Parts Emporium
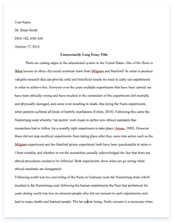
- Pages: 4
- Word count: 785
- Category: Accounting Customer
A limited time offer! Get a custom sample essay written according to your requirements urgent 3h delivery guaranteed
Order NowIntroduction: Sue McCaskey, the new materials manager of a wholesale distributor of auto parts is facing a lot of problems with the inventory. The inventory is misplaced, its individual records for products are not properly compiled, the customer service is insufficient, and there is loss of potential sale. Summary and data of inventory statistics (inventory turns) are not available. Sue has to figure out how to cut down on the bloated inventories, along with improving the inadequate customer service. She decides to begin with sample of two products to investigate the main reason of the problems- the EG151 exhaust gasket and the DBO32 drive belt. Analysis: Parts Emporium is facing various issues due to its inventory problems. These problem may effect the company in both long-term and short-term as these problem may demand a lot of time to be rectified.
Their first problem is the customer service department, which places orders on the backorder which are not filled from stock right away which makes the company to loose 10% of demands to its competitors. The second and the most major problem is the requirement and need of the Parts Emporium for a new inventory management system. When the inventory and customer service data was from the warehouse was requested by McCaskey, she was unable to get those data. This leads to situation where the company is unable to track where the money is being lost and how to resolve the situation as their current system is not effective and efficient. Conclusion: According to my analysis and calculation the way how company should manage its inventory of two items is given in the Appendix-A. The recommendations of these two items has led to reduction in total cost by 26% in case of EG151 exhaust gas kit and 55% in case of DB032 drive belt as shown in the Appendix -A
APPENDIX A
(1) EG151 Exhaust Gasket
a. The New Plan:
Firstly we calculate the weekly demand average by taking the estimates of the
annual demand and the variability. Weekly demands are for the first 21 weeks of the current year, we assume that there are 52 weeks per year:
Demand Average (Weekly): 2142/21= 102 gaskets per week
Annual Demand : 102(52)= 5304 gaskets
Holding cost: $1.85 per gasket (per year)
Ordering cost: $20 per order
EOQ=
= 339 Gaskets
Now we use the G151 data to calculate the standard deviation of demand.
Standard Deviation in weekly demand= 2.86 gaskets
Standard Deviation in demand during the lead time= 2.86√2= 4.04
R= average demand during lead time + safety stock
= 2(102) + 1.65(4.04)= 210.66 (rounded off as 211 gaskets)
b. Cost Comparison:
Cost Category
Current Plan
Proposed Plan
Difference
Ordering cost
5304 / 150 x 120 = $707
5304 / 150 x 0.68 x 12.99 = $313
+$394
Holding cost
1.85(150 / 2)= $139
339 x 1.85 / 2= $314
-$175
Total
$846
$627
+$217
The total cost has reduced by 26% per year. the safety stock is higher with the proposed plan, as compared to the current plan. The safety stock level cannot be determined in the current system. The extra cost of the safety stock is minimal with the proposed plan, being $1.87(7) = $12.95. Lost sales will be less with the proposed plan, $4.16 per gasket. If 10 percent of annual sales were lost with the current system, the cost is $4.16(0.10)(5304) = $2206. Loss will be reduced if proposed plan is implemented. (2) DB032Drive Belt
a. The New Plan
The following calculations are based on the weeks 13 to 21, the reason to not include week 11 and 12 are because of the products start up makes the estimates unreliable.
Demand Average (Weekly) = 52belts per week
Annual Demand = 2704 belts
Holding Cost = $0.97 per year
Ordering Cost= $10 per order
EOQ=
= 236 Gaskets
We now use the DB032 table to find the standard deviation:
Standard deviation in weekly demand = 1.76 belts
Standard deviation in demand during lead time = 1.76√3 = 3.05 belts R= average demand during the lead time + safety stock
= 3(52) + 1.65 (3.05) = 161.03 belts
b. Cost Comparison
Cost Category
Current Plan
Proposed Plan
Ordering Cost
2704 / 1000 x 10= $27
2704/1000X0.52X8.89= $115
Holding Cost
0.97 x 1000 / 2 = 485
236X0.97/2= 114
Total
$512
$229
The total of these costs have reduced by 55 percent. The safety stock of the proposed plan will be higher (as with the gaskets), but the added cost of the safety stocks is only $0.97(5) = $4.85 The lost sale is the big cost here of 4.27 per belt. If 10 percent of the sales were lost, the cost with the current method will be $4.27(0.10)(2704) = $1155. This loss will be less if implemented with the proposed plan.
References:
[1] http://www.investopedia.com/terms/b/back-order.asp