor compression refrigeration cycle and gas refrigeration cycle. In vapor compression refrigeration cycle, the refrigerant is vaporized and condensed alternately. This cycle is the modified of the Rankine cycle operating in reverse. It also can be the Reversed Carnot Cycle operates on the reversed direc tion. For the gas refrigeration cycle, the refrigerants remain in the gaseous phase throughout the entire cycle. The Reversed Stirling Cycle and the Reversed Bryton Cycle can be categorized in this gas refrigeration system. The Reversed Stirling Cycle is the cycle of Stirling refrigerator operated.
1.2Stirling Cycle Refrigerator
Stirling Cycle Refrigerator is one of the machine that operating on the Stirling cycle machine. In Stirling cycle, it has two popular cycles that are Stirling cycle engine and Stirling cycle refrigerator. The operation of the Stirling cycle involves an isothermal heat-addition process and isothermal heat -rejection process. It different from the carnot process. The two isentropic processes are replaced by two constant -volume regeneration process. In the Stirling cycle machine, it has five components that are working gas, heat-exchangers, displacer mechanism, regenerator, and expansion/compression mechanism. The working gas is trapped within the system. Stirling cycle has heat-exchangers that are heat absorbing heat-exchanger and heat rejecting heat-exchanger. Heat absorbing heat-exchange is used to transfer heat from outside system to the working gas, while heat rejecting heat-exchanger is used to transfer the heat from the working gas to the outside system. Displacer mechanism is used to move the working gas between the hot and cold end of the machine.
The function of regenerator is as a thermal barrier between the hot and cold ends of the machine. Regenerator also can be a ‘thermal store’ for the cycle. The function of expansion/compression mechanism is to expands or/and compress the working fluid and it also can produce net work output that is used to move the heat from low to high temperature region.
Many advantages of Stirling cycle engine and Stirling cycle refrigerator. Stirling cycle engine has a constant high efficiency, low noise compare with other internal combustion product and can theoretically be a very efficient engine to convert heat to mechanical work at carnot efficiency. Stirling cycle refrigerator can be used over a wide temperature range, good efficiency for a large capacity, compactness and long life time. The working gas in the Stirling cycle refrigerator can be air, helium or hydrogen. This working gas has no ozone depletion potential and zero global warming potential. It is different for domestic refrigerator that using CFCs and HCFCs that can cause global warming and ozone depletion. The Stirling cycle refrigerator also can cool-down the food below 30˚C for the long time.
Stirling cycle refrigerator usually use a piston-cylinder, in either α or β configuration. A α-configuration machine uses two pistons which displace and expand/compress the gas at the same time. A β-configuration machine has a separate displacer-piston and expansion/compression piston (usually called a power-piston).In β-configuration, the first process is expansion under an isothermal condition. At this stage, low-pressure working gas was expands isothermally at cold end temperature and absorb heat from the cold space. Second process is isochoric displacement. The displacer-piston transfers all the working fluid through the regenerator to the hot end of the machine. Heat is delivered to the gas when it passes through the regenerator and makes the temperature of the gas raised at the hot space. When the temperature rises, gas pressure was increased significantly.
The third process is isothermal compression. The power piston doing work and compresses the gas at hot end temperature. After that, it rejects the heat to the hot space. The last process is isochoric displacement. The displacer piston transfers all the working gas isochorically through the regenerator to the cold and of the machine. Heat is absorbed from the gas as it passes through the regenerator, thus lowering the temperature of the gas at cold space. When the temperature reduces, the gas pressure was drop and the system returns o it initial conditions.
There are two types of Stirling cycle refrigerator that is V-type integral Stirling refrigerator (VISR) and the split type-displacer Stirling refrigerator (STFSR). The different between these two types is it driving mechanism of the displacer. The displacer for the V-type integral Stirling refrigerator is directly driven by a motor through a crank-shaft mechanism. For the split type-displacer Stirling refrigerator, the displacer is driven by the fluid force or gas pressure which is produce indirectly by the piston motion and the stroke and it also depends on the operating conditions. Many analyses have been done on the V-type integral Stirling refrigerator. They have been investigated about the power consumptions and the coefficient of performance. But not so much analysis has been done for the split type free-displacer Stirling refrigerator.
Many researches have studied about the Stirling cycle refrigerator with regard of their application and have found that are many factor affect the performance of the Stirling cycle refrigerator.
1.3Objective
• To study a mathematical model of V-type Stirling cycle for refrigeration system. • To get a conceptual design of V-type Stirling cycle for refrigeration syste
1.4Scope
This research is accompanied with scopes to ensure the project will achieve the objective and not exceed within its intended boundary. There are few scopes that have to be followed. The scopes that have been set are;
• Study about Stirling cycle
• Identify the general concept of thermodynamic cycle for the Stirling cycle refrigerator. • Make literature review on Stirling cycle for refrigerator. • Solve mathematical model for Stirling cycle refrigerator using ideal gas law equation and ordinary differential equation (ODE) • Simulate the mathematical model for Stirling cycle refrigerator. • Propose the conceptual design of Stirling cycle refrigerator.
