Power Plant Optimization through New Processes and Technologies
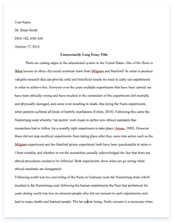
- Pages: 5
- Word count: 1123
- Category: Energy Plantation Power
A limited time offer! Get a custom sample essay written according to your requirements urgent 3h delivery guaranteed
Order NowOverview
India’s growing economy and the expansion of its manufacturing industry contribute to the country’s increasing dependence on energy. Currently, total installed generation capacity is over 200 GW, and is going to be over This Insight gives an overview of the present energy demand and supply gap in India. The highlight is on strategies for effective energy management, utility management system, and tools to optimize power plant performance.
400 GW by 2022. The country imports coal, oil, and gas to meet the needs of its expanding electric power industry and other process industries. To sustain its economic growth, India needs to expand its capacity to manufacture cement, metals, and other commodities. Typically, these industries
are energy intensive, which further increases the energy demand. Therefore, the country and its industrial companies are focusing on energy management and energy conservation. ARC Advisory Group’s tenth India forum in Hyderabad in July focused on Transforming Industry through New Processes and Technologies for process and batch industries. At the forum, suppliers discussed optimization of plant operations through various strategies, such as energy management and renovation and modernization of process and power plants. Manish Kumar Singh, Engineering and Consulting Group, Siemens, discussed energy management issues along with the company’s end user client Sanjay Mantri, Associate Director, Dr. Reddy’s Lab, who presented a case study on a Utility Management System (UMS). Debashish Patra, Additional General Manager, Steag Energy Services, India, recommended tools that can help power plants optimize performance.
Energy Management Challenges
Manish Kumar Singh, Engineering and Consulting Group, Siemens, said that energy is a vital cost component as it typically constitutes over 30 percent of total production cost. In India, there is a dire need to bridge the prevalent demand and supply gap. Conventional sources of energy (coal) are in short supply, making the country import-dependent, which impacts pricing. Singh said that energy requirements differ from plant to plant: steam and power; chilled brine; chilled water; and compressed air. It is also very important to look at the effluents that are generated at the time of production. Presenting his thoughts on implementing energy management he said it should start by creating transparency, and end by optimizing operations.
Utility Management System
Sanjay Mantri, Associate Director – Automation Systems, Dr. Reddy’s Lab, presented a case study on the utility management system installed in Dr. Reddy’s Lab, and explained how the company optimizes energy in three ways. First, it reviews the currently available equipment; second, it looks at the fuel-energy cost at the time of benchmarking; and third, it reduces fuelenergy costs and looks for alternatives. Many other utilities in an organization consume significant energy and optimization can be achieved if it channels all the energy in one single level. To achieve this, companies need to centralize monitoring, minimize human intervention, employ stringent quality management, benchmark the system, and implement safety measures.
Mantri said that UMS is a single window automation system for centralized monitoring or control of utility equipment to improve its performance by utilizing real-time data, status, and alarms. UMS benefits are made visible as all the utility equipment such as pumps and cooling towers are started or stopped from the central SCADA system. Systems are provided in the utility office for displaying graphics of the real-time status of all connected utility equipment; data are logged at a frequency of one minute; and realtime historical data are stored in the system for comparison and analysis. UMS provides economical and operational benefits.
These include improved product quality; reduced production downtime; a single window system; enabling quick measurement of electrical and other critical parameters and optimization of process control enhanced maintenance management; enabling predictive planned load sharing; load shedding and demand management; and energy accounting for benchmarking and realtime efficiency. However, according to Mantri, implementing UMS also presented some challenges. These include retrofitting electrical equipment; the need to shut down equipment and thus make it unavailable for manufacturing; focusing on short term gain; selecting the right team of functional experts who understand the cultural nuances; and the need for full-time involvement of the project execution team.
Advanced Software Tools for Optimization of Power Plant Performance Debashish Patra, Steag, presented on advanced software tools for optimizing power plant performance. His presentation focused on solutions implemented for NTPC, India’s largest power company, and renovation of old and upcoming power plants in India. He recommended some advanced tools to optimize the performance of power plants. Patra discussed about offline and online tools available for optimizing the performance of power plants. “Ebsilon,” an offline tool, helps model both new and old power plants by topology and design calculations. Ebsilon also helps users map and analyze the performance of existing and upcoming power plants, and plan renovations.
This tool helps map different types of thermal power plants: fossil, nuclear, combined heat and power, etc. It also helps map cycles, such as refrigeration cycles and desalination processes. Further, Patra discussed the company’s online tool, Performance, Analysis, Diagnostics, and Optimization (PADO), which Steag has successfully installed at NTPC and BHEL power plants in India. PADO helps power plants by improving the quality of measurements; validating data; and evaluating boilers, turbines, condensers, and other components. It also helps optimize unit operation (sootblowing, setpoints) and calculate “whatif” scenarios, and such others. He discussed the various PADO modules as shown in the graphic below.
PADO Modules
PADO modules involve five types of sub modules: Base modules: data visualizer, data validation, and Ebsilon model Fault detections: statistical process control and fault tree Optimization: sootblowing optimizer, and boiler setpoint optimizer Physical conditions: lifetime monitoring and metal temperature Performance analysis: performance monitoring and what-if analysis Patra spoke about the company’s other two software systems for plant optimization. These include a simulator for operator training to enhance skills and a computer-based maintenance management system (CMMS) to improve maintenance and operational activities.
Recommendations
Economic development has increased India’s energy consumption. India’s economic development depends on the manufacturing industries, most of which require technology upgrading and ready availability of cost-effective and environment-friendly energy sources. Based on ARC research and analysis, we recommend the following actions for owner-operators: • • • • • Benchmark energy consumption Work to both increase energy generation and reduce energy consumption Explore available technology-based solutions for monitoring and managing energy consumption Establish key performance indicators (KPIs) for energy Renovate existing plants, and introduce optimization systems for upcoming projects as a standard to achieve energy efficiency For further information or to provide feedback on this Insight, please contact your account manager or the authors at [email protected] or [email protected]. ARC Insights are published and copyrighted by ARC Advisory Group. The information is proprietary to ARC and no part may be reproduced without prior permission from ARC.