The differences between Fordist and Post-Fordist work
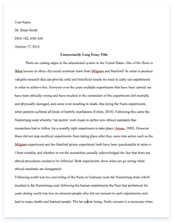
- Pages: 8
- Word count: 1979
- Category: Work
A limited time offer! Get a custom sample essay written according to your requirements urgent 3h delivery guaranteed
Order NowThis essay will focus on the differences between fordist work and post-fordist work. To make the statement clear, I will first present a general definition on both fordism and post-fordism which will involve the back ground of emergence of these two systems. Questions such as how do two systems work in different period, and how do systems developed economics in different ways will be also explained in the essay. Economic change driven by technology change, labour practice change, industrial organization change and market demand change in consumption patterns.
Although there are conflicts between fordist work and post-fordist work, however, they may exist in the same society. Therefore, I will give some examples to support this point in the end. Fordism takes its name from Henry Ford, the American car manufacturer at the turn of the 20th century. The concept itself describes a particular form of economic process based on the idea of a production line. Henry Ford was the first person using the assembly line-the ultimate embodiment of division of labour theory. Ford set up plants in the USA and Britain at the start of the twentieth century to manufacture the Model âTâ Ford.
The poster of his company is âyou can have any colour you like, so long as it is blackâ. This summarizes quite well what Fordist assembly line technology is all about-a standardized product but manufactured at a low price to make it available to the masses. Fordism refers to the system of mass production and consumption characteristic of highly developed economies during the 1940s-1960s. (Scott, P749) Under Fordism, mass consumption combined with mass production to produce sustained economic growth and widespread material advancement.
Fordism is a model for the low cost production of standardized goods for a mass market. Fordism is also an example of the deskilling of work that Braverman considered characteristic of capitalist production. Braverman thinks that assembly-line technology maximized alienation. Under fordism, work was divided into small tasks. These tasks were carried out by low skilled workers with little training. There is a clear division between a mass of semi-skilled workers and a small number of skilled workers carrying out key tasks. Production was controlled by a centralized management.
Under fordism, workers need little skill. Braverman accepted that all societies have had social divisions of labour. In these societies, individuals carry out separate and specialized roles. However, he claimed that only modern capitalism has produced the manufacturing division of labour. By breaking the work into small tasks, the capitalists can reduce the labour cost. They no longer need to employ skilled craft workers at a high wage rate to make a whole product. Unskilled workers can carry out the simplest parts of production.
The more work is divided up and break down, the smaller proportion of work requiring skilled labour. As a consequence, work is deskilled. Braverman saw deskilling as the product of management decisions rather than technology. The techniques used to manage labour in the early factories depended largely on punishment. Later in nineteenth century, there is a movement. Managers made a bigger use of positive incentive schemes intended to increase productivity by paying workers accounting to the amount they produced. This approach is known as scientific management.
Braverman thought that the scientific management of Frederick W Taylor had had an impact on upon the organization of work in capitalism. Scientific management is major innovation to the turn of the century. Scientific management is sometimes referred as Taylorism. Mc Donalds scientific management style is apparent in that it offers: efficiency. Food and service can be easily quantified and calculated. Ritzer suggests that some Mcdonald institutes have become to combine the emphases on time and money. For example, Pizza Hut serves a personal pizza within 5 minutes otherwise the pizza is free.
Consumers will certainly eat in those restaurants. The staffs who work in fast food restaurant are trained to do a limited number of tasks in precisely the way they are told to do. Managers impose their control by ensuring those tasks are carried out correctly. Enzo Mingione argues that there has been a shift from fordist to post-fordist production in the world economy. To justify the naming of post-fordism there has to be implications that post-fordism has demonstrably emerged form tendencies originating within fordism, but still has marks of crucial break with it.
The movement from fordist work to post-fordist work involves a decline in heavy industry and mass production, and a shift to the service sector and those companies making smaller production runs of more specialized products. This results in a reduction in the number of full-time staff with secure employment and an increase in casual, part-time and temporary employment. As a labour process post-fordism can be defined as a flexible production process based on flexible systems and an appropriately flexible workforce. Its crucial machinery is microelectronics-based information and communications technologies.
Post-fordism is based on the dominance of a flexible and permanently innovative pattern of accumulation. It is based on flexible production, rising incomes for polyvalent skilled workers and the service class and increased profits based on technological and other innovations. Also post-fordist accumulation will be more oriented to world wide demand, not so much on demand within a state. Post-fordism is more demand than supply-driven. Competition will turn on non-price factors such as improved quality and performance for individual products and responsiveness to customers.
The money form will be dominated by private, rootless bank credit which circulates internationally. Michael J Piore believed that capitalist countries have entered a post -fordist society. He also claims that much work is now organized according to the principles of flexible specialization. According to Piore, manufacturers have used new technology, particularly computers, to make manufacturing more flexible. New technology helps industry to meet changing demands. Consumers are increasingly demanding more specialized products and the demand for mass-produced article is decreasing.
