Design of Styrene Production Plant
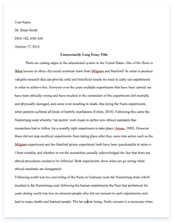
- Pages: 13
- Word count: 3086
- Category: Plantation
A limited time offer! Get a custom sample essay written according to your requirements urgent 3h delivery guaranteed
Order Now1.0INTRODUCTION
As part of the requirements for the Chemical Engineering degree course, the students have to complete 6 credit hours in Plant Design Project (PDP). The PDP is divided into Plant Design Project I (CAB 4014) and Plant Design Project II (CAB 4014). The PDP I and PDP II are offered in the 9th and 10th semesters respectively. Each PDP course carries 3 credit hours. This guideline specifically addresses the Plant Design Project I (PDP I).
This guideline provides the necessary information for students/supervisors in carrying out their duties for PDP I in UTP.
2.0OBJECTIVES
The main objective of PDP 1 is to train/develop students in the application of all the elements of knowledge and skills that have been accumulated throughout the undergraduate program for solving design related problems for typical process industrial plant. The second objective of the course is to develop the skills of working in a team and to nurture leadership qualities. Written and oral communication skills as well as the capability in decision making are also nurtured by the project.
3.0OUTCOMES
At the end of this course, students should be able to:
• Integrate their chemical engineering skills and knowledge in a detailed design of a chemical plant. • Screen a variety of potential process routes and identify the most cost-effective route for a chemical plant • Perform manual mass and energy balance calculation for a chemical plant • Optimize the energy usage by conducting appropriate pinch analysis for a chemical plant • Carry out simulation for a chemical plant using a computer-aided design/engineering software (e.g. ICON,ICON, PDS, PROCEDE, MATLAB)
4.0SCOPES
The scopes of PDP I are as follows:
• Conducting literature survey: properties of the products, usage and cost, alternative process routes for manufacturing the product, chemical and physical property data for all the raw materials, intermediates and final products, environmental considerations, safety considerations, etc. • Identifying and selecting the best process route for a particular design project. • Developing the best possible process flowsheet for the selected chemical process route. • Developing the complete material and energy balance calculations for the selected process. • Using related computer-aided design/engineering software (e.g. ICON, PDS, PROCEDE, MATLAB) as a tool for the design. • Conducting a heat integration study in the final PFD (if applicable) • Making the necessary decisions, judgements and assumptions in design problems.
5.0DURATION
PDP 1 carries 3 credit hours and students are expected to accomplish their project in 14 weeks during the first semester of their final year. A proposed milestone of PDP I can be found in Appendix I.
6.0RESPONSIBILITIES
6.1Students
Students must make their own initiative and able to work in a team in bringing the project to completion. Students will also be required to exercise teamwork spirit and job co-ordination during undertaking the design project. The students may elect one of their team members as the group leader. Among the expected responsibilities are as listed below: • Obtaining information and material rightfully and honestly. Plagiarism will cause serious consequences. • Seeking advice and guidance from supervisors when necessary. • Maintaining good discipline and personal conduct when searching for relevant information especially when out of campus. • Preparing themselves against any failure such as work lost due to computer crashes. • Preparing a logbook for each member and maintain a good record of individual activity and progress. • Undertaking the detailed design of at least one unit operation per person. • Submitting all reports on time as specified by plant design project coordinator. • Giving/putting significant individual contribution or effort towards the completion of the group task. Failure to take the above responsibility/responsibilities may lead to failing the course.
3 Plant Design Project Coordinator (PDPC)
Head of Department will appoint a Plant Design Coordinator (PDPC) and his/her assistants to coordinate PDP I. The responsibilities of PDPC and his/her assistants include: • Identifying and selecting design project title. • Dividing students into respective groups.
• Assigning students to respective supervisors. • Planning and managing the schedule for PDP I course implementation. • Providing briefing on PDP I course requirements to lecturers and students. • Arranging special seminars in selected topics related to the project to give additional skills to the students to complete the project. • Coordinating students’ oral presentation
• Arranging external examiners from industry to participate in the assessment of students’ report and oral presentation. • Compiling and finalizing students’ final scores for submission to examination committee. • The assistants of PDPC will assist him/her in all the above activities.
