IKEA Operations Management Argumentative
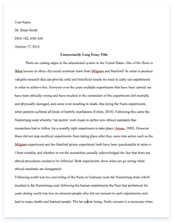
- Pages: 14
- Word count: 3315
- Category: Ikea
A limited time offer! Get a custom sample essay written according to your requirements urgent 3h delivery guaranteed
Order NowFor a business to succeed in the modern day competitive environment, it is necessary for it to undertake effective operations management. Operations may be defined as that part of a business oriented organization whose responsibility is the production of goods and services (Slack et al., 2010). Operations management refers to the activity of managing the resources used in the production and delivery of products and services. The fact that operations function produces the goods and services makes it critical to any organization. Operations management forms one of the three core functions in an organization the other two being the marketing function and the product and service development function. In order to operate effectively, these core functions are supported by other functions such as the accounting and finance function and the human resources function.
The process of operations management is equally important in small organizations as it is in larger ones. In every business organization, production and delivery of products and services efficiently and effectively is necessary rather than desirable. Due to resources limitations, managing operations in a small business always turns out to be more difficult compared to large organizations that have the resources necessary in allocating specialized tasks to individuals (Lowson, 2003). In order to adequately address business challenges related to operations management, the case of IKEA, a international home products retailer company will be looked into. The essay aims at looking at how operation management concepts have affected IKEA and three areas of operations management that are likely to impact on IKEA’s success. In the recent years, the managers at IKEA have been affected by the concepts of changing technologies, continued globalization of markets, changing job designs, quality management and global manufacturing. Furthermore the operations management areas of facility and work design, supply chain design and capacity management relate to the challenges and are likely to impact on IKEA’s success.
1. Key challenges that have become very significant to IKEA managers with regard to operations management.
1.1 Changing technologies
Today, advances in technology have a profound effect on every aspect of business, operations management included. The operations strategy adopted by an organization defines the way in which it competes with its rivals in the market place. Some of the strategies include quality, low cost, customization and speed of delivery (DavenPort & Brooks, 2004). Contrary to the past where trade-offs were involved before the adoption of these strategies, technology has raised the performance bar of businesses through allowing organizations to compete on several dimensions simultaneously. Business technology has revolutionized the manner in which business organizations conduct business. IKEA has been able to implement business technology to level the playing field with its competitors.
The company has been able to use computers, websites, personal digital products and servers to develop a competitive edge in the economic market place. IKEA managers have always considered implementation of technology in the planning process of the business. This has continued to enable them create efficient operations by using the best technologies available (Baraldi, 2008). The company has maximized its use of Internet technologies by advertising and selling its products online. Today’s continuous change in technology has vastly affected IKEA. Change in technology has mainly been seen through its designs (Li et al., 2011). Instead of selling pre-assembled furniture, the company ensures its furniture is designed to be self assembled such that the products can be flat packed efficiently. This has led to the reduction of costs and convenience to customers who rely on public transport. The managers at IKEA report that key challenge with changing technology has been ensuring that all its employees are abreast of the latest technologies.
1.2 Continued globalization of markets
Globalization of economies is an inevitable reality today. For IKEA and other international organizations, managing global operations across disparate markets and cultures has always presented both an opportunity and a challenge from an operations management perspective. The trend where global markets have become more competitive and intertwined has forced companies to try and optimize and standardize global business processes in addition to leveraging their business assets and talent pool. An organization wishing to succeed in the international markets must therefore consider the success factors for managing global operations effectively while at the same time enabling greater market responsiveness and lowering costs. Globalization refers to the integration of world’s people, governments and firms (Silveria, 2003). Globalization has resulted from closer ties in international trade, which has led to the increase in cross-country investments. Globalization has further been aided by advancement in communications and information technologies. One of the effects of globalization has been “expanded markets” (Helo, 2004). Initially, IKEA was selling products in Sweden only, the country in which it was founded. Globalization has enabled the IKEA to sell its products in different countries and continents across the world.
Globalization of markets has also enabled the company to lower its costs through production of goods in different countries where labour is cheap. The company has continued to expand its market in emerging economies of Africa and Asia with the notable country being Hong Kong. This has been implemented with the realization that emerging economies will form the future market for its products.
