The Kot Addu Power Company
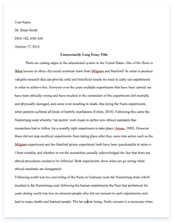
- Pages: 29
- Word count: 7012
- Category: Management Power
A limited time offer! Get a custom sample essay written according to your requirements urgent 3h delivery guaranteed
Order NowThe Kot Addu Power Company (KAPCO) runs a 1600 MW combined cycle Power plant at Kot Addu, a small town, in the middle of Pakistan. The company came into existence in the June of 1996 when the Water and Power Development Authority (WAPDA) the state run power generation utility of Pakistan, privatized the plant by offering 36 % stake to strategic investor “National Power” of U.K. along with management control. Kot Addu site is situated in District Muzaffargah, 100 KM north east of Multan on the left bank of river INDUS at a distance of 16 Km from TAUNSA BARRAGE. The area is surrounded by agricultural land stretched on the north and west side of Kot Addu. There are some adjacent areas covered with wind blown sand dunes which were formed with the passage of time. These sand dunes too are being gradually converted into agricultural land. Apart from above, there were very little educational facilities available in the area prior to setting up of this Power Station which has now almost been doubled and some of the School have been upgraded. The essential amenities are also now made available to the residents. Introduction to the Power House Complex
The complex comprises three blocks, 1, 2, and 3. Each block is independent in it and can be considered a separate power station. There are 2 combined cycle modules in each block no. 1 and 2 whereas block 3 has only one module. This is the physical distribution. For the commercial purpose the complex is divided into three blocks called Energy block 1, 2, and 3. The power purchase agreement provides different energy charges for the electricity generated and dispatched from each block. The energy block 1 (plant block 3) is the latest and was in commissioning stage when NP took over management in June 1996 whereas other blocks were completed and commissioned between 1986-1995.
The plant block 3, being latest, is the most efficient plant and provides the cheapest electricity to customer. Its total capacity is 397 MW. In order of priority, whenever there is generation demand from the customer, this block is run first. When the demand exceeds then only other plants are run. The complex history over past 4 years shows that plant block 3 runs round the clock throughout the year at maximum capacity. In case this plant can not run at full capacity due to any fault or break down of machines, the customer need is made up from other available plants that are relatively expensive but the customer pays lowest energy charges (of block 3) for the deficit generation. This results in significant loss. Therefore this block is the most valuable asset of the company. Heat Recovery Steam Generating System
The gas turbines, despite of their low installation cost, easy and speedy erection and high loading rate could not win the deserving popularity over the steam turbines due to the poor efficiency of the former. In the conventional gas turbine unit, substantial amount of heat energy was lost through the turbine exhaust gases which leave the turbine at about 580 Deg. Centigrade. To make use of this wasteful energy, an innovative concept of combined cycle plant, now has been introduced by the gas turbine manufacturers. Under this design, the exhaust of the gas turbine is made to pass through a conduction type boiler (commonly called as HEAT RECOVERY STEAM GENERATOR). High-pressure steam so generated is then used to run the steam turbine, which thus produces power without any fuel. This raises the plant efficiency to nearly 49 % against the 28 % of the conventional gas turbine. Agreements between WAPDA & KAPCO
WAPDA entered into an agreement with KAPCO for the purchase of the power for next 25 years from this plant. The tariff covered two kinds of payments viz. capacity and energy payment. The capacity payment is made on the available capacity of the plant and is mainly used by the company to meet the fixed expenses and 756 million dollar debt liability that it inherited from WAPDA. The energy payment is done on the actual dispatch from the plant. It covers the fuel cost and there is hardly and saving from this part. The agreement allows 36 complex days for the scheduled outages and 500 complex hours for the unscheduled / forced outages. In case the accumulated outage period over the year exceeds the agreed allowance, the company is liable to pay the liquidated damages at a rate of 1.6 times of what it gets as capacity payment.
