Supercritical Carbon Dioxide as a Green Solvent
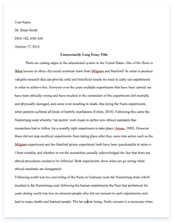
- Pages: 11
- Word count: 2656
- Category: Coffee
A limited time offer! Get a custom sample essay written according to your requirements urgent 3h delivery guaranteed
Order NowThe majority of chemical processes in chemical synthesis are carried out in solution and organic solvents usually are the first choice. To satisfy this demand, 15 billion kilograms of organic are produced worldwide each year. [1] These solvents often bear considerable risk due to their toxicity, flammability or environmental hazards. Furthermore, they have to be separated from the products and recycled or disposed at the end of the process, increasing the overall production cost. Although they play a valuable role, organic solvents are responsible for significant air, soil and water pollution. One important effort in the development of environmentally friendly chemical processes is the reduction of solvent use through the development of solvent-free processes and more efficient recycling protocols. Since most of these approaches necessitate a pollution prevention program the replacement of organic solvents by environmentally benign reaction media is preferred. Ionic liquids, fluorous biphase systems and water are currently being studied as solvent alternatives. Another actively studied alternative is supercritical carbon dioxide (spCO2). All have potential benefits and disadvantages that need to be considered. [13]
Although supercritical fluids are known since the discovery of the critical temperature 175 years ago, their use as reaction media for organic synthesis emerged only during the last 1015 years. Especially the use of scCO2 as a solvent for selective extraction and synthesis processes attracts considerable interest. Not only is scCO2 used in diverse areas as dry cleaning, dying of fabrics and polymers, metal degreasing and material processing, its application in food chemistry is nowadays even more established. The main commercial example is the production of decaffeinated coffee. [4] This paper aims to analyze the use of scCO2 as a decaffeinating agent for coffee beans and solvent for the synthesis of fluoropolymers. The benefits and disadvantages of scCO2 will be outlined and a comparison to previously used methods will be made.
1. Supercritical Carbon Dioxide
Figure 1 shows the phase diagram of pure carbon dioxide. At 31.0 °C and 73.75 bar the endpoint on the evaporation line is reached. Beyond this critical point, no distinct liquid or vapor phase is observed and the new supercritical phase exhibits properties that are reminiscent of both states. The favorable diffusivity of a gas is combined with the increased density of a liquid. Due to these unique properties scCO2 is an ideal solvent for many applications. [5]
Figure 1. Phase diagram of pure CO2
General advantages and disadvantages associated with the use of scCO2 [5]: Advantages: ⢠⢠⢠⢠Non-explosive, non-flammable, non-corrosive, relatively non-toxic (significant safety advantage). CO2 is naturally abundant.1 Excellent heat transport capacities: removal of heat from exothermic reactions, avoiding hot spots. Inert towards oxidation, excluding any formation of byproducts from oxidation of the solvent. If CO2 can be withdrawn from the environment, employed in a process, then returned to the environment ācleanā, no environmental detriment occurs. However, most of the CO2 employed in processes today is collected from the effluent of ammonia plants or derived from naturally occurring deposits. Ultimately, one should consider the source of CO2 used in a process in order to judge the sustainability of the process. [5]
Simplified work-up procedures. Reduce of organic and hazardous wastes. No residual CO2 after synthesis and processing.
Disadvantages: ⢠⢠⢠⢠High critical pressure. The relatively high energy cost involved in generating and recirculating supercritical CO2. The hazards and costs of high-pressure equipment. The potential damage to the ozone layer.
