Plastic recycling
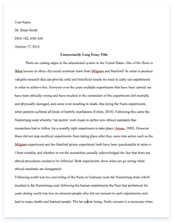
- Pages: 15
- Word count: 3512
- Category: Marketing Plastic Pollution Recycling
A limited time offer! Get a custom sample essay written according to your requirements urgent 3h delivery guaranteed
Order NowPlastic recycling is the process of recovering scrap or waste plastic and reprocessing the material into useful products, sometimes completely different in form from their original state. For instance, this could mean melting down soft drink bottles and then casting them as plastic chairs and tables. Plastics are also recycled/reprocessed during the manufacturing process of plastic goods such as polyethylene film and bags. A percentage of the recycled pellets are then re-introduced into the main production operation.
This closed-loop operation has taken place since the 1970s and has made the production of some plastic products amongst the most efficient operations today. Compared with other materials, such as glass and metal, plastic polymers require greater processing (heat treating, thermal depolymerization and monomer recycling) to be recycled. Due to the high molecular weight of their large polymer chains, plastics have a low entropy of mixing. A macro molecule interacts with its environment along its entire length, so total energy involved in mixing it is largely due to the product side stoichiometry (see enthalpy). Heating alone is not enough to dissolve such a large molecule, so plastics must often be of nearly identical composition to mix efficiently. When different types of plastics are melted together, they tend to phase-separate, like oil and water, and set in these layers. The phase boundaries cause structural weakness in the resulting material, meaning that polymer blends are useful in only limited applications. Another barrier to recycling is the widespread use of dyes, fillers, and other additives in plastics.
The polymer is generally too viscous to economically remove fillers, and would be damaged by many of the processes that could cheaply remove the added dyes. Additives are less widely used in beverage containers and plastic bags, allowing them to be recycled more often. The use of biodegradable plastic is increasing.
5 Stages of the Plastic Recycling Process
Reference: PERLOG (press release distribution)
Plastic recycling is the term given to the processing of waste plastic which turns old or scrap plastic in to a useable product which can then re-enter the manufacturing chain.
PRLog (Press Release) – Oct. 27, 2011 – Plastic recycling is the term given to the processing of waste plastic which turns old or scrap plastic in to a useable product which can then re-enter the manufacturing chain. In order for the plastic to be in a suitable format for re use in manufacturing environments such as by injection moulding companies the waste or scrap plastic, needs to go through several recycling processes.
Stage One â Sorting the Plastic
Firstly the waste plastic needs to be collected by the recycling company, once the plastic arrives at the recycling plant the first stage is sort the plastic in to the specific types, plastic recycling is more complex than
that of metal or glass recycling due to the many different types of plastic and more importantly mixed plastic cannot be used in manufacturing without delivering poor quality products, hence why plastic recycling companies need to be thorough when it comes to sorting the waste plastic in to the different forms prior to the next stage in the recycling process.
Stage Two – Washing Waste Plastic
Once the waste plastic has been identified and separated in to one of its many forms the cleaning process can begin, this usually starts with washing to remove paper labels, adhesives and other impurities, all the labels on your plastic containers, bottles and even your wheelie bin need to be completely removed as these will lower the quality of the finished recycled plastic.
Stage Three- Shredding the Plastic
The shredding stage is when the waste plastic is taken and loaded on to conveyor belts or directly in to huge hoppers that funnel the clean scrap towards rotating metal teeth that rip the plastic in to small pellets which are bagged up afterwards ready for testing.
Stage Four â Identify and Classify the Plastic
Once the shredded plastic has been bagged it is then chemically tested and labelled as to its exact specification, this rGrade plastic can be used as is by adding to a mix of virgin plastic in a manufacturing run, alternatively the rGrade plastic can be further recycled.
Stage Five – Extruding
This is the final stage in recycling plastic, this involves melting the clean shredded plastic and extruding in to the form of pellets which then go on to manufacture the next lot of plastic products.
Reasons to Recycle Plastic
Reference: Biofina (the future of bio renewable plastics)
Millions of tons of plastic waste end up in landfill when the vast majority of it can be recycled, itâs all too easy for us to throw away trash without a second thought but we need to take care of our planet and not just reduce the amount of trash we bury, but also given that plastic is derived from oil a natural product with ever depleting resources, it makes sense to recycling as much as possible. Recycled products are becoming more popular and important and are growing every day, as oil exploration moves to ever more hostile and difficult to reach locations, which will of course will result in prices of products made from oil to increase.