The first year of the business went very well. WAPDA was prompt in making payments, but it did not lost very long. WAPDA as well as Govt. of Pakistan were in financial crises because of corruption and in efficiencies. Ultimately WAPDA engaged KAPCO and National Power in a complicated legal battle over the tariff issue by filing petitions in the high court. The court finally passed an interim order in October 1998 that restricts KAPCO to receive Rs. 1.98 per KWh of electricity. The objective behind this legal wrangling was to pressurize KAPCO / National Power to agree and out of court settlement for deduction of tariff. With the incoming of present Govt. the matters have been solved to fair extent. Organizational Structure
The powerhouse complex is spread over 280 acres. As stated earlier there are three independent blocks and each block is independent in itself. Each block has machines of different make where different technology is used. Production department operates the plant and maintenance departments are responsible for up keep of the plant through preventive maintenance, trouble shooting, and major / minor overhauling after predetermined period. At the face, it is a functional structure. The specialist functions like finance, IT, Personnel, Legal / Administration are common and provide service which Production and maintenance departments need to carry out their work. The production department has it own centralized structure. Each block has its separate maintenance department that is further subdivided into three sections with respect to functions Viz. electrical, mechanical, and ‘instrument and control’. A senior engineer head each function. Resident Engineer 1 heads block 1 maintenance department whereas resident engineer 2 is responsible for block 2 and 3 maintenance teams. However there is an additional position of Assistant Resident Engineer at block 3 who is responsible to resident Engineer. The senior engineer of this block report to both resident engineer and assistant resident engineer. Performance History
The project has performed well thought the period ever since it has been privatized i.e. June 1996. The contribution of block 3 in overall generation of the complex has been much beyond the satisfactory levels.
OBJECTIVES
The project has been completed to achieve the following objectives: a) To reduce mass scale load shedding.
b) To firm up Hydel Power Generation during water shortage period. c) To facilitate operation and maintenance of other power stations. d) To cover emergencies and power shortages with quick generation of power supply from this power station which is the salient feature of gas turbines.
OPERATIONAL STRATEGY
Corporate Strategy
Whatever the type of firm, top management’s responsibility is to plan the organization’s long-term future. Corporate strategy defines the business (es) that the company will pursue, new opportunities and threats in the environment. Also addressed is business strategy, or how a firm can differentiate itself from the competitors. Choices could include producing standardized products versus customized products or competing on the basis of cost advantage versus responsive delivery. Corporate strategy provides an overall direction that serves as the framework for carrying out all the organization’s functions. Strategic Choices
Corporate strategy defines the direction of the organization over the long term and determines the goals that must be achieved for the firm to be successful. Management sets corporate strategy by making three strategic choices: determining the firm’s mission, monitoring and adjusting to changes in the environment, and identifying and developing the firm’s core competencies. Application at KAPCO
Before the privatization the organization was working under WAPDA like a typical Govt. Organization and had no formal corporate strategy. However, after privatization in June 1996, the organization is working on the subject and a draft corporate strategy has been finalized. The strategy is being kept secrete at the moment and no further details are available.
MISSION
A firm’s mission statement answers several fundamental questions. An understanding of the firm’s mission helps managers enter ideas and design new products and services. If its mission is too broadly defined, the firm could enter areas in which it has no experience. If the mission is to narrowly defined, the firms could miss growth opportunities. This should also include the aspects like environment and core competencies. The management should be able to identify and deal with environmental changes when formulating mission statements. Application at KAPCO
The organization does not have any formal MISSION or VISION statement ever since its privatization. The employees in the organization just know that they have to work and produce electricity / power with minimum possible expenditure. In the process of the organization development an in formal Mission Statement has been devised which is kept forth for achieving the organizational goals. The proposed Mission Statement is as under: “KAPCO is an independent power produces that provides electricity for WAPDA distribution network. It will continue to contribute in the developing economy of Pakistan by maintaining its capacity and maximizing availabilities.”