4 Committee of Supervisors
The committee consists of a main and with not more than two assistant supervisors. The responsibilities of the committee can be summarized as below: • Advising the students on the preparation of their design projects. • Arranging meeting with students periodically. The supervisors are expected to meet their students once a week. • Monitoring students’ progress from time to time. • Assisting students in defining the problem involved accordingly. • Assigning the students to undertake individual detailed calculation of mass and energy balance • Reviewing and assessing the individual student progress. • Assessing reports and commenting on the work. • Delivering seminar lectures on some special topics if requested by the PDPC
PROCESS FLOW OF PDP I
PDPC will assign the general problem for the manufacture of a certain product. The required capacity for the plant may also be indicated in the assignment. As the first step the students have to carry out a literature survey on the given product covering all the aspect of the design problem. By taking general design considerations into account, students will then have to synthesize the best process flow sheet. The next step is to calculate the material and energy balance for the chosen flowsheet. The students must perform manual calculations of material balances first. Then only the students can use available software like ICON for this purpose. However, all the inputs to the software must be tabulated and justified. At this stage, preliminary cost estimation for the design should be prepared using short cut methods. The process flow diagram for the project is shown in FIGURE 1.
8.0 INTERIM REPORT
Students are expected to submit their interim reports as provided in the Gantt Chart.
8.1 Format
8.1.1Language
The report must be written in English Language.
8.1.2Font and spacing
All text should be one and half spacing (Times New Roman regular font style, size 12) written on a white A4 paper on one side of each sheet. The following however should be single spaced: • Foot notes
• Tables and figures
8.1.3Length
The length of report should be not less than 50 and not more than 100 pages of (excluding appendices). Students are encouraged to use brief and straightforward wording and avoid jargon as much as possible. The number of pages for the appendices is unlimited.
8.1.4Numbering
All pages should be numbered in proper sequence from introduction to the end of the report. Page number must be positioned at the bottom and centered.
8.1.5Heading and Margin
Major headings, such as INTRODUCTION, should be capitals, bold and font size 14. Secondary headings such as Example, should be in bold. The top, bottom, and right margins are 1 inch except for the left margin, which is 1.3 inch.
8.1.6Mathematical Text
Mathematical text must be spaced out; superscript and subscript must be clearly shown. All equations, terms and symbols must be written in italic.
8.1.7 Tables and Figures
Tables and figures less than a page in size should be inserted into the text near the point of reference. Tables should not be carried over to the next page. Margin limits are the same as text full-page. All tables and figures should be numbered and captioned consecutively. Table heading should be positioned at the top middle of each table. The figure heading should be positioned at the bottom middle of each figure.
8.1.8Bindings
The report must be presented in an ABBA Lever Arch Files (404 Standard).
8.2Contents
8.2.1 Title Page
The title page should be set out in accordance with the attached specimen sheet in Appendix II. The project title should be clearly and precisely defined as has been assigned by the PDPC.
8.2.2Certification
This section should be approved by supervisor after he/she has satisfied with the correction or amendment done by the student. See Appendix III for specimen sheet.
8.2.3Acknowledgements
Most design teams obtain considerable assistance and advice from supervisors, industrial consultants, librarians, faculty and fellow students. This section provides an opportunity to acknowledge their contributions with an expression of appreciation and thanks.
8.2.4Table of Contents
All sections in the report should be listed, including the page numbers on which they begin. Hence, all pages in the report, without exception, must be numbered. Each main section must begin with a new page.
8.2.5Executive Summary
The students should highlight all the important features of the report from the technical reasons for undertaking the study to the conclusion. Remember that most readers only read the summaries of reports and every word counts. Avoid padding phrases and phrases that refer to the reports.
8.2.6Main Body
The main body of the report must be composed of the following chapters:
Chapter 1: Introduction
Background of the design project, problem statement, objectives, scopes of work.
