Hazard: Occupational Safety and Health and Information
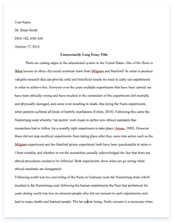
A limited time offer! Get a custom sample essay written according to your requirements urgent 3h delivery guaranteed
Order NowThe Hazard Communication Standard [63] first went into effect in 1985 and has since been expanded to cover almost all workplaces under OSHA jurisdiction. The details of the Hazard Communication standard are rather complicated, but the basic idea behind it is straightforward. It requires chemical manufacturers and employers to communicate information to workers about the hazards of workplace chemicals or products, including training. The Hazard Communication standard does not specify how much training a worker must receive. Instead, it defines what the training must cover. Employers must conduct training in a language comprehensible to employees to be in compliance with the standard. It also states that workers must be trained at the time of initial assignment and whenever a new hazard is introduced into their work area.
The purpose for this is so that workers can understand the hazards they face and so that they are aware of the protective measures that should be in place. It is very difficult to get a good understanding of chemical hazards and particularly to be able to read MSDSs in the short amount of time that many companies devote to hazard communication training. When OSHA conducts an inspection, the inspector will evaluate the effectiveness of the training by reviewing records of what training was done and by interviewing employees who use chemicals to find out what they understand about the hazards.[64] The United States Department of Transportation (DOT) regulates hazmat transportation within the territory of the US by Title 49 of the Code of Federal Regulations.[65] * Dangerous Goods
All chemical manufacturers and importers must assess the hazards of the chemicals they produce and import and pass this information on to transportation workers and purchasers through labels andmaterial safety data sheets (MSDSs). Employers whose employees may be exposed to hazardous chemicals on the job must provide hazardous chemical information to those employees through the use of MSDSs, properly labeled containers, training, and a written hazard communication program. This standard also requires the employer to maintain a list of all hazardous chemicals used in the workplace. The MSDSs for these chemicals must be kept current and they must be made available and accessible to employees in their work areas.
Chemicals that may pose health risks or those that are physical hazards (such as fire or explosion) are covered. List of chemicals that are considered hazardous are maintained according to the use or purpose. There are several existing sources that manufacturers and employers may consult. These include: * Any substance for which OSHA has a standard in force, including any substance listed in the Air Contaminants regulation. * Substances listed as carcinogens (causing cancer) by the National Toxicology Program (NTP) or the International Agency for Research on Cancer (IARC). * Substances listed in the Threshold Limit Values for Chemical Substances and Physical Agents, published by the American Conference of Governmental Industrial Hygienists (ACGIH). * Restricted Use Products (RUP) Report; EPA[19]
Ultimately, it is up to the manufacturer to disclose hazards. There are other sources of information about chemicals used in industry as a result of state and federal laws regarding the Community Right to Know Act. The Air Resources Board is responsible for public hazard disclosures in California.[66] Pesticide use disclosures are made by each pest control supervisor to the County Agricultural Commission.[67]Epidemiology information is available from the California Pesticide Information Portal, which can be used by health care professionals to identify the cause for environmental illness.[68]
Under the Oregon Community Right to Know Act (ORS 453.307-372) and the federal Superfund Amendments and Reauthorization Act (SARA) Title III, the Office of the State Fire Marshal collects information on hazardous substances and makes it available to emergency responders and to the general public. Among the information which companies must report are: * Inventories of amounts and types of hazardous substances stored in their facilities. * Annual inventories of toxic chemicals released during normal operations. * Emergency notification of accidental releases of certain chemicals listed by the Environmental Protection Agency. The information can be obtained in the form of an annual report of releases for the state or for specific companies. It is available on request from the Fire Marshal’s Office and is normally free of charge unless unusually large quantities of data are involved. [edit]Chemical labeling requirements
Each container that contains a hazardous chemical must be labeled by the manufacturer or distributor before it is sent to downstream users. There is no single standard format for labels. Each product must be labeled according to the specific type of hazard. Pesticide and fungicide labeling is regulated by the Environmental Protection Agency.[69] * The identity of the hazardous chemical(s) by common or chemical name. * Appropriate hazard warnings.
* The name and address of the manufacturer, distributor, or the responsible party.
* Product use instructions
Your employer is required to inform you of:
* The requirements of the Hazard Communication rules.
* The operations in your work area where hazardous materials are present. * The location of the written hazard communication program, the list of hazardous chemicals, and the MSDSs of chemicals that you will be exposed to. In addition, these items must be covered in training:
* Methods to detect the presence of hazardous chemicals.
* Physical and health hazards of the chemicals.
