Preparation of Detergents
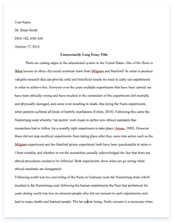
- Pages: 13
- Word count: 3234
- Category: Water
A limited time offer! Get a custom sample essay written according to your requirements urgent 3h delivery guaranteed
Order NowIf you look up detergent in a dictionary it is simply defined as cleaning agent. During the last two to three decades, however, the word detergent has tended to imply synthetic detergent, or syndet for short, rather than the older soap. In fact, commercial formulations consist of a number of components, and we shall use the term surface-active agent, or it’s abbreviation surfactant, to describe the special active ingredients that give detergents their unusual properties. Synthetic detergents dissolve or tend to dissolve in water or other solvents. To enable them to do this, they require distinct chemical characteristics. Hydrophilic (water loving) groupings in their molecular structure, and hydrophobic (water hating) groupings, help the detergent in it’s “detergency” action. The first soaps were manufactured in ancient times through a variety of methods, most commonly by boiling fats and ashes. Archaeologists excavating sites in ancient Babylon have found evidence indicating that such soaps were used as far back as 2800 B.C.
In Europe, the use of soap declined during the Middle Ages. However, by the fifteenth century, its use and manufacture had resumed, and an olive-oil based soap produced in Castile, Spain, was being sold in many parts of the known world. Castile soap, which is still available today, has retained its reputation as a high-quality product. During the colonial period and the eighteenth century, Americans made their own soap at home, where most continued to produce it until soap manufacture shifted away from individual homes to become an industry during the 1930s. The first detergent, or artificial soap, was produced in Germany during World War I. In 1946, the first built detergent appeared, comprising a surfactant (a surface-acting agent or soap) and a builder (a chemical that enhances the performance of the surfactant as well as rendering the laundering process more effective in other ways). Pushed along by economic prosperity and the development of relatively inexpensive washing machines in the wake of World War II, detergent sales soared; by 1953, they had surpassed soap sales in the United States.
CLASSIFICATION OF SYNTHETIC DETERGENTS
Detergents are classified as either:
* Anionic: negatively charged head
* Cationic: positively charged head
* Non-ionic or neutral: uncharged head
Class| Example| Chemical Properties| Uses|
Anionic| CH3(CH2)11OSO3-Na+
sodium dodecyl sulfate| Usually contain either
a sulfate (SO4) head| widely used due to cost and performance – laundry detergents
-dishwashing liquids-oven cleaners|
| CH3(CH2)11C6H4SO3-Na+
sodium dodecylbenzenesulfonate| or  a sulfonate (SO3) head| |
Cationic| CH3(CH2)11NH3+Cl-
dodecylamine hydrochlorideCH3(CH2)15N(CH3)3+Br-
hexadecyltrimethylammonium bromide| Usually contain a modified ammonium ion as active site which produces a germicidal action. More expensive than anionic detergents.| -cleaning plastics -hair shampoos
-nappy washes
-fabric softeners and conditioners|
Non-ionic
or neutral| CH3(CH2)14COOCH2C(CH2OH)3
pentaerythrityl palmitate| Contains polar parts, eg, OH groups, to provide water solubility. No ionic groups so no reaction in hard water.
Low lathering prevents foam build up in dishwashers.| -car shampoos -dishwasher detergents
-cosmetics|
Anionic Detergents
A class of detergents having a negatively charged surface-active ion, such as sodium alkyl benzene sulfonate Neutral or non-ionic detergents:
Non-ionic detergents are used in dish washing liquids. Since the detergent does not have any ionic groups, it does not react with hard water
ions. In addition, nonionic detergents foam less than ionic detergents. The detergent molecules must have some polar parts to provide the necessary water solubility. Cationic Detergents:
Another class of detergents have a positive ionic charge and are called “cationic” detergents. In addition to being good cleansing agents, they also possess germicidal properties which makes them useful in hospitals. Most of these detergents are derivatives of ammonia. A cationic detergent is most likely to be found in a shampoo or clothes “rinse”. The purpose is to neutralize the static electrical charges from residual anionic (negative ions) detergent molecules. Since the negative charges repel each other, the positive cationic detergent neutralizes this charge. It may be surprising that it even works because the ammonium (+1) nitrogen is buried under the methyl groups as can be seen in the space filling model. In the graphic on the left, the polar part of the molecule consists of three alcohol groups and an ester group. The non-polar part is the usual long hydrocarbon chain Bile Salts – Intestinal Natural Detergents
Bile acids are produced in the liver and secreted in the intestine via the gall bladder. Bile acids are oxidation products of cholesterol. First the cholesterol is converted to the trihydroxy derivative containing three alcohol groups. The end of the alkane chain at C # 17 is converted into an acid, and finally the amino acid, glycine is bonded through an amide bond. The acid group on the glycine is converted to a salt. The bile salt is called sodiumglycoholate. Another salt can be made with a chemical called taurine. The main function of bile salts is to act as a soap or detergent in the digestive processes. The major action of a bile salt is to emulsify fats and oils into smaller droplets. The various enzymes can then break down the fats and oils. Amphoteric Detergents
These contain both acidic and basic groups in their molecule, and can act as cationic or anionic detergents, depending on the pH of the solution, or as both cation and anion.Amphoterics These have the characteristics of both anionic detergents and cationic fabric softeners. They tend to work best at neutral pH, and are found in shampoo’s, skin cleaners and carpet shampoo. They are very stable in strong acidic conditions and have found favour for use with hydrofluoric acid.
