Waterproofing Case
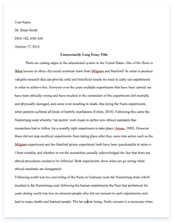
- Pages: 9
- Word count: 2111
- Category: Water
A limited time offer! Get a custom sample essay written according to your requirements urgent 3h delivery guaranteed
Order NowRainwater, in most cases, is the most pure available source of water, something which gives rainwater preference over other available sources of water but more importantly, roof drainage pollution is also caused by rainwater. In United States the average amount of rainfall across the country is 35″ and the amount of land that is affected by excess water capable of damaging homes and properties is around 20%. Some of the most common environmental and moisture problems that are faced by a modern day house constructors, by the weather and or climate and their suggested solutions shall be addressed by this report. Following important problem areas will be briefed, with main focus on waterproofing systems.
i. Lot drainage
ii. Management of gutter water
iii. Waterproofing of foundation
iv. Base waterproofing
v. Sump pumps
According to membership’s poll on Building Pathology of CIB Commission W86, among the problems of building pathology, water related problems are the most predominant. A leaky foundation present in a residential building can ruin the furniture, appliances and pose threat to the structure as well. In a commercial organization it can disrupt work processes and cause damage to expensive machinery or equipments. Moisture and water if present in and around residential dwellings pose continuous threat to the foundations of the house and upon neglecting, supports the growth of mildew within the house and wood eating fungus attacks in the foundation or the structural members. The need of proper residential drainage systems and application of waterproofing techniques is inevitable in such circumstances.
Historical background:
Paradoxically, the Hanging gardens of Babylon was first known waterproofing project designed almost 26 centuries ago, that anticipated the problems caused by excess waters (Henshell, 2000). The demand for a higher quality of waterproofing rose after Second World War as the rapid growth of air-conditioning industry made underground and windowless basements feasible as human residential places. Also the pre-World War construction involved traditional masonry walls capable of absorbing substantial amounts of rainwater and in a cyclical process of wetting and drying; they used to shed water by evaporation process. The masonry walls were however, replaced by the metal and glass panels with water shedding method via vertical flow, that is directly releasing to the foundation soil, leading to waterproofing problems at basement of the structures. The rapidly rising costs of the waterproofing failures accompanied a change in modern building trends. Extensive use of electronic equipments in underground basements, audiovisual equipment contained in public assembly spaces
Lot Drainage system:
To control the surface waters, every residential infrastructure must have a landscaping or grading system to direct the water drains to a collection point or a sewer to avoid flooding of the lot. The graded lot drains away the surface drainage from the melting of snow, groundwater and rainstorms from the foundation or the building in order to minimize the impact of these excess waters on adjacent properties. All owners of property are responsible for the proper grading of their lots to direct surface drainage towards the public right-of-way. In common practice the required grading is achieved by providing minimum 5% slope to the lot, as expressed in the Figure 1, which in turn would require the height if the foundation to be increased accordingly. Among the disadvantages of this system, the biggest is the requirement of complete reconstruction of the grading system of the lot.
Figure 1
Gutter Water Management:
For the prevention of excessive moisture, the roof and gutter water management is necessary. Usually, in a house, most gutters require inspection and accumulations removed on regular basis. For few types of clogging the gutter guard usage is partially effective. The minimum requirement of 5 feet from foundation walls is required for the discharge of roof drainage. The recommended method for the release of roof water is shown in Figure 2. For the conduction of water from underground point to a release point, a PVC plastic pipe can be used.
Waterproofing of foundation:
Besides burning down, the worst possible thing that can occur to a house or a building is foundation related problems. The foundation apart from providing support and stability to the building, the foundation is what keeps the structure where it was erected. The main source of majority of the problems that affects the foundation is water. The swelling of wet soil below a structure causes the foundation to lose its strength. That’s the main reason to keep the foundation isolated from water. Many waterproofing techniques and systems are deployed to keep liquid water and water vapor away from the concrete foundation.
As buying a home is a long term investment, to ensure it lasts long, the waterproofing products for the foundation of the house should be foolproof. Upon failure of waterproofing the moisture can freely penetrate through the foundation, cracks or any voids into the house. This can result in the growth of mold and mildew. It can also considerably lower air quality inside the structure eventually decreasing the house value.
Waterproofing Systems:
Based on different parts of a building’s structure, the waterproofing systems can broadly be classified among following categories.