3. Extraction of Caffeine from Coffee Beans
Caffeine is an alkaloid that is naturally found in coffee beans and tea and is often added to soda and energy drinks. Other commonly known alkaloids are nicotine, cocaine, morphine and codeine. Caffeine is of major importance with respect to the physiological properties of coffee and determines the bitter character. The estimated global annual consumption of caffeine is 120 000 tones, making it the most widely used psychoactive substance in the world. It stimulates the central nervous system, having the effect of temporarily restoring alertness. The caffeine content of coffee beans varies from 1.0 to 2.5% and a typical cup of regular coffee contains 70-140 mg of caffeine depending on the preparation, blend an cup size. [4] Drinking coffee is usually associated with sleepiness, nervousness, intestinal discomfort, heart stimulation and increase of blood pressure, resulting in a serious increase of the demand for decaffeinated coffee products. In the last decade the number of decaffeinated coffee consumers has grown more than 4- to 5-fold. Therefore, 20% of the worldās coffee production needs to be decaffeinated.
In the history of decaffeination benzene, chloroform, ethyl ether, ethanol, trichloroethylene, acetone, ⦠have all been used to decaffeinate beans. Because of obvious health, safety and environmental reasons, solvent based decaffeination using the above mentioned extraction media has been banned. Until the mid-1970ās dichloromethane (DCM) was considered to the best solvent for the extraction of caffeine. Its low boiling point and low vapor flammability contributed to the success of DCM. However the negative effects of DCM on both human health and the environment as well as its contribution to the depletion of the ozone layer obliged the coffee industry to put a stop to the use of DCM. The manufacture, transport and use present a risk to the environment. The search for a solvent free from toxicity criticism continued. Ethyl acetate (EA), an ester naturally occurring in many fruits such as bananas and apples became the solvent of choice. Because it is completely digestible and consumed daily in a wide range of foods its toxicity has never been questioned by the FDA.
Even though EA is less toxic and environmentally more friendly than DCM, scCO2 and āSwiss Waterā extraction are nowadays preferred over EA extraction. In general, the process of decaffeination using carbon dioxide can be described as follows. It begins with mixing the coffee beans with water to bring the moisture content to about 50%. The beans swell, pores open and caffeine is converted into a mobile form that can diffuse out of the bean. The moisturizing step is essential for decaffeination. The swollen beans are loaded into a thick-walled stainless steel extractor. Liquid carbon dioxide is pumped in at the operating pressure of about 300 atm and is heated to about 338 K. As can be seen from Figure 1, CO2 behaves as a supercritical fluid. After the system is filled, carbon dioxide is recirculated between the extractor and the scrubber. Carbon dioxide flowing through the extractor dissolves caffeine. In the scrubber, caffeine is removed from carbon dioxide using water. Manipulating the carbon dioxide to water ratio is the key factor of the entire setup. In the extractor there is a high ratio of carbon dioxide to water, while in the scrubber water this ratio is lowered by adding water.
The scrubber water preferentially carries away the caffeine. The recirculation is repeated for 8-12 hours depending on the initial caffeine content. At the end of the recirculation, carbon dioxide is pumped from the system to a strong tank and is recycled. The beans are unloaded for drying. The subsequent drying reduces the moisture to its original level and vaporizes the carbon dioxide. [4] Carbon dioxide is the most commonly used supercritical fluid in food applications. It is not only cheap and readily available at high purity, but also relatively safe (non-flammable, noncorrosive, non-explosive and non-toxic) to handle. Furthermore, it can be easily removed by simple expansion to environmental pressure values. When being recycled it does not contribute to the environmental CO2-problem. Because of the insolubility of mineral salts and high molecular weight compounds such as proteins, and polysaccharides, scCO2 extraction of caffeine is the most selective method. All essential flavor and aroma elements remain unaffected in the coffee bean.
Itās a colorless, odorless and tasteless gas that gives no solvent residue. On the other hand, decaffeination plants using scCO2 are only commercially feasible at an annual capacity of at least 3000 tons because of the high start-up cost. The use of scCO2 does not only require the use of expensive high-pressure equipment, but also results in an energy demand for generating and recirculating the extraction āsolventā. In addition, more safety precautions need to be considered. But isnāt the greenest solution to use no āsolventā at all? Indeed, in 2004 Silvarolla et al discovered a naturally decaffeinated Coffea Arabica plant from Ethiopia, a species recognized for the high quality of its beans. Coffea Arabica is the most cultivated and consumed coffee in the world and has an average caffeine content of 12 mg g-1. This newly discovered plant however contains only 0.76 mg g-1. Silvarolla et al concluded that the naturally low caffeine content is due to a mutation of the caffeine synthase gene. [6] In addition genetic engineering studies resulted in the knock out of the gene encoding for theobromine synthase, an enzyme involved in caffeine biosynthesis in coffee plants. As a result the caffeine content is reduced up to 70%. [7] But will the consumer buy decaffeinated coffee cultivated from genetically modified plants?
