Pre-contract Stage
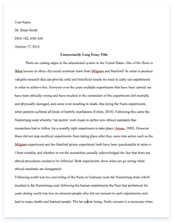
A limited time offer! Get a custom sample essay written according to your requirements urgent 3h delivery guaranteed
Order NowPre-contract Stage
Contractor’s Tendering Procedure
• Agreement to tender
• Decision to tender
• Examination of tender documents
• Estimating process timetable
• Enquires of quotations
• Method statement and tender programme
• Site visit
• Outstanding information resolved with consultants
• Pricing process
• Adjudication
• Submission of tender
*In pricing process:
• All-in-rates for trade items or BQ
• Domestic sub-contractors and suppliers
• Nominated sub-contractors and suppliers
(prime cost and provisional sums)
• Preliminaries and conditions of contract
• Daywork charges
• Allowance for firm-price tender
• Project overheads
• Profit and risk
Tender Stage
At tendering stage for the main contract, a contractor has to be deciding which parts of the work to be taken up by sub-contractors. Since tendering for the sub-contractors are to be carried out simultaneously with the tendering of the main contract. The potential sub-contractors and suppliers’ prices may be included when pricing the main contract’s tender. Usually the tendering process for sub-contractors will be less formal, normally be selective tendering or informal negotiations. Sometime the Main contract’s estimator may just simply call up a few better acquainted sub-contractors to get quotations. It is important that quotations or priced sections of the BQ being submitted by the sub-contractor within scheduled time to suit the main tender.
Final Account
Bills of Quantities
• All Work and Liability are itemized with Quantities
– Prepared by Client (with consultants e.g. QS)
– Released for pricing by Tenderers
– Form a same scope of works for pricing
– Quantities form part of Contract
– Each Item Quantity x Rate inserted by Tenderer = Amount of Item – Sum up the Amounts of Items to get the Total i.e.
Tender Sum
Schedules of Rates
• All Work and Liability are itemized but the Client is not responsible for the measurement of Items Quantities • Prepared by Client (with consultants e.g. QS) or Tenderers – Based on other tender documents, Quantities are measured by Tenderers or Client • With the method of measurement specified by Client
• With rules stipulated by trade practice
– Quantities not form part of Contract
– Each Item Quantity x Rate inserted by Tenderer = Amount of Item – Sum up the Amounts of Items to get the Total i.e. Tender Sum
Bills of Measurable Items
• Items (from other tender documents) of
– Works
– Activity
– Liability
• Tenderer infill Item Rate
• Quantity x Rate = Item Amount
Bill of Prime Costs & Provisional Sums
• Prime costs
– filled in by Employer for
• Works executed by Nominated Sub-Contractors
• Materials supplied by Nominated Suppliers
– Adjusted with actual costs of nominated subcontracts
• Provisional Sums
–filled in by Employer for the works/activities/liabilities unknown in tendering stage –Adjusted with actual costs
4.3
Assume that the project is a Contract Sum Project “Lump Sum Contract”. The quality and quantity of the work included in the Contract Sum shall be deemed to be that which is shown upon or described in or implied from the Contract Documents.
Therefore, the highest priority has always been placed on quality. So, quality assurance and quality control are essential elements in the schedule. During construction, the employer’s representative should inspect the works and test materials and goods, checking the types, standards and quality of materials and goods, standard and quality of workmanship and quality of work in the project can be control the quality in the project. Moreover, the quality of works should be carried out under the Contract according to the Specification and Drawing.
The Contractor shall provide all materials and goods of the types, standards and quality described in the Contract Documents to the satisfaction of the Employer’s Representative. Where the Contractor is responsible for selection of the materials and goods in accordance with a performance specification or otherwise the materials and goods shall be fit for their purpose. The quality of materials and articles supplied for any purpose are to be approved by the Employer’s Representative prior to their use in the Works. The Contractor shall also provide samples of workmanship for all trades and obtain the Employer’s Representative’s approval prior to commencement of each trade. All subsequent workmanship shall be to the standard of the approved samples.
The Contractor shall submit for the Employer’s Representative’s approval within two weeks after the award of the Contract a quality plan.
The quality plan shall include: (a) Quality management organization covering all stages of planning, design, construction, completion and handover of the various portions of the Works; (b) Reporting line, responsibilities and authority of the quality management representatives for the day to day management of the work with particular reference to the supervision, inspection and testing of the work; (c) Details of the methods to be used by the Contractor for the selection of sub-contractors and major suppliers capable of providing goods and/or services for compliance with quality systems which can be audited; (d) A typical inspection and test plan identifying the control elements of quality activities at various stages of works, the frequency and the degree of inspection and testing, the acceptance criteria or relevant specification, necessary hold point and the inspection and testing authority; and (e) Detailed method statements of construction and/or manufacture and installation of the work.
It is a term of the Development Agreement that Construction Contracts (including subcontracts) entered into in connection with the construction of the Development shall provide that all warranties, indemnities, guarantees, express and implied conditions as to the quality of workmanship and fitness for purpose, maintenance and service periods and the like shall be to the benefit of and be enforceable by the Company.