1.3 Changing customer expectations
The needs and expectations of customers define a company’s business strategies. IKEA managers have noted that their customers’ expectations are dynamic from both time and location perspectives. In order to adequately meet customers’ expectations, IKEA has been engaging in customer expectation management (Baraldi, 2008). Customer expectation management is the process through which a business identifies and defines customer expectations. It shows the way in which customer expectations exist in every customer’s touch point and helps business organizations create processes that help align them with their business’s success strategies. Meeting changing customers’ expectations has impacted on IKEA through expansion of the customer base, reduction of customer attrition, and increase in profit per customer through extending the customer life-cycle duration. IKEA has continued to align its business strategies to customer’s expectations through considering several imperatives. These imperatives include responsiveness, collision, dexterity, transparency, dependability, preventability, accountability and empowerment (Baraldi, 2008).
1.4 Changing job designs
Job design refers to how work in a business organization is allocated to workers. The original scientific management theory on job design is Taylorism and it emphasizes standardization of tasks and adequate and proper training of workers for them to administer their respective tasks (Menda, 2004). At IKEA, each employee is allocated a task that suits him or her the best. The operations managers have realized that the best way to deal with the changing job design challenge is by employing reward systems so that the employees remain motivated. IKEA also ensures that resources are allocated in a manner that is commensurate with specific jobs. The jobs at IKEA are constructed such that efficiency of the worker and the department under which they fall is maximized (Li et al., 2008).
1.5 Quality Management
Evaluation is a critical aspect in determining whether a business organization is successful, is maintaining individuality, generates profits and is a benefit to consumers (Vrat, 1998). Quality in an organization tends to follow to different flows of power that have been known to revolve around each other. The most common method used and that which is employed at IKEA is the vision and strategy model, which encircles the chain of command. IKEA began by developing its vision and strategy, and then invited professionals to look at the financial perspective of its situation.
This was followed by an evaluation of the learning and growth of the organization and the customer perspective. After the successful determination of the perspective and approach, it was revisited intermittently so as to determine possible adjustments necessary for growth (Baraldi, 2008). The challenge identified in quality management at IKEA was ensuring quality without compromising on finances, learning and growth, internal business processes and focus on customer perspective (Li et al., 2011). At IKEA, each level of the company is checked for quality following the order of employees, supervisors, departmental heads and division managers respectively. This is done because each level of the company has an affects the business and its success. At every level, the company determines effectiveness, efficiency and the drive (Baraldi, 2008).
1.6 Global manufacturing
According to Sonntag (2003), global shifts in international competition, consumption trends and global manufacturing are the main factors that will be involved in shaping the future of movement of goods and the demand for distribution space and warehouse. Better support of remote production sites that offer lower costs of labour offered by supply chain tracking and logistics networks has been reported as the main cause of global shifts in manufacturing (Silveria, 2003). Traditionally, goods requiring high labour content have always sought global production centers at which they can access the lowest possible costs in benefits and wages. Initially, IKEA products were manufactured in Sweden only. Due to high operation costs in Sweden, the company sought other production centers with the same materials but with lower operating costs. The company has sought production in countries where there are lower wages and in which there are viable platforms for business to thrive.
2. Areas of operations management likely to have the most impact on the success of IKEA
2.1 Facility and work design
Regardless of whether a company is a goods-producing or service-providing, facility layout and work design highly affects the organization’s ability to meet customers’ needs, provide value and enhance sustainability (Slack et al., 2010). A poorly designed facility leads to locking management into non-competitiveness and it may turn out to be costly to correct. By definition, a facility layout refers to how the specific arrangement of physical facilities is done. Studies on facility layout are necessitated by the construction of a new facility, significant change in demand or throughput volume, introduction of new good or service and installation of different processes, equipment or technologies. Layout studies are done so as to minimize delays in customer movement and material handling, maintain flexibility, promote high employee morale, provide good maintenance and housekeeping and to enhance sales in manufacturing and service facilities (Slack et al., 2010).