As companies become more flexible, they require more flexible and skilled workers. Under post-Fordism, because of workers have long training, and they are important to the company, they enjoy more job security. Flexible specialization increases the skills needed by the workforce and unlike industries where scientific management techniques are used, workers may cooperate with management in organizing the labour process. Job satisfaction increases and industrial conflict decreases. Similar views have been developed by the British economist John Atkinson in his theory of the flexible firm.
Atkinson believes that a variety of factors have encouraged managers to make their firms more flexible. According to Atkinson, there are two forms of flexibility. One is functional flexibility. The other is numerical flexibility. Functional flexibility refers to the ability of managers distribute workers between different tasks. (Haralambos, P713)It requires the employees with multi skilled and also can work in different areas within a firm. If one staff is absent, the other one can cover him easily. Such flexible workers are the cores of a companyâs workforce. They are employed full time and have job security.
The core is usually made up of managers, designers and technicians. Numerical flexibility on the other hand refers to the ability of firms to reduce or increase the size of their labour force. (Haralambos, P714) The first peripheral group have full time jobs but less job security than core workers. They are easier to recruit than core workers because their skills are common to many different firms. The second peripheral group of workers are more flexible. They are not full time permanent employees; they may work part time, on short -term contracts or under temporary contracts.
Other ways of working are also used such as self-employment and home working. Like Piore, Atkinson doesnât agree with Braverman where Braverman thought work had been deskilled. Atkinson thought most workers have their skill increased. In many different aspects, fordism and post-fordism are totally different. In the technology aspect, fordism has low technology, low skill needed and mass production while post-fodism has technological innovation, higher skilled needed and batch production. In the product aspect, fordism has mass marketing combined with mass consumption and has relatively low cost.
However, under post-fordism, the product has high price and high quantity. In the labour aspect, under fordism, the jobs are fragmented into small tasks and also the workers have short training. In contrast, under post-fordism, workers have long training with multi skill. However, Anna Pollert tried to dismantle the theory of flexibility. She argues that the flexibility process within the organisation of work. She believes that the theory is certainly over-simplified and at times inaccurate. Firstly, Pollert doesnât believe that fordist production methods have ever been as dominant as flexibility and post-fordist theory implies.
Small batch production was important in the twentieth century. And also she thinks that the companies use flexibility to produce specialized products was nothing new. Pollert believes that there has never been any market reduction in the importance of mass production. Moreover, Pollert thinks that the spread of flexibility in industry is in any case limited by the cost of new technology. Computer controlled machinery is very expensive and often only big firms can afford it. Japanese business is a good example of producing cheap, well-designed and reliable products rather than specialist products in small numbers.
Secondly, Pollert claims that flexibility can have a wide variety of effects upon work. She says that more flexibility production may lead to continuing traditional skills, deskilling, skill increases and skill polarisation. Management may come into conflict as a result of the introduction of new technology or management proposals for new working practices. The term of neo-fordism is referred to a half-way position between fordism and post-fordism. Many of the post-fordist changes in work organization and management are merely minor modification to basic fordist methods.
Neo-fordism describes flexible development which remains within mass production. It tends to result in a workforce with limited forms of multi skill rather than attempting to create skilled craft workers with knowledge to contribute the system of production. Argos Company is a good example for neo-fordism. Consumers select their purchases from catalogues which displaying over two thousands goods. The goods come from the âback of the shopâ and the stock request forms completed by the consumer are recorded on the computer for automatic reordering and resupplying.
The âjust in timeâ method of reordering stock enables Argos to hold sufficient stock in store to fulfil current demand without overstocking. Staffs who are generally part-time women and students aged 16-19 years are employed to operate till. Full time workers are normally store managers, area managers, buyers and decision makers. There is little training for the part time till, counter or âback of shopâ workers. Decision making is not expected in the job because the computer programme deals with it all. (Madry N. and Kirby M, P58) Although there are conflicts between fordism and post-fordism, but two systems may exist in the same society.
Car manufacture is an example. Up to now, the car manufactures still have mass production combined with mass consumption. However, the workers have multi skill. They can move to different departments easily. More over, the system of management is controlled by the computer. More and more high technology is used in the production of cars. So in this case, we either live in a fordist or post-fordist society. The steel industry is a mass product market. Products increase from 607 million metric tonners in 1990 to 761 million metric tonners in 2000 while the employment decrease form 2. million in 1974 to less than 0. 9 million in 2000. The reason for that is new technology increasing its productivity. Hence, both fordism and post-fordism can exist in the same industry. In conclusion, fordism has mass production combined with mass consumption. Post-fordism on the other hand has flexible specialization with new technology. There is a movement from fordist society to post-fordist society where workers tend to have more skills and have a good knowledge about new technology such as computer. However, mass production is still used in most industries combined with some new technology.