CORE COMPETENCIES AND COMPETITIVE PRIORITIES
Core Competencies
Core competencies are organizational unique resources and strengths which management considers formulating strategy. These core competencies include:
1. Workforce
2. Facilities
3. Market and financial know how
4. System and technology
Competitive Priorities
A firm gains an advantage with its operating system by outperforming competitors in terms of one or more of these capabilities. There are eight possible competitive priorities for operations, which fall into four groups. Cost
1. Low cost operations
Quality
2. High performance design
3. Consistent quality
Time
1. Fast delivery
2. On time delivery
3. Development speed
Flexibility
1. Customization
2. Volume flexibility
A firm may organize itself into one or more operating systems, each designed to support a particular set of competitive priorities for a particular set of products or services. Application at KAPCO
Core competencies
Work force
A work force of approximately 800 to 900 hundred people is working in the organization in 4 technical shifts and 1 general shift as following: Technical shifts 3 x shifts work 8 hourly daily on rotational basis 1 x shifts remains at rest
General Shift for 8 hours on daily basis (from 0800 to 1600 hrs) Market and Financial know How There is no marketing department nor are there any competitor. The organization do not carry out any marketing function. However, a commercial and financial department exists. For the billing purpose formal financial procedures are adopted. System Technology
In the recent past the organization has installed new technology plant for power production. There are combinations of hybrid technology plants i.e. Gas and Furnace Oil combination, Gas and High Speed Diesel combination and Steam Operated Turbines. The company is also shifting their information system on the modern lines gradually. Competitive Priorities
Cost
All efforts at every level are directed to reduce the production cost. This is being achieved by the very extensive use of Gas Turbine plant i.e. block 3. Quality
High performance quality in the organization is referred as efficient use of plant i.e. with minimum cost maximum output. Time
The aspect is of utmost importance. Priorities like Fast Delivery and On Time Delivery are applicable as the company is producing required amount of voltage at prescribed timing with complete accuracy. Flexibility
There is no concept of flexibility, which is being implemented. The company is rather tied up with the strict schedules of using various plants. Strategy Based On Flows
These are five fundamental manufacturing and service strategies based on flows are: 1. Make-to-Stock Strategy
2. Standardized service strategy
3. Assemble-to-order strategy
4. Make-to-order strategy
5. Customized service strategy
Application at KAPCO
No concept of strategy based on flows is being followed / observed in the organization. However, all production is being done on the orders / demand received from WAPDA. One may say that make to order strategy is being follows for production of electricity.
DECISION MAKING IN OPERATIONS
Operations managers make many choices as they deal with various decision areas. Although the basic steps includes: 1. Recognize and clearly defined the problem.
2. Collect the information needed to analyze possible alternatives. 3. Choose and implement the most feasible alternative.
Sometimes hard thinking in a quiet room is sufficient. At other times reliance on more formal procedures is needed. Various methods used are break-even, preference matrix, decision theory and decision tray. Application at KAPCO
None of the above method is being implemented by the company for estimating demand. The demand is received directly from WAPDA (The only customer of the company) and company produces power / electricity accordingly.
WORKFORCE MANAGEMENT
Team
Employee involvement, also called worker participation or labor-management joint-ness, is a key tactic for improving competitiveness. One way to achieve employee involvement is by the use of teams, which are small groups of people who have a common purpose, set their own performance goals and approaches, and hold themselves accountable for success. Teams differ from their more typical “working group” because: The members have a common commitment to an overarching purpose that all believe in and that transcends individual priorities. The leadership roles are shared rather than held by a single, strong leader. Performance is judged not only by individual contributions, but also by collective “work products” that reflect the joint efforts of all the members. Open-ended discussion, rather than a managerially defined agenda, is prized at meetings. The members of the team do real work together, rather than delegating to subordinates. Employee Empowerment
The three approaches to teamwork most often used are problem solving teams, special purpose teams, and self-managing teams. All three use some amount of employee empowerment, which moves responsibility for decision farther down the organizational chart – to the level of the employee actually doing the job. Application at KAPCO
Generally the concept of problem solving team or special purpose team exist in the organization culture. This is more evident when major overhauls of the plants are done. Individuals are made responsible in different teams (each selected from respective shift) for specific jobs. However, the culture needs definite improvement. TRAINING
In a global marketplace, firms face changing market conditions brought on by new competitors and changing customer preferences. Firms must rely on their employees to anticipate possible problems, develop new products and services, and increase productivity to remain competitive. The emphasis on efficient process requires the employees have a broader base of skills so that they can take on greater variety of assignments and communicate with employees in other areas. Firms engage in a variety of training programs, including the following: Global training
Administrative training
Technical training
Application at KAPCO
