Mud Density
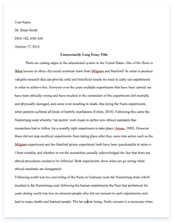
- Pages: 7
- Word count: 1648
- Category: Water
A limited time offer! Get a custom sample essay written according to your requirements urgent 3h delivery guaranteed
Order NowDrilling mud is important in the petroleum industry. Drilling mud can be composed of various types of clay. All the clays have their unique properties and when prepared with water, they will exhibit different viscosity, gel strength, and most importantly, the rheological characteristic of the drilling mud. We are required to observe the difference between Bentonite, and Attapulgite clay in both salt water and fresh water. It was also required to differentiate the few non-Newtonian fluid models, and determine the model associated with Bentonite, and Xanthan Gum.
It is clear that Bentonite and Attapulgite give different characteristic to the drilling mud. Bentonite has a low yield of clay and it is highly ineffective in salt water. Attapulgite have a high yield of clay and it doesĀ not shown any significant signs of swelling. Bentonite encountered severe swelling when mixed with fresh water. Overall, Attapulgite would be a better choice when making drilling mud.
Bentonite with fresh water exhibits Bingham Plastic properties while the Xanthan Gum with fresh water showed a fluid with a Power Law model.
* Objective
This lab is primarily divided into 2 parts. Part 1 of this lab is to determine how bentonite and attapulgite clay affects viscosity in both water and salt water. Part 2 is to determine the rheological model describing the relation between shear stress and shear rate in a water based drilling fluid. * Theory and concept
Properties of water based drilling mud are controlled mainly by the type of clay added to the drilling fluid to change its properties for better wellbore efficiency. The first part of the lab will produce twelve samples. There will be bentonite or attapulgite added to either salt water or water. The amount of clay added will be 3, 6 and 9% of the weight of water. The density and viscosity will be determined. Density will be determined using the mud balance; and viscosity will be determined using the Fann VG meter (rotational viscometer). There will also be a marsh funnel used to determine relative viscosity to water. Water will only be used for this part of the experiment. Mud Density
Density is the weight per given volume. Measuring the density of the drillingĀ fluid is important to determine the buoyancy force induced when drilling and the hydrostatic pressure the drilling fluid acts at the bottom-hole pressure. A higher density will prevent formation fluid from entering the well bore. In this lab, the density is determined using the mud balance shown in Figure 1. The mud cup takes a fixed volume of fluid sample and by adjusting the rider until balanced, a reading can be taken. This apparatus has to be calibrated using fresh water.
Figure 1
Mud Balance
Source: http://www2.mst.dk/udgiv/Publikationer/2001/87-7944-820-8/html/kap01.htm
Thixotropy
Thixotropy or the Gel strength is measured at a low shear stress after allowing it to thicken/sit for a given amount of time (10 seconds and 10 minutes by API standards). The strength of the mud cake formed will help in preventing water from entering the wellbore, as well as the drilling fluid circulating in the wellbore to leak out into a fracture. Viscosity
Part 1
Viscosity is the fluidās resistance to flow. The viscosity of the mud determines the efficiency and even ability to lift cuttings out of the well bore. Addition of different types of clay will affect the viscosity as well as the use of salt water as oppose to plain water. Using an API standard Fann VG meter, the apparent viscosity is defined as:
μApp=[600 rpm dial reading]2
Figure 2
Schematic diagram of a concentric cylindrical viscometer
Part 2
The Fann VG meter also has various rotation speeds, all of which is useful to determine the drilling fluid rheological model for shear stress to shear rate. The main components will be two cylinders; one will be referred as theĀ Rotor, and the other the Bob. The Rotor is the external cylinder that is connected to the motor giving it a constant angular velocity. The inner cylinder, the Bob is connected to a spring that gives a dial read out. Both cylinders are submerged into the fluid and there is a small annular space in between the Rotor and Bob; when the Rotor is rotating, the fluid will cause a torque on the Bob. Depending on the dimensions, the Fann VG meter used had this relation to shear stress:
Ļ= Īø
Where:Ļ = shear stress [lbf/100 ft2]
Īø =Dial reading
The shear rate is determined by:
γ=1.7*rpm
Where:γ= shear rate [sec-1]
rpm = revolutions per minute
Figure 3
Newtonian Model
Most Drilling fluids are non-Newtonian fluids, either viscosity changes with shear rate (ie. Power Law Model or Herschel-Bulkley Model), or a plastic yield must be overcome (ie. Bingham Plastic Model). A Newtonian model is the simplest. The shear stress is directly proportional to the shear rate as shown in figure 2. Common day liquids are Newtonian like water, honey and oil. The constant proportionality relating the two is called viscosity.
