Operations Management & Quantitative Techniques
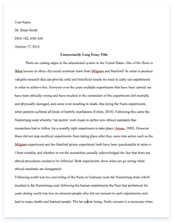
- Pages: 9
- Word count: 2199
- Category: Accounting Management
A limited time offer! Get a custom sample essay written according to your requirements urgent 3h delivery guaranteed
Order Now1. Develop a master production schedule for the breadmaker. What do the projected ending inventory and available-to-promise numbers look like? Has Realco “overpromised”? In your view, should Realco update either the forecast or the production numbers? A master production schedule for the bread-maker will be presented below. Demand Management Week 1 Week 2 Week 3 Week 4 Week 5 Week 6 Week 7 Week 8. Weekly demand for bread-maker is 20,000 20,000 20,000 20,000 20,000 20,000 20,000 20,000. Working days in a week is 6 6 6 6 6 6 6 6. MPS demand for bread-maker 3,333 3,333 3,333 3,333 3,333 3,333 3,333 3,333. Realco Company should update the production numbers since from the available figures, it is clear that the bread-makers produced are far much greater than the demand anticipated. The weekly production is 40, 000 while the assumed demand per week is about 20,000 bread-makers. The production numbers could be adjusted to about 25,000 bread-makers. This is owed to the fact that the highest current order according to Jack Jones is 23, 500.
2. Comment on Jack’s approach to order promising. What are the advantages? The disadvantages? How would formal master scheduling improve this process? What organizational changes would be required? One advantage of this approach is that it is cost effective.
This is due to the fact that it is much cheaper to produce a whole batch of a given product compared to production of each single order. One disadvantage that is worth noting is that, the approach may result to overhead production, whereby the production may exceed the actual demand. Moreover, this approach may lead to loss of customers and market share due to failure to meet individual tastes and preferences (Bundy, 1999). Formal master scheduling would improve the process by keeping control and accountability of the entire production and shipment promising. Additionally, it can help protecting lead time and booking future deliveries. The schedule controls the manufacturing process and not the customer demand. One of the organizational changes that would be necessary in the adoption of a formal master scheduling is managerial changes whereby the company has to hire a master scheduler to be in charge of the process. Technological changes such as installing master scheduling software are also necessary.
3. Following up on Question 2, which do you think is worse, refusing a customer’s order upfront because you don’t have the units available or accepting the order and then failing to deliver? What are the implications for master scheduling? Accepting an order and then failing to deliver is worse that refusing a customer’s order upfront because of unavailability of units. As noted earlier, master scheduling plays the role of controlling the manufacturing process rather than the customer demand. This means that orders would only be accepted following availability of units. Master scheduling enables a company to know the number of units or products available for sale. Knowledge of the available units of products guides the order placement and acceptance process. It is thus appropriate to refuse a customer’s order upfront in cases where units are not available. Additionally, accepting an order and then failing to deliver may result to losing of customer base or market share due to false promises. Customers tend to rely on companies that are trustworthy. Hence, failing to deliver an order may break the trust and rapport between a customer and a business. 4. Suppose Realco produces 20,000 breadmakers every week, rather than 40,000 every other week.
According to the master schedule record, what impact will this have on average inventory level? Inventory refers to the materials and goods that a company can sell. This level is especially crucial for enterprises that rely on the sale of materials and goods. When average inventory levels are too low, an enterprise may run out of a given product and lose possible sale. On the other hand, if the levels are too high, an enterprise may encounter depreciation, spoiling and even storage problems (Cox and Blackstone, 2002). Production 20,000 bread-makers every week by Realco would result to a low average inventory. This implies that Realco Breadmaster Company could run out of bread-makers and lose potential customers or sales. For instance, the current orders for week one amount are 23,500. A weekly production of 20, 000 bred-makers implies that there would be a deficit of 3, 500 bread-makers. Realco Company would therefore lose three thousand five hundred potential sales by reducing the weekly production to 20,000. Chapter 13 Case Study: Supply-Chain Challenges in Post-Earthquake Japan
The March 11 earthquake in Japan crippled the Japanese automakers, exposing the frailties of the favored lean production system. Key Japanese automakers were forced to shut down their operations after most of their suppliers were crippled by the earthquake. Key parts need for production flow could not be secured on time. Lean production system encourages manufacturers to produce only the product they need, with the key focus being reduction of wastage in the production system (Shah and Ward, 2007). The lean production system has several advantages and disadvantages. After stabilization of the production system, Japanese automakers had to come up with a “foolproof” supply chain that ensured necessary parts of production were always available. The proposed plan will effectively help the Japanese automakers to deal with natural disasters as well as some of the challenges facing the automakers. This paper looks at the lean systems and some of the proposed changes in the supply chain. 1.What are some of the advantages of the supply chain used in the Japanese auto industry before the March 11 earthquake and tsunami? What were some of its disadvantages? Most Japanese automakers used the lean production systems, whose main philosophy was that automakers should only produce what is needed, in necessary quantities at the right time.