Below-grade Waterproofing:
This type of waterproofing measures and products prevent underground waters and surface waters from penetrating into components of a structure and structure itself. These types of waterproofing materials include products that form plastic films, cementations’, bituminous waterproofing products. These types of waterproofing system are designed to bear hydrostatic pressures and usually are not subjected to weathering effects such as exposing to sunlight and other types of radiation.
Above-grade Waterproofing:
Combination of systems or products preventing the penetration of water into exposed elements of structures. These systems can withstand weathering but are not subjected to high hydrostatic pressures. Above-grade waterproofing products includes all kinds of plasters, paints and renders with very low water absorbing coefficients and with high vapor permeability.
Damp-proofing systems:
These systems are usually used as secondary systems to primary waterproofing materials. Damp-proofing systems prevent the transmission of water vapors or moisture in minor amounts. Damp-proofing is usually asphalt based coating less recommended in residential construction but accepted as a form of treatment in many cases. These materials are neither subjected to hydrostatic pressure nor weathering effects. Major drawback of damp-proofing is its inability to seal or patch larger holes and cracks
Roof Waterproofing Systems:
The roof waterproofing systems act as external layers and are used to prevent water intrusions in slightly graded directions and horizontal direction as well.
Liquid Membranes:
The liquid membranes are spray applied membrane with polymer-modified asphalt as main constituent. The liquid membrane can be applied by spray, roller or trowel to the foundation walls. Rubbery coating is formed on the wall when the applied liquid gets solidified. To treat voids, tie-holes and joints, the liquid membrane can be mixed with the cement or any trowel grade material to form a mixture before the application of the coating
The advantages of the liquid waterproofing include the quick application procedure, low cost and good elongation. The main disadvantage of liquid membranes is the non uniformity involved in application to the foundation walls. The recommended thickness of the coating should be 60 mils and all but a few applicators can manage the degree of preciseness that is required.
Sheet Membranes:
The most common sheet waterproofing materials consists of asphalt membranes that are self-adhering and rubberized which are laminated to a waterproof film of polyethylene. The asphalt side covered with paper is made considerably sticky and upon application the paper is removed. It can patch the damaged areas with number of layers as per the requirement. When applied poorly, a sheet waterproofing may have many seams with poor sealing capabilities.
The main advantage of sheet membranes is their consistency in thickness as they are manufactured with precise tolerances so 60 mils coverage can be made sure. Sheet membranes also possess good elongation. One of a chief disadvantage of sheet membranes is their higher cost. The cost of sheet’s material itself is usually greater as compared to the liquid membranes. Application cost is also higher because of the cutting involved, handling of the material, reinforcing and detailing processes involved during installation.
Cementitious Waterproofing:
Cementitious waterproofing membranes are used for protection of exposed structural components and buildings, to prevent long-term wetting from surface or seepage waters and to withstand low and high hydrostatic pressures as well. Due to their weather resisting ability, they can be used for exterior surface protection as well as in waterproofing of wet rooms or tanks. Many types of waterproofing membranes or slurries are available including standard rigid and flexible cementitious waterproofing (Lutz, 2005). Typical applications of cementitious membranes are waterproofing and sealing of e.g. toilets, bathrooms, water tanks, terraces and balconies, and swimming pools.
Moreover it is also used for the protection of structures of concrete after their rehabilitation process, and for new reinforced structures as well for resistance against the penetration of water, carbon dioxide and chlorides to prevent corrosion. Advantages of cementitious waterproofing include their resistance against excess water and long term weathering, higher load-carrying capacity compared to other waterproofing, excellent permeability to water vapors. Also the cement based waterproofing is non-toxic, can be applied on damp or wet surfaces, and compared to bitumen based products, cementitious waterproofing physical properties are less dependent on temperature. However, the disadvantage of using cement is that this waterproofing cannot tolerate any crack movements or joints as cement is incapable of stretching.
Bentonite waterproofing:
A clay material known as Sodium Bentonite has been enjoying the major preference from architects and builders over the past few years because of its property to absorb very high amounts of water. As it absorbs water, the clay swells up to 15 times of its initial volume and seals the cracks and joints by pushing itself into these gaps. Bentonite waterproofing comes in form of panels in the form of corrugated cardboard with clay particles held within the cardboard’s flutes. These panels can be applied with powder-actuated tool or can be nailed.
The only issue with bentonite panels is that, when using other waterproofing membranes, they can be inspected and integrity of seal can be confirmed before backfilling. But in case of bentonite waterproofing, the seal will not form until the water reaches the panel and foundation is backfilled. Apart from water absorbing and sealing ability, advantages of bentonite waterproofing includes the non-polluting nature, low labor cost can be applied on lower temperatures as well.