Although the company does not have any competitors yet the company face a grate a most of electricity demand from WAPDA. To this demand a highly skilled personal, (specially Engineer) are required. As the project kept on developing in phases i.e. from 1984 (1st phase) to 1992 (last phase), To improve the skill and update the technical know how of the working staff for the new machinery, a training program was launched right from the beginning of the project. As a result of this a number of station engineers received foreign training in different fields. Entire program of training to different categories of staff was out in five Phases. Phase I
As per contract agreement 7 engineers were trained in Germany and 9 in Italy. The training was conducted at the training center / factories of the machine manufacturers. Besides the above one months local training was also imparted to the staff at site. Phase II
Under this phase 30 engineers received training in the field of operation and maintenance of plant. The training was arranged in France. A local training was also arranged at site for the staff where operation and maintenance of the gas turbines unit 5-8 was taught for a month. Phase-III
For the combined cycle plant unit Forty engineers were trained in Germany. Locally the operation and maintenance staff for these units was trained at site by the foreign expertise for a period of 24 weeks. Phase-IV
For operation and maintenance of steam turbine units 11&12, Twenty engineers received foreign training in the relevant field. Training was imparted at France. In addition to the foreign training, a local training was also imparted by foreign experts to the operation and maintenance staff. A batch of 20 officials attended the course. Phase-V
15 engineers were sent to Germany under this phase. The participants of this course received training in the field of Electrical, Mechanical and I&C maintenance of power plant. A multi field training course, covering a span of 13 weeks was arranged at the plant for local training of staff. About 50 persons availed this training to get acquaintance with the new machinery. Capacity
Capacity is the maximum rate of output for a facility. The facility can be a workstation or an entire organization. The operations manager must provide the capacity to meet current and future demand; otherwise, the organization will miss opportunities for growth and profits. Capacity plans are made at two levels. Long-term capacity plans. These plans cover at least two years into the future. Whereas, short-term capacity plans focus on work-force size, overtime budgets, inventories, and other types of decisions. Capacity Planning
Capacity planning is central to the long-term success of an organization. Too much capacity can be as agonizing as too little. When choosing a capacity strategy, managers have to consider questions such as the following. How much of a cushion is needed to handle variable, uncertain demand? Should we expand capacity before the demand is there or wait until demand is more certain? Measures of Capacity
No single capacity measure is applicable to all types of situations. Output measures are the usual choice for line flow processes. Input measures are the usual choice for flexible flow processes. Peak Capacity
The maximum output that a process or facility can achieve under ideal conditions is called peak capacity. Peak capacity can be sustained for only a short time, such as a few hours in a day or a few days in a month. A firm reaches it by using marginal methods of production, such as excessive overtime, extra shifts, temporarily reduced maintenance activities, overstaffing, and subcontracting. Effective Capacity
The maximum output that a process or firm can economically sustain under normal conditions is its effective capacity. In some organizations, effective capacity implies a one-shift operation; in others it implies a three-shift operation. Steps Determining Capacity Cushions
Businesses find large cushions appropriate when demand varies. Large cushions also are necessary when future demand is uncertain. Another type of demand uncertainty.
Supply uncertainty also favors large capacity cushions. Small cushions have other advantages; they reveal inefficiencies that may be masked by capacity excesses-problems with absenteeism, for example, or unreliable suppliers. Once managers and workers have identified such problems, they often can find ways to correct them. Application at KAPCO
Power Generation
Peak Capacity
Peak capacity of the project is 1600 MW which is achieved through combined cycle power plants. Effective Capacity
Effective capacity of the plant is 1340 MW at any instance during the entire year. According to the contract the company is bound to provide same amount of power i.e. 1340 MW (equal to effective capacity for the next 25 years to WAPDA) Although the demand for power supply is received from WAPDA is any instance during the year. However as a process 95 days before the commencement of the next year, average ten ta demand is received in giga watts / hrs from WAPDA. Basing on this forecast capacity planning by the company is done. Brief calculations for generation of capacity is as following: 1340 MW x 365 days x 24 hrs = 11738400 MW hrs
11738400 / 1000 = 11738.400 giga watts hrs
Thus total generation capacity per year is = 11738400 Giga watts hrs Capacity cushion
Keeping in view the unscheduled break downs, prolonged scheduled shut down for maintenance / overhauls WAPDA has given a cushion of 670 Giga watts hrs to the company. The calculations are as under: Cushion in terms of time = 500 complex hrs
= 500 hrs x 1340 MW hrs = 670000 MW hrs
By dividing with 1000 = 670000 / 1000 = 67 Giga watts hrs
Company must try and maintain the unscheduled breakdowns and forced outages within this specified capacity cushion of 67 gigal watts hrs. Contrary the company has to pay liquidation charges to WAPDA. In case company maintain and efficient work standard and provide required capacity of power to WAPDA those grace has (670 MW hrs) are kept in reserve for the company which it can utilize during major overhauls which normally exceeds the prescribed time limit for one or the other reason. Liquidation Damages
In case company is unable to provide required capacity of power to its customer WAPDA and over utilizes the grace capacity of 670 MW hrs. then the company is bound to pay liquidation damages to WAPDA at a rate of 160% or 1.6 times.
