Chemical Hazards
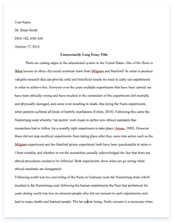
- Pages: 14
- Word count: 3409
- Category: Chemistry
A limited time offer! Get a custom sample essay written according to your requirements urgent 3h delivery guaranteed
Order NowChemicals can affect the skin by contact or they affect the body either through the digestive system or via the lungs if air is contaminated with chemicals, vapor, mist or dust. There can be an acute effect, i.e. the person is affected immediately, or there can be a chronic effect, i.e. the person is affected in the medium to long term due to the accumulation of chemical or substances in or on the body. INTRODUCTION
Hazards in a workplace are controlled by a combination of âlocal controlsâ Specific to a hazard, and âmanagement controlsâ for ensuring that these are implemented and remain active. THIS IS AN IMPORTANT PRINCIPLE TO REMEMBER.
The implementation of controls to fix a specific hazard, e.g. chains to prevent gas cylinders toppling over, or hearing protectors to reduce exposure to noise, must be supplemented by management activities to ensure they are being implemented, that they are adequate, and that they remain effective. The mechanism for the control of a hazard may not necessarily be a physical one, but may be a rule or practice designed to reduce the risk from the hazard. It is necessary to ensure that once hazard controls are put in place they stay in place and are used, and it is also necessary to provide a feedback mechanism for ensuring whether or not the controls are adequate and responsibilities are Understood by all.
CONTROL OPTIONS
When a hazard has been identified and assessed as needing some control measure, then the next process to go through is the selection of which option is required. The final choice of an option is based on factors such as the potential severity of harm posed by the hazard, the likelihood of injury or illness occurring, the cost of control measures, or whether it has been identified as a significant hazard.
It is important, however, to LOOK AT ALL OPTIONS before making a decision, even though the identified hazard may already have some controls in place. CONTROL OF SIGNIFICANT HAZARDS
Hazards that are assessed as âsignificantâ present such a degree of risk that the Act requires a more formal approach in dealing with them. The primary aim is the elimination of significant hazards if practicable. Sections 8, 9 and 10 of the Health and Safety in Employment Act 1992 contain specific requirements for the control of significant hazards. These sections require that the following steps are to taken once significant hazards have been identified in an organization:
1. Significant hazards to employees are to be eliminated where practicable. 2. If this is impracticable, those hazards are to be isolated. 3. If this is also impracticable, all practicable steps must be taken to minimize the likelihood that the hazard will be a source of harm to the employees. If this step is followed:
⢠It must include the supply and use of protective equipment; and
⢠Employee exposure to the hazard must be monitored, and health monitoring carried out with employee consent.
Once the significant hazards in the workplace have been identified, it is necessary to decide which of the three steps is to be used to control each hazard. Outline of the process
For each of the previously identified significant hazards the following questions must be asked in order:
⢠Can the hazard be eliminated?
If so, list the steps to achieve this or, if not, why not?
TEST YOUR REASONS FOR NOT ELIMINATING IT AGAINST THE âALL
PRACTICABLE STEPSâ REQUIREMENTS ,
OR IF NOT, THEN
⢠Can the hazard be isolated from the employees?
If so, what steps are needed or, if not, then why not?
TEST YOUR REASONS FOR NOT ISOLATING IT AGAINST THE âALL
PRACTICABLE STEPSâ REQUIREMENTS,
OR IF NOT, THEN
⢠What will be done to minimize the likelihood of harm from the hazard? ⢠What equipment and clothing are needed to protect employees from the harm?
⢠How are employeesâ exposure to the hazard and their health in relation to the exposure being monitored?
List the answers and then
TEST YOUR STEPS FOR MINIMISING THE LIKELIHOOD THAT THE
HAZARD WILL CAUSE HARM AGAINST THE âALL PRACTICABLE
STEPSâ REQUIREMENTS
The hierarchy of steps above ensures that supplying employees with protective equipment to guard against the hazard is not done without first considering and evaluating the other more effective options.
CONTROL OF OTHER HAZARDS
The process used for significant hazards may also be used to determine the control methods for other hazards. However, should you choose not to, then the following process can be used.
The process outlined
For each âother hazardâ ask these questions in the following order: ⢠Can the hazard be removed by design and engineering?
⢠Can the hazard be removed by substitution?
⢠Can the risk from the hazard be reduced by changing the process? ⢠Can the risk from the hazard be reduced by enclosing it to isolate it from workers?
⢠Can the hazards be removed at source before they can affect the workforce? ⢠Can the hazard be reduced by segregating the process from workers other than those needed to the process?
