Project on ” Arvind mill” ( the product mix and its strategy)
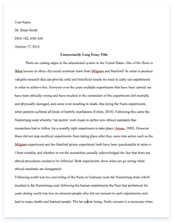
- Pages: 19
- Word count: 4691
- Category: Strategy
A limited time offer! Get a custom sample essay written according to your requirements urgent 3h delivery guaranteed
Order NowPROJECT ON âARVIND MILL (THE PRODUCT MIX AND ITS STRATEGY)â Master of Commerce
Semester-I
(2013-2014)
Submitted
In Partial Fulfillment of the requirements
For the award of degree of
M.Com-I
By
Suraj Shridhar Tripathi
Seat No: _______
Tolani College of Commerce
Sher-e-Punjab society,
Andheri (East),
Mumbai-400 093
PROJECT ON âARVIND MILL (THE PRODUCT MIX AND ITS STRATEGY)â Master of Commerce
Semester-I
(2013-2014)
Submitted
In Partial Fulfillment of the requirements
For the award of degree of
M.Com-I
By
Suraj Shridhar Tripathi
Seat No: _______
Tolani College of Commerce
Sher-e-Punjab society,
Andheri (East),
Mumbai-400 093
CERTIFICATE
This is to certify that Suraj Shridhar Tripathi of M.Com Semester I (2013-2014) has successfully completed the project on âArvind Mill (The Product Mix and Its strategy)â under the guidance of .
Project Guide: ____________________________
Course Coordinator: ____________________________
External Examiner: ____________________________
Principal: ____________________________
DECLARATION
I, Suraj Shridhar Tripathi, the student of M.Com Semester-I (2013-2014) hereby declare that I have completed the project on âArvind Mill (The Product Mix and Its strategy)â
The information submitted is true and original to the best of my knowledge. References have been cited wherever necessary.
Date: ___________
Place: Mumbai
Signature of Student
Suraj Tripathi
ACKNOWLEDGEMENT
Preparing the project on âArvind Mill (The Product Mix and Its strategy)âhas given me extensive practical knowledge related to the course. I would like to first thank our principal Dr.A.A.Rashid, for his valuable support in preparing this project. I express my deep sense of Gratitude to the Course Coordinator, Ms.Sadhana Venkatesh for the valuable guidance and support during my project work. I am thankful to my guide Dr. Vasudev Iyer for providing me the guidance throughout the course of this project. I am also thankful to her for patiently and critically evaluating the content of this project. I would like to take this opportunity to express my gratitude to all the staff of the library and the computer lab for their support.
Index:
SR NO
TOPIC
PAGE NO
1
INTRODUCTION
7
2
Various processes / departments of Arvind Mills
11
Methodology
34
7
PRODUCT MIX
8
STRATEGY
9
Findings & Facts and figures
19
conclusion
20
REFRENCES
35
AGRICULTURE PROTECTION IN RICH COUNTRIES,
IMPLICATION FOR DEVELOPING COUNTRIES
by Suraj Shridhar Tripathi
Introduction About the company
Arvind Limited started with a share capital of Rs 2,525,000 ($55,000) in the year 1931. With the aim of manufacturing the high-end superfine fabrics Arvind invested in very sophisticated technology. With 52,560 ring spindles, 2552 doubling spindles and 1122 looms it was one of the few companies in those days to start along with spinning and weaving facilities in addition to full-fledged facilities for dyeing, bleaching, finishing and mercerizing. The sales in the year 1934, three years after establishment were Rs 45.76 lakh and profits were Rs 2.82 lakh. In the mid 1980âs the textile industry faced another major crisis. With the power loom churning out vast quantities of inexpensive fabric, many large composite mills lost their markets, and were on the verge of closure. Yet that period saw Arvind at its highest level of profitability. At this point of time Arvindâs management coined a new word for it new strategy â Renovision. It simply meant a new way of looking at issues, of seeing more than the obvious and that became the corporate philosophy. The national focus paved way for international focus and Arvindâs markets shifted from domestic to global, a market that expected and accepted only quality goods. Cottons were the largest growing segments. But where conventional wisdom pointed to popular priced segments, Renovision pointed to high quality premium niches.