Key Concepts
* Synthetic detergents can be made from petrochemicals, fats and oils. * Synthetic detergent molecules, like soap molecules, generally consist of a hydrophilic head and a hydrophobic tail. * The hydrophobic, long hydrocarbon chain tail of the detergent molecule is attracted to particles of oil or grease by dispersion forces (Van der Waals or London or Weak Intermolecular Forces). * The hydrophilic, charged or polar head of the detergent molecule is attracted to water molecules. * Synthetic detergents are less sensitive to the effects of calcium and magnesium ions in hard water. * A number of additives are used to enhance the cleaning ability of detergents. * Branched-chain synthetic detergents are far less biodegradable than continuous-chain synthetic detergents.
Raw Materials
Although people commonly refer to laundry detergent as “soap,” it is actually a synthetic combination that functions much like soap, with certain major improvements. Soap cleans because each soap molecule consists of a hydrocarbon chain and a carboxylic group (fatty acids) that perform two important functions. The carboxylate end of the soap molecule is hydrophilic, meaning that it is attracted to water, while the hydrocarbon end of the molecule is both hydrophobic (repelled by water) and attracted to the oil and grease in dirt. While the hydrophobic end of a soap molecule attaches itself to dirt, the hydrophilic end attaches itself to water. The dirt attached to the carboxylate end of the molecule is chemically dragged away from the clothes being cleaned and into the wash water.
Properly agitating and rinsing the clothes furthers the cleansing process. The major difficulty with using soap to clean laundry shows up when it is used in hard water—water that is rich in natural minerals such as calcium, magnesium, iron, and manganese. When these chemicals react with soap, they form an insoluble curd called a precipitate. Difficult to rinse out, the precipitate leaves visible deposits on clothing and makes fabric feel stiff. Even water that is not especially hard will eventually produce precipitates over a period of time. While the hydrocarbons used in soap generally come from plants or animals, those used in detergent can be derived from crude oil. Adding sulfuric acid to the processed hydrocarbon produces a molecule similar to the fatty acids in soap. The addition of an alkali to the mixture creates a surfactant molecule
In the blender method of making powder laundry detergent, the ingredients—surfactant, builders, antiredeposition agents, and perfumes—are simply blended together in a mixer, released onto a conveyor belt, and packaged accordingly. This method is favored by smaller companies. that will not bond with the minerals in hard water, thus avoiding the accumulation of precipitates. In addition to a surfactant, modern detergent contains several other ingredients. Among the most significant are builders, chemicals which serve several purposes. Most importantly, they increase the efficiency of the surfactant. They also sequester minerals in hard water, meaning that they hold them in solution, preventing them from precipitating out. Furthermore, builders can emulsify oil and grease into tiny globules that can be washed away. Some, like sodium silicate, inhibit corrosion and help assure that the detergent will not damage a washing machine. Still other builders contribute to the chemical balance of the wash water, making sure that it conduces to effective washing.
