Total Quality Management Free
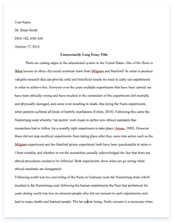
- Pages: 5
- Word count: 1202
- Category: Management
A limited time offer! Get a custom sample essay written according to your requirements urgent 3h delivery guaranteed
Order Now
Total Quality Management (TQM) is perceived as the totality of the efforts of an organization to aspire for quality for the purpose of satisfying customer needs. A review of related literature, however, revealed that until recently, this concept has been defined by several authors and researchers in different ways. In other words, while organizations agree that TQM basically involves product quality and customer satisfaction, it appears that unanimity in defining what TQM really means has not yet been reached.
It has been referred to as a method of management which encompasses an organization’s “culture, attitude and organization” aimed at ensuring customer satisfaction by emphasizing quality in every phase of an organization’s operations (Total Quality Management, n.d.). It has also been described as a method which combines management tools and employee involvement in a program of continuous improvement for the purpose of increasing efficiency (Hashim, n.d.).
Rue & Byars (2004), on the other hand, maintain that TQM does not simply involve methods or management tools but is in fact “a philosophy or way of thinking” which dominates the outlook of all members of an organization towards their jobs and the quality of their products. According to Rue & Byars TQM as a philosophy highlights the involvement of all employees from the highest executive down to the lowest ranked worker in an organization’s objective of achieving customer satisfaction. The Department of Trade and Industry of the United Kingdom, on the other hand, offered a far broader definition, stating that
TQM is the way of managing for the future and is far wider in its application than just assuring product or service quality – it is a way of managing people and business processes to ensure complete customer satisfaction at every stage, internally and externally. TQM, combines with effective leadership, results in an organization doing the right things right, first time.
Some researchers believe that the concept was perfected by the Japanese with the help of American experts sometime between the 1980s and the 1990s to make their products competitive in the market, particularly the American market, suggesting that TQM was not a Japanese creation (Richardson, 2005). While agreeing that the concept was not created in Japan but merely applied religiously by the Japanese, some quarters, however, believe that it was originally practiced in Japan earlier, during the 1950s. Industrial leaders of that country sought to institute reforms for the purpose of upgrading the quality of Japanese products which could not compete in the world market during the 1940s because they were then considered “cheap and shoddy” (History of Quality, n.d.).
These researchers claim that it was developed through the efforts of American quality experts W. Edwards Deming, Joseph Juran, and Armand V. Feigenbaum who were hired by the Japanese not only to guide them in upgrading the quality of their products but to assist them in coming up with innovative ideas as well. While their project initially dealt with issues involving product quality only, it later expanded to include the quality of work in all areas of operation (History of Quality, n.d.).
Still others insist that TQM as a concept of management traces its root in 1911 when Frederick Taylor published his Principle of Scientific Management whose objective was to provide industrial organizations with a much-needed framework for increasing productivity through the efficient and effective use of manpower. His concept was founded on the importance of product inspection to quality control by inspecting the finished products to prevent faulty products from leaving the production plant; and pay meticulous attention to detecting defects in the products; test the finished products to verify whether production complied with specified procedures (History of Quality, n.d.).
However, available literature reveals that Taylor’s treatise failed to catch the attention of industrial leaders who were concentrating on raking in the profits without genuine regard for quality. In the 1920s, an improvement to Taylor’s concept emerged in the Statistical Theory advanced by Dr. Walter A. Shewhart. This theory performed a significant role in product quality control. Dr. Shewhart showed, using a control chart which he developed, that any deviation occurring in the process of production results to variances and even defects in the finished products. He convinced industrial leaders through his statistical method of controlling quality that doing away with any deviation in their processes would ultimately result to high quality products (History of Quality, n.d.).
It was this theory of Shewhart that other experts like Dr. W. Edwards Deming, Dr. Harold F. Dodge, and Harry Romig later developed but was likewise ignored by industrialists. It was not until the Japanese industrialists sought the help of W. Edwards Deming, Joseph Juran, and Armand V. Feigenbaum in the late 1940s to show them how to manufacture high quality and innovative products that the importance of ‘total quality control” finally took center stage (History of Quality, n.d.).
Deming was later considered the brain of the post-war revival of the Japanese industry because it was his philosophy and the training that he provided the Japanese engineers and industrial leaders that transformed Japan into one of the leading industrial powers in the world. His philosophy was contained in his famous “14 Points” which explained how total quality could be achieved (Leadership Institute Inc., 2005).
The phrase “total quality management” surfaced during the 1980s. Following the example of Japanese companies, western organizations introduced their own version of quality schemes but instead of using the phrase “total quality control” they used “total quality management.” The phrase developed into a general term which referred to a broad range of activities involved in achieving quality. Typically, TQM is defined to include the elements of “customer focus, the involvement of all employees, continuous improvement and the integration of quality management into the total organization.” Unanimity as to what specific practices constitute total quality management was not achieved, however, until1988 when the United States government developed a clear model for total quality management that organizations should adopt. It was the granting of the Malcolm Baldrige Award that finally established specific criteria as to what should constitute total quality management in terms of the actual activities, policies and practices of organizations. This award was later replicated in Europe when the European Foundation of Quality Management held their own version of the European Quality Award in 1992 (History of Quality, n.d.).
References
Hashmi, K. (n.d.). Introduction and Implementation Of Total Quality Management (TQM).
Retrieved November 16, 2007 from
http://www.isixsigma.com/library/content/c031008a.asp
History of Quality. (n.d.). Business Performance Improvement Resource.
Retrieved November 16, 2007 from
http://www.bpir.com/total-quality-management-history-of-tqm-and-business-excellence-bpir.com-150.html#inspection
Leadership Institute Inc. (2005). Who is Dr. W. Edwards Deming? Retrieved November 16,
2007 from http://www.lii.net/deming.html
Richardson, T. (2005). TQM: Total Quality Management. Retrieved November 19, 2007
from http://www.witiger.com/internationalbusiness/TQM.htm
Rue, L.W. & Byars, L.L. (2004). Supervision: Key link to productivity (8th ed.). New York:
McGraw-Hill/Irwin.
Total Quality Management (TQM). (n.d.). Free Management Library. Retrieved November
16, 2007 from http://www.managementhelp.org/quality/tqm/tqm.htm
United Kingdom Department of Trade and Industry. (n.d.). Retrieved November 19, 2007
from http://www.businessballs.com/dtiresources/total_quality_management_TQM.pdf