LITERITURE REVIEW
2.1Introduction
The original stirling cycle engine was invented, developed and patented in 1816 by the Scottish minister Dr. Robert Stirling with help from his brother that is engineer. The engine that was build by him was so heavy and complicated. The engine is build for use in hot-air engine as alternative to the steam engine. After that, many investigations have been made on stirling cycle. In 1834, John Herschel was suggested that this stirling engine could be used as a refrigerator and after that Alexander Kirk was constructed the
first stirling cycle refrigerator in 1864.
From that moment, many developments have been made on stirling cooler. Today, stirling cooler are used in many application. The evolution in stirling cooler design also was grow up until today.
2.2Thermodynamic Analysis
In thermodynamic analysis, the first things that need to understand is how this V-type Stirling cycle refrigerator operates. In general, the V-type Stirling cycle refrigerator has 4 thermodynamic processes as shown in Figure 3.2 and Figure 3.3.
Process 1-2: Compression Process
Work is expended to compress the gas while it is mainly in the compression volume.
Process 2-3: Cooling Process
The gas is moved from the compression volume to the expansion volume. On its way the gas is cooled so that it has a temperature near that to the cooler when it arrives in the expansion volume. This cooling takes place at constant volume and causes the pressure to decrease.
Process 3-4: Expansion Process
The cooled gas is expanded in the expansion volume. The expansion causes a further decrease in temperature. Less work, than was needed for compression, can be extracted from the expansion because the pressure is lower.
Process 4-1: Heating Process
The cold gas is moved back from the expansion volume to the compression volume. On its way the gas is heated so that it has a temperature near that to the heater when it arrives in the compression volume. The heating occurs at constant volume and causes the pressure to increase. The cycle can now be repeated by beginning with the process 1-2.
2.3Type of Application for Stirling Cycle Refrigerator
Today, many application have been made on Stirling cycle refrigerator including • Heat shock test device
• Freezing drier
• Thermal property test device
• Blood/cell storage-devices
• Cold cooler
• Household use as a freezer and refrigerator
• As solar-powered Stirling cycle refrigerator
The study in theory and experiment of the stirling cycle refrigerator has been discuss by many researcher. Variety of methodology has been used to study this stirling refrigerator. A study in theory is needed to make the simulation of it real situation when this stirling refrigerator operates. It also needs some mathematical module. Meanwhile, the study that been made by experiment need an understanding on the procedure of the experiment to get the perfect result. Because of that, literature review must be made to more understand the study of stirling refrigerator in theory and experiment. For this literature review, four journals have been selected. Two of the journals are for V-type Stirling cycle refrigerator. Another two journals are for power-piston Stirling cycle refrigerator The V-type Stirling cycle refrigerator use α-configuration that has two pistons which displace and expand or compress the gas at the same time. The power-piston Stirling cycle refrigerator use β-configuration that has a separate displacer-piston and expansion or compression piston.
2.2Literiture Review on V-Type Stirling Cycle Refrigerator
Sun Le’an, Zhoa Yuanyang, Li Liansang and Shu Pengchang (2008) have been discussing about the performance of a prototype Stirling domestic refrigerator. They was investigated the thermal performance of the V-type Stirling cycle refrigerator. The working fluid that was used on this prototype is helium and nitrogen. The temperature range that was used is over -20 to -60 ˚C. They make this study to optimal the design and operation of the V-type Stirling cycle refrigerator when it is applied to the domestic refrigeration system. In this prototype, the cold head is installed between the expansion port and the regenerator and the electric heater covers the cold head. The compression and expansion pistons are driven by a crank-shaft mechanism functioning with a fixed phase between compression and expansion processes. They have done the experiment test on the prototype of V-type Stirling cycle refrigerator. They used helium and nitrogen as a working gas. In this experiment, they use three kinds of configuration (Table 1).
The charged pressure for the helium and nitrogen is from 0.25 Mpa to 1.4 Mpa and the rotational speed frequency was 10-40 Hz. They also have done the theoretical analysis and computer simulation on the thermodynamic process. The result from the simulation was compare with the result from the experiment test. From their experiment, the cooling capacity is much greater for helium than nitrogen because of it specific heat capacity is larger than nitrogen and the flow resistance of helium is much smaller than nitrogen. The pressure loss for nitrogen is larger than the helium. Other result is the cooling capacity increases with rotational speed and COP has a maximum when using helium as a working fluid. But it different for nitrogen, the cooling capacity and COP have an optimum. The optimum rotational speed for COP is from 500-700 rpm for nitrogen and 800-1000 for helium.
