TQM – Total Quality Management
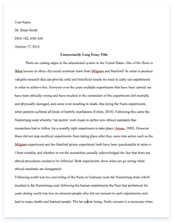
- Pages: 13
- Word count: 3180
- Category: Management Qualities
A limited time offer! Get a custom sample essay written according to your requirements urgent 3h delivery guaranteed
Order NowIntroduction
Recent years, quality and high standards in all spheres of business become the major concern of HRM. At the beginning of new millennium, TQM is used as a strategic weapon for control and high standards, improved quality and communication in organizations. The idea of this concept is to get products to a market faster, with fewer defects, and at a lower cost. TQM can be seen as a strategy which determines the direction and objective of the company.
There are different definitions of this concept, but the most exact and informative is proposed by Hill (1991) who explains that “top management determines quality priorities, establishes the systems of quality, management and the procedures to be followed, provides resources and leads by example” (45). Beckford (2002) sees TQM as a philosophy of work and “a way of managing, rather than an added extra, then other management philosophies, methods and tools must be subsumed within it” (117). In spite of benefits and opportunities proposed by TQM, some researchers (Antony, Preece, 2002; Beckford, 2002) underline that TQM cannot be panacea for all organizations aimed to improve their performance and standards of work.
Monitoring of the environment is an important method that helps to search for new trends and evaluate opportunities and threats of TQM for a particular business (Bishop, Daily, 2003). The issue of TQM is a topical one because in rapidly changing environment more and more companies and businesses need a strategy which covers the entire organization determining its strategic direction and development. The aim of the paper is to examine and evaluate the concept of TQM and its application to modern business environment.
Literature Review/Research from Sources
Two themes in the research literature have been particularly prominent in recent years: “the ways of improvement” as a source of service planning and the debate over the different methods and models of successful production techniques. Up-to-date scholarship on both of these themes is reflected in recent researches R.B. Chase, R.F. Jacobs (2003), N. Slack, S. Chambers, R. Johnston (2003), P. Dawson (2003) etc. In their studies these researchers develop a new theoretical approach which can be applied into practice. In their theoretical studies, the researchers provide a lot of example of quality control and TQM. These authors join theoretical and practical side of strategy, giving recommendations for improvement in management to ensure customer satisfaction.
They underline that quality begins and ends with marketing: once customer requirements are defined, a quick reporting process is needed, which should be maintained throughout design, specification, manufacture and inspection. A big layer of literature concerning TQM belongs to such guru as T. Hill “Production and Operation Management: Text and cases” (1991) and J.H. Mills (2003) “Making Sense of Organizational Change”. Their theoretical studies examining the concepts of TQM, quality control, the role of standards, etc. are the basis of any research in the field of production and operations management.
Recent years, there is increasing number of conferences and workshops aimed to familiarize diverse target audience with new developments in TQM and quality control. Today, a special attention is devoted to IT and the role of technology in TQM and quality circles, ISO 9001 and new regulations (TQM and Quality Assurance News, 2006). Taking into account events and issues discussed in 2006, it is evident that management is concerned about new technological changes and innovations in TQM.
They underline that a feedforward method can be seen as an important measure to ensure success of TQM projects. This is where monitoring at some early stage of a system or process may indicate that an adjustment should be made at a later stage of the process, prior to the final output. The issues of IT and their benefits for TQM lead to heated discussions and increased number of studies aimed to test and evaluate the role of new technologies in TQM. The main attention is given to the business level of strategy where the key question is “How can we compete effectively in this particular market with TQM?”
The most common generic strategies at this level are (1) become the low cost producer, (2) differentiate your product or service, and/or (3) change the scope of competition by either enlarging the market to include global markets or narrowing the market by focusing on small niches not well served by competitors. Another sphere of concern is staff and human capital which play a crucial role in TQM and quality control. Recent debates concern the role of managers who must deal with new people issues because the changes brought about by information technology and TQM principles definitely require a new kind of employee (TQM and Quality Assurance News, 2006; TQM Conferences, 2006).
