Facilitate Continuous Improvement
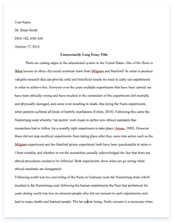
- Pages: 14
- Word count: 3301
- Category: Improve Management
A limited time offer! Get a custom sample essay written according to your requirements urgent 3h delivery guaranteed
Order NowActivity 1
1. Employees can take the initiative in matters that are related to improving the quality of services offered by the organization or by resolving existing problems. Managers should create situations that encourage employees to take initiatives without hesitation. Managers should encourage their employees to act responsibly even if employees falter in the beginning. Only then will employees feel more responsible and take the first step. 2.
Activity 2
Using accurate information is the best possible approach for companies to monitor the situation and react according to how events unfold. But even if all the âimportantâ data is collected, it will only be advantageous if it is used properly. The best tool to handle large amounts of data is an Information Management System (IMS), which provides management with an access to actions that are taking place in the field in order to see if operations are aligned with business processes.
Activity 3
1. Sustainability could be defined as an ability or capacity of something to be maintained or to sustain itself. Itâs about taking what we need to live now, without jeopardising the potential for people in the future to meet their needs. 2.
Stress
A high-stress work environment can lead to health problems and work errors. Air Quality
Poor air quality isn’t just a problem in manufacturing or heavy-duty work
sites that emit pollutants. Noise
A noisy work environment can cause headaches in the short term. Ergonomics
Insufficient lighting and uncomfortable desk chairs are examples of workplace ergonomics that can lead to health problems and work quality.
Activity 4
At the workplace, coaching and mentoring is used when the management finds that there are working individuals who need to enhance their potentials to perform better in their jobs and to be more productive.
Activity 5
1. A strategy is a recipe or program for results. In NLP, a neurological strategy is how you order and sequence your experience to produce a result. Recipes for results. A strategy is a recipe for a result. A recipe includes which ingredients, how much, what to do when, and in what order. Your modalities are the main ingredients. Your fives senses are the main ingredients in the recipe: Visual, auditory, kinesthetic, gustatory, and olfactory. We deal with sensory input on two levels â internal and external. We can process our sense internally or externally. For example, when you see something in your mindâs eye, itâs internal. When you have a feeling inside, thatâs kinesthetic internal. When you hear a whistle, thatâs auditory external. When you hear a voice in your mind, thatâs auditory internal.
2.
a. Yes, it is subsection of knowledge management system.
b. Too often, the effects of technology on the organization are not given enough thought prior to the introduction of a new system. There are two sets of knowledge necessary for the design and implementation of a knowledge management system (Newell et al., 2000):
The technical programming and design know-how
Organizational know-how based on the understanding of knowledge flows
c.Knowledge management, KM, systems improve information robustness by adding context and relationship data to stored documents. The six steps of knowledge management include creating, capturing, analyzing, indexing, storing and disseminating information. By adding information to documents, either through tags or semantic analysis and topic ontologies — the terms used to describe and represent an area of knowledge â users can find complete answers more quickly. 3.
Step 1: Establish Knowledge Management Program Objectives
Step 2: Prepare for Change
Step 3: Define High-Level Process
Step 4: Determine and Prioritize Technology Needs
Step 5: Assess Current State
Step 6: Build a Knowledge Management Implementation Roadmap
Step 7: Implementation
Step 8: Measure and Improve the Knowledge Management Program
Activity 6
Processes can be formal or informal. Formal processes â also known as procedures â are documented, and have well-established steps.
For example, you might have procedures for receiving and submitting invoices, or for establishing relationships with new clients. Formal processes are particularly important when there are safety-related, legal or financial reasons for following particular steps.
Informal processes are more likely to be ones that you have created yourself, and you may not have written them down. For example, you might have your own set of steps for noting meeting actions, carrying out market research, or communicating new leads.
Activity 7
1. Meetings â One of the most common ways to communicate. They can vary from only 1 person to thousands based on message and audience appropriate. It is up to you to maximize every minute of the time spent to have dialogue. Make sure it is a dialogue and not a monologue. It is the best way as you have the verbal and non verbal cues that enhance the communication and avoid misinterpretation.
