The Rise and Fall of Levi Strauss & Co.
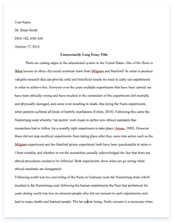
- Pages: 4
- Word count: 911
- Category: Employment Weakness
A limited time offer! Get a custom sample essay written according to your requirements urgent 3h delivery guaranteed
Order NowThe ultimate demise of Levi Jeans Company came long before the announcement was made on the closing of eleven of its US factories, ending the jobs of over 6,000 employees–many of which had been long term. Although many manufacturing type businesses are notorious for their “slave labor wages” and less than reputable working conditions, Levi’s Strauss broke the mold by maintaining its character of always treating its workforce fair and employees as valued. The company was ranked in many polls and by numerous magazines as one of the best to work for.
What led to the downfall? Most say that it was the abandonment of the old piecework system in 1992. Under the old system, an employee did one dedicated task such as sewing buttons or zippers. The worker was paid according to the amount of individual work completed. Unfortunately, the recurring tasks showed increases in “repetitive-stress injuries”, for example, carpel tunnel syndrome. At this point came the birth of the ‘work group method’, which the company saw as more productive. The idea of teamwork seemed profitable for Levi’sUS based factories whose competition was already turning to the overseas markets to cut costs on labor. It was obviously more economical for them to hire a seamstress at several dollars a day (overseas) as opposed to having to pay hourly wages stateside. “Teamwork is the basis for solving frustrating and costly workplace problems, such as high stress, unsolved conflicts, low job satisfaction, and high turnover”, says Steve Carney, the author of The Teamwork Chronicles. The idea backfired on Levi’s and inevitably turned the workers against their counterparts.
The buddy teams worked as long as you had an entire team of experienced, top performers. But predictably, “longtime friendships were dissolved as faster workers tried to banish slower ones.” (King, 1998) Morale took a plunge when the skilled and faster team workers began seeing their paychecks take a nosedive. Veteran employees were upset at the fact that they had to make up the work when an absent or less experienced team member slowed them down–all for lower pay. Physical altercations took place between those employees who felt that other workers on their team were not pulling their weight.
Even after hiring a consulting firm, Sibson & Co., to analyze all the issues that were being brought about from the corporate-wide changes, they were told to “start from scratch”. Basically revamp the whole system–from the day-to-day processing to the pay scale used. “Teams created pressures and tensions and a lot of unhappiness,” says Levi’s CEO, Robert Haas. (King, 1998) It’s definitely not for everyone. For the most part the remaining factories are going back to the old ways of doing business.
You have heard the old saying, “Good things come in small packages”. Maybe in this case, if Levi’s is so intent on work groups, the groups should be smaller. Its easier for a group of five people to get along as opposed to thirty-five. Having larger groups working together affords to opportunity for small groups within it to get together and ‘gang-up’ on the weakest links, which is what is trying to be avoided.
In the Army we learned that you are only as strong as your weakest person. This is ‘fine and dandy’ because we are all getting the paycheck we have earned in regards to our rank. It does not matter if ‘Soldier X’ does not feel like putting in 100% today. Leadership roles are also determined by rank, so there is little to no question as to who is in charge. With the circumstances of the Levi’s company, many factors come into play. Questions such as ‘Who is the leader of the group? Is it the senior person? The fastest working person? How is each person evaluated? Who evaluates them? How are task assignments to be divided up? Voluntarily or by discussion? Are critical tasks being fulfilled?
Another recommendation would be for the teams to be ‘evenly distributed’, if possible. For the most part, staff still working at the plants were veteran employees. Good managers should already be aware of their employees’ strengths and weaknesses, and be able to play them to their advantage. Maybe even put one strong seamstress with one weaker one on a team. The weaker one could learn from the other. The team is still making their quotas and learning from one another also.
Is there one complete and full proof answer the Levi’s company could have used to avoid the downsizing from happening? Probably not. They were more concerned in exhausting all other efforts and keeping their US workers employed before “having” to take the business overseas. When the inevitable happened, they offered the employees the best severance packages in history and offered to pay to retrain them to go back into the workforce pot. Even at the loss of millions of dollars, this is by far still a commendable company.
Works Cited:
Carney, Steve. “The Teamwork Chronicles and The Power of We.”
http://www.powerofwe.com/
King, Ralph T. “Jeans Therapy: Levi’sFactory Workers are Assigned to
Teams, And Morale Takes a Hit.” Wall Street Journal. May 20, 1998.
Lester, Richard K. “Companies That Listen to Their Innervoices.”
Technology Review. May/June 1998.
“People Process Management.” http://www.netwise.ac.uk/CMS/teach
people.html
Shoulberg, Warren. “Levi Stress.” Home Textiles Today. Mar 8, 1999.
“Surviving the Group Project: A Note on Working in Teams.” http://
web.cba.neu.edu/~ewertheim/teams/ovrvw2.ht