This system offered automakers several advantages. First, the production system significantly reduced costs for the automakers as there was little direct labor required because all the non-value added activities are eliminated. This is because parts are produced in different factories and delivered to the motor makers who join them together to complete the production process. As such, very little floor space is required as well as less warehouse space per a unit of output. There are less schedule delays as the production of vehicles is continuous depending on the demand for vehicles. Another key advantage associated with this production system is high quality because quality control measures have been integrated in the production system. Cases of defects are usually detected at the source of the parts and redone before they are added to other parts. The system gives a key competitive advantage to Japanese automakers as they are able to quickly adjust themselves to changing economic conditions. Finally, lean production system leads to better communications between various functions such as marketing, design and production among others. This is because production is based on customer’s demand. Abdulmalek and Rajgopal (2007) observed that companies using lean system have developed communications system with their suppliers as suppliers only produces what they are ordered to produce.
However, this form of production also had several weaknesses, most of them which were exposed by the earthquake and tsunami. Lean production systems can only operate efficiently where there are stable systems. Unstable systems cause bottlenecks in the production chains which interrupts the production flow. The earthquake interfered with the transportation system as well as some of the suppliers. As such, some of the parts needed in the production of cars could not be delivered. This system can only operate effectively where there is no constraints as the production process can be affected by a single delay in the production chain. Another disadvantage associated with lean production system is its inability to operate in an environment where there is unpredictable demand, where high variety is required and the stock keeping level is low (Christopher & Towill, 2000). 2. Is Toyota’s plan for a “foolproof” supply chain consistent with the Lean production philosophy? Explain. Due to the disadvantages associated with lean production system, Toyota proposed that automakers should come up with a supply chain that would make sure that the automakers are not affected by natural disasters. The new proposed plan was inconsistent with the philosophy of lean production.
The system will require some of the parts to be produced in bulk and stored as a measure of making sure that the company was well prepared in case there is another earthquake. This first proposed change in the supply chain is to have those suppliers that are in the lower chain to hold inventories of special parts that could be used for several months. According to Christopher and Towill (2000), suppliers should be able to determine the necessary inventory that they should keep through forecasting the customer’s needs in the industry. The new supply chain will also require each region to have its independent supply chain, a move that would increase the number of suppliers as well as factors of production required (Bozarth & Handfield, 2010). As such, the proposed supply chain is not as lean as the proposition made by Toyota would increase the number of parts produced by the suppliers. They would also result in warehouse costs for the company. 3. Can you think of any additional ways Toyota (and its competitors in the Japanese auto industry) can improve upon the company’s plan to create a “foolproof” supply chain? One of the ways which Toyota can be able to improve on the “foolproof” supply chain is forecasting global areas where there are higher demands for cars and building new hubs.
This should be complemented by having multiple sources of various parts. One of the ways of eliminating inefficiencies in the supply chain is by having multiple sources for single parts to make sure that the supply chain is more competitive. This can be achieved by developing a quality checking system that will be used to ensure that all multiple sources are able to meet the quality that the automakers require for their production. This is in line with a decision by the automakers to open up the supply chain, taking the role of quality control to make sure that they access only high quality parts for their production process. 4. What impact do you think Toyota’s plan will have on the way it handles relationship management in its supply chain? This proposed plan will definitely affect the way that Toyota handles relationship management in its supply chain. The company will be more involved with its suppliers as it has to make sure that its suppliers adopt the strategies proposed in the new plan. This may include constantly revising the amount of inventory that it requires a certain supplier to hold in their warehouse as well as dictating the areas that the suppliers in the chain should set up new branches so as to reduce the various risks in the supply chain.
However, the plan presents a significant challenge in the communication process between Toyota and its supplier. For example, Toyota will have to be more involved with the suppliers in the production process as inventories keeping may result in more wastage for the supplier. Additionally, there may be a problem where there is change in Toyota needs as there is inventory involved. The lean system offered several advantages to the Japanese automakers before the March 11 earthquake. The production system reduced cost; reduced wastage; ensured quality was maintained; eliminated delays; and led to better communications between various production functions. However, the system was key disadvantage was exposed by the earthquake; it was difficult to maintain production in unstable conditions as delays in one part required for production interfered with the whole production process. As such, Toyota was in dire need for a new plan that would make ensure that natural disasters did not interfere with the production process. The new Toyota plan required that suppliers should keep few months’ inventories and establisher independent production units in new areas. This is not consistent with the philosophy of lean production systems. The plan can be improved by having multiple sources for motor parts instead of single sources and creation of new production hub in new countries. The plan will require Toyota to maintain close communications with the suppliers. This new supply chain will be highly useful in countering the disadvantages of lean production system.
References
Abdulmalek, F. A., & Rajgopal, J. (2007). Analyzing the benefits of lean manufacturing and value stream mapping via simulation: a process sector case study. International Journal of production economics, 107(1), 223-236. Bozarth, C.C., and Handfield, R.B. (2008). Introduction to operations and supply chain management (2nd ed.). Upper Saddle River, New Jersey: Pearson Prentice Hall. Bundy, W. (Spring 1999) “Miller SQA: Leveraging Technology for Speed and Reliability. Supply Chain management Review, 3(2), 62-69 Christopher, M., & Towill, D. R. (2000). Supply chain migration from lean and functional to agile and customized. Supply Chain Management: An International Journal, 5(4), 206-213.
Cox, J. F., & Blackstone J. H., eds. (2002). APICS Dictionary (10th Ed).Falls Church, VA: APICS.
Shah, R., & Ward, P. T. (2007). Defining and developing measures of lean production. Journal of operations management, 25(4), 785-805