Reverse Logistics
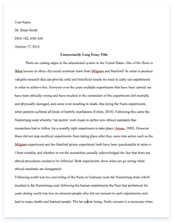
- Pages: 4
- Word count: 958
- Category: Logistics
A limited time offer! Get a custom sample essay written according to your requirements urgent 3h delivery guaranteed
Order NowReverse logistics stands for all operations related to the reuse of products and materials. It is “the process of planning, implementing, and controlling the efficient, cost effective flow of raw materials, in-process inventory, finished goods and related information from the point of consumption to the point of origin for the purpose of recapturing value or proper disposal. More precisely, reverse logistics is the process of moving goods from their typical final destination for the purpose of capturing value, or proper disposal. Remanufacturing and refurbishing activities also may be included in the definition of reverse logistics.”
The reverse logistics process includes the management and the sale of surplus as well as returned equipment and machines from the hardware leasing business. Normally, logistics deal with events that bring the product towards the customer. In the case of reverse logistics, the resource goes at least one step back in the supply chain. For instance, goods move from the customer to the distributor or to the manufacturer. Let’s look at an example; a manufacturer produces product A which moves through the supply chain network reaching the distributor or customer.
Any process or management after the sale of product A involves Reverse Logistics. If product A happened to be defective the customer would return the product. The manufacturing firm would then have to organise shipping of the defective product, testing the product, dismantling, repairing, recycling or disposing the product. Product A will travel in reverse through the supply chain network in order to retain any use from the defective product. This is what reverse logistics is about.
Business implications
In today’s marketplace, many retailers treat merchandise returns as individual, disjointed transactions. “The challenge for retailers and vendors is to process returns at a proficiency level that allows quick, efficient and cost-effective collection and return of merchandise. Customer requirements facilitate demand for a high standard of service that includes accuracy and timeliness. It’s the logistic company’s responsibility to shorten the link from return origination to the time of resell. By following returns management best practices, retailers can achieve a returns process that addresses both the operational and customer retention issues associated with merchandise returns.
Further, because of the connection between reverse logistics and customer retention, it has become a key component within Service Lifecycle Management (SLM), a business strategy aimed at retaining customers by bundling even more coordination of a company’s services data together to achieve greater efficiency in its operations. Reverse logistics is more than just returns management; it is “activities related to returns avoidance, gate keeping, disposal and all other after-market supply chain issues”.
Returns management – increasingly being recognized as affecting competitive positioning – provides an important link between marketing and logistics. The broad nature of its cross-functional impact suggests that firms would benefit by improving internal integration efforts. In particular, a firm’s ability to react to and plan for the influence of external factors on the returns management process is improved by such internal integration. Third-party logistics providers see that up to 7% of an enterprise’s gross sales are captured by return costs. Almost all reverse logistics contracts are customized to fit the size and type of company contracting. The 3PL’s themselves realize 12% to 15% profits on this business.
————————————————-
“Studies have shown that an average of 4% to 6% of all retail purchases are returned, costing the industry about $40 b return of unsold goods. In certain industries, goods are distributed to downstream members in the supply chain with the understanding that the goods may be returned for credit if they are not sold. Newspapers and magazines serve as examples. This acts as an incentive for downstream members to carry more stock, because the risk of obsolescence is borne by the upstream supply chain members. However, there is also a distinct risk attached to this logistics concept.
The downstream member in the supply chain might exploit the situation by ordering more stock than is required and returning large volumes. In this way, the downstream partner is able to offer high level of service without carrying the risks associated with large inventories. The supplier effectively finances the inventory for the downstream member. It is therefore important to analyze customers’ accounts for hidden costs.
Refusal of the products in the cash on delivery process (COD) In case of e-commerce business, many websites offer the flexibility of Cash on delivery (COD) to the customer. Sometimes customer refuses the product at the time of delivery, as there is no commitment to take the product. Then the logistic service providers do follows the process of “Reverse logistics” on the refused cargo. It is also known as Return to origin (RTO).In this process the e-commerce company adds the refused cargo to its inventory stock again, after proper quality checks as per the company’s rules.
REFERENCE
1. ^ Hawks, Karen. VP Supply Chain Practice, Navesink. Reverse Logistics Magazine Winter/Spring (2006). http://www.rlmagazine.com/edition01p12.php 2. ^ Rengel, P. & Seydl, C. (May 2002). Completing the Supply Chain Model. Retrieved on 2008-04-25. 3. ^ Harrington, Ryan, VP & GM for Reverse Logistics / Projects, NYK Logistics. Reverse Logistics Magazine. Winter/Spring (2006). http://www.rlmagazine.com/edition01p14.php 4. ^ Greer, 2004
5. ^ Rogers, 2002
6. ^ Mollenkopf D., Russo I. and R. Frankel, «International Journal Physical Distribution Logistics Management» , vol. 37 , n. 7 , 2007 , pp. 568-592 “The returns management process in supply chain strategy”. Retrieved 2008-05-05. 7. ^ “Reverse side of logistics: The business of returns”. Forbes. 2005-11-03. Retrieved 2008-03-14. 8. ^ Tom Van Riper for Forbes Magazine / Reseller Sees Many Happy Returns (December 2005). http://www.forbes.com/2005/12/06/retailing-wal-mart-cx_tvr_1207reselling.html 9. ^ Business Logistics & management – theory and practice – JJ Vogt, Wj Pienaar, PWC de Wit – OXFORD 2002. p236