LOCATION
Facility Location is the process of determining a geographic site of a firm’s managers must keep in minds various factors. Desirability of a particular site including proximity to customers, suppliers and transportation cost are important. Managers can divide location factors into dominant and secondary factors. Dominant factors are those derived from competitive priorities (cost, quality, time, and flexibility) and have a particularly strong impact on sales or costs. Other factors may need to be considered, including room for expansion, construction costs, accessibility to multiple modes of transportation, the cost of shuffling people and materials between plants, insurance costs, competition from other firms for the work force, local ordinances (such as pollution or noise control regulations), community attitudes, and many others. Application at KAPCO
In site selection following factors were kept in view.
Existing PARCO facility for transportation of HSD from Karachi to Mehmood Kot, which is about 35 km from Kot Addu. From Mehmood Kot, a 10 inches diameter pipeline has been to laid this power station and HSD pumping was commissioned in June 1989. (Later on it has been switched over to furnace oil since 2nd Feb. 1991.). Sweet under ground water
Future load center of north west areas
Possible use of gas from nearby Dhodak Field
Near to Kot Addu junction Railway Station
To provide job opportunity to the Location
General uplift and development of area.
Layouts
Layouts’ planning involves decisions about the physical arrangement of economic activity centers within a facility. An economic activity center can be anything that consumes space. The goal of layout planning is to allow workers and equipment to operate most effectively. Before a manager can make decisions regarding physical arrangement, four questions must be addressed. 1. What centers should the layout include?
2. How much space and capacity does each center need?
3. How should each center’s space be configured?
4. Where should each center be located?
The location of a center has two dimensions: (1) relative location, or the placement of a center relative to other centers, and (2) absolute location, or the particular space that the center occupies within the facility. Application at KAPCO
Layout of the company was although initially planned by WAPDA but basic considerations of expansion and keeping the various block and storage locations well within the reach of each other were kept insight. Initial location of the plant which were constructed in 1985 facilitated the gradual development of the site till project completed in 1992. Forecasting
A forecast is a prediction of future events used for planning purposes. Forecasts are needed to aid in determining what resources are needed, scheduling existing resources, and acquiring additional recourses. Accurate forecasts allow schedulers to use machine capacity efficiently, reduce production times, and cut inventories. One of the biggest challenges in business is forecasting customer demands. It is a difficult task because the demand for good, and services can very greatly. Forecasting demand requires uncovering underlying patterns from available information. Application at KAPCO
Power Demand Forecasting
KAPCO does not carryout any forecasting for the demand from its customer WAPDA. It is rather customer by itself forward the demand. The demand from WAPDA is received five yearly, yearly, monthly, weekly and even daily i.e. A day ahead. As regard demand from WAPDA is concerned at times it is received right when required that even the demand received it is always unpredictable and tentative because of the typical requirement and technology involvement. Forecasting for Major / Minor Overhauls and Maintenance
Basing on WAPDA’s demand and running records of the various plants and personnel experience of the engineers forecasting for the overhaul minor maintenance and schedule outages is done by the company. A very comprehensive procedure is being adopted for scheduled outages which are the major events for the company ( as these outages has direct bearing on the overall efficiency of the company).
INVENTORY MANAGEMENT
Inventory Management is an important concern for managers in all types of businesses. For companies which operate on relatively low profit margins, poor inventory management can seriously undermine the business. The challenge isn’t to reduce costs or to have plenty around to satisfy all demands, but to have the right amount to achieve the competitive priorities for the business most efficiently. Application at KAPCO
Inventory of Outputs
There is no inventory for the power which is being produced by the company. Whatever power / electricity is generated transmitted simultaneously to its customers. Inventory of Inputs
A huge inventory is maintain for various inputs i.e. Furnace Oil, High Speed Diesel and Spears. National Gas
No inventory of the natural gas is maintained. The gas is coming directly from SNGPL company and is used in the plants. There are no storage of the gas at location SNGPL daily provide 70 million cubic feet of gas to the company for 8 months i.e. from 15 March to 15 November. If this amount of gas is not received KAPCO charges liquidation damages from SNGPL Ltd. Furnace Oil and High Speed Diesel Inventory
An inventory of 21 days requirement of Furnace Oil and High Speed Diesel is maintain always in the company. Quarterly demand is sent to Pakistan State Oil (PSO) 44 days in advance. This demand is based on WAPDA’s requirement of power which is received 46 days before the start of the quarter. These supplies are kept in storage tanks at location. The company has 27 tanks each having capacity of 8,000 metric cubic oil. PSO is the only supplier and there are no problems on supply. Spares Inventory
Minor maintenance scheduled outages for major overhauls, unscheduled outages and washing outages requires availability of huge amount of spares round the clock at location. All the spare parts are imported. Therefore, to meet emergent needs spare parts are kept in stock for worth Rs. 2 billion. In addition a huge numbers of spare part are imported keeping JIT system in vogue. Inventory Review
Periodic inventory review (monthly basis) is conducted in the company.