2. Conference Callsâ These days this is the most common as it does not require the time and expense of travel. The dialogue can take place though its dependant on voice intonation and clarity of the verbal message. They only require cost of phone call and there are many paid and free services that will facilitate use of a conference call line for many people to dial into. Its also a common way for classes to be recorded and replayed when its convenient for you.
3. Newsletters/ Email/ Posters â This strategy is one way communication and utilizes emailed updates, hard copy brochures, posters, newsletters mailed or emailed. One of the weaknesses is that messages are delivered and you cannot guage if they were read and understood, deleted as sometimes there is no feedback. That immediate feedback is valuable for strengthening your message and making sure impacts and feedback are quickly received.
Activity 8
Continuous improvement is constantly adapting by getting and using information, and by evaluating changes to make sure they were effective. It requires:
Good information about your environment, from a variety of sources, to evaluate your outcomes (what you do) and your processes (how you do it). The ability to pull people together from different levels and areas to freely discuss the information and issues involved, come up with ideas, evaluate them, choose some, and carry them out. Systematic ways to measure your progress and the outcomes of your changes. A real desire to do it, even if it means changing power relationships and doing some things you do not completely agree with.
Activity 9
1. Serial Number Description Status
1 How is my product backlog looking?
2 Is the product backlog prioritized?
3 How is the sprint burn-down chart looking?
4 Are the user stories following the INVEST model?
5 Are Daily Scrum call updates in the right format?
6 Am I dealing with the impediments?
7 Are sprint review comments adjusted in the backlog?
8 Are retrospective items tracked?
9 Are all chickens informed?
10 Are team members really communicating with each other? 11 Are onshore/offshore teams touching base?
12 Are team members updating their statuses in the cards correctly?
2. Checklists structure a personâs observation or evaluation of a performance or artifact. They can be simple lists of criteria that can be marked as present or absent, or can provide space for observer comments. These tools can provide consistency over time or between observers. Checklists can be used for evaluating databases, virtual IM service, the use of library space, or for structuring peer observations of instruction sessions.
3. One such business intelligence tool that allows you to do this is known as a dashboard. A dashboard is simply a means of displaying information. There are a variety of different kinds of business dashboards that you can use to display the information compiled in your reports. The dashboard facilitates this process by making it extremely easy to convert information into charts and graphs.
Activity 10
The management functions listed above can be categorized by using the acronym POSDCORB (Bonoma & Slevin, 1978, from Gulick & Urwick, 1959):
· Planning: outlining philosophy, policy, objectives, and resultant things to be accomplished, and the techniques for accomplishment · Organizing: establishing structures and systems through which activities are arranged, defined, and coordinated in terms of some specific objectives
· Staffing: fulfilling the personnel function, which includes selecting and training staff and maintaining favourable work conditions
· Directing: making decisions, embodying decisions in instructions, and serving as the leader of the enterprise
· Coordinating: interrelating the various parts of the work
· Reporting: keeping those to whom you are responsible, including both staff and public, informed
· Budgeting: making financial plans, maintaining accounting and management control of revenue, and keeping costs in line with objectives
Summative Assessment 1
Q1.
1. Meetings â One of the most common ways to communicate. They can vary from only 1 person to thousands based on message and audience appropriate. It is up to you to maximize every minute of the time spent to have dialogue. Make sure it is a dialogue and not a monologue. It is the best way as you have the verbal and non verbal cues that enhance the communication and avoid misinterpretation.
2. Conference Callsâ These days this is the most common as it does not require the time and expense of travel. The dialogue can take place though its dependant on voice intonation and clarity of the verbal message. They only require cost of phone call and there are many paid and free services that will facilitate use of a conference call line for many people to dial into. Its also a common way for classes to be recorded and replayed when its
convenient for you.
3. Newsletters/ Email/ Posters â This strategy is one way communication and utilizes emailed updates, hard copy brochures, posters, newsletters mailed or emailed. One of the weaknesses is that messages are delivered and you cannot guage if they were read and understood, deleted as sometimes there is no feedback. That immediate feedback is valuable for strengthening your message and making sure impacts and feedback are quickly received.