Chapter 2: Literature Review
Carry out research to uncover the latest information on feed and product properties, product price, market and possible site locations that may lead to a more profitable design. Literature resources include encyclopedias, handbooks, journals, reports, indexes and even World Wide Web (Internet). Standard method for quoting must be implemented and standardize throughout the report.
Chapter 3: Preliminary Hazards Analysis
The preliminary hazard analysis should be carried out during feasibility study to define/determine safety-related aspects that influence the design. The study should cover the following points: • Summary of previous accidents on similar type of plants. • Identification of material and chemical hazards in the process such as feed, intermediates, products and by-products, flammability data, toxicity data, chemical interactions etc. Compile all MSDS in the appendix session. • Discussion on the possibility to reduce potential consequences of an accident by considering inherent safety aspects such as substitute hazardous chemicals, reduce inventories, lower pressure and temperatures, safe location, siting, plant layout and transportation. • Identification of any requirement/compliance by local safety regulations and design guidelines
Chapter 4: Conceptual Design Analysis
To evaluate few alternative processes and select the best process among them for the design. 4.1Preliminary Reactor Optimization
To optimize the reactor conversion, selectivity and yield with appropriate recycle block by performing economic potential analysis based on a simple reactor cost model.
4.2Process Screening
Developed few process alternatives based on the separation train sequence using heuristic approach or minimum vapor flow approach. Perform preliminary mass balance, which must be manually done in spreadsheet (block form). No ICON simulation should be used here. Evaluate the alternatives and select the best configuration with appropriate justifications.
4.3Economics Evaluation
Conduct a profitable analysis by evaluating the economic potential of the project. Appropriate comparison to initial economic evaluation must be performed.
4.4Process Flowsheeting
Performing the detailed process flowsheet based on the selected process with their interconnections (involving the reaction, separation, and temperature and pressure-change operations). A complete Process Flow Diagram (PFD) must be generated by using ICON. All inputs to the flowsheeting software must be listed in the report and explained and justification for the choice values provided. Process Flow Diagram should be drawn on A1 size paper, then folded and inserted in A4 sized plastic wallets, along with the report. All streams are numbered clearly and all the process units are labelled. In addition, the drawing should contain a material balance block that is a table showing for each numbered stream: • Total flow rate
• Flow rate of each chemical species • Temperature
• Pressure and other important properties e.g. enthalpy, density etc. All units must be reported in SI.
Chapter 5: Heat Integration
To optimize the energy usage by conducting appropriate pinch analysis. A heat integration study may be incorporated in the final PFD if applicable for the particular flow sheet chosen. In addition, care must be taken to ensure appropriate heating and cooling media are being applied at the most cost effective way.
Chapter 6: Process Flowsheeting
Produce a full description of the finalized PFD after heat integration.
8.2.13Conclusion and Recommendation
This section is important as it reflects the essence of the report. Hence, the highlights from Introduction and Theory sections should be included.
8.2.14References
All references should be cited according to Harvard system. References including sources of physical data should be listed. The following method of referencing must be followed. In the text refer to the work by the last name of the author followed by the year in brackets. If there are 2 authors give the last name of both the authors. If there are more than 2 authors give the last name of the first author followed by et.al. In the bibliography list all the references in the alphabetical order of the last name of the first author. All the authors must be listed as shown in the examples below, followed by year in bracket, the name of the article or book, Name of the Journal, Volume, No and page No. In the case of books the name of the book, edition and publisher should follow the name of the author and year. For example:
Nozhevnikova et. al (1997) has discussed the methanogenesis reactions taking place in natural environments. Abu-Absi and Actis (1999) give a detailed description of different reactions taking place in an anaerobic reactor. Metcalf and Eddy (1991) discussed about the operational aspects of anaerobic reactions. Otton(1998) has presented results on anaerobic digestion in fluidised bed reactors. Adam (2000) gives some interesting insights into the natural anaerobic processes.
Listing of these references is as shown below.
References
1.Abu-Absi, N.R. and L.A. Actis (1999), Encyclopaedia of Bioprocess Technology: Fermentation, Bio Catalysis and Bio Separation, Vol 1, John Wiley and Sons, New York.