The case studies suggest that almost all spheres of business benefit from the concept of TQM and quality control. Manufacturing and service companies, healthcare (Jasin et al 1998) and education (Sallis, 2002), public companies and government organizations implement the concept of TQM (or its elements) for quality control and high standards of performance. For instance, Richard H. Harris and Theodore H. Poister (1997) examined and analyzed the impact of TQM on highway maintenance. They came to conclusion that:
“PennDOT’s TQM activities in the highway maintenance area are associated with a 7 percent improvement in overall effectiveness over the long run, with benefits exceeding costs by 35 percent. … TQM activities can impact favorably on the bottom line of service delivery” (Harris & Poister, 1997: 298).
IBM, a leader in IT and software, provided analysis of the effectiveness of TQM and its benefits for software industry (Ferris et al 1998). This research proves that end-of-the-line monitoring needs to be replaced by a more effective method of quality monitoring. This can be achieved by the introduction of a Statistical Process Control technique which involves identifying all the processes in the organization and what the inputs and outputs are. Once the process is specified, the inputs and suppliers, and outputs and customers, can also be defined, along with the quality control.
The most interesting findings concern educational establishments and health care organizations implemented quality circles and just-in-time techniques (Jasin et al 1998). These studies prove that TQM is a concept which benefits different types of businesses with different organizational structures (Prasad et al 1999). These case studies show that central to the TQM approach is a need for a change in the attitude and culture prevailing within many organizations.
Organizations have to move away from the acceptance of defects and mistakes as if they are just part of life. Divisional, competitive structures within organizations need to be broken down and replaced with committed, co-operative relationships between all employees, who should see themselves as working towards the same goal. Linked with attitude change is the need to create a climate of continuous improvement (Sallis, 2002; Kanji, 2002; Mehrotra, 2006).
Community policy is another sphere of successful implementation of TQM techniques and tools. In community policy performance deficiencies can result from motivational problem which is closely connected with lack of skills. To improve this situation police officers need training taking into account rapid environmental changes. The purpose of training is to improve knowledge and skills. These concepts are applied to TQM where training can increase the confidence, motivation and commitment of staff; provide recognition, enhanced responsibility, and the possibility of increased pay and promotion; give a feeling of personal satisfaction and achievement, and broader opportunities for career progression; and help to improve the availability and quality of staff (Thurman et al 2001)
In sum, case studies and recent events depict the important role of TQM in business based on new technological development and new philosophy. These findings show that TQM is a topical issue which proposes great opportunities and benefits for modern companies and businesses in the period of globalization and integration. All customers have some expectation of the quality of the goods or services which have to be provided. Agreement should be reached within the organization based on the specification and high standards. Given an acceptable specification, customers will expect the product or service which is provided to conform to their needs.
Discussion
The concept of TQM is widely used in production and defined as a strategy which aims at improving a business’s effectiveness and flexibility, by eliminating waste so that results can be achieved quicker and more cheaply. Within production quality is seen as the responsibility of all employees. It is pursed through various methods that are intended to ensure consumer satisfaction.
One of the measures for improvements of the product is the original ‘zero defects’ program. It was established by the Martin-Marietta Corporation in the USA around 1962. It was introduced to augment the established statistical quality control program in order to try to improve product quality beyond that level which might economically be achieved by the statistical procedures. The program is in large part a ‘motivational’ device which sought to organize and motivate direct and indirect workers to achieve higher levels of quality in their work. The slogan ‘zero defects’ is an important part of this motivational exercise (Slack, Chambers, Johnston, 2003).
The main elements of ‘zero defects’ programs are: (1) a motivational package aimed at reducing individual operator controlled defects; (2) a prevention package aimed at reducing management controlled defects. This pack age centered around ‘error cause removal’ (ECR) suggestions to be made by employers for subsequent analysis and action by supervisors. These suggestions are submitted to the supervisor on ECR forms which defined the probable error cause and proposed action; (3) procedures to provide for prompt feedback to the worker (Slack, Chambers, Johnston, 2003).
Another measure of improvement is the quality circle approach to quality assurance. This approach was widely established in Japan before being adopted in Europe and North America. Wherever employed the QC approach rests upon the motivation of individuals and the organization of efforts to improve quality through error reduction, etc., and as such the procedure is designed to supplement conventional quality control procedure. A quality circle comprises a group of workers and supervisors in a single area or department which meets regularly to study ways of improving quality and to monitor progress towards such goals.