4. Synthesis of Fluoropolymers
Fluoropolymers have many technical applications in the form of lubricants or coatings. They are generally insoluble in most conventional organic solvents and traditionally their synthesis and processing have relied on the use of chlorofluorocarbon (CFC) solvents2 which have been identified as one of the main causes of depletion of the ozone layer. [8] Because of their unreactivity and therefore extremely high life span up to 100 years, CFCās were mainly used as refrigerants, propellants and solvents. The ability to quench flame propagation resulted in numerous applications such as flame retardants and fire extinguishants. Nevertheless, after it Fluoropolymers are typically synthesized in aqueous polymerization systems (both emulsion and suspension), non-aqueous systems (Freon-113), or in hybrid Freon-113/aqueous hybrid systems. Such processes require the use of large quantities of water, CFCs (for non-aqueous polymerizations), and fluorinated surfactants for emulsion polymerization.
Was proven that CFCs are responsible for the decomposition of the ozone layer, their use was banned or strictly regulated. UV radiation homolytically breaks off the chlorine atom producing highly reactive chlorine radicals which catalyze the conversion of ozone into oxygen. New processes that limit the use or replace CFCs by environmentally friendly chemicals were needed. Perfluorocarbons, hydrofluorocarbons, perfluoroalkyl sulfides and perfluorinated cyclic amines were proposed as alternative solvents in the manufacture of nonaqueous fluoropolymers. Due to the high cost and commercial unavailability their potential use on an industrial level for bulk chemical synthesis was abandoned. [10] Because of the high solubility of many fluoropolymers in liquid and supercritical CO2, the possible use of scCO2 as a reaction medium for synthesizing and processing fluoropolymers was investigated. [11]
A close collaboration between the University of North Carolina at Chapel Hill and DuPont (Fayetteville, USA) eventually lead to commercialization of certain grades of TeflonĀ® products based on CO2 technology, which have superior properties to those manufactured by conventional methods. The process employs CO2 as the continuous phase instead of 1,1,2-trichloro-1,2,2-trifluoroethane or water and surfactant. This was the first commercial example of polymerization in scCO2. [9] Most commercially available fluoropolymers are prepared from a relatively small group of olefins including tetrafluoroethylene (TFE), chlorotrifluoroethylene (CTFE), vinylidene fluoride (VF2), hexafluoropropylene (HFP), ethylene, and perfluoroalkyl vinyl ethers (PAVEās). Many of these monomers are flammable and some are explosive. Specific problems related to TFE are: [9,12]
Flammable when mixed with air. High propensity for explosion during expansion to a gas from its liquid phase under pressure. Highly explosive as a gas at elevated temperatures. Exothermic auto polymerization in the presence of oxygen (explosion risk). Copolymers of TFE with HFP or PAVEās exhibit high levels of carboxylic acid end groups, changing the polymer properties and complicating post-polymerization steps.