Thus in 1987-88 Arvind entered the export market for two sections -Denim for leisure & fashion wear and high quality fabric for cotton shirting and trousers. By 1991 Arvind reached 1600 million meters of Denim per year and it was the third largest producer of Denim in the world. In 1997 Arvind set up a state-of-the-art shirting, gabardine and knits facility, the largest of its kind in India, at Santej. With Arvindâs concern for environment a most modern effluent treatment facility with zero effluent discharge capability was also established. Year 2005 was a watershed year for textiles. With the muliti-fiber agreement getting phased out and the disbanding of quotas, international textile trade was poised for a quantum leap.
In the domestic market too, the rationalizing of the cenvat chain and the growth of the organized retail industry was likely to make textiles and apparel see an explosive growth. Arvind has carved out an aggressive strategy to verticalize its current operations by setting up world-scale garmenting facilities and offering a one-stop shop service, by offering garment packages to its international and domestic customers. Of Lee, Wrangler, Arrow and Tommy Hilfiger and its own domestic brands of Flying Machine, Newport, Excalibur and Ruf & Tuf, is setting its vision of becoming the largest apparel brands company in India.
JOURNEY
1931
Arvind Limited is set up by three brothers Kasturbhai, Narottambhai and Chimanbhai Lalbhai with a share capital of Rs 2,525,000 (US$55,000) backed by state-of-the-art technology, with the aim to produce high-end superfine fabric. 1934
With sales reaching Rs 45.76 Lakhs, and a profit of almost Rs 3 Lakhs, Arvind establishes itself amongst the foremost textile units in the country. 1986
– An uninterrupted record of not missing out on paying dividend to its shareholders. – An established leader in fine & superfine cotton fabrics for Indian market. 1986
Renovision: First company to bring globally accepted fabrics Denim, yarn dyed shirting fabrics & wrinkle free gaberdines to India. 1987
– The largest zero discharge green effluent treatment plant in India. – Commitment to greener world 1987
– First company to bring International shirt brand âArrowâ to India – First Company to start dedicated âretailâ outlets for Arrow brand. – Awarded various awards for highest exports and ISOÂ 1989
– Largest denim & shirting in South Asia.
– 3rd largest denim capacity in the world
1997
First Indian company to verticalise the cotton textile business from cotton fields to apparel retailing. 1997-1998
First company to introduce ERP SAP business solutions
2008
Company launches ‘Megamart’, now India’s largest value apparel-retail chain Largest portfolio of International brands: Lee, Wrangler, Nautica, Jansport, Kipling, Tommy, Arrow, US Polo, Izod, Pierre Cardin, Palm Beach, Cherokee, hart Schaffner Marx Lifestyle Fabrics
The Fabric of a Global Society
In a world without boundaries, Arvind fabrics are equally universal in their appeal. Arvind aims to enrich lifestyles globally, inspiring diverse customers with the beauty of their fabric. Denim
There are many delightful features of Arvind denim: An annual capacity of 110 million meters; the position of 3rd largest producer of denim in the world; and an export network of 70 countries worldwide. Prominent products in this category include ring denim, indigo voiles, organic denim, bi-stretch denim and fair trade certified denim. This is apart from regular light, medium and heavy weight denims. They come in various shades of indigo, sulphur, yarn-dyeds, in 100% cotton and various blends. The facilities of Arvind Denim are accredited with ISO 9001, ISO 14001, OEKOTEX 100, GOTS, Organic exchange standard, FLO for fair trade and Lycra Assured. As one of the largest denim producers in the world, Arvind caters to quality markets of Europe, US, West Asia, the Far East and the Asia Pacific. Shirting
It is one of the most well-known products of Arvind Group, selling at a premium in the international market. It has an astonishing annual capacity of 34 million meters. Prominent products within this category include fabrics with non-iron properties, mechanical finishes, printed fabrics apart from the cotton and cotton blends in Linen, Lycra, Polyester, Modal, Silk etc. with varieties in yarn dyeds and solids. Further, Arvind has a unique plant for manufacturing very light weight indigo dyed fabrics in yarn dyed and solids for top weights. Arvind Shirting has a liquid ammonia based fabric processing plant and a state-of-the-art print house â a first for India and one of the few in Asia. Backed by the latest technology and state-of-the-art equipment, every stage of the production process, right