Most companies (Chandler , McEvoy, 2000; Antony, Preece, 2002) seek to establish quality circles largely on a voluntary basis. Those volunteering is often up to half of the direct and indirect workers involved in the activities of a particular department. They are offered training in the analysis and identification of quality problems and problem-solving procedures. Once this training is completed the circle is formed and is invited to tackle particular quality problems nominated by management or identified by the circle itself. Each quality circle normally tackle a series of projects, one at a time, identifying quality problems and means of eliminating such problems and establishing targets (often financial targets) to be achieved through quality improvement (Johnston, 2003).
It is necessary to underline that quality circles have some similarity to ZD programs, however, the former is essentially a group approach and the latter individual. The QC methodology probably requires considerable effort to establish and sustain, and it is perhaps for this reason many companies which have adopted the approach, have tended to concentrate on this one concept, rather than trying to sustain several different types of prograe or campaign.
One of the most popular methods is “Just-in-time” technique. “Just-in-time” has been defined as involving “the production of the necessary items in the necessary quantities at the necessary time” (Chase, Jacobs, 2003). Using this method the materials and items required by a process are made available at that process as and when they are required, and not before. This method is very effective because queues awaiting processing at an operation are minimal, but work-in-progress is low. “Just-in-time” is not the normal steady-state arrangement for an open rating system; it provides safety measures.
Given the uncertainty which exists in most operating systems, like uncertainties of demand, the processing times of particular operations, loss rates, etc., it has been quite common to build inventories into the system to provide some degree of safety. If an inventory exists between two processes then the failure of one does not immediately impact on the activities of the other. An inventory might also exist so that increases in demand can be met without the immediate need to change the rate at which the operating system works (Eboch, 1998). “Just-in-time” aims to create a zero or low inventory operating system. It is argued that the reduction in inventory is of considerable benefit in its own right (reduce space requirements, reduce the amount of tied-up capital, reduce the risk of loss and damage and reduce handling requirements).
The main contradictions of TQM and its implementation are that there is no a unified solution for all businesses and companies trying to introduce quality control and high standards. TQM does not guarantee a cost saving approach and benefits for companies fail to meet changing economic conditions and technology. In spite of great benefits and opportunities discussed by HR professionals, many TQM implementations fail because of different reasons. One of these reasons is that human function and staff is often neglected in the operational process of TQM.
The studies on this topic pay much attention to successful implementations of TQM, but do not explain the reasons of failure. Also, they do not see human resources as a major driven force of quality control, and for this very reason, diminish the role and impact of poor performance. Very often employees are neglected during the development stage of TQM, so they feel lack of motivation and lack of training which resulted in failure (Beckford, 2002).
From the standpoint of successful management, a need to minimize risks in TQM is urgent. A significant and disturbing feature of TQM is the negative attitude towards the benefits of TQM shown by many employees. Too often TQM is seen as a necessary expense to achieve output targets. It is not seen as providing long-term benefits or improving organizational performance. A common view of TQM is an activity undertaken by large corporate bodies who can afford it. The research by Bishop and Daily (2003) prove:
“managers should pay particular attention to the mediating role of teamwork on the effects that training and management support have on perceived EI success. U.S. business organizations spend over $52 billion per year on training, much of which has questionable effectiveness” (Bishop & Daily, 2003: 395).
In many firms TQM analysis is accompanied by the use of a variety of accounting ratios such as return on capital employed, profitability and so on. Different ratios have more relevance at different stages of the firm’s development than at others, so that while profitability may be appropriate for established firms, productivity and sales may be more useful for newly established companies and cash flows may be more significant when firms are in decline. At this stage, firms do not involve employees into TQM.
So, during implementation stage many employees do not understand the goal of TQM and cannot achieve results expected by the company. Some companies fail to meet requirements of TQM when one part of the system, technology, is improved to the detriment of other parts of the system. Researchers (Dow, 1999; Dawson, 2003) suggest that TQM plan should ensure that all resources would be maximally responsive to customer needs. Doing so requires a general understanding of consumer behavior; in addition, TQM must collect and analyze as much information as possible about the needs of each customer and prospect.