Recycled plastic – the fashion fabric of the future
Reference: Innovations report (forum of science, industry and business) A novel research project is looking at ways to recycle plastic bottles for use in the fashion industry in a bid to halt the landfill crisis. Although recycled PET (Polyethylene terepthalate) has been used in a limited way in the fashion industry, Northumbria University PhD student Yukie Nakano is working to identify the barriers affecting the wider introduction of recycled textile products. Yukie, who is also a research assistant in the Centre for Design Research, is also experimenting with recycled plastic to produce new types of visually enhanced fabrics â mainly knitting yarns – to evaluate the potential market for their use as textiles.
Ex-fashion designer Yukie said: âPET is fairly easy to recycle and can be made into flakes which can then be spun as a yarn. It has been used in a limited way in the fashion industry but it never really took off.
VINYLPLUS & RECOVINYL ARE GRADUALLY CLOSING THE LOOP
Waste collection is, of course, the starting point for any recycling process. This is why Recovinyl was established to motivate the collection and recycling processes through financial incentives. This strategy proved to be a highly effective way of taking the modest PVC recycling volumes that existed in the pre-Vinyl 2010 EU to an impressive 250,000+ tonnes a year of post-consumer PVC waste. But preventing material from being landfilled is not a sustainable end in itself. To close the loop and preserve resources in a more sustainable system, product manufacturers need to be encouraged to keep increasing the volumes of recyclate that they include in their new products. VinylPlus has increased its target for recycling to 800,000 tonnes by 2020 (now including ex-factory industrial waste as well as post-consumer waste) and has switched its focus to stimulating the re-use of recycled material. The goal is to create a âPull Marketâ where the increase in recycled volume of PVC will be paired with an increase in demand for recyclate. To achieve that, Recovinyl will act as a mediator between recyclers and converters by certifying the quality and volume of the recycled PVC that is being produced and purchased.
PVC, a Recyclable Material – Ideal for Reprocessing
Reference: recovinyl plus
PVC (polyvinyl chloride), sometimes known as âvinylâ, is a thermoplastic material made of 57% chlorine (derived from industrial grade salt) and 43% carbon (derived predominantly from oil / gas via ethylene). PVC is inexpensive to make, requires minimal maintenance when in use, and is extremely durable (it is commonly used to make long-lasting products, often with a life-expectancy exceeding 60 years). Thanks to its unique polymer structure, PVC products are well suited for recycling when they come to the end of their life. PVC compounds are 100% recyclable physically, chemically or energetically. After mechanical separation, grinding, washing and treatment to eliminate impurities, it is reprocessed using various techniques (granulated or powder) and reused in the production. There are two principal ways of recycling PVC:
â˘Mechanical recycling: PVC waste is ground into small pieces that can be easily processed into new PVC compounds ready to be melted and formed into new products. â˘Feedstock recycling: PVC waste is broken right back down into its chemical molecules, which can be used again to make PVC or other
materials.
Dumping PVC in a landfill takes up precious land and squanders a valuable resource. Most PVC products are voluminous and light, and may last for hundreds of years without degrading. Its value should always be re-captured in some way either through recycling or at the very least by utilising its calorific value as a component of a clean energy-from-waste system, in industry power generation or district heating schemes. As landfill is being progressively restricted within the European Union, recycling will gradually become the principal option for many end-of-life PVC products.
Plastics Recycling and The Need For Bio-Polymers
Reference: International society of environmental botanist
Indians have a remarkably small ecological footprint compared to citizens in advanced countries. Non-biodegradable waste in large Indian cities averages just 50 â 100 gm per capita per day, compared to 1-2 kg in the West. Sadly, this is often disparaged as âbackwardnessâ or under-development, rather than recognizing and appreciating the natural conservation culture of Indians, who will repair and use appliances and cars for years, hand down clothing to relatives or servants, waste no food, and even save paper and string for re-use. However, the sheer abundance of thin-film plastics has broken this habit. The sheer availability of not just carry bags, but bread wrappers, packaging of fresh foods and provisions like rice, dal etc, shrink-wrap, micro-packs of cosmetics and pan parag etc is far beyond the need or capacity of families to re-use them. So they get thrown away, and this has overwhelmed the ability of cities to handle this waste. Only low gauge low-value plastic is a problem, as milk pouches etc are rarely thrown away; they still find their way directly to waste buyers. Organic waste has been a valuable resource for centuries, returning nutrients and micronutrients to the soil in a sustainable cycle. For this reason, the composting of biodegradable municipal waste is now mandatory for every urban local body under the MSW Rules 2000. But thin-film plastic packaging is creating a major problem. In 1993 it was estimated that 1.5-2% by weight of municipal
waste reaching the dumpsites and compost plants is thin-film plastic. Some recent estimates are as high as 7-9%. What is worse is, that regardless of the weight content in waste, by volume thin plastics are equal to or even more than the volume of compost produced. The capital cost and operating cost of machinery to separate out plastics from processed waste currently makes the compost unaffordable high-priced for farmers. WHAT IS RECYCLED?