An organization usually has four choices in carrying out planning of the layout of the physical area of the facility. The major layout patterns include product layout, process layout cellular layout and fixed position layout. A product layout refers to the arrangement based on the sequence of operations, which are performed when manufacturing a good or delivering a service. The advantages of product layout include less material handling, shorter processing time; lower work-in-process inventories, simple planning and control systems and lower labour skills. A process layout is defined as consisting of functional grouping of equipment or activities that perform the same work. When considering cellular layout, design is done according to self-contained groups of equipment as opposed to functional characteristics of equipment. In a fixed position layout, there is consolidation of the resources necessary for manufacturing or delivering a service such as people, equipment and materials in one physical location (Slack et al., 2010).
The reason why this area of operations management is important for IKEA is the congestion that arose in its stores due to its immense success that attracted customers in large numbers. Customers loyal to IKEA became increasingly frustrated with overcrowding and long waiting times before accessing their desired products. In response, the company launched a programme for designing out the prevailing bottlenecks. The changes included clearly marking in-store shortcuts, coming up with express checkout tills for customers carrying a bag only, redesigning the car parks, a new ware house system for preventing popular product lines running out and more children play areas (Baraldi, 2008). By carrying out facility and work design, IKEA was able to solve the problem of dwindling of customers who loved the company’s products but hated the shopping experience at the IKEA stores. In order to achieve success through facility and work design, IKEA needs to implement product layout in planning the physical areas of all its stores. This will ensure that customers spend little time in sighting the product they desire without necessarily forming long queues at the entrance. The company also needs to ensure that products serving the same or related purposes are located in the same physical position. This will enhance the customers’ experiences at IKEA stores thus meeting their expectations and this will lead to an increase in sales volumes.
2.2 Supply chain design
Supply chain is by definition a subsystem of value chain dealing with physical movement of materials and goods along with supporting information through the processes of supply, production and distribution (DavenPort & Brooks, 2004). The key functions of supply chain include procurement of supplies and materials, order processing and sales, materials and inventory management, information management, transportation and distribution, customer service and finance. A supply chain must be designed in a manner that will lead to the promotion of speed and efficiency. A poor supply chain can result in decline in profits and loss of customers. With time, a company’s product lines and markets change and expand thus necessitating redesign of supply chains so as to ensure maximum profits, time to deliver, customer perception of value and quality. Generally speaking, a supply chain coordinates the flow of materials, information and services among the elements comprising a supply chain so as to maximize customer value.
The key components of supply chain include supply, manufacturing and distribution. Supply focuses on raw materials ordered and delivered to manufacturers, manufacturing focuses on the conversion of the raw materials into finished products and finally, distribution ensures that the products reach the consumers through an organized network of warehouses, distributors and retailers. A goods-producing supply chain comprises of suppliers, manufacturers, distributors, retailers and customers, all arranged in a hierarchical order (Olson & Wu, 2010). Supply chain design is critical if IKEA is to achieve success in its business. Its supply chain comprises of designers, suppliers, manufacturers, distributors, retailers and customers. IKEA outsources the design, supply and manufacturing aspects of the supply chain. It mainly concentrates on distribution, retail and ascertaining and meeting customers’ needs. In managing the supply chain, the company’s ensures that the involved costs do not affect the affordability of its products.
For instance, the company instructs its designers “no design will be accepted by the company” if it is unaffordable to the customers no matter how elegant and trendy the final product looks. To reduce the cost of final products, IKEA ensures that the location of its distribution centres are convenient to its retail centres and that the retail centres are convenient to the customers. However, the aspect of location of retail centres has been reported as a major challenge with many people opposed to the suburban location of its stores (Baraldi, 2008). If properly applied, supply chain will lead to the reduction in the prices of IKEA’s final products. The company must begin by ensuring that the raw materials are obtained in areas where the prices for them are low. To ensure this, the company must give consideration to the concept of global manufacturing and resolve the challenges surrounding it. The company must encourage its designers to come up with designs that will lead to cheap yet excellent product. The company must locate its distribution and retail centres in locations that are convenient to the customers.