⢠Can personal protective equipment be used to reduce the risk of injury? ⢠Can rules or procedures be developed to reduce the risk of injury? Put in place and how you intend to implement these hazards. It is important to realize that the methods and systems for the control of hazards, whether significant or not, DO NOT exist in isolation from the other activities organizations undertake in order to carry out their business. The hazard identification and control Risk Assessment Steps: –
* Step 1 – Identify the Hazards
* Step 2 – Decide Who Might be Affected
* Step 3 – Ensure Necessary Controls are Adequate and In Place
* Step 4 – Record the Findings
* Step 5 – Review What you Have Done
A risk assessment should follow five simple steps:
Identify the Hazards
Step 1 – Look for the hazards. If you are doing the assessment yourself, walk around your workplace and look at what could reasonably be expected to cause harm. Ignore trivial points and concentrate on what could result in serious harm or affect several people or more. Try to look at your business with a fresh pair of eyes.
Decide Who Might be Affected
Step 2 – Decide who might be harmed and how. Remember that some people may be at greater risk, for example trainees, new members of staff, contractors, young people, expectant mothers or employees with existing medical conditions. Also do not forget to include cleaners, visitors, maintenance people, members of the public especially children, and shift workers.
Ensure Necessary Controls are Adequate and In Place
Step 3 – Evaluate the risks and decide whether existing precautions are adequate or whether more needs to be done. Consider how likely it is that each hazard could cause harm. Even after all precautions have been taken, some risk usually remains. What you have to do is to decide for each significant hazard is whether this remaining risk is high, medium or low. First, ask yourself: * Have you done everything you are legally required to do? For example, there are legal requirements on prevention of access to dangerous parts of machinery. * Have you applied generally accepted industry standards? The aim is to make all risks small. If you find something that requires action, ask yourself: * Can I get rid of the hazard altogether?
* If not, how can I control the risk so that harm is unlikely? Use the following hierarchy to reduce risk:
* Try a less risky option
* Prevent access to the hazard
* Organize the work activity to reduce exposure to the hazard * Issue Personal Protective Equipment (PPE)
* Provide washing facilities for the removal of contamination and first aid
Record the Findings
Step 4 – Record your findings. If you have five or more employees, you must record the significant findings of your risk assessment. This means writing down the significant hazards you have identified and what action you have taken to reduce the risk. There is a legal requirement to make sure that your risk assessment is suitable and sufficient. You will need to show that: * Proper checks were made
* You identified who might be harmed, and how
* You dealt with all the obvious or significant hazards
* The action you took was reasonable and reduced the risk
Review What you Have Done
Step 5 – Review your assessment. A risk assessment should be a working document that is reviewed regularly to ensure that it is still effective. You should consider reviewing your assessment, for example, when your main business activity changes, if you move premises or when you purchase new pieces of equipment. If, when reviewing your assessment, you identify new hazards then your assessment may need to be revised to control these new hazards. Roles and Responsibilities
1. Designate, assign, appoint or engage a competent person leading a team of personnel (including contractors) associated with the process or activity to conduct risk assessments; 2. Ensure that the risk control measures are implemented without undue delay after the completion of risk assessment; 3. Inform all persons working at the workplace of the risks, and the means to minimise or, where possible, eliminate the risks; 4. Provide a risk assessment register to record the findings of risk assessment; 5. Endorse and approve the risk assessments conducted;
6. Keep risk assessment records for inspection for at least three years from the date of the assessment; and submit the records to the Commissioner for Workplace Safety and Health if the Commissioner so requires; 7. Review and update the risk assessment at least once every three years or whenever there is a significant change in the work, or after an incident involving the work process; 8. Ensure that all employees are aware of the risk assessment for the work activity they carry out; 9. Develop and implement safe work procedures (SWPs) for work which poses safety or health risks to workers; and 10. Keep a written description of SWPs and produce this to the inspector for inspection when requested.
MANAGEMENT CONTROLS
These are the activities that an organization uses to manage a safety and health programmed. There are usually a number of basic management control activities that are common to all hazards, although some hazards may require more. These include:
⢠Involvement of employees in the development of health and safety procedures.
⢠An information system to ensure employees are informed about and understand the risks from hazards they work with.
⢠An accident reporting and investigation system.
⢠Regular surveys of the workplace.
⢠Responsibilities being assigned to ensure hazard controls are implemented and remain effective.
⢠An audit system for checking that the controls for specific hazards are in place and working.
⢠An adequate training programme and adequate supervision for all staff.