from spinning of the yarn to final processing and testing of the fabric, ensures that stringent quality standards are met and products remain eco-friendly. Khaki
The many virtues of Arvind Khaki merit your undivided attention: An annual capacity of 21 million meters which facilitates the launch of two new collections annually; and the distinction of being the only khakis division in South East Asia to do so. The division provides the finest fabrics in the variants of 100% Cotton, Cotton Rich Polyester Blend, Cotton Lycra, Cotton Tencel, Cotton Linen, etc to name a few. The division has an integrated plant with weaving and processing facilities. The most prominent products in this range include Chinos, Canvas, Ribstop, HBT, Tussore, Cavalry, Structures and Dobbies. Knits
Arvindâs knits department has an annual knitting capacity of 10,000 tons. Apart from the basic knitting capabilities (jersey, pique, rib, and interlock), Arvind has mastered specialty knitting techniques such as yarn-dyed autostripers, jacquards, and stretch fabric. The knits vertical has a fabric dyeing capacity of 6500 tons per annum and yarn dyeing capacity of 3500 tons per annum. It has the ability to process both tubular and open-width fabric and offer specialty finishes like mercerization, singing and various forms of brushing and peaching. The department also boasts of a state-of- the art print shop equipped with fully automatic placement printing capabilities. Voiles
Arvind is the uncontested market-leader in the manufacture of voiles, with a production capacity of 33 million meters per annum. Arvindâs voiles are primarily used as blouse material and are sold in the domestic market through an impressive network of 150 dealers, reaching over 5000 retail outlets throughout India. High quality Swiss voiles are exported to Switzerland, Sri Lanka and countries in the Middle East.
VARIOUS PROCESSES / DEPARTMENTS OF ARVIND MILLS
a. Spinning department
The first step in the manufacturing of all kinds of fabric i.e. spinning of
bales of raw cotton into yarns of various kinds suited for producing varieties of fabric. Trivia about Arvind Mills:
âVoileâ fabric is mainly used for knitting purposes and for making saris too, but is mostly exported to the middle east In addition to collaborations with multinational apparel giants, Arvind Mills runs its own brands of clothing e.g. Excalibur, Flying Machine, Ellites et al Cotton is procured from a host of countries including far-flung ones like Egypt, America and Germany Recently, Arvind Mills has come up with its unique product, Ready To Stitch (RTS) kits Cost of fabric accounts for ~65% of the cost of raw material 850 million m2 of denim fabric is manufactured every month at facilities at Naroda, entirely dedicated for this purpose Towards this end, 4500 tonnes of yarn is spun every month, an exercise that contributes 450 crores towards costing only for denim.
There are primarily two kinds of technologies that are in popular usage vis-a-vis spinning of yarn namely open end technology, also called roter spinning owing to its being the key component in the machines involved, and ring spinning technology. The facility at Naroda works entirely on open end technology and produces ~60 tonnes of yarn a day with 5472 roters being around on campus. At other manufacturing facilities of AM, ring technology is used, which generally results in production of 70 tonnes of yarn a day. Rest of the yarn required for fabric production The cotton spinning can be done using any of the four technologies: 1. Ring spinning
2. Open end spinning
3. Drap spinning
4. Air-jet spinning
The open end technology of spinning requires cotton to be processed in mainly 4 broad stages as enumerated below: Blowing: In this stage physical, in situ and ex situ impurities are gotten rid of raw cotton Carding: Cotton, thus purified, is put into cylinders in sliver form Drawing: Parallelization of fiber takes place
Roter spinning: The main process of drawing cotton fiber into yarn is carried out b. Weaving department The weaving department has 203 weaving machines en Toto, of the make ZAX and 209i, the latter being an older version. The machines are of the company TSUDAKOMA, a Japanese concern as opposed to the spinning department where the machines were of German companies. The ZAX machines work at 750 rpm whereas 209i model machines work at 650 rpm.