As it was mentioned above, TQM is not panacea for all problems and deficiencies faced by the companies today. Unique talents among employees, including superior performance, productivity, flexibility, innovation, and the ability to deliver high quality are ways in which people provide a critical ingredient in developing TQM. Successful TQM lies in responding to internal and external change. This involves the clarification of objectives, the specification of problems, and the search for and implementation of solutions. An understanding of how decisions are made helps in understanding change process and reduces the risk to fail.
Conclusion
In sum, TQM is an effective approach to quality improvements and high standards, but companies should pay a special attention to its benefits and threats. This means that managers must plan strategically both externally and internally and that internal strategic planning has to involve everyone in the workplace. Today, many firms and public organizations are finding out that managing for quality means more than just fine-tuning production controls.
This strategy can be applied to many spheres of business including education and healthcare, production and service markets. In general, TQM is an approach aimed at improving the effectiveness and flexibility of business as a whole and is aimed at eliminating wasted effort as well as physical waste, by involving everyone in the process of improvement; improving the effectiveness of work so that results are achieved in less time and at less cost.
References
- Antony, J., Preece, D. (2002). Understanding, Managing and Implementing Quality: Frameworks, Techniques and Cases. London: Routledge.
- Beckford, J. (2002).Quality. London: Routledge.
- Bishop, J.W., Daily, B.F. (2003). ‘TQM Workforce Factors and Employee Involvement: The Pivotal Role of Teamwork’. Journal of Managerial Issues, 15, 393-395.
- Chandler, G.N., Mcevoy, G.M. (2000). Human Resource Management, TQM and Firm Performance in Small and Medium-Size Enterprises. Entrepreneurship: Theory and Practice, 25, 43.
- Chase R.B., Jacobs R.F. (2003). Operations Management for Competitive Advantage. Hill/Irwin; 10 ed
- Dawson, P. (2003). Reshaping Change: A Processual Perspective. London: Routledge.
- Dow, D. (1999). ‘Exploding the Myth: Do All Quality Management Practices Contribute to Superior Quality Performance?’ Production and Operations Management, 8 (1) 1-25.
- Eboch, K. (1998). ‘The TQM Paradox: Relations among TQM Practices, Plant Performance, and Customer Satisfaction’ Journal Of Operations Management, 17 (1) 58-75.
- Ferris, S.F., Quint, R. Sant, R. (1998). ‘Financial Theory and Practice in the Application of TQM: The Case of IBM Rochester’. Journal of Managerial Issues, 10, 13-18.
- Harris, R. H., Poister, Th. H. (1997). ‘The Impact of TQM on Highway Maintenance: Benefit/cost Implications’. Public Administration Review, 57, 294-298.
- Hill, T. (1991). Production and Operation Management: Text and Cases, Prentice Hall.
- Johnston R. (2003). Cases in Operations Management, 3rd Ed. Pearson Education Limited.
- Jasin, M.M., Meacham, K.A., Alavi, J. (1998). ‘The status of TQM in healthcare. Health Mark Questions’ 15(3): 61-84.
- Kanji, K.G. (2002). Measuring Business Excellence. London: Routledge.
- Mehrotra, D. (2006) Applying Total Quality Management In Academics. http://www.isixsigma.com/library/content/c020626a.asp (accessed August 2006).
- Mills, J.H. (2003). Making Sense of Organizational Change. London: Routledge.
- Prasad, S., Tata, J., Thorn, R. (1999). ‘The Influence of Organizational Structure on the Effectiveness of TQM Programs’. Journal of Managerial Issues. 11, 440.
- Sallis, E. (2002). Total Quality Management in Education. London: Kogan Page.
- Slack N., Chambers S., Johnston R. (2003). Operations Management.FT Prentice Hall.
- Thurman, Q., Zhao, J., Giacomazzi, A. (2001). Community Policies in a Community Era. Los Angeles: Roxbery Publishing Co.
- TQM and Quality Assurance News. (2006). 2006http://www.qmi.com/news/industry/tqm/Default.asp?language=English (accessed August 2006).
- TQM Conferences. (2006) http://www.tqmconferences.com/ (accessed August 2006).