Q2.
These are the keys to effective strategic planning implementation for your business.
Full and active executive support,
Effective communication,
Employee involvement,
Thorough organizational planning and competitive analysis, and Widespread perceived need for the strategic planning.
Q3.
Feedback and feed forward are two types of control schemes for systems that react automatically to changing environmental dynamics. Each utilizes sensors to measure important factors and a set of rules to react to changes in those factors. Feedback and feed forward controls may coexist in the same system, but the two designs function in very different ways.
Q4.
This unit is about how to lead and manage continuous improvement. It particularly emphasizes the role of managers in:
developing systems
analyzing information to monitor and adjust performance strategies, and manage opportunities for further improvements.
This unit applies to managers who take an active role in managing continuous improvement in order to achieve the organization’s objectives. Managers play
an important part in improving the organization.
Some examples of continuous improvement processes are:
staff meetings that review what happened and decide on improvements cyclical audits and reviews of workplace, team and individual performance evaluate and monitor effectiveness
improving systems, processes, services and products
policies and procedures that allow the organization to systematically review and improve the quality of its products, services and procedures comparing performance to industry benchmarks
seeking and considering feedback from a range of stakeholders
Q5.
Kaizen, also known as continuous improvement, is a long-term approach to work that systematically seeks to achieve small, incremental changes in processes in order to improve efficiency and quality. Kaizen can be applied to any kind of work, but it is perhaps best known for being used in lean manufacturing and lean programming. If a work environment practices kaizen, continuous improvement is the responsibility of every worker, not just a selected few.
Q6.
Use Tally Charts for Data Collection and continuous quality improvement
One of the simplest of the 7 quality tools for continuous quality improvement is that of the Tally chart, a tool that many will be familiar with from early years at school. Used to record data in a quick and easy method the tally chart is often overlooked due to its simplicity.
Q7.
a.
Among the most widely used tools for continuous improvement is a four-step quality modelâthe plan-do-check-act (PDCA) cycle, also known as Deming Cycle or Shewhart Cycle:
Plan: Identify an opportunity and plan for change.
Do: Implement the change on a small scale.
Check: Use data to analyze the results of the change and determine whether it made a difference. Act: If the change was successful, implement it on a wider scale and continuously assess your results. If the change did not work, begin the cycle again.
b.
A method for the improvement of business process performance. A knowledge management system is most often used in business in applications such as information systems, business administration, computer science, public policy and general management. Common company departments for knowledge management systems include human resources, business strategy and information technology.
c.
Aggregate of the organizational activities, incentives, plans, policies, procedures, processes, resources, responsibilities, and the infrastructure required in formulating and implementing a total quality management (TQM) approach.
d.
The concept of sustainability is based on the premise that people and their communities are made up of social, economic, and environmental systems that are in constant interaction and that must be kept in harmony or balance if the community is to continue to function to the benefit of its inhabitantsâ now and in the future.
Summative Assessment 2
Project 1
2.4. Establish continual improvement strategy
A range of different continual improvement strategies can be adopted to suit an organizationâs safety goals, business needs, culture, priorities, etc. However, there is generally a common route that all organizations will follow in identifying their continual improvement programme. An essential element of any strategy is recognition by senior management that process improvement changes can potentially impact either nuclear or conventional safety. Thus, it is essential that changes to plants, processes and organizations be properly evaluated for their potential impact on safety; and, that the implementation of such changes is controlled effectively with additional safety measures put in place as deemed necessary. Many successful organizations have given their continual improvement programmes an identity that becomes synonymous with the success and quality of their performance. It should be recognized that the successful integration of continual improvement principles may take four to six years of sustained leadership and commitment in order to become a natural part of the organizationâs culture.
To support the strategy, a framework should be established that includes requirements for: ⯠Developing performance indicators;
⯠Providing reasons for such a major improvement programme; ⯠Communicating plans to raise the level of awareness of all staff; and, ⯠Defining the continual improvement methodology (Annex I provides examples of process improvement methodologies).
