McLeod Motors LTD
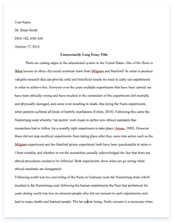
- Pages: 5
- Word count: 1199
- Category: General Motors Logistics
A limited time offer! Get a custom sample essay written according to your requirements urgent 3h delivery guaranteed
Order NowMcLeod Motors Ltd factory in Chilliwack, British Columbia makes over 40 models of electric motors ranging from one quarter to 10 horsepower. The company has a number of customers in the original equipment manufacturer (OEM) market, which used the motors as components in larger products, and also in the replacement market. Naturally, McLeod’s product mix changed over time as its OEM customers phased products in and out and made annual supply decisions. Recently the company has started facing problems in inventory management since it standardized end shields considering that it would cut both the manufacturing costs and inventories. But the results have been otherwise.
Location of Inventory
The plant is divided into three parts. One half is for production; the other half is divided into a small office, and a Warehouse. The warehouse is used for storing and managing the inventory which is located inside the Plant and is headed by plant manager Sue Reynolds.
Major Function of Inventory
Inventory is a list of goods and materials held available in stock by the business. The inventory store keeps the raw materials, work in process, and finished goods and supplies.
Reason for increase in inventory level
In the beginning of the current quarter it was decided by the management to standardize the end shields. The earlier analysis suggested that such standardization would cut down the inventory levels as well as the manufacturing cost. For attaining optimal productivity, the decision was implemented but didn’t yield the expected results. Rather dropping the inventory levels down, it has resulted in a rise.
Action Required
Serious consideration is required to address the problem. As a first step, the decision taken earlier should be rolled back thus eliminating that standardization of end shields that created the problems instead of providing better results.
Problem Statement
To get the Inventory levels back to some acceptable and manageable stage
To reduce the inventory cost that has gone up by 25%
To try having minimal possible affect on the reduced manufacturing cost
Analysis
In the commencement of the current quarter it was determined by the management to standardize the end shields. The previously carried out analysis reported that the standardization of end shields would bring down the current manufacturing cost of motors being developed and would also reduce inventory levels to a considerable extent. For attaining optimal productivity the decision was implemented but didn’t prove effective enough. Though the manufacturing cost has gone down; not up to the expected mark but rather dropping the inventory levels down, it has resulted in a rise. Such an increase has been the reason for 25% more inventory cost and has caused unavailability of storage space. Hence the problem needs to be resolved as early as possible by Plant Manager Sue Reynolds.
Recommendation
An association between inventory and productivity can arise in several ways. One chain of causality begins with successful problem solving, which leads to productivity gains and subsequent inventory reduction. One piece of evidence is the finding of a relatively weak connection between productivity gains and sub-sequent inventory reductions.
Vendor-managed inventory (VMI) is a supply-chain initiative where the supplier is authorized to manage inventories of agreed-upon stock-keeping units at retail locations. The benefits of VMI are well recognized by successful retail businesses such as Wal-Mart. In VMI, distortion of demand information (known as bullwhip effect) transferred from the downstream supply-chain member (e.g., retailer) to the upstream member (e.g., supplier) is minimized, stock out situations are less frequent, and inventory-carrying costs are reduced. Furthermore, a VMI supplier has the liberty of controlling the downstream re supply decisions rather than filling orders as they are placed. Thus, the approach offers a framework for synchronizing inventory and transportation decisions.
Although current interest in supply-chain management overlooks certain transportation/distribution issues, substantial savings are realizable by carefully incorporating a shipment strategy with the stock replenishment decisions for VMI systems. This impact is particularly tangible when the shipment strategy calls for a consolidation program where several smaller deliveries are dispatched as a single load, realizing scale economies inherent in transportation. Formally, shipment consolidation refers to the active intervention by management to combine many small shipments/ orders so that a larger, hence more economical, load can be dispatched on the same vehicle (Brennan 1981, Hall 1987, Higginson and Bookbinder 1995). The main motivation behind a consolidation program is to take advantage of the decreased per unit freight costs due to economies of scale associated with transportation.
Application
In the production and distribution of goods, inventory is the currency of service. An increase in service can virtually always be achieved through an increase in safety stocks, so a supplier inevitably faces a trade-off between service levels and inventory costs. This and related tradeoffs are discussed at least qualitatively in most operations management textbooks in some of the managerial literature, and in the research literature. It raises the question of just how much service inventory can buy; i.e., what is the marginal cost of a service improvement, in units of inventory, if the improvement is achieved through increases in inventory?
For VMI applications, the supplier is empowered to control the timing and quantity of downstream re supply decisions. Thus, the supplier has more freedom to consolidate re supply shipments over time and geographical regions. Full vehicles are more likely to be dispatched, transportation scale economies are easier to achieve, and there is ample opportunity to synchronize the inventory and transportation decisions
Works Cited
Abdelwahab, W. M., M. Sargious. 1990. Freight rate structure and optimal shipment size in freight transportation. Logist. Transportation Rev. 6(3) 271-292.
Arcelus, F. J., J. E. Rowcroft. 1991. Small order transportation costs in inventory control. Logist. Transportation Rev. 27(1) 3-13.
Arntzen, B. C., G. G. Brown, T. P. Harrison, L. L. Trafton. 1995. Global supply chain management at Digital Corporation. Interfaces 25(1) 69-93.
Cheung, K. L., H. Lee. 1998. Coordinated replenishments in a supply chain with vendor-managed inventory programs. Techinal Report, Stanford University, Stanford, CA.
Closs, D. J., R. L. Cook. 1987. Multi-stage transportation consolidation analysis using dynamic simulation. Internat. J. Phys. Distribution Materials Management 17(3) 28-45.
Flynn, J., S. Gartska. 1990. A dynamic inventory model with periodic auditing. Oper. Res. 38(6) 1089-1103.
Gupta, O. K. 1992. A lot-size model with discrete transportation costs. Comput. Indust. Engg. 22(4) 397-402.
Kleywegt, A., V. Nori, M. Savelsberg. 1998. A computational approach for the inventory routing problem. Technical Report, Georgia Institute of Technology, Atlanta, GA.
Lee, C.-Y. 1986. The economic order quantity for freight discount costs. IIE Trans. 18(3) 318-320.
—–. 1989. A solution to the multiple set-up problem with dynamic demand. IIE Trans. 21(3) 266-270.
Schenck, J., McInerney, J. 1998. Applying vendor-managed inventory to the apparel industry. Automat. I.D. News 14(6) 36-38.
Stidham, S., Jr. 1977. Cost models for stochastic clearing systems. Oper. Res. 25(1) 100-127.
Taylor, H. M., S. Karlin. 1998. An Introduction to Stochastic Modeling, 3rd ed. Academic Press, San Diego, CA.
Yano, C., Y. Gerchak. 1989. Transportation contracts and safety stocks for just-in-time deliveries. J. Manufacturing Oper. Management 2 314-330.