2.3 Capacity management
Capacity refers to the capability of a manufacturing resource or service resource such as a process, facility, piece of equipment or workstation to achieve its predetermined purpose over a specific period of time (DavenPort & Brooks, 2004). With regard to capacity 12
management, a business organization must ensure that it has sufficient capacity for the meeting of customer demands and providing high levels of customers’ services, as this is critical if the business organization is to achieve success and be sustainable economically in the long-term. The main determinant for capacity is the resources available to the organization, that is, facilities, labour and equipment. Capacity also refers to the manner in which these resources are organized and their respective efficiency as determined by specific work methods. Capacity may be viewed in two distinct ways; as units of resource available or as maximum rate of output per unit time (Slack et al., 2010). Capacity management affects IKEA through coping with fluctuations in demand. At times the company’s products’ demand is so high such that a deficit emerges in the supply side.
This sometimes disappoints the customers hence failing to meet their expectations. Globalization of markets imposes more challenge to the company, as it must meet demands of different markets in different organizations. When high demand for a product that is in short supply occurs simultaneously in multiple markets, the company runs into problems. If properly applied capacity management will lead to the understanding of demand trends for products thus reducing the incidence of shortages that result from fluctuations in demand. By ensuring that there are noshortages in products even in peak periods, customer needs and expectations will be met thus leading to increase in sales volumes. The company must also enhance its global manufacturing so as to ensure there is enough supply of products.
Conclusion
Despite the success experienced in recent years, IKEA continues to face operations management related challenges. These challenges include changing technologies, continued globalization of markets, changing customer expectations, changing job designs, quality management, and global manufacturing. In order to increase its level of success, IKEA must improve the areas of operations management that relate to the mentioned challenges. These areas include facility work and design, supply chain design and capacity management. Facility and work design will enhance customers’ experiences at the stores; supply chain design will increase efficiency thus reducing the cost of final products while capacity management will ensure that the company doesn’t suffer from fluctuations in demand.
Reference:
Baraldi, E. (2008) Strategy in Industrial Networks: Experiences from IKEA. California Management Review, 50(4), pp. 99-127. DavenPort, T. H. & Brooks, J. D. (2004) Enterprise Systems and the Supply Chain. Journal of Enterprise Information Management, 17(1), pp. 8-19. Helo, P. (2004) Managing Agility and Productivity in the Electronics Industry. Industrial Management and Data Systems, 104(7), pp. 567-577. Li, H., Guo, H., Skibniewski, M. & Skitmore, M. (2008) Using the IKEA Model and Virtual Prototyping Technology to Improve Construction Process Management. Construction Management and Economics, 26(2), pp. 991-1000. Li, H. et al. (2011) Rethinking Prefabricated Construction Management Using the VPbased IKEA model in Hong Kong. Construction Management and Economics, 29(1), pp. 233-245. Lowson, R. H. (2003) The Nature of an Operations Strategy: Combining Strategic Decisions from the Resource-based and Market-driven Viewpoints. Management Decision, 41(6), pp. 538-549. Menda, R. (2004) The Role of a Manufacturing Audit in Crafting the Production System. International Journal of Operations and Production Management, 24(9), pp. 929-943. Meredith, J. & Roth, A. (1998) Operations Management in the USA. International Journal of Operations & Production Management, 18(7), pp. 668-674. Olson, D. L. & Wu, D. D. (2010) A Review of Enterprise Risk Management in Supply Chain. Kybernetes, 39(5), pp.
694-706. 15
Raymond, L. (2005) Operations Management and Advanced Manufacturing Technologies in SMEs: A Contingency Approach. Journal of Manufacturing Technology Management, 16(8), pp. 936-955. Rose, J. (2009) The Problem of Technological Barriers. Kybernetes, 38(1/2), pp. 25-41. Shao, X., Qi, M. & Gao, M. (2012) A Risk Analysis Model of Flight Operations Based on Region Partitions. Kybernetes, 41(10), pp. 1497-1508. Silveria, G. J. (2003) Towards a Framework for Operations Management in Ecommerce. International Journal of Operations & Productions Management, 25(2), pp. 200-212. Slack, N., Chambers, S. & Johnston, R. (2010) Operations Management. 6th ed. London: Pearson Education Limited. Sonntag, V. (2003) The Role of Manufacturing Strategy in Adapting to Technological Change. Integrated Manufacturing Systems, 14(4), pp. 312-323. Vrat, P. (1998) A Report on Operations Management in India. International Journal of Operations & Production Management, 18(7), pp. 651-653.