QUALITY MANAGEMENT
Quality can be defined in a various ways. In a general sense, quality may be defined as meeting or exceeding the expectations of the customer. For practical purposes, it is necessary to be more specific. Quality has multiple dimensions in the mind of the customer, and one or more of the following definitions may apply at any one time. Quality can be defined in terms of: Conformance and specification
Value
Fitness for use
Support
Psychological impressions
One of the important element of quality (TQM) is employees involvement in totality. Good quality or total quality can pay off in terms of high profits. The new and latest concept of quality is continuous improvement or exceeding the level of customer’s satisfaction. Application at KAPCO
In KAPCO the concept of the quality is followed but in slightly different form. Instead achieving customer satisfaction or exceeding the level of customer satisfaction the organization measure quality in following terms: Display of best efficiency in running the Furnace Oil / HSD plants, Gas Turbine Station, Heat Recovery Steam Generators and Boilers. Least utilization of raw material i.e. Furnace Oil, HSD. Their priority remains to use gas and steams. Excellent maintenance mechanism.
No line losses
No unscheduled outages
No extra tripping out
Maintenance of regular operations
Quality is also measured in terms of:
Preventive Maintenance
Break down maintenance
Condition based Maintenance
Pro-active maintenance
ISO 9000 Certification
The company, does not have any certification from international standard organization. Monitoring Quality
Quality is monitored through National Power central station at Islamabad. The company has direct Hot Line (electronically controlled) as well as a special monitoring system called SCADA. Any break down, fluctuation and tripping is monitored at National Power Central Station Islamabad. This contributes to the overall quality / efficiency of the organization. It is from this station that various demands are placed and in-turn plants are operated. The best measure of the company’s quality is to have the least or No liquidated damages during the year. Since there are no threats to the company from the market, other competitors, threats of raw material, gas or HSD the company maintains high standard of efficiency. Thus achieve required quality. Another important quality measure is to maintain 1340 MW
hrs output throughout the year. This standard is expected to last for the duration of contract of 25 years ever since its privatization. Quality Policy
An explicit quality policy does not exist. In last three years many procedures, local management instructions have been issued and operational procedures defined from time to time The quality policy for KAPCO is defined as:
The company business is to generate and sell electricity to its only customer “WAPDA” as and when it demands. Therefore quality for KAPCO means, “Meeting agreed WAPDA’s requirements”. This is possible by maintaining the reliability and performance of the plant at minimum cost but with care for people, plant and environment.
SCHEDULING
Scheduling allocates resources over time to accomplish specific tasks. Normally, scheduling is done after many other managerial decisions have been made. Sound scheduling can help an organization achieve its strategic goals. Operational scheduling focuses on how best to use existing capacity, taking into account technical production constraints. Application at KAPCO
Work force Scheduling
There are two types of workforces:
1. Direct Employees.
Those who work in the energy blocks and on plants and boilers. 2. Indirect Employees
Those who work for general duties other than the energy blocks. The organization has 3 x shifts of 8 hours working daily, whereas 1 x shift remains on rest for 6 days. General shift works for 8 hours daily. Operational Scheduling
This is one of the best application being applied in the company. In operational scheduling major outage plans for the next 5 years are scheduled. Basing on this 5 year planning annual plan is made and approved from WAPDA. Normally outages are scheduled from July to November which is low period for the Thermal Power Stations. This scheduling process includes: Scheduling for outage starts 18 months before when a particular plant is indicated for major overhaul. 15 months before the commencement of the project the purchase requisitions are sent to the purchase department. It takes 3 months to receive the quotations.
