The Seven Layout Strategies Presented
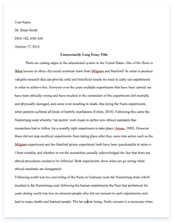
- Pages: 3
- Word count: 526
- Category: Job
A limited time offer! Get a custom sample essay written according to your requirements urgent 3h delivery guaranteed
Order NowThe seven layout strategies presented in this chapter are office layout, retail layout, warehouse layout, fixed position layout, process oriented layout, work cell layout, and last product oriented layout. Each layout has its own objective for example office layout positions workers, their equipment and space. The next layout is retail layout it allocates shelf space and responds to customer behavior. warehouse layout objective is to balance low cost storage with low cost material handling. 11. The layout variables that I would consider particularly important in an office layout where computer programs are written are . An office layout in constant flux as the technological change sweeping society alters the way offices function.
The five core characteristics of a good job design are skill variety, requiring the worker to use a variety of skills and talent. Next is job identity allowing the worker to perceive the job as a whole and recognize a start and a finish. Third is Job significance providing a sense that the job has an impact on the organization and society. Autonomy is the following character tics which offers freedom, in dependence and discretion. The last one is feedback, providing clear, timely information about performance. 6. The differences among job enrichment, job enlargement, job rotation, job specializations, and employee empowerment are many. Job specialization would assist in reducing labor costs of multi skilled artisans. Job enlargement is considered a horizontal reconstructing method in that the job is enlarged by adding related tasks.Job enrichment is a type of job redesign intended to reverse the effects of tasks that are repetitive requiring little autonomy. Some of these effects are boredom, lack of flexibility, and employee dissatisfaction (Leach & Wall, 2004). Job rotation is the practice of transferring an employee from one work station or activity to another during the working day in order to add variety to a job: often used in assembly line work.
You can distinguish between the types of risks in the supply chain are processes, controls, environmental. process is considered raw material and component availability, quality and logistics. Control is considered management metrics and reliable secure communication for financial transactions, product design, and logistics reading. Last is Environmental which consists of custom duties, tariffs, security screening, natural disaster, political issues and currency fluctuations. 14. Purchasing can implement just in time deliveries by real time inventory tracking.
The four type of inventory are raw material and purchased components, work in process, maintenance, repair, and operating , and last finished goods. Raw represent the cost of components purchased from other manufacturers that will become part of the finished product. Work in process inventory refers to the products that are not yet complete. A reflection of the amount of manufactured product in stock that is available for customer purchase.
The types of cost that are involved in an inventory system are costs holding: cost of capital invested and space required; shortage cost: the cost of lost sales or customers who never return; the cost of lost good will; order cost: the costs associated with ordering, transporting, and receiving the items; unit cost: the actual cost of the item.