Production of sulphur dioxide
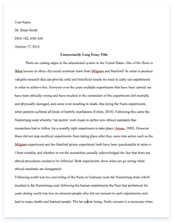
- Pages: 7
- Word count: 1614
- Category: Chemistry College Example
A limited time offer! Get a custom sample essay written according to your requirements urgent 3h delivery guaranteed
Order NowIntroduction
Currently, fertilizers used on the West Coast are made and then transported from other parts of New Zealand. Because fertilizers have a reasonably large mass the cost of this transport can be expensive. This report will investigate the processes involved in making superphosphate fertilizer, including the manufacture of sulfuric acid from sulfur using the contact process. Also in this report will be an outline of the positive and negative effects that using this particular fertilizer has on the environment, as well as any possible effects that the manufacturing process will have on the environment.
Making sulphuric acid
Sulphuric acid is the main component in the process of making superphosphate fertilizer and in terms of mass is the most abundantly produced chemical in the world. Sulphuric acid is made from sulfur using the contact process as mentioned earlier. When making superphosphate fertilizer, the sulphuric acid needed will be made on site. There are three steps to make sulphuric acid. Below I will explain the three steps involved in the process of making sulphuric acid.
Step 1
Production of sulfur dioxide
The elemental sulfur is purchased on the international market after being recovered as a by-product of the oil refining process. It is then melted in a brick-lined tank at temperatures of up to 140°C and all the impurities such as ion and organic compounds are filtered off.
Lime(ph5.8-6), chemically known as calcium oxide is added to the melted sulfur to reduce its acidity to a more neutral PH level. Doing this also reduces its corrosiveness.
Then this sulfur is pumped to the burner where it is burnt in hot oxygen in a reaction which creates sulfur dioxide gas at 8-9%v/v (SO2). this gas exiting the burner is very hot at temperatures up to 830°C due to the fact that the ∆H (change in enthalpy) is negative therefore it is an exothermic reaction so it releases energy. Then it is passed through a hot gas filter to remove any residue ash particle.
S + O2 → SO2 ∆H = -300 kJ mol-1
Step 2
Conversion to sulfur trioxide
Sulfur dioxide (SO2) is then converted to sulfur trioxide (SO2) in a reaction with oxygen, using vanadium pentoxide (V2O5) as a catalyst to speed it up. This reaction occurs in a four-stage reaction vessel called a converter. Each stage has a solid catalyst bed which the gas will pass through. The bed consists of the catalyst and potassium sulfate spread over a silica base to produce a porous support which will increase the surface area greatly. Have a larger surface area increases the reaction rate because there is more surface for the reaction to occur on. It is deduced that the catalyst used ( V2O5) increases the rate of the overall chemical reaction by oxidizing the SO2 to SO3 and then re-oxidizing itself using the oxygen present in the gas stream.
The equilibrium constant in this reaction decreases with increasing temperature. This means that as the temperature increases, the reaction slows down. Therefore the reaction is temperature dependent. If the temperature becomes too low the equilibrium point will not be reached. If it is too high the conversion rate will become very slow. The ideal gas temperature is 400°C-500°C, if maintained in this range it will result in a high reaction and also a high conversion equilibrium.
Like the first step in making sulfur trioxide, this reaction is exothermic. As the reaction occurs, heat is generated in each of the stages and across each of the catalyst beds. The heat produced must be removed at each stage to maintain the optimum reaction temperature within the following stage. In the diagram below you can see how much the temperature increase during each stage(stage represented by a no.1 bed, no.2 bed etc). During stage 1 the temperature increases 200°C. Stage 2 there is an increase of about 50°C and stages 3 & 4 is a very small increase no more than 20°C.
Above: a diagram showing the percentage of conversion of SO2 to SO3 gas that would be reached at an SO2 concentration of 8% v/v and a range of temperatures. (source-http://nzic.org.nz/ChemProcesses/production/1B.pdf )
The greatest degree of cooling is required between stage 1 and stage 2.
SO2 + 1/2O2 → SO3 ∆H = -100 kJ mol-1
Step 3
The absorption of SO3 to form sulfuric acid
Sulfur trioxide(SO3) reacts with water(H2O) to produce sulfuric acid. Although on paper this reaction seems simple, in reality, it is far more complicated. The reaction of sulfur trioxide with water is highly exothermic and produces an acid rain which is difficult to condense into sulfuric acid and can be a potential environmental risk. That is why in an industry this reaction is done in a discrete way. The sulfur trioxide is absorbed in a countercurrent flow of 98-99% sulfuric acid in the absorption tower to produce a chemical called oleum(H2S2O7). Then water is carefully added to the oleum to remake concentrated (98%) sulfuric acid. During this whole stage, it is vital that the sulfuric acid is maintained at about 98% concentration. At any lower concentrations, the water vapor pressure increases sharply and the resultant acid mist is not readily re-absorbed and may escape into the atmosphere. The plant will operate under an air discharge permit which controls emissions of sulfur dioxide and total acidity. Traditionally mild steel has been used as the main material of construction for process equipment containing 98% sulfuric acid. The corrosion rate is adequately low, except at the air/liquid interface where atmospheric moisture encourages corrosion. The trend is now towards more sophisticated materials including Teflon lined steel pipework which will reduce iron contamination of the sulfuric acid but will be more expensive.