â˘Â Implementing emergency procedures, perhaps in conjunction with local emergency services, to limit the consequences of an emergency. Responsibility
Responsibilities are assigned to ensure that the existence of each hazard is made known to all those exposed to it, and that they are instructed in the use of the correct procedures when exposed to the hazard.
Example
An illustration of the connection between the management control activities mentioned above and the local control activities can be made by looking at the following simple example, where the hazard could not be eliminated or isolated. Hazard: Exposure to talc when emptying bag into hopper.
Assessment: Sustained inhalation of significant amounts of talc can produce symptomatic pneumoconiosis. MSDS sheet
supplied with product states precautions needed.
Local controls: – Ventilation hood over hopper (interlocked with process).
– Protective face mask (worn when emptying bags).
– Disposable overalls.
Management controls:
– Plant survey every month to check procedures and the efficiency of ventilation system.
– Training for staff in hazards of talc and reasons for protective clothing.
– Audit every year to ensure training is given and that hazards and responsibilities are known about and understood.
Medical examination of people using talc every three years as part of ongoing monitoring process.
– Test every six months to what extent staff are exposed to talc. Use personal monitoring method.
– Employees given the results of monitoring
Hazard Control Plan
To be developed in consultation with management and employees with specialist advice as appropriate.
HAZARD TO BE CONTROLLED
A. HAZARD CONTROLS
RESPONSIBILITIES
1) To implement
2) To monitor
TIMEFRAME FOR IMPLEMENTATION
B. MANAGEMENT CONTROLS
RESPONSIBILITIES
1) To implement
2) To monitor
TIMEFRAME FOR IMPLEMENTATION
10 Types of hazards
Use these notes to help you identify and assess hazards that might occur in your workplace.
Chemical hazards
Chemicals can affect the skin by contact or the body either through the digestive system or through the lungs if air is contaminated with chemicals, vapour, mist or dust. There can be an acute (immediate) effect, or a chronic (medium to long-term) effect from the accumulation of chemicals or substances in or on the body.
Noise hazards
Excessive noise can disrupt concentration, interfere with communication, and result in loss of hearing. High impact noises are particularly damaging. Noise can also mask out signals, affecting communication or danger warnings.
Radiation hazards
Equipment such as radioactive gauging devices or the radioactive trace element used in analytical chemistry produce Ionizing radiation. Non-ionizing radiation covers infrared radiation (heat-producing processes), lasers, ultraviolet radiation (welding, sunlight), and microwaves (high-frequency welders, freeze drying).
Electrical hazards
These include the risk of injury from all forms of electrical energy.
Lighting hazards
Inadequate lighting levels are a potential safety hazard. A common problem area is the reaction time needed for the eyes to adjust from a brightly lit to a darker environment â such as a forklift driver coming indoors from bright sunlight. Temporary lighting is often inadequate.
Vibration hazards
This includes whole-body vibration â for example, truck drivers, people standing on vibrating platforms, and operators of mobile equipment â and also more localized vibration effects from such equipment as hand tools, chainsaws, and pneumatic hammers.
Temperature hazards
Extremes of cold or heat can cause problems such as tiredness, vulnerability to infections or reduced capacity to work.
Biological hazards
These include insects, bacteria, fungi, plants, worms, animals and viruses. For example, poultry workers exposed to bird feathers and droppings to which they are allergic can contract a medical condition. Brucellosis is a well known problem in New Zealand associated with people handling meat and meat products infected with rubella. Hepatitis and the AIDS virus are other biological hazards.
Ergonomic hazards
Ergonomics (the âfitâ between people and their work) covers risk of injury from manual handling procedures, incorrectly designed desks or workstations, audio and visual alarms, and colour coding control mechanisms.
Physical hazards
These include a wide range of injury risksâ as diverse as being caught in or by machinery, buried in trenches or hurt by collapsing machinery. This category also includes the hazards from working in confined spaces, being hit by flying objects, caught in explosions, falling from heights and tripping on obstacles. HIERARCHY OF HAZARD CONTROLS
1.Elimination Most Effective Control
2. Substitution
3. Engineering Controls (Safeguarding Technology)
4. Administrative Controls (Training and Procedures)
5. Personal Protective Equipment Least Effective Control
EXAMPLES OF EACH STEP IN THE HIERARCHY OF HAZARD CONTROLS
1. Elimination
The best way to control a hazard is to eliminate it and remove the danger. This can be done by changing a work process in a way that will get rid of a hazard; substituting anon-toxic chemical for a toxic substance; having workers perform tasks at ground level rather than working at heights; and other methods that remove the hazard all together.
2. Substitution
The second best way to control a hazard is to substitute something else in its place that would be non-hazardous or less hazardous to workers. For example, a non-toxic (or less toxic) chemical could be substituted for a hazardous one.