Together they churn out a lac m2 of cloth a day. In total the department has 159 ZAX machines and 44 209i. There happen to be 261 labourers working in 4 shifts in the department with 20 staff members i.e. 5 in each shift, out of whom there is one supervisor for each shift. A beam card keeps all the records of what is being put on the machine and under whom it is supervised. Inputs used for the weaving departments can vary from:
1. OE- open end
2. ER- even ring
3. UR- uneven ring
Lycra is used to increase the elasticity of the fiber. Filament is used in the fiber which is exported to countries where the level of sweating is lower as compared to Indian condition where majorly cotton is used for the same reason. The weaving department has the distinction of being the largest at Arvind Mills and exports close to 95% of its manufactured fabric. Discussing the denim fabric, the core competence of AM, original denim is composed of 100% cotton but with a view to bring in variations to the material in consonance with the emerging trends in the market, various natural fibers like linen and synthetic fibers like filament, lycra, polyester are added to cotton. While weaving such mixed fabric, the core is made of the addend and original cotton is wound around it. Yarn woven vertically is called warp while that woven laterally is termed as weft. For weaving purposes a cotton count ranging from 5 to 20 is generally used. c. Dyeing department.
Arvind Mills has a grill section that was loaded with 12 beams of yarn, though latest machinery could support even 16 of them. They are also known as warping beams and their design depends upon the texture and construction of fabric e.g. weight, length etc. Each beam consist of 350-400 ends and 12 such beams are joined together to form one at last with 4000-4800 ends which is used in the weaving process. Four types of dyeing processes are used in
Arvind mills namely: 1. Indigo dyeing
2. SBIT-sulphur bottoming indigo topping
3. IBST-indigo bottoming sulphur topping
4. Sulphur dyeing
All the above processes differ in the process of loading on the fabric. The dyeing process in a flow chart is explained below. (Ref. fig 1.1 ) Pre-wetting PWA
|
W.B.1 (W.B.-Washing box)
|
Dye box (6 shades are used)
|
W.B.2
|
Sulphur
|
W.B.3
|
Pre dryer
|
Saw box (Sizing)
|
Post dryer
|
Compromising (speed is increased)
|
H/S
d. Finishing department
The department churns out 300000 meters of finished denim cloth a day. What happens to the fabric that has come off loom is called surface finishing that entails softening of fabric, thus making it fit to wear. Further, de sizing is done in order to reduce tension in the knit yarn, to ensure that it doesnât break out of undue tension.
To accomplish the process, there are three basic mechanisms involved namely desized finishing, desized mercerized finishing and desized mercerized tint finishing. In yesteryears, there existed a demand for long lasting colors in denim apparel, which is no longer present. Consumers are becoming more inclined towards denim that loses color in a few washes. For such emerging needs and choices, double dyeing concept has been adopted that renders denim fabric various effects after subsequent washes. The process is as follows
1. Singeing is done and the hairiness of the fabric is burned by flames. 2. Desizing removes the sizer put on by the suker muller in the dyeing department to increase the strength of the fabric (a mixture of desizing agent, alcozyme and acetic acid is used for the same). 3. Mercerizing is the process of caustic wash and the unit studies is GPL (gram per liter). 4. Stunter is used to settle the width shrinkage and to adjust the elasticity by killing the elastic properties of lycra in the fabric which is to the tune of 30 to 40% earlier and can be dropped down to 3 to 8% as per customer requirement. Finishing techniques used in Arvind mills are:
1. Glaze finishing
2. Padding
3. Curing
4. Montfort finishing
5. Foam finishing
In addition there is an intervening singeing and washing process that brings in more softness in the fabric. The product is washed off water soluble chemical remnants, steam dried and then causted that lead to swelling of the material. Earlier foam technology was used for this purpose, which has now been replaced by wet technology that gives more softness and binding to fabric. This is the followed by moving the fabric through centering machines that kill extra percentage of inbuilt Lycra to peg elasticity at the desired level as demanded by the customers. Temporizing is the next process to be carried out with the help of rubber and leads to permanent shrinkage of the fabric. e. Quality Assurance department
Traditional view:
Traditionally quality assurance was looked as if a post-mortem report where in the yarn and the fabric was checked for the quality and standards as per required by the customer. a proper policing was kept on what has been done and what is to be done Modern view:
In the modern day quality assurance has a wider scope and it includes activities like process ownership and calliberation where in the department ownership is given to a person and it becomes his/her duty to deal with it in the most efficient manner. Quality assurance at Arvind mills has the following labs. : 1. Cotton laboratory