Modern detergents have several other ingredients including antiredeposition agents, chemicals that help prevent soil from settling back on washed clothes. Fluorescent whitening agents are also common. By converting invisible ultraviolet light into visible blue light, these help to maintain brightness or whiteness. Oxygen bleaches such as sodium perborate improve the detergency of the mixture, especially in low-phosphate or no-phosphate products, as well as helping to remove some types of stains. Processing aids such as sodium sulfate are also used to prevent caking and to standardize product density. Enzymes and perfumes are also found in commercial detergents. Enzymes (a type of protein) break down some stains to make them easier to remove and are an essential ingredient in various pre-soak products used to treat heavily soiled clothes prior to laundering. Perfumes or fragrances cover the odour of the dirt and any chemical smell from the detergent itself. Suds control agents also have a role in detergents—too many suds can cause mechanical problems with a washing machine. The Manufacturing Process
IntroductionIn the mid-1970’s when the additive TAED for low temperature was introduced the wash temperature could be reduced to significantly without loss of performance, thus reducing the amount of energy consumed by households. In addition, there is now a significant trend towards tablets instead of powder. The beauty of the tablet format is the ability to offer an easy to handle product that contains the exact amount of ingredients to provide optimal results.The main environmental benefit is the substantial reduction of chemical disposal into waste water treatment while ensuring the best wash result. The exact formulation of each tablet is critical and dependent on the performance of the feeding device for each ingredient in the production line.End Products Since the end of the 80’s detergent compositions have been rich in technical developments: for example the introduction of compact (higher density) powders with activated bleach, color enhancers, the introduction of tablets and more recently capsules. There is also a trend towards the use of concentrated liquids.
Loss-in-weight feeders are mounted in carousel fashion. These units meter enzymes. Weigh belt feeders control the flow of detergent ingredients into the process. Other belt feeders are used as bulk flow meters. Detergent powders, tablets and capsules of different brands are generally packed in bags and boxes of different sizes. | Weigh Belt feeders control the flow of detergent ingredients into the process.Loss-in-weight feeders are mounted in carousel fashion. These units meter enzymes. | Although there are three ways of manufacturing dry laundry detergent, only two are commonly used today. In the blender process favored by smaller companies, the ingredients are mixed in large vats before being packaged. The machines used are very large: a common blender holds 4,000 pounds (1,816 kilograms) of mixed material, but the blenders can accommodate loads ranging from 500 to 10,000 pounds (227 to 4,540 kilograms). By industry standards, these are small batches for which the blender process is ideal.
While some settling may occur, the resulting detergent is of high quality and can compete with detergents made by other processes. The second commonly used method of production is called the agglomeration process. Unlike the blender process, it is continuous, which makes it the choice of very large detergent manufacturers. The agglomeration process can produce between 15,000 and 50,000 pounds (6,800 and 22,700 kilograms) of detergent per hour. In the third method, dry ingredients are blended in water before being dried with hot air. Although the resulting product is of high quality, the fuel costs and engineering problems associated with venting, reheating, and reusing the air have led to this method being largely replaced by agglomeration.
THE BLENDER PROCESS
* First, ingredients are loaded into one of two machines: a tumbling blender or a ribbon blender. The tumbling blender, shaped like a rectangular box, is turned and shaken from outside by a machine, while the ribbon blender is a cylinder fitted with blades to scrape and mix the ingredients. After the ingredients inside the blender have been mixed, a doorway at the bottom of the bowl is opened. With the blender still agitating the ingredients, the mix is allowed to run out onto a conveyor belt or other channeling device. The belt then moves the detergent to another area of the factory where it can be dropped into boxes or cartons for delivery to wholesalers or distributors.