i) Thin-film plastic
Today, Indiaâs landscapes are littered with so much thin plastic that many citizens desire a total ban on its use, with some initial success that fades with time. Since a few hundred carry-bags are required to make a kilo of saleable scrap, it is simply not economical for waste-pickers to collect such ultra-thin waste, even if it is 20 micron or more, so it remains in the garbage in increasing quantities. This will change as soon as higher prices for waste-pickers are possible, say Rs 5 per kg to a rag picker. This may happen because the year 2002 has seen an exciting new use for such waste. The KK Process chops thin-film road-waste into tiny flakes, and its customized dosing machine can introduce this light fluff uniformly into viscous bitumen in hot-mix plants. Tests at Bangalore and the Indian Road Research Centre proved that resultant roads will have as much as three times better life and resistance to both heat, cold, rutting and cracking.
ii) PET bottles
Globalization has flooded Indian cities with packaging that is theoretically recyclable but is not in practice recycled. PET bottles for soft drinks and mineral water are the biggest problem, as they end up in gutters and block surface and underground drains, causing flooding in low-lying areas and enormous economic loss annually, especially to the poorest that normally live in the worst-affected areas. The US and EU have stringent laws for take back of such wastes, so they dump their PET waste almost free in India for recycling mainly by IOCâs Futura Industries at Chennai. They recycle this and post producer waste from PET bottle factories, leaving our own post-consumer waste uncollected and unrecycled, because we have no laws at present to prevent such waste dumping into the country.
Energy and economic value of platic
Refrence: journalistâs resource research on todayâs new topic
Plastic trash is a potential â and plentiful â fuel source, but up to the present many regions of the United States have been reluctant to adopt waste-to-energy technologies. Among the reasons are the availability of relatively cheap land for trash disposal, recyclers who viewed such programs as potential threats, and resistance by local homeowners. A 2011 study by Columbia Universityâs Earth Engineering Center for the American Chemistry Council, âEnergy and Economic Value of Non-recycled Plastics (NRP) and Municipal Solid Wastes (MSW) that are Currently Landfilled in the Fifty Statesâ (PDF), attempts to calculate the energy contained in discarded materials and its economic value. In their study, the researchers first calculate the amount of plastic waste in the United States in 2008 based on EPA data and the centerâs own survey, then use this information to apportion the amount of waste and lost âenergy valueâ per state. Key study findings include:
â˘Overall U.S. post-consumer plastic waste for 2008 was estimated at 33.6 million tons; 2.2 million tons (6.5%) were recycled and 2.6 million tons (7.7%) were burned for energy; 28.9 million tons, or 85.5%, were discarded in landfills. â˘The United States currently has the capacity to convert just 10% of the postrecycled municipal solid wastes (27 million tons) to energy. â˘Connecticut, Massachusetts, Hawaii, Virginia and Minnesota were rated the best at sustainable plastic waste management, measured by utilization of post-consumer plastic and tons of waste in landfills. Alaska, New Mexico, Montana, Oklahoma and Mississippi were rated the worst. â˘The potential energy contained in the 28.9 tons of post-consumer plastics deposited in landfills in 2008 equals the amount of BTUs in 36.7 million tons of coal, 139 million barrels of oil, or 783 billion cubic feet of natural gas. Uses of plastic
Packaging represents the largest single sector of plastics use in the UK. The sector accounts for 35% of UK plastics consumption and plastic is the material of choice in nearly half of all packaged goods. The percentage consumption of lastics are :
Mechanical engineering 2%, medical 2%, footwear 1%, packaging 35%,Building and construction 23%, electrical and electronics 8%, furniture/houseware 8%, transport 2%, agriculture 7%,toys and aports 3% and others 3%. Types of plastic
There are about 50 different groups of plastics, with hundreds of different varieties. All types of plastic are recyclable. To make sorting and thus recycling easier, the American Society of Plastics Industry developed a standard marking code to help consumers identify and sort the main types of plastic. These types and their most common uses are:
HDPE
High-density polyethylene – Bottles for milk and washing-up liquids.
PVCPolyvinyl chloride – Food trays, cling film, bottles for squash, mineral water and shampoo.
LDPELow density polyethylene – Carrier bags and bin liners.
PPPolypropylene – Margarine tubs, microwaveable meal trays.
PSPolystyrene – Yoghurt pots, foam meat or fish trays, hamburger boxes and egg cartons, vending cups, plastic cutlery, protective packaging for electronic goods and toys.
OTHERAny other plastics that do not fall into any of the above categories. – An example is melamine, which is often used in plastic plates and cups.