12 months before the start of the project of the overhaul or scheduled outages the final demand is placed to the suppliers by the purchase department. 1 to 2 months before the start of the project spares are received at location. (Since the spares are imported from abroad therefore a cushion of 1 to 2 months is kept for negotiating the hurdles of the process). Many major items are received just in-time (JIT) as well. All prose and cons of the shipment of material either by air or by sea are considered and efforts are made to have the least possible cost with best possible delivery means at due time. Shut down Scheduling
There are three types of scheduling for shut down as following: 1. Scheduled outage or planned outages.
2. Unscheduled outages or forced outages.
3. Washing outages for gas turbines
Following parameters are kept in view for scheduling of various types of outages discussed above. 1. For scheduled outages WAPDA gives 36 complex days for each machine. 2. For major overhauling 50 to 60 days at average are preempted by WAPDA for each machine. 3. For hot gas path inspection 30 days are given.
Basing on above parameters formal scheduling of shut down is made on annual basis. This scheduled plan is approved by WAPDA and the maintenance are under taking accordingly. Schedule For Cranes And Lifting Equipments
Schedules for cranes and lifting equipment have been developed very recently for the first time. Inspection of these items is in progress nowadays through an independent agency. Identification no is being punched on each equipment. In addition red color market is also being put on tested equipments.
DISTRIBUTION OF POWER
Application at KAPCO
Power Transmission
For export of electric energy, this station is equipped with a two level (132 KV & 220 KV) switchyard. Six machines (Unit No. 1, 2, 3, 4, 9 to 10) of the plant are connected with the National Grid through 132 KV swithcyard whereas the remaining nine machines (Unit No. 5, 6, 7, 8, 11, 12, 13, 14 & 15) terminate at 220 KV Switchyard. Four auto transformers further provides an interlink between the two switchyards thus the system flexibility for power transmission of all the machines is enhanced. The power generated by this station is transmitted to the National Grid through network of ten lines as detailed below: Line 1: KAP 4 —- 132 KV, 100 MW. Industrial State, Multan Line 2: KAP 5 —- 132 KV, 100 MW. Muzaffar Garh I
Line 3: KAP 6 —- 132 KV, 100 MW. Muzaffar Garh II
Line 4: KAP 7 —- 132 KV, 100 MW. D. I. Khan I
Line 5: KAP 8 —- 132 KV, 100 MW. D. I. Khan II
Line 6: KAP 9 —- 132 KV, 100 MW. Kot Addu
Line 7: Multan I —- 220 KV, 250 MW. New Multan I
Line 8: Multan II —- 220 KV, 250 MW. New Multan II
Line 9: Multan III —- 220 KV, 250 MW. New Multan III
Line 10: Multan IV —- 220 KV, 250 MW. New Multan IV
SUPPLY CHAIN MANAGEMENT
Supply chain management seeks to synchronize a firm’s functions and those of its suppliers to match the flow of materials, services and information with customer demand. a basic purpose of supply chain management is to control inventory by managing the flows of materials. Application at KAPCO
The KAPCO has an efficient supply chain management system for provision of Natural Gas, Furnace Oil, HSD and Spares. As regard gas it is directly coming from the SNGPL Ltd. to the plant on daily requirement basis. A minimum and maximum requirement levels have been finalized with SNGPL Ltd. by the Government on permanent basis. In case SNGPL Ltd. does not meet the requirement liquidated damages are charges by KAPCO. For Furnace Oil and HSD the contractor is PSO. The demand is placed 44 days in advance of the requirement on quarterly basis as the oil had to be transported from Kamari to Lal Pir and then to KAPCO location. A special 59 Km long pipeline has exclusively been laid from DHODAK to KAPCO for provision of Furnace Oil. This meets the major supply for the company’s requirements.
Aggregate Planning
Application at KAPCO
As such no formal aggregate planning is done in the company. However the company has a performance section, which maintain all records on day to day basis. Physical coordination of various executives is done very frequently. Meeting are held quite often. Commercial and performance manager, 2 engineers, Computer qualified staff, billing staff and HR staff monitor aggregate operations and insure followings: 1. Liquidated damages (if any) are reduced to minimum.
2. company must generate power to its requires capacity and demand, with minimum possible cost.
FINANCIAL IMPLICATIONS
Application at KAPCO
A formal finance / billing section exists in the company. It ensures the billing is done to the customer (WAPDS) on monthly basis according to the contract and power provided. At the same time it maintain all bills received from suppliers and make necessary arrangements and adjustments of payments. In this connection following parameters are kept in view by the department: Prices of the Furnace