3. Engineering Controls (Safeguarding Technology)
If a hazard cannot be eliminated or a safer substitute cannot be found, the next best approach is to use engineering controls to keep the hazard from reaching the worker. This could include methods such as using noise dampening technology to reduce noise levels; enclosing a chemical process in a Plexiglas “glove box”; using mechanical lifting devices; or using local exhaust ventilation that captures and carries away the contaminants before they can get in the breathing zone of workers.
4. Administrative Controls (Training and Procedures)
If engineering controls cannot be implemented, or cannot be implemented right away, administrative controls should be considered. Administrative controls involve changes in workplace policies and procedures. They can include such things as: * Warning alarms
* Labeling systems
* Reducing the time workers are exposed to a hazard, and
* Training.
For example, workers could be rotated in and out of a hot area rather than having to spend eight hours per day in the heat. Back-up alarms on trucks that are backing up are an example of effective warning systems. However, warning signs used instead of correcting a hazard that can and should be corrected are not acceptable forms of hazard control.
5. Personal Protective Equipment
The use of personal protective equipment (PPE) is a way of controlling hazards by placing protective equipment directly on workers’ bodies. Examples of personal protective equipment include: respirators, gloves, protective clothing, hard hats, goggles, and ear plugs.
Personal protective equipment is the least effective method for protecting workers from hazards. PPE should be used only while other more effective controls are being developed or installed, or if there are no other more effective ways to control the hazard.
This is because:
* The hazard is not eliminated or changed.
* If the equipment is inadequate or fails, the worker is not protected. * No personal protective equipment is fool-proof (for example, respirators leak). * Personal protective equipment is often uncomfortable and can place an additional physical burden on a worker. * Personal protective equipment can actually create hazards. For example, the use of respirators for long periods of time can put a strain on the heart and lungs. While there are some jobs, such as removing asbestos, where wearing adequate personal protective equipment is absolutely essential, there are many jobs where employers hand out personal protective equipment when in fact they should be using more effective hazard control methods.
A WORD OF CAUTION:
When planning for hazard controls, remember that the control selected must not eliminate one hazard while creating another.
For example, it is not acceptable to remove air contaminants from one area by venting them to another area where another group of workers will be exposed. Hazard control measures should eliminate or reduce hazards for all who are potentially exposed to them.
HAZARD CONTROL: WHOSE RESPONSIBILITY?
The ability and responsibility to design jobs safely in the first place, or redesign them when a hazard is detected, lies with management. It is the role of workers and unions to promote the use of the âHierarchy of Controlsâ, making sure those employers are providing the most effective methods for hazard control possible.
Chemical hazards
A chemical hazard can be considered as any chemical agent that may compromise water safety or suitability, as shown in Table 5.1.
Table 5.1: Examples of chemical hazards that may occur in drinking-water supply systems. Chemicals from watershed/catchment| Chemicals fromReservoir storage| Chemicals fromWater treatment process| Chemicals from distribution | | | | |
Nitrate Arsenic Fluoride PesticidesOther heavy metalsOrganic toxicants Herbicides Rodenticides| Algal toxins Cleaners Liner chemicals LubricantsPesticides Herbicides| Flocculants pH adjusters Disinfection byproductsImpurities in treatmentchemicals| Copper Lead Cleaners PetroleumproductsLiner chemicals|
The control measures (see Chapter 6) needed and the frequency of monitoring should reflect the likelihood and consequences of loss of control. In any system, there may be very many hazards and potentially a large number of control measures. It is therefore important to rank the hazards in order to establish priorities. Simple risk assessment matrices are available and have been successfully applied toprioritising hazards in the water industry (e.g. Gray and Morain 2000; Deere et al. 2001). These typically apply technical information from guidelines, scientific literature and industry practice with well informed expert judgement supported by third-party peer review or comparison against other systems (benchmarking). Benchmarking differs from other quality improvement techniques in that its focus is on identifying what the external best practices are for key business functions and processes and has been defined as:
âA method for facilitating continuous improvement by systematically comparing oneâs own processes, practices and performance against the best practice of others with a view to adopting, adapting or enhancing that practice to oneâs own situationâ
REFERENCE
www.osh.govt.nz/order/catalogue/archive/identifyhazards.pdf
Workplace Safety & Health – Ministry of Manpower
Guidance for Hazard Determination for Compliance with the OSHA Hazard Communication Standard https://www.usi.edu/RiskMGT/pdf/USIHazComChem.pdf
http://smallbusiness.healthandsafetycentre.org/PDFs/small%20business/hs_insert.pdf