* Protective measures, including work practices, ventilation, personal protective equipment, and emergency procedures. * How to read and understand labels and MSDSs.
* The hazards of non-routine tasks, such as the cleaning of tanks or other vessels, or breaking into lines containing chemicals. [edit]Material Safety Data Sheet (MSDS)
MSDSs are often hard to figure out, even for trained safety professionals. MSDS information is required by EPA, OSHA, DOT, and/or DOE regulations depending upon the type of hazardous substance. The Material Safety Data Sheet includes the following information.
1. Product identity and ingredients by chemical or common name.
2. Physical and chemical characteristics.
3. Physical hazards, such as fire and explosion.
4. Health hazards, including symptoms.
5. Primary routes of entry of the chemical into the body.
6. Legal
exposure limits (OSHA and other recommended limits).
7. Whether the chemical can cause cancer.
8. Precautions for safe handling and use.
9. Control measures, including ventilation, personal protective equipment, etc.
10. Emergency and first aid procedures.
11. The date the MSDS was prepared.
12. Name, address, and phone number of the manufacturer.
13. Regulatory agencies, such as United States Environmental Protection Agency EPA SARA
Title III rules EPCRA Chemical manufacturers may legally withhold the specific chemical identity of a material from the MSDS and label in the case of bona fide trade secrets. In such cases the following rules apply: * The MSDS must indicate that trade secret information is being withheld. * The MSDS must disclose information concerning the properties and effects of the hazardous chemical, even if the actual chemical identity is withheld. * The trade secret information must be disclosed to a doctor or nurse in a medical emergency. * In non-emergency cases health professionals can obtain a trade secret chemical identity if they can show they need it for purposes of health protection and if they sign a confidentiality agreement. [edit]Exposure records
The Hazard Communication standard requires that chemical information must be transmitted to employees who work with hazardous materials. Employee exposure records can tell if a worker is actually being exposed to a chemical or physical hazard and how much exposure he or she is receiving. OSHA regulations that establish access rights to these records are found in 29 CFR 1910.1020: Access to Medical and Exposure Records.[70] This information is usually the product of some type of monitoring or measurement for: * Dusts, fumes, or gases in the air.
* Absorption of a chemical into the body, e.g. blood lead levels. * Noise exposure.
* Radiation exposure.
* Spores, fungi, or other biological contaminants.
Employees and their designated representatives have the right under OR-OSHA regulations to examine or copy exposure records that are in the possession of the employer. This right applies not only to records of an employee’s own exposure to chemical, physical, or biological agents but also to exposure records of other employees whose working conditions are similar to the employee’s. Union representatives have the right to see records for any work areas in which the union represents employees. In addition to seeing the results, employees and their representatives also have the right to observe the actual measurement of hazardous chemical or noise exposure. Exposure records that are part of an OR-OSHA inspection file are also accessible to employees and union representatives. In fact these files, with the exception of certain confidential information, are open to the public after the inspection has been legally closed out. [edit]Medical record
Many employers keep some type of medical records. These could be medical questionnaires, results of pre-employment physical examinations, results from blood tests or more elaborate records of ongoing diagnosis or treatment (such as all biological monitoring not defined as an employee exposure record). OSHA regulations that establish access rights to these records are found in 29 CFR 1910.1020: Access to Medical and Exposure Records.[70] Medical records are considerably more personal than exposure records or accident reports so the rules governing confidentiality and access to them are stricter. Employee medical records do not include a lot of employee medical information because of this extra scrutiny. A good rule of thumb is that if the information is maintained separately from the employer’s medical program, it probably will not be accessible.
Examples of separately maintained medical information would be records of voluntary employee assistance programs (alcohol, drug abuse, or personal counseling programs), medical records concerning health insurance claims or records created solely in preparation for litigation. These records are often kept at the worksite if there is an on-site physician or nurse. They could also be in the files of a physician, clinic, or hospital with whom the employer contracts for medical services. An employee has access to his or her own medical record (29 CFR 1910.1020). An individual employee may also sign a written release authorizing a designated representative (such as a union representative) to receive access to his or her medical record. The latter might occur in a case where the union or a physician or other researcher working for the union or employer needs medical information on a whole group of workers to document a health problem. Certain confidential information may be deleted from an employee’s record before it is released.
What is Hazard Communication?