Injection Waterproofing:
Injection waterproofing is one of the most economical methods to repair the leaks exclusively for concrete foundations. This type of waterproofing is used where filling a crack or void in concrete will eliminate the threat of basement leak. Two types of low cost and durable injection waterproofing techniques were designed and adapted for use in waterproofing of residential basements.
i. Epoxy crack injection:
To fill a crack in concrete foundation, the crack is injected with a low pressure epoxy resin as shown in Figure which, when cured, bonds the cracks on both side with excellent bond strength (Aqua-guard, 2013).
ii. Polyurethane injection:
Also known as urethane injection, this type of waterproofing involves injection at higher pressures than an epoxy type. As shown in the figure the machine increases the pressure of the injection (Aqua-guard, 2013). Upon injection a non-toxic resin chemically expands within any cavity or crack. It also has lesser cure time than epoxy injection and therefore is used for rapid stopping of active basement leak
Global importance:
Excess water and moisture damaging the residential structure and the practice of application of waterproofing techniques have been followed from many years. The International Residential Code (IRC) has specified the terms and conditions of damp-proofing or waterproofing requirement by the structure in section R406. Foundation walls whether concrete or masonry “that retain earth and enclose interior spaces and floors below grade shall be damp-proofed from the top of the footing to the finished grade” (International Code Council, 2007). The list of permissible materials such as bituminous coating and acrylic-modified cement is also provided by IRC. The requirement of waterproofing by IRC is “in areas where a high water table or other severe soil-water conditions are known to exist” (International Code Council, 2007).
Waterproofing procedures:
Saving the labor cost can also be managed in the waterproofing process. Almost all the manufacturers of waterproofing products require a user to be a certified applicator before the installation is guaranteed. The user is certified by the manufacturer itself for a specific waterproofing product. Different application processes are involved by waterproofing products involve.
References:
http://www.clemson.edu/psapublishing/pages/FYD/HL252.pdf
http://www.lifeofanarchitect.com/residential-drainage/
http://www.cityoflakeforest.com/pdf/cd/drain.pdf
http://www.articlesbase.com/gardening-articles/solving-residential-drainage-pr
oblems-and-installing-residential-landscape-drainage-systems-throughout-the-houston-texas-area-693691.html
http://search.proquest.com.ezproxy.apollolibrary.com/docview/231109903/fulltext/13BCE10538A1A4C3AA5/6?accountid=35812
http://www.concretenetwork.com/foundation-waterproofing-drainage/dampproofing.html http://publicecodes.cyberregs.com/icod/irc/2009/icod_irc_2009_4_sec006.htm
http://www.mbam.org.my/mbam/images/MBJ3Q05pdf/@WATERPROOFING(72-76).pdf
http://www.aquaguardinjection.com
http://books.google.com.pk/books?id=i42c77dYETIC&printsec=frontcover&source=gbs_ge_summary_r&cad=0#v=onepage&q&f=false
http://search.proquest.com.ezproxy.apollolibrary.com/results/13BD2465C3664F9DBAD/1/$5bqueryType$3dbasic:OS$3b+sortType$3drelevance$3b+searchTerms$3d$5b$3cAND$7ccitationBodyTags:Cementitious+Waterproofing$3e$5d$3b+searchParameters$3d$7bNAVIGATORS$3dsourcetypenav,pubtitlenav,objecttypenav,languagenav$28filter$3d200$2f0$2f*$29,decadenav$28filter$3d110$2f0$2f*,sort$3dname$2fascending$29,yearnav$28filter$3d1100$2f0$2f*,sort$3dname$2fascending$29,yearmonthnav$28filter$3d120$2f0$2f*,sort$3dname$2fascending$29,monthnav$28sort$3dname$2fascending$29,daynav$28sort$3dname$2fascending$29,+RS$3dOP,+flags$3dFT,+chunkSize$3d20,+instance$3dprod.academic,+ftblock$3d1+660848+670831+194001+670829+194105+194000+660843+660840+105,+removeDuplicates$3dtrue$7d$3b+metaData$3d$7bUsageSearchMode$3dBasic,+dbselections$3dallAvailable$7d$5d?accountid=35812
http://www.credoreference.com.ezproxy.apollolibrary.com/search.do?query=Cementitious+Waterproofing&view=facet
books.google.com/books?id=i42c77dYETIC&printsec=frontcover&source=gbs_ge_summary_r&cad=0#v=onepage&q&f=true