Total Quality Management Argumentative
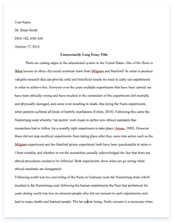
- Pages: 6
- Word count: 1487
- Category: Management Qualities
A limited time offer! Get a custom sample essay written according to your requirements urgent 3h delivery guaranteed
Order NowTotal quality management (TQM) is an integrated organisational effort designed to improve quality at every level. TQM is an approach to improving the effectiveness and flexibilities of business as a whole. It is essentially a way of organising and involving the whole organisation, every department, every activity and every single person at every level. TQM ensures that the management adopts a strategic overview of the quality and focuses on prevention rather than inspection. TQM is a process whereby the need to get everything right the first time and to continually improve the business production is required. Do It Right the First Time (DIRTFT) is a TQM approach where getting things right first time is important to ensure that the business focuses on the customer. “It” quite simply is the customer requirements. However, simple is not so simple. The customer requirements must be clearly defined and communicated. This is done with drawings and specifications but also must be considered when developing procedures and training programs, performing failure mode and effect analysis, and reviewing process capabilities.
It is a concept that needs to be embraced within the business community now more than ever. Granted problems can occur which were not anticipated but the concept of doing something right the first time is a money saver for any business. The key to accomplishing this objective is having the right processes and instructions in clear language so all employees know what is expected of them. Businesses focus on their bottom line and attempt to evaluate how they can increase profits. It is an objective of all businesses who want to be successful and have a fair share of the marketplace for their products and services.
The concept or culture in some cases may be difficult for some businesses but when they understand how they can profit, they readily accept the concept. The world of business today is different with a global economy. In the past competition was not about the world but competition across the street or in your city or state. Today competition is much more widespread than in the past. It is also difficult given the economic conditions of our country and the world in general. True not all businesses compete globally as some compete just in our own country. The concept of doing something right the first time applies to all businesses regardless of type, location or market share. The cost factor is the biggest incentive to putting this policy in place for it costs less money to do something right the first time than to do it over a second time. Each time an item needs to be redone it costs additional time and money in manpower not to mention the lost time in making new products.
Quality is also involved in this concept as doing it right the first time means doing it with quality. Quality is engrained in this concept as poor quality often results in unsatisfied customers and sometimes returned products for replacement or rework. Products and services lacking quality characteristics is looked upon unfavourably by customers. Businesses need to look at the benefits of quality initiatives within their organization along with the concept of doing it right the first time. Poor quality products and services cost businesses in lost sales revenue not to mention the possibility of lost customers who may go somewhere else to purchase products from competitors. It can also cost the loss of potential customers.
The cause of poor quality affecting this principle can sometimes be attributed to unclear instructions or instructions which do not convey what must be done. Doing something right the first time is a culture that seems to be lacking in businesses today. This is evidenced by reports of product recalls along with customer returns costing companies money and damages their reputation with consumers. The costs of running a business can be high especially in some industries but that costs can be reduced by reducing the potential for reworking products not meeting established standards. Another benefit if this principle were to be practiced in every business is a boom to the economy. When businesses make more and better products their profit increases by reduced costs and a potential increase in customers who are happy with the products or services.
Doing Things Right the First Time is a philosophy, a mentality, and a performance standard.
It’s a practical measure against which any system; process, action, or outcome can be analysed. It’s important to note that focusing on how you can do everything right the first time does NOT mean that you are trying to perfect. It means that you are changing your perspective on the “How” part of your job and improving your overall performance. To accomplish this feet, you must demand that the following three things to take place: •Recognise the high cost of mistakes and quality issues.
•Continuously think of the places where flaws occur in your performance. •Work proactively to address the flaws in your systems and behaviours so that quality performances take place. Basic requirements for DIRTFT
Doing it right the first time and every time refers to every activity in the organisation. For this concept to work management has to make sure they do everything right from the goal setting, to recruitment of the right personnel, establish the right processes, choose the right materials and choosing the right machinery and equipment to use. Top management also has a duty to define the requirements for each employee. Each employee has to fully understand their role in the organisation and they are supposed to accomplish their duties, if instructions are not clearly spelt out defects will be found in the final product. The resources of achieving the requirements have to be available for the concept to be fruitful in any organisation. Employees need to be motivated all the time without motivation they will produce goods with a lot of defects thus costing the organisation. Set right Goals
It is essential to set the right goals and objective.
The Attitude of Do It Right the First Time
Have you ever had an employee say something along the lines of “Hey, I just do what I’m told and keep my head down and my mouth shut.” Do It Right the First Time does not even enter this picture. Creating an atmosphere where employees feel free to speak up when they see a problem or have a question is the first step in creating an atmosphere that supports “Do It Right the First Time.” In today’s economy with high unemployment, management must work overtime to make sure the negative attitude does not invade their facility. What are you doing to make sure your company employees have an attitude to “Do It Right the First Time”. •Management must make clear where it stands on quality.
Without top management commitment the process is doomed to failure. Top management must communicate it has a zero defect strategy if it wants a quality improvement process. The primary action to accomplish this is to write and communicate a Quality Policy. Either management is on-board with a Quality Improvement Process or they are not. If management is involved in providing resources and determining which projects have what priority than the company is on the right road for a successful Quality Improvement Process. •A framework is needed to coordinate the quality improvement process which is driven by the quality improvement team. This is the vehicle to remove roadblocks to progress and provides a formal communications medium to ensure the quality improvement efforts are coordinated throughout the company. Each department should have a representative on the team and a charter is needed. •Keep the Quality Improvement Process Serious, but Fun
This is people’s livelihoods on the line. Do this wrong and jobs are going away, most likely yours will be one of the first to go. Select serious issues but be willing to let team members be spontaneous and open. Sometimes the only way to create that spark in a quality improvement process is with a little humour.
•Allowing the Quality Improvement Process to Become a Motivational Program
When the Quality Improvement Process goes from creating real and lasting preventive measures and becomes a method to “get the employees involve” or create “caring” in the employees it will fail. Employees will see through the rhetoric and realize management is not serious or interested. The expectation is the employees will change in some way rather than the system.
•Focusing the Quality Improvement Process not only on operations Operations makes the products that get sold but the cause of non-conformances can occur in order entry, purchasing, engineering, logistics that is any area of the company. The whole system must be controlled to be effective. The entire process must be looked at, not just the area where they manufacture a saleable product.