Chemicals pose a wide range of health hazards (such as irritation, sensitization, and carcinogenicity) and physical hazards (such as flammability, corrosion, and reactivity). OSHA’s Hazard Communication Standard (HCS) is designed to ensure that information about these hazards and associated protective measures is disseminated. This is accomplished by requiring chemical manufacturers and importers to evaluate the hazards of the chemicals they produce or import, and to provide information about them through labels on shipped containers and more detailed information sheets called material safety data sheets (MSDSs). All employers with hazardous chemicals in their workplaces must prepare and implement a written hazard communication program, and must ensure that all containers are labeled, employees are provided access to MSDSs, and an effective training program is conducted for all potentially exposed employees.
The HCS provides people the right-to-know the hazards and identities of the chemicals they are exposed to in the workplace. When employees have this information, they may effectively participate in their employers’ protective programs and take steps to protect themselves. In addition, the standard gives employers the information they need to design and implement an effective protective program for employees potentially exposed to hazardous chemicals. Together these actions will result in a reduction of chemical source illnesses and injuries in American workplaces. HAZARD COMMUNICATION STANDARD
SUMMARY
Protection under OSHA’s Hazard Communication Standard (HCS) includes all workers exposed to hazardous chemicals in all industrial sectors. This standard is based on a simple concept – that employees have both a need and a right to know the hazards and the identities of the chemicals they are exposed to when working. They also need to know what protective measures are available to prevent adverse effects from occurring. SCOPE OF COVERAGE
More than 30 million workers are potentially exposed to one or more chemical hazards. There are an estimated 650,000 existing hazardous chemical products, and hundreds of new ones are being introduced annually. This poses a serious problem for exposed workers and their employers. BENEFITS
The HCS covers both physical hazards (such as flammability or the potential for explosions), and health hazards (including both acute and chronic effects). By making information available to employers and employees about these hazards, and recommended precautions for safe use, proper implementation of the HCS will result in a reduction of illnesses and injuries caused by chemicals. Employers will have the information they need to design an appropriate protective program. Employees will be better able to participate in these programs effectively when they understand the hazards involved, and to take steps to protect themselves. Together, these employer and employee actions will prevent the occurrence of adverse effects caused by the use of chemicals in the workplace. REQUIREMENTS
The HCS established uniform requirements to make sure that the hazards of all chemicals imported into, produced, or used in U.S. workplaces are evaluated and that this hazard information is transmitted to affected employers and exposed employees. Chemical manufacturers and importers must convey the hazard information they learn from their evaluations to downstream employers by means of labels on containers and material safety data sheets (MSDS’s). In addition, all covered employers must have a hazard communication program to get this information to their employees through labels on containers, MSDS’s, and training. This program ensures that all employers receive the information they need to inform and train their employees properly and to design and put in place employee protection programs. It also provides necessary hazard information to employees so they can participate in, and support, the protective measures in place at their workplaces.
All employers in addition to those in manufacturing and importing are responsible for informing and training workers about the hazards in their workplaces, retaining warning labels, and making available MSDS’s with hazardous chemicals. Some employees deal with chemicals in sealed containers under normal conditions of use (such as in the retail trades, warehousing and truck and marine cargo handling). Employers of these employees must assure that labels affixed to incoming containers of hazardous chemicals are kept in place. They must maintain and provide access to MSDS’s received, or obtain MSDS’s if requested by an employee. And they must train workers on what to do in the event of a spill or leak. However, written hazard communication programs will not be required for this type of operation. All workplaces where employees are exposed to hazardous chemicals must have a written plan which describes how the standard will be implemented in that facility.
The only work operations which do not have to comply with the written plan requirements are laboratories and work operations where employees only handle chemicals in sealed containers. The written program must reflect what employees are doing in a particular workplace. For example, the written plan must list the chemicals present at the site, indicate who is responsible for the various aspects of the program in that facility and where written materials will be made available to employees. The written program must describe how the requirements for labels and other forms of warning, material safety data sheets, and employee information and training are going to be met in the facility. EFFECT ON STATE RIGHT-TO-KNOW LAWS
The HCS pre-empts all state (in states without OSHA-approved job safety and health programs) or local laws which relate to an issue covered by HCS without regard to whether the state law would conflict with, complement, or supplement the federal standard, and without regard to whether the state law appears to be “at least as effective as” the federal standard. The only state worker right-to-know laws authorized would be those established in states and jurisdictions that have OSHA-approved state programs. These states and jurisdictions include: Alaska, Arizona, California, Connecticut (state and municipal employees only), Hawaii, Indiana, Iowa, Kentucky, Maryland, Michigan, Minnesota, Nevada, New Mexico, New York (state and municipal employees only), North Carolina, Oregon, Puerto Rico, South Carolina, Tennessee, Utah, Vermont, Virgin Islands, Virginia, Washington, and Wyoming.