They have make conclusion that each component must be matched each other to get the required specifications and to obtain optimal configuration for V-type Stirling cycle refrigerator component. They also choose the helium as a working fluid because the helium is better than nitrogen. Another conclusion is the optimum rotational speed for the cooling capacity is different between nitrogen and helium. The COP has a peak value around 900 rpm for helium and 600 rpm for nitrogen.
|Configurations |1 |2 |3 | |Regenerator length (mm) |80 |60 |50 | |Regenerator diameter (mm) |55 |50 |40 |
Table 1: The specifications for three configurations of the regenerator
Ö. Ercan Ataer and H. Karabulut (2004) have discussed about thermodynamic analysis of the V-type Stirling cycle refrigerator. They have divided the V-type Stirling cycle refrigerator into 14 fixed volumes that is expansion and compression spaces, cooler, heater and regenerator. Each control volume in the V-type refrigerator is an open system subjected to a periodic mass flow. The conservation of mass and energy equation are written for each control volume of the refrigerator. A computer program is written in FORTRAN, and the equations are solved iteratively. They have calculated the COP and work done of V-type Stirling cycle refrigerator in numerical analysis. They also calculate the mass, temperature and density of the working fluid for each control volumes. A simplified iterative numerical method is developed to solve the equations of the V-type Stirling cycle refrigerator. In this study, they were used air as the working fluid. They also used the different charge pressures in this thermodynamic analysis of V-type Stirling cycle refrigerator. The charge pressure that was used is taken between 2 and 5 bar.
From their result, the amount of work done and cooling rate of the machine are 3.05 and 4.37 J per cycle. Other result is the COP is decrease when the charge pressure increases. This happens due to increase in cyclic work. The wall temperature of expansion space also decreases with charge pressure. They have made conclusion that the charge pressure higher than 2 bar will decrease the COP of the Stirling cycle refrigerator and the second conclusion is increased in the heat transfer areas and the heat transfer coefficients causes increase in the COP of the machine.
2.3Literature Review on Power Piston Stirling Cycle Refrigerator
Emre Oguz and Fatih Ozkadi have done the experimental investigation on a Stirling cycle cooled domestic refrigerator. They choose a prototype of a free piston Stirling cooler from private company to integrate into domestic refrigerator cabinet. They use thermosyphon system as a heat transfer mechanism. The prototype was tested with different charge quantities of refrigerant. They used R134a as the refrigerant in the thermosyphon system. The experiment also used different input voltage for the cooler. Helium had been chosen as the working gas in the free piston Stirling cooler. The frequency that they used for this experiment is 1Hz. A fan was placed in the cabinet to increase the convective heat transfer coefficient. The ambient temperature is 25 ± 0.5°C for all tests. During the specified steady-state intervals, the temperatures inside the cabinet are well within ± 0.3°C for 240 minute tests and ± 0.7°C for the tests that last longer than 1000 minutes. They have recoded the temperature of cold side thermosyphon, the temperatures of the shelves for the cabinet and the input power of the Stirling cooler during prototype is being tested. They also calculated the evaporator outlet, condenser outlet and inlet, and Stirling cooler for warm and cold head temperatures.
The result from that experiment is the cold head, evaporation and average cabinet temperatures decreases as the input voltage of the Stirling cooler increased. Other result is COP was increase as the cold head temperature increases at constant warm head and drive voltage condition. There also has three parameters that can give effect to refrigeration capacity and thermal performance that is cold head temperature, the warm head temperature and input voltage. But input voltage does not give any effect to the COP. The conclusion that they make from this experiment is the COP value can be higher than 2.5 at the certain operating conditions depending on the cold and warm head temperatures. Other conclusion is free piston Stirling coolers can be integrated into domestic refrigerator cabinets in several ways including the thermosyphon system and the forced air convection heat transfer mechanism. This method also can be preferred for both cold and warm sides of the cooler because there are no additional components consuming energy in the thermosyphon system. But more theoretical and experimental research is needed on thermosyphon systems to estimate the heat transfer and pressure drop.
Bancha Kongtragool and Somchai Wongwises (2005) have made a thermodynamic analysis of a Stirling engine including dead volume of hot space, cold space and regerator. Although this analysis was done on stirling engine, but the concept and the theory from this analysis can be used in Stirling cycle cooler to find the dead volume. The objective of this study to analysis an imperfect regeneration Stirling engine with dead volume based on the classical thermodynamics. They have developed an isothermal model for an imperfect regeneration Stirling engine. That engine also includes dead volume of hot space, cold space and regenerator. They also make numerical simulation on regenerator effectiveness and dead volumes. The effects from the simulation have being studied. The result from that study is the mass of the working fluid only depend on dead volume.
It increases with increasing of dead volume. The compression work, expansion work and engine network decrease with increasing dead volume. It means that a large dead volume requires a small amount of compression work and gives a small amount of expansion work. An engine with large dead volume also will produce only a small amount of engine network. For a perfect regenerator, the external heat input and output is not required and the total heat input decreases with increasing dead volume. An imperfect regenerator requires external heat input. However, the total heat input is like to increase with increasing of dead volume. The total heat input also increase with decreasing regenerator effectiveness. The conclusion that they make for this analysis is the Stirling engine with a given dead volume, an inefficient regenerator will not affect the engine network if the regenerator effective temperature is an arithmetic mean of the heater and the cooler temperature. But, an engine with an inefficient regenerator needs more heat input and better cooling than an efficient one.
Figure 3.3: temperature-entropy diagram
Figure 3.2: Pressure-volume diagram