Researchers at DuPont discovered that TFE can be handled more safely as a mixture with CO2. In the presence of sufficient CO2, TFE does not form explosive mixtures with air. [13] In addition to the much safer handling, transporting and stocking conditions, no large amount of HCl is needed3. Because CO2 is also the reaction medium for polymerization, the removal of the stocking agent is unnecessary. This seriously reduces waste treatment and energy costs. One of the main advantages of using scCO2 as a solvent is its inertness to free radical chemistry. [11] No chain transfer to the solvent during free radical initiated polymerization can occur. Chain transfer to the solvent typically results in lower molecular weights chains and a decrease of the polymerization rate. Indeed, for certain type of materials synthesized in scCO2 it is necessary to add chain transfer agents to control molecular weight and maintain melting processability of the product. [9]
Additionally, the content of acid end groups is an order of magnitude lower than that for fluoropolymers synthesized in conventional organic and aqueous reaction systems. The efficient transport (due to the low viscosity of scCO2) of monomer units into the polymer phase, maintaining high concentrations of monomer in the vicinity of the active chain ends, favors bimolecular propagation over unimolecular βscission (Figure 2)4. Furthermore, the low temperature that one can use with CO2 is beneficial for cross polymerization. Polymers containing high levels of acid end groups require expensive high-temperature hydrolysis and fluorination steps. [9]
Figure 2. β-scission in fluoroolefin polymerization.
Previously TFE was handled as a liquid azeotrope mixture with HCl (33 mol% TFE and 67% HCl) before polymerization. However, the disposal of the large amount of HCl and the toxicity potential of shipping the acid was a disadvantage. [14] 4 spCO2 is in general a good solvent for diffusion controlled reaction.
Such modifications are necessary since under the extreme conditions which are required to melt process fluoropolymers, these end groups can decompose to form bubbles, discolorations and molecular weight changes in the final product. Additional benefits when scCO2 is used are the direct isolation of the product from the reactor and the purity of the end product: no contamination from solvents or surfactants occurred. Obviously working with scCO2 means significant capital investment in costly high-pressure equipment and benefits from simplified work-up procedures and savings through elimination of organic and hazardous wastes. The commercialization of TeflonĀ® based materials by DuPont is clear evidence that the balance is on the side of scCO2. Nowadays nearly all fluoropolymers are manufactured using an aqueous emulsion or suspension polymerization process. This type of technology requires the application of fluorinated surfactants such a perfluorooctanic acid (PFOA). Many of these surfactants are currently under scrutiny due to bioaccumulation and environmental persistence. Since the polymerization of fluoroolefins in scCO2 does not require surfactants, both the academic and industrial world are confident that scCO2 will become the solvent of choice for the synthesis of fluoropolymers.
5. Bibliography
[1] Desimone, J. M. Science 2002, 297, 799. [2] Clark, J.; Macquarrie, D. Handbook of Green Chemistry and Technology Blackwell Publishing, Oxford, Great Britain, 2002. [3] Jenck, J. F.; Agterberg, F.; Droescher, M. J. Green. Chem. 2004, 6, 544. [4] Ramalakshmi, K., Raghavan, B. Crit. Rev. Food Sci. Nutr. 1999, 39, 441. [5] Beckman, E. J. J. Supercritical Fluids, 2004, 28, 121. [6] Silvarolla, M. B.; Mazzafera, P.; Fazuoli, L. C. Nature 2004, 429, 826. [7] Ogita, S.; Uefuji, H.; Yamaguchi, Y.; Koizumi, N.; Sano, H. Nature, 2003, 423, 823. [8] Solomon, S.; Garcia, R. R.; Sherwood, F.; Wuebbles, D. J. Nature, 1986, 321, 755. [9] Wood, C. D.; Cooper, A. I.; DeSimone, J. M. Curr. Opin. Sol. Stat. Mater. Sci. 2004, 8, 325. [10] Romack, T. J.; DeSimone, J. M.; Treat, T. A. Macromolecules 1995, 28, 8429. [11] DeSimone, J. M.; Guan, Z.; Elsbernd, C. S. Science 1992, 257, 945. [12] Romack, T. J.; Combes, J. R.; DeSimone, J. M. Macromolecules 1995, 28, 1724. [13] Van Bramer, D. J.; Shiflett, M. B.; Yokozeki, A. Safe Handling of Tetrafluoroethylene. US Patent 5 345 013, 1993. [14] Du, L.; Kelly, J. Y.; Roberts, G. W.; DeSimone, J. M. J. Supercrit. Fluids 2009, 47, 447.