The strategy should also indicate what is to be accomplished by all levels of management to implement the requirements of the continual improvement programme in their area, such as:
4
⯠Which process improvement tools might be used;
⯠Establishment and maintenance of the process improvement programme; ⯠Communication of the continual improvement tools;
⯠Development and education of personnel; and,
⯠Improvement of both internal and external environments.
The strategy should be flexible enough to allow the 2.4. Establish continual improvement strategy A range of different continual improvement strategies can be adopted to suit an organizationâs safety goals, business needs, culture, priorities, etc. However, there is generally a common route that all organizations will follow in identifying their continual improvement programme. An essential element of any strategy is recognition by senior management that process improvement changes can potentially impact either nuclear or conventional safety. Thus, it is essential that changes to plants, processes and organizations be properly evaluated for their potential impact on safety; and, that the implementation of such changes is controlled effectively with additional safety measures put in place as deemed necessary. Many successful organizations have given their continual improvement programmes an identity that becomes synonymous with the success and quality of their performance. It should be recognized that the successful integration of continual improvement principles may take four to six years of sustained leadership and commitment in order to become a natural part of the organizationâs culture.
To support the strategy, a framework should be established that includes requirements for: ⯠Developing performance indicators;
⯠Providing reasons for such a major improvement programme; ⯠Communicating plans to raise the level of awareness of all staff; and, ⯠Defining the continual improvement methodology (Annex I provides examples of process improvement methodologies).
The strategy should also indicate what is to be accomplished by all levels of management to implement the requirements of the continual improvement programme in their area, such as: 4
⯠Which process improvement tools might be used;
⯠Establishment and maintenance of the process improvement programme; ⯠Communication of the continual improvement tools;
⯠Development and education of personnel; and,
⯠Improvement of both internal and external environments.
The strategy should be flexible enough to allow the selection of the most appropriate approach for each improvement. A rigid approach that restricts the use of the most suitable tools and methodologies should be avoided. It is important to develop a strategy that outlines to the staff the plan (or roadmap) for the introduction.
Project 2
The significance of continuous improvement goes far beyond the quality movement. Ultimately it is about organizational renewal and efforts to prevent organizational ossification. Drawing and elaborating on the analysis of âsmall winsâ offered by Karl Weick and Frances Westley (1996, 454â455), the significant benefits associated with continuous improvement can be detailed as follows:
Continuous improvement typically mobilizes large numbers of employees on behalf of organizational improvement in contrast to large-scale innovation efforts that often involve only selected experts. The contribution of such broad mobilization of employees is potentially large. As a corollary of these broad-based efforts, small wins in large systems can occur in parallel as well as serially, resulting in the aggregate, in large numbers of change efforts leading in turn to a magnification of results. A series of small wins often precedes and follows large changes, first paving the way for these changes by providing momentum and basic learning, and second by eliminating the impediments to optimizing the new processes or products. In this sense, small wins make large-scale change possible. Leonard Lynnâs study of the introduction of the basic oxygen furnace technology in steel making nicely illustrates this process (Lynn 1982). When many seemingly revolutionary changes are scrutinized, they are found to be based on a series of small wins.
Consider the revolutionary impact that the step-by-step reduction of machine setup times and die change times, pioneered at Toyota, had on changing the economics of small lot production in the auto industry (Robinson 1991, 85â86). By being anchored in current practices, small wins encourage learning that is rooted in daily work routinesâexactly the kind of learning that is most likely to be transformed into effective practiceâthat is, to be retained and institutionalized. This process is at the heart of the Brown and Duguidâs (1991) elaboration of how communities of practice lead to innovation. The potential for institutionalization is particularly large when the changes are implemented by the same people who proposed them. Small wins by disparate improvement groups are opportunistic and widely distributed. As such they represent uncorrelated probes in an evolutionary system.
This is a particularly valuable asset. The heterogeneous nature of these probes means that they are more likely to uncover unanticipated properties of the environment and promote beneficial learning. Probing and learning provide a valuable model of learning, problem solving, and improvement that is broadly applicable. Small process wins are often based on tacit knowledge that is not easily noticed and imitated by competitors. This contrasts with large-scale changes and product innovation, which are more likely to be based on explicit and codified language and available to competitors through reverse engineering. It is easier to sustain competitive advantage.