2.Adam, D. (2000), Where there is muck there is gas, http://WWW.nature.com/nsu_pf/000420-1.html (date last access)
3.Metcalf. C and R. Eddy (1991), Wastewater Engineering: Treatment, Disposal and Reuse, 3rd Ed., Mc-Graw Hill Inc, New York.
4.Nozhevnikova, A.N., C.Hollinger, A.Amman and A. J. B Zehnder (1997),
“Methanogenesis in Sediments from Deep lakes at Different Temperatures (2-70oC)”, Water Science and Technology, Vol 36, No 3, pp 384-396.
5.Otton, V. (1998), Anaerobic Digestion in Fluidised Bed Reactor, MSc Thesis, Institute National Polytechnik, Grenoble.
8.2.15Appendices
Lengthy calculations, figures, results from programming, derivation of design data, etc. should be enclosed in the appendices. Students must provide a clear explanation and the author name for each calculation. The Process Flow Diagram (PFD) should be drawn in an A1-size paper. The drawing should then be folded and inserted in an A4-size plastic pocket as part of the interim report.
9.0INTERIM ORAL PRESENTATION
Within the Week 12 to 13, each group will be assessed by the internal examiners through the interim oral presentation. This presentation consists of process flow sheets with complete material and energy balance. During the presentation, students are expected to be able to explain: • Background of the design project, reasons for and range of study as well as definition of the problem. • The potential hazard associated to the processes.
• Process flowsheeting design
• Potential heat integration.
• Basic costing.
• Selection of equipment.
• Future implementation on the design.
10.0RESOURCES AND SERVICES REQUIREMENTS
Students are allowed to seek information or any sort of material needed for the project at any institutions or other places. Application letters to Head of Programme should be written by the students through the main
supervisor. The main supervisor must fill-up Form PDP I-1 (Appendix IV) and submit to PDPC together with the application letter. All requisitions are subjected to approval of Head of Programme.
11.0ASSESSMENT TECHNIQUE
At the end of the semester, all student works will be assessed and final grade will be given. Table 1 summarizes the overall technique of assessment. The internal examiners will be selected among the supervisors to assess the interim oral presentation and report.
Table 1. Assessment Scheme
|Assessment Stage |Examined by and % marks |% Contribution to | | |Supervisor |Internal |Group mark |Individual mark | | | |Examiner | | | |Interim Oral Presentation | |25 |15 |10 | |Individual Progress Performance |10 | | |10 | |Interim Report |25 |40 |65 | | |C-factor | | | |Total |90% |10% |
12.0GRADING SCHEME
1 Interim Oral Presentation
The interim oral presentation contributes 25% of the overall PDP I marks. The internal examiners are responsible to assess the presentation in the technical and non-technical aspects. Samples of score sheets can be referred to Form PDP I-2 and PDP I-3 (Appendix IV)
1. Interim Report
Supervisors and internal examiners will judge the final report. The report accounts for 65% of the overall marks in which 25% comes from the supervisor and 40% from the internal examiners. See Forms PDP I-4 (Appendix IV).
2. Individual Progress Performance
Each group is required to conduct an official meeting once in every two weeks. The first official meeting must be held in the first lecture week of the semester. The last official meeting will be held on week 13th, which will constitute a total of seven (7) official meetings. Minutes of meeting (MOM) must be submitted to the main supervisor within one (1) week after the meeting. Supervisors have to evaluate the individual progress performance by filling up the Form PDP I-5 (Appendix IV). Individual progress performance will contribute 10% of the overall individual marks. Students and supervisor may conduct additional meetings as frequent as required.
12.4 Peer Review
Students get to evaluate among themselves through the peer review session by filling up Form PDP I-6 (Appendix IV) and return it to PDPC.
12.5C-Factor
C-factor is introduced to assess students on their contribution to the group work by the supervisors. Supervisors can take the results from the peer review as a reference in assessing the C-factor. The amount of the group mark that can be obtained by individual is depending on the C-factor value that he/she gets. See Form PDP I-7 (Appendix IV)