2. Physical testing laboratory
3. Chemical testing laboratory
4. Callibaration laboratory
5. Colour quest laboratory
6. Clearance department
COTTON LABORTARY:
Cotton is held for the 70% cost of the fabric cost only and hence becomes a major factor which if controlled will add maximum contribution to the strength of avind mills. The coefficient of variance is calculated for the width, diameter and hairiness of the fibre. The machine used for this purpose is USTER TESTER 5.the fibre is passed at a speed of 400m/min and the variance is hence calculated. The variance is calculated against international or the preset arvind standards The length, weight and the exact count of the fibre is also calculated and the CASCADE machine is used for this purpose which ensured the right thing at the right time as per customer demands. PHYSICAL TESTING LABORTARY:
This testing happens at the yarn manufacturing stage and the yarn is tested for its 1. Length
2. Elongation
3. Elasticity etc
The yarn should be tested in a way so as to know whether the yarn can take all the loadings or not and if yes to what extent can it take. This helps in
deciding what processes the yarn can face and what effects cab be deduced. Single yarn strength and its elongations is measured using the USTER TENSORPAID 3 machine which is the most trusted name in the field and comes from Switzerland. INSTRON 4465 is used to check the tensile strength of the fibre and the tear strength is also calculated in grams. For all the above written testingâs the standard lab conditions are made at a temperature of 60+/- 2 f and the humidity level is maintained at 65%+/-2% Factors like stretchabliltyskew and shrinkage are tested after marking is done followed by three washings of the fabric; the fabric is tonned to the environment after keeping it in the standard environment. CHEMICAL TESTING LABORTARY:
In the chemical laboratory they check all the fuels, dyes, and all the chemicals that are used in the production process. They even check the denim if it is washed with bleach how much it fades the colour. They try different process like how the denim would react in different conditions like in case of perspiration, salt water, normal water, in extreme temperature. COLOUR QUEST LABORTARY:
In the colour quest they try to find out the different shades and they see to it that after the washing and drying process does the shade match the requirement of the customer or not. CALIBRATION LABORATORY:
Definition:
Calibration is a specialized measurement process where in one compares test and measuring instruments/equipments of unknown status to well defined standards of greater accuracy in order to detect /eliminate error by adjustments & report any variation in accuracy capability.
CALIBRATION ACTIVITY
Calibration through in âhouse facility
93%
Calibration throughout-side agencies
7%
CALIBRATION FACILITY AT CALIBRATION LABORATORY
PARAMETERS
INSTRUMENT & FUNCTIONS
Temperature
Mercury thermometer, temperature indicator & controllers, temperature switches, temperature gauges, temperature transmitters.
Pressure
Pressure gauge, vacuum gauge, pressure transmitter, pressure switch.
Mass
Analytical weighing balance
Electrical
AC/OC voltage, AC/DC current, single phase power, frequency, resistance capacitance, conductance, logic pulses, logic levels.
Digital & analogue amateur, multimeters, panel meters, frequency meters.
Dimensional
Measure tape, steel scale, verniar capture, micro meter, dial gauge.
Gas lab instruments
Lab instruments used for quality conformance tests & physical testing lab & chemical testing lab.
f. DTNG Department
In Arvind mill manufactures 8.5 million of denim per month. Out of which 60% is exported and remaining is manufactured for the domestic market. There are around 34 companies who are the manufactures of the denim product in the market. The USP of arvind mill is that it believes in innovation and constantly keeps on innovating new products. It innovates around 1700 new product material every year which is equivalent to 5 new product materials every day. Arvind mill manufactures around 1600 denim fabric out of which 1300 includes different shades of blue colour. New designs are created on the basis of the following parameters:-
1) Customer based development: Product is developed on the basis of customer requirements. Sometimes the customer asks for the exact imitation of the product (on the basis of texture, strength, durability, etc) at a cheaper rate. In order to target the exact customers and fulfil demands Arvind mills has its marketing team worldwide including Europe who keeps on meeting the customers from time to time in order to get their feedback and review for the required product.
2) Design collection: Arvind mills also displays its designed products at fashion shows held at various public functions to promote it brand awareness as well as show the distinct variety of product it manufactures. The process of creating a designing concept and further executing it takes around 18 months. One of the products of arvind mills âAuto meterâ was proposed for making in January 2009; the production process started in April 2009 and was launched in the market in the year 2010.
