Presentation on Total quality management in Gillette Argentina
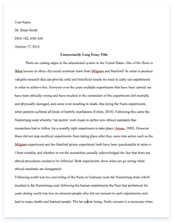
- Pages: 5
- Word count: 1038
- Category: Argentina Business Management Qualities
A limited time offer! Get a custom sample essay written according to your requirements urgent 3h delivery guaranteed
Order NowBACKGROUND Founded in 1901 & by 1905 had started operations abroad Sales office in London & manufacturing site in Paris Best known for its razors and blades Leader in batteries (Duracell), dental care(Oral-B) and toiletries (Gillette Series) Top seller of writing products (Paper mate and Parker pen) and electric shavers
PowerPoint Presentation:
Manufacturing operations in 20 countries & distribute products in 200 territories 1.2 billion people around the world used Gillette products every day
GILLETTE IN ARGENTINA:
GILLETTE IN ARGENTINA Gillette opened operations in Argentina after World War 1 Company early presence in Argentina allowed it to remain and grow, while other competitors fled from the country’s political and economic instability In late 1980 country suffer from regular inflation & scarcity and Gillette found a whole new way of managing the business Sophisticated hedging of dollars, buying and selling at appropriate times and meant communicating almost daily with key suppliers Gillette Argentina never fail to deliver a profit to headquarters, with the exception of 1989
QUALITY COMES IN TO FOCUS:
QUALITY COMES IN TO FOCUS Argentina started to focus on quality in 1980, with Carlos Rotundo, director of manufacturing and logistics Uses cross functional teams to achieve better efficiencies Gillette management team began to take stock of the significant changes occurring within their business environment As trade barrier were coming down, they realized that to survive within this new environment, they turned to TQM Michael Sharp, the HR director for Gillette, investigated a number of consultant on TQM and hire Organizational Dynamics Inc. (ODI) as the consulting firm to help Gillette implement quality principles
GETTING SERIOUS ABOUT QUALITY:
GETTING SERIOUS ABOUT QUALITY ODI developed the quality initiative for Gillette Initiative was based on customer focus, total participation, systematic support of the effort, measurement of results, and continuous improvement ODI recommended creating a quality structure, consist of : Quality council Steering committee Quality director Quality Action Team (QAT) for achieving wide participation in total quality programs
PowerPoint Presentation:
In 1992, Mexico introduced a program for TQM that involved one to one contracts between individuals working interdependently Argentina started applying both the ODI approach with team as well as the contract approach QAT employees received specialized training in four-phase problem solving process, called FADE 1. Focus – development of a problem statement 2. Analyze – use of data to understand the magnitude of the problem 3. Develop –determination of solution & implementation plan 4. Execute – implementation of the plan and measurement of its impact
PowerPoint Presentation:
QAT members were trained in basic quality tools, brainstorming, force field analysis and cost-benefit analysis Teams were assigned facilitators who were trained as team leaders Team leader received formal training in areas relating to group dynamics, leadership skills, effective meetings, and group conflict One-to-one contract system successfully introduced in Mexico and produced 10000 contracts within 1 st few years of operation Argentina, Colombia and Chile began its implementation soon after Mexico
Gillette Argentina, a new TQM approach :
Gillette Argentina, a new TQM approach In dec 1993 victor walker appointed as a total quality manager along with Carlos Rotundo as a program director. Investigation of complaints about contract approach to quality. Action team approach towards quality. That approach help them to remove unnecessary departmental barrier and selfish approach. This is called new Gillette Argentina TQM approach.
Meeting the challenges of quality:
Meeting the challenges of quality After forming the quality team the steering committee turns its attention to the factors like full support of management , increasing participation, execution of objectives and sustaining of momentum. victor walker tries to win the support of all his operating committees for the implication of TQM. Quality council and steering committee which consist the cross functional managers played an important role in implication of TQM program.
PowerPoint Presentation:
As a result of implication of TQM program people start in participating in the quality improvement. In starting of that program the people of sales department supporting least. Without the participation of sales department implication of TQM is not possible because main motive of implication of TQM is customer satisfaction. After nine months and several discussions with sales manger now sales department starting to participating in TQM program.
Implication of TQM:
Implication of TQM In first step steering committee sets the annual objectives for the TQM program. After that quality action teams shows how these objectives helps in improving outcomes. In last quality action team presented the benefits to operating teams. For sustaining the momentum of TQM walker initiated two new aspects – Annual performance appraisal Special recognition program called quality stars.
Outcomes of TQM:
Outcomes of TQM Increase in participation of employees. Creation of teamwork climate. More focus on customer satisfaction. Change in work culture. A survey is operated to measure the customer satisfaction level also shows that customer satisfaction level increases.
PowerPoint Presentation:
Some of the financial benefits like – Annual sales grows by 19% in between 1993to 1998. Average profit growth was 22% for same period. Increase in rate of inventory turnover. Operating expenses decreased by 40%. ROA increased by 60% Total benefit of TQM is about $17.8 millions for same period.
CONCLUSION:
CONCLUSION Quality was thriving as a business process in Gillette Argentina but in other parts of the country is works as a driving force. According to Bob King – TQM was not a particular concept in Gillette Argentina, TQM was faded as per the business philosophy. Although he also thought that TQM have some benefits.
PowerPoint Presentation:
According to Mike Sharp – TQM had became a outmoded phase. Although he supported the basics of TQM like- Working as a team Mapping Continues improvement
PowerPoint Presentation:
Both King and Sharp supports Micozzi and expected from him to continue to spread the world again. They also thought that – although the initiative was once dying and in some Latin American subsidiaries quality initiative had never really taken hold. But they support the fact that in Latin America things are rapidly change and there is a great opportunity for companies that put the customer first.
PowerPoint Presentation:
Words of Micozzi “ Call it the way you want, but without teamwork and customer focus, you are bound to fail, now or back then in 1993.”