CONCLUSION:
Reference: Agri food and veterinary( authority of Singapore) Safe Use Of Plastic Food Packaging And Containers
Plastics are used in the manufacture of a wide range of food packaging and containers. Food packaging keeps food safe from contamination and from damage during distribution while providing fresh food for consumers. Plastic containers such as cups, plates, bowls and bottles offer a range of lightweight and unbreakable kitchenware for our daily household use. The diversity of properties of plastics allows them to perform many of the necessary tasks. Plastics are made from long chain polymers and each polymer is composed of small building units called monomers that are chemically linked together. Different combinations of monomers yield polymers with different properties and characteristics. In addition, plastic additives are incorporated into polymers during the manufacturing process to confer specific properties to the polymer for certain packaging applications. For example, the introduction of nucleating agents improves the clarity and stiffness of a plastic polymer which allows it to be used for making rigid and clear containers that show-off the contents and appeal to consumers. Chemicals that are used in the manufacture of plastic packaging or containers can migrate into foods during use. The quantities of migrating chemicals will depend largely on the nature of food, the contact temperature and the contact time. However, proper usage of the plastics will have insignificant or very low levels of chemical migration, which does not pose any health risk to consumers even after long-term use. When manufacturers design a plastic packaging, they will take into consideration the type of food and its contact time with the packaging, and the amount of heat to which the plastic will be subjected. It is therefore crucial that consumers do not misuse packaging materials in an unintended or unanticipated manner as this may result in greater amounts of chemical migration than would otherwise be expected. The following are some guidelines for safe use of plastic food packaging and containers.
Plastics and conventional oven
â˘Unless indicated otherwise, plastic packaging used for commercial packing of food is not suitable for use in conventional ovens. They may catch fire or melt and resulting in chemical migration into foods. â˘Reheat pre-cooked foods in a conventional oven only if they are sold in specially made “ovenable” packaging and oven reheating instructions are given by the manufacturer. Plastics and microwave oven
â˘Only use plastic containers that are labeled as microwave-safe for microwave cooking or reheating. Do not use the container in a microwave oven if you are in doubt or unable to find the manufacturer’s instructions for microwave use. â˘Cold or freezer storage containers such as yoghurt, margarine and ice-cream tubs are not manufactured for reheating or cooking food in a microwave or conventional oven. They are not heat stable and chemicals from the plastic may migrate into the food during heating. Plastic cling films
â˘Do not use cling films in conventional ovens or with pots and pans on cooker hobs where the films may melt into the food. â˘Always follow the manufacturer’s instructions on the proper usage of the cling films. â˘Only use cling films designated as suitable for use in microwave oven. â˘When re-heating or cooking food in a microwave oven, ensure that the microwave-safe cling film does not touch the food. If the film touches the food, the film could get overly hot and possibly melt or may migrate chemicals into the food.
Freezing, defrosting and cooking fresh produce in commercial plastic packaging â˘It is safe to freeze meat directly in its original commercial plastic wrapping. For long storage, rewrap or over-wrap the meat tightly with moisture proof freezer bags to maintain the quality and texture of the meat. ⢠Do not defrost or cook the meat in its original commercial packaging in a microwave oven, as the plastic packaging may not be microwave-safe. Reusing plastic packaging and containers
â˘Commercial plastic packaging that has been used for storing non-food items (e.g. detergents) should never be reused as food containers. They have not been tested safe for food storage and they may contain non-food residues that contaminate food. â˘Plastic packaging that are used for commercial packing of food and takeaway plastic food containers used in eating outlets are disposable items designed for single use and are not intended for repeated storage of food. They are safe for their immediate intended purpose but not beyond what they are designed for. â˘Only use those takeaway food containers that are labeled microwave-safe for reheating food in the microwave oven. They should not be reused for microwave heating. â˘Plastic packaging for microwaveable convenience meals are designed for one time usage with the type of food packed in it and should not be reused for storing or microwave heating of food. â˘Only use reusable plastic food containers (e.g., cups, plates, bowls, bottles and boxes used in household kitchens) for repeated storage of food. These containers have the sturdiness, thermal stability and other attributes needed for a reusable food container. â˘Reusable plastic food containers can be subjected to wear and tear after a period of use. They should be replaced when they have turned cloudy or discoloured or if cracks or heavy abrasions start to appear.
REFRENCE
1.)PERLOG( Press release distribution) www.prlog.com
2.)BIOFINA( The future of bio renewable plastics) biofinagroup.com
3.)Innovation report forum of science, industry and business www.innovations-report.com
4.)Recovinyl plus ( www. Recovinyl.com)
5.)International society of environment botanist (isebindia.com)
6.)Journalist resource research on todayâs new topic
(journalistresource.org)
7.)Agri food & veterinary Authority of Singapore (www.ava.gov.sg)
8.) texyloop: recycle de textile pvc (texyloop.com)
9.) Polystyrene recycling (polystyrene packaging council)
10.) Polymer processing .com