3) Trouble shooting: with the new technologies good quality of the same material at a cheaper rate can be manufactured. Due to huge demand of its denim product in the market Arvind mills department of weaving spinning and finishing outsources not less than 1000 tonnes of yarn per year.
g. Inspection Department
After the processing of the denim in the finishing department it is sent to the inspection department where certain parameters are checked n then inspected in the inspection machine. The parameters that are checked before inspecting in the machines are 1. Feel of the denim
2. Look of the denim
3. Weight of the denim
4. Shrinkage
5. Skewing
6. Elasticity of the denim
The operator checks for the damages, spots, knots in the denim .there are certain signs that are used for the damages like if he finds out any knot he puts a dot on that place Dispatching is done according to the customer requirements. For dispatching the denim bale is packed. There is special packing machine of LEVY & SMITH .After the role is inspected it is passed on to conveyer belt where a bar code sticker is placed with certain details like yards of denim, meters, pieces, 4 point ,quality number , style , bale number , particular number is given to each bale. After that it is passed through 150 degree Celsius so the total air is vacuumed from the bale. Then it is sent to the sorting department where the bales are sorted out as per the requirement and style by the sticker that was placed on the bale. h. ISO & EMS Department
ISO 9001-2001-2008
ISO is a system certificate and not a product certificate .It tells us about how the procedure and systems are in place or not. It says if your system is on place then your product will be good automatically. After you apply for ISO certification first thing that takes place is pre-assessment auditing standards they find out the discrepancy or non-conformity. After all the discrepancies are removed there is certification audit. There is 100% audit of all the departments and report is send to the committee and they give the certificate according to details in report for auditing. ISO has appointed different companies to do that.
The certificate is given for 3 years and for every 6 months surveillance audit is done. They check around 30 -40% of the departments and during the period of 3 years again 100% auditing is done of all the departments. During the surveillance audit they will take sample size and would do the auditing. After 3 years you can apply for re-certification and whole procedure takes place again. Then there is another certification that is EMS (environment management system) .it looks after whether the surrounding atmosphere is safe for the other people or not. It looks after certain parameters like noise pollution, air, water, land pollution for that certain standards are followed and are taken care of. there is and ETP which is EFFLUENT TREATING PLANT which treats water ,chemical and dyes to bring down to certain PH level which is then sent to drainage that water is not harmful after the treatment . The sludge that remains after the treatment of water is dumped to a certain land that is certified by the government for disposal of such harmful wastes. There are other types of certifications are
ISO -14000-2004 is followed which looks after the resources utilization or depletion of resources. ISO-18000 OSHOâS its occupational standards for health and safety where every measure for safety of the staff is taken into consideration. i. Marketing Department
As Arvind mill is one of the leading company in textile industry they provide their fabric to domestic as well as international market also. They have different teams which handle marketing activity in different region. Arvind mill produce 8 million meter fabric every month. Out of which 60% is exported and the rest is manufactured for the domestic market. For, promotion of their products in domestic & international market they organize fashion shows. They have different designer for U.s, Europe, and domestic market. They introduce their new collection twice every year (summer spring and autumn winter) known as American line collection for the American market and Europe line collection for the European market. Apart from that the also hold exhibition and seminars for the concerned buyers. j. Human Resource Department
In strategic business unit the retention rate of the employee is low as the plant is 80 years old. When a new employee joins the plants the excitement level of the employee is quite high but within time it declines. At Arvind mills an attempt is being undertaken to decrease the number of employees especially those who do not have the required employment skills. The employee strength is over 2500 across all the units.
METHODOLOGY
Primary data
1. Data provided from the company on this program, if already some work is in place. 2. Meetings with the distributors to identify the discrepancies and areas of concern which can then be made the focal point of the loyalty program 3. Interviews with the functional heads to provide assistance and guidance to help understand the intent of this program and what are the factors which the company can offer to them 4. Firm may help to set up meetings with other company functional heads to get industry data Secondary data
1. Online websites can be used to gather data on similar loyalty programs of other firms. 2. Standard structures and formats can be attained from the intranets and internet forums.