Above: Vapour pressure and percent of sulfuric acid (http://nzic.org.nz/ChemProcesses/production/1B.pdf ) as you can see it is vital for the concentration to remain around 98% as this results in the lowest amount of vapor pressure.
H2SO4 (l) + SO3(g) → H2S2O7(l)
H2S2O7(l) + H2O(l) → 2 H2SO4(l)
Overall reaction: SO3+ H2O → H2SO4 ∆H = -200 kJ mol-1
Above: is a process flow diagram of a sulphuric acid plant (it is a bit hard to see) (http://nzic.org.nz/ChemProcesses/production/1B.pdf )
Making Superphosphate:
Once the sulphuric acid has been produced in sufficient amounts(excess product can be sold or used to produce other products) you can then begin to start producing the superphosphate fertilizer. The basic reaction in the manufacture of superphosphate is the reaction of sulfuric acid with insoluble phosphate rock which forms the soluble calcium dihydrogen phosphate (Ca(H2PO4)2. As described in the following equation:
PO4 (3-) + H2SO4 → H2PO4 – + SO4 (2-)
The phosphate rock can be sourced from many places including Jordan, Nauru, Israel, Morocco, and the USA. These sources are mainly fluorapatite (Ca3(PO4)3F) and constitute about 70-85% Calcium phosphate (Ca3(PO4) in terms of weight. Although these figures can vary depending on the source.
The reactions that occur during the production of superphosphate are complex but can be summarised to give the following:
1. Ca5(PO4)3F + 5H2SO4 → 5CaSO4 + 3H3PO4 + HF
2. Ca5(PO4)3F + 7H3PO4 + 5H2O → 5Ca(H2PO4)2 . H2O + HF
And combined, these reactions give the following equation:
2Ca5(PO4)3F + 7H2SO4 + 3H2O → 7CaSO4 + 3Ca(H2PO4)2 + H2O + 2HF
There also some other reactions that are occurring at the same time, such as the silica minerals associated with the fluorapatite reacting with virtually all the HF to form silicon tetrafluoride. However, as a gas, it is recovered as a hydrofluosilicic acid in the scrubbing system.
Step 1:
Phosphate rock is ground up
Phosphate rock that has been mixed in a blending plant to produce a product with a total phosphate concentration of 15% is ground up to produce a mixture in which at least 75% is less than 75 microns in diameter. Then the composition is analyzed and altered until the desired proportions of minerals are present. This powdered rock is stored in a large hopper.
Step 2:
Manufacture of superphosphate
The phosphate rock, sulphuric acid, and water are mixed together in a horizontal mixer with the approximate feed rates:
• Water – 6 tonnes/hour
• Phosphate rock – 25 tonnes/hour
• 98% Sulfuric acid – 14.5 tonnes/hour
A constant flow of this sloppy mix is dropped out of the mixer into the Broadfield den which is the room with a slow-moving floor (30cm/min). This enables the setting of the “cake” and its reciprocating sides to prevent the drying mixture adhering to the walls. The superphosphate “cake mixture” is then cut out of the den using a rotating cutter wheel after approximately a 30 minute retention time.
The superphosphate is then worked further in the conditioner which consists of a set of rotating paddles to knead and break up the product. Additives may also be added at this time such as potassium chloride, limestone, and ammonium sulfate. Water is also often added to improve the product’s consistency in preparation for granulation.
Step 3:
Granulation
The granulation stage is important if you want to produce a superphosphate product with the required physical properties. The granulation process is a circuit consisting of a pulverizer, granulation drum, and classifier. The purpose of the pulverizer is to break up any lumps in the product before it is fed into the granulation drum. The granulation drum rolls the superphosphate to form granules then the granules are passed out one end of the drum through a classifier which is a wire screen. Granules that are too large(>6mm) to fit through the classifier are recycled back through the circuit while the finished product is transported via conveyor belt to the storage area.
The superphosphate will cure in the store for up to 2 weeks before it is dispatched.
Effects On The Environment
The most significant potential environmental hazard is dust (from the grinding of phosphate rock) and gaseous hydrofluosilicic acid (from the reaction between hydrofluoric acid and silica or quartz) emissions. These, however, are both carefully monitored, also a dust catcher and gas scrubber are used.
Conclusion
Bibliography:
http://www.tropicalpermaculture.com/what-is-fertilizer.html
http://feeco.com/wp-content/uploads/2017/04/NPK-Fertilizer-Infographic.pdf
https://www.lovethegarden.com/community/fun-facts/how-does-fertilizer-work
http://www.gcsescience.com/aa15.htm
http://nzic.org.nz/ChemProcesses/production/1B.pdf -most used source