Figure 4
Bingham Plastic Model
A Bingham Plastic Model is similar to a Newtonian model; however it requires a plastic yield to be overcome before any shearing in the fluid will occur. The relation between shear stress and shear rate is shown in figure 3 and can be expressed as:
Ļ=Ļy+μp*γ
μp=θ600-θ300
Ļy=Īø300-μp
Where: Ļ = Shear stress [lbf/100 ft2]
Ļy = yield point [lbf/100 ft2]
μp = Plastic Viscosity [cp]
γ = Shear Rate [sec-1]
Īø600 = dial reading at 600rpm
Īø300 = dial reading at 300rpm
Figure 5
Power Law Model
A Power Law Model is similar to a Newtonian model, however it has no linearity as shown in figure 4. The shear rate and shear stress are related through an exponential term, ānā which is the flow behavior index. A power law model can be expressed as:
Ļ=K*(γ)n
n=3.322*logā”(Īø600Īø300)
K=510*Īø300(511)n
Where:Ļ = Shear stress [lbf/100 ft2]
K= Consistency index [lbf/100 ft2]
γ = Shear Rate [sec-1]
n = flow behavior index
Īøx = dial reading at x rpm
Flow behavior index ānā| Type of fluid|
<1| Pseudoplastic, or shear thinning; an increase in shear rate results in a decrease in viscosity| 1| Newtonian; shear rate and shear stress are directly proportional| >1| Dilatants, or shear thickening; an increase in shear rate results in an increase in viscosity|
Figure 6
Herschel-Bulkley Model
A Herschel-Bulkley Model is basically a Power Law model with a BinghamĀ plastic model combined together. A plastic yield is required to initiate flow, and once the fluid is viscous, the relation between shear stress and shear rate is similar to one of the Power Law Model. This can be shown in figure 5. This can be express as:
Ļ=Ļy+K*(γ)n
Where:Ļ = Shear stress [lbf/100 ft2]
K= Consistency index [lbf/100 ft2]
γ = Shear Rate [sec-1]
n = flow behavior index
Ļy = Yield Stress [lbf/100 ft2]
With four different models in mind, the selection of the appropriate model is done by plotting shear stress as a function of shear rate will give one of the 4 curves. Linear regression is used to determine the line of best fit. The two lowest rpm reading, usually 3rpm and 6rpm can be neglected from the plotting. The low rpm give an inaccurate reading because the fluid is almost at a stand still and gel strengthening is occurring. * Experimental Procedure
Part 1
1. Calibrate mud balance using fresh water. (Fresh Water Density at 21 ĢC): 8.3 lb/gal 2. Measure the funnel viscosity of water at room temperature. (Water: 26 seconds) 3. Twelve samples will be prepared in this lab section. Six of these will be mixed using fresh water, and the other six with salt water. Half of those six samples, three samples, will be mixed using 3%, 6% or 9% of Bentonite or Attapulgite by weight of water. Fresh Water| Salt Water (20,000 ppm NaCl)|
Bentonite| Attapulgite| Bentonite| Attapulgite|
Each sample will be mixed with 3%, 6% or 9% of clay by weight of water. 4. Obtain 350cc of either fresh or salt water in the mixing cup and start blender. 5. Obtain right amount of clay from bulk container.
6. Using a spatula, slowly and carefully, add reasonable amounts of clay into the mixing cup while blender is on. Be careful with spatula hitting theĀ mixer and clay dust puffing into the air. Avoid inhaling clay dust. 7. Mix sample for a minimum of 10 minutes or when sample is well mixed. 8. Place sample into Fann VG viscometer and measure apparent viscosity of sample at 600 rpm. Apparent viscosity can be calculated using formula from theory. 9. Measure density of sample using mud balance.
10. Dispose of sample properly, clean equipment and repeat with the other samples until done. Part 2
1. Calibrate mud balance using fresh water. (Fresh Water Density at 21 ĢC): 8.3 lb/gal 2. Measure the funnel viscosity of water at room temperature. (Water: 26 seconds) 3. Two samples will be prepared in this lab section. Both will use fresh water. One sample will have 35 grams of bentonite, and the either will have 4 grams of Xanthan Gum. 4. Obtain 350cc of either fresh or salt water in the mixing cup and start blender. 5. Obtain right amount of clay from bulk container.
6. Using a spatula, slowly and carefully, add reasonable amounts of clay into the mixing cup while blender is on. Be careful with spatula hitting the mixer and clay dust puffing into the air. Avoid inhaling clay dust. 7. Mix sample for a minimum of 10 minutes or when sample is well mixed. 8. Record mud temperature using digital thermometer. Place thermometer well in the center of the mud, avoiding contact with the mixing cup. 9. Measure density of sample using mud balance.
10. Place sample into Fann VG viscometer and record dial readings at 600, 300, 200, 100, 6 and 3 rpms.
11. Determine 10 sec and 10 minute gel strength.
12. Dispose of sample properly, clean equipment and repeat with the other samples until done.