THE AGGLOMERATION PROCESS
* In this method, dry ingredients for a detergent are first fed into a large machine known as a Shuggi agglomerator (Shuggi is the manufacturer). Inside the agglomerator, sharp, whirling blades mix the material to a fine consistency; the process resembles food being textured inside a food processor. * After the dry ingredients have been blended, liquid ingredients are sprayed on the dry mix through nozzles fitted into the agglomerator’s walls. The blending continues, causing an exothermic (heat-producing) reaction to occur. The resulting mixture is a hot, viscous liquid similar to gelatin that hasn’t hardened. * Next, the liquid is allowed to flow out of the agglomerator. As it leaves the machine, it collects on a drying belt where its own heat, exposure to air, and hot air blowers render it friable—easy to crush or crumble. The newly made detergent is then pulverized and pushed through sizing screens that ensure that no large lumps of unmixed product go out to the market. The result of this process is a dry detergent made up of granules of the mixed detergent. THE SLURRY METHOD
* In this process, ingredients are dissolved in water to create a slurry. With a pump, the slurry is blown through nozzles inside the top of a cone shaped container as hot, dry air is simultaneously forced into the bottom of the cone. As the slurry dries, “beads” of dry detergent fall to the bottom of the cone, where they can be collected for packaging. LIQUID DETERGENT
* If the detergent is to be liquid rather than powder, it is simply mixed back in—after all ingredients are blended—with a solution consisting of water and various chemicals known as solubilizers. The solubilizers help the water and detergent blend together more fully and evenly. Quality Control
Manufacturers constantly monitor the quality of their detergents, and they utilize the same testing methods to assess the effectiveness of new products. In one method, light is shined onto a piece of fabric that has been soiled and then washed in the test detergent. The
To make liquid detergent, the dry powder is simply mixed back in with a solution consisting of water and chemicals known as “solubilizers.” These chemicals help the water and detergent blend together more evenly. amount of light reflected, compared to the amount reflected by a sample of the original fabric, is a measure of cleanliness. A reflection rate of 98 percent is considered quite good and indicates that the detergent has cleaned properly. Another method involves laboratory burning of a small amount of material that has been soiled and then laundered. The weight of the ashes, plus the weight of the gaseous results of the burning, reveal how much of the dirt remained in the fabric after laundering. A result that is much higher than a clean test sample indicates that a significant amount of dirt was retained in the laundered sample. Naturally, the goal is to come as close to the weight of a clean control sample as possible.
Production Process for Laundry Detergent Powder Process
Laundry detergent production is typically a continuous process. There are a large number of ingredients which must be continuously, simultaneously and accurately fed into a mixer or onto a conveyor belt, which in turn supplies the continuous mixer. Feeding of Base Powder and Additives
The base powder is produced from various solid and liquid ingredients. The actual mass flow rate of base powder being produced is metered by a Smart Weigh Belt, mounted at the discharge of either a spray tower or fluidized bed. Next, other loss-in-weight dry feeders add additional minor powder ingredients onto the conveyor belt with the base powder. The combined ingredients then enter a continuous mixer, where liquid additives such as perfumes are dosed in exact proportion using liquid loss-in-weight feeders or liquid PID control. After mixing, the detergent powder passes through a final sieving and metering stage. In the final step, a Smart Weigh Belt transfers the finished product into the packing operation. There it flows directly to a packing machine, tablet press or into FIBC’s for intermediate storage or bulk transport.
Typical Production Process for Laundry Detergent Powder
Typical Ingredients
The powder feeder must handle a wide range of ingredients such as:
* Sodium carbonate
* Sodium bicarbonate
* Sodium perborate
* Sodium sulphate
* Tetrahydrate
* Sodium tripolyphosphate
* Sodium silicates
* Sodium percarbonate
* Anionics
* Encapsulated enzymes
* Colored beads
* Anti-foaming powder
* Polymers that release stains
* Polymers that prevent new stains
* Sodium silicates
The liquid feeders supply:
* Anionics
* Non-ionic
* Perfumes
Smart Weigh Belt Feeder for Base Powder Production
The K-Tron Smart Weigh Belt (SWB) feeder is the perfect solution for a compact gravimetric feeder which can handle large volumes of bulk material with different flow characteristics. The SWB feeders offers continuous online taring by using two weigh modules and are available in both 300 and 600 mm belt widths. Automatic and continuous online tarring of the weigh belt reduces costly maintenance, line shutdowns and laborious manual calibration while at the same time substantially improving long term accuracy and stability. The conveyor is removable from the stainless steel housing via a telescopic support structure. This facilitates thorough cleaning of the feeder.
Application & Technology
* The application of the synthetic detergents generally produced a marked inhibition of the lowering of the pH in plaques, but in no case was the inhibition complete. In comparable experiments Zephiran and Phemerol gave a greater degree of inhibition than Damol and Tergitol-7. As a rule, it was found that the eflect of the synthetic detergents on the pH after 10 per cent glucose was much greater in the cases where the plaques were relatively thin than when the plaques were relatively thick. * Application of the synthetic detergents in a solution containing an auxiliary substance, such as an alkaline buffer, did not significantly change the inhibitory effect produced by the detergent, although some of the auxiliary agents did raise the pH levels of both the control and test pH curves. * The latest cleaning technologies include enzyme-containing detergent formulations and zeolite-based detergents. Of these, the enzyme detergents are proving extremely useful in keeping a check on environmental pollution. They offer a suitable option to the synthetic detergents with regard to their biodegradability, low toxicity, non-corrosiveness, environment-friendliness, enhanced cleaning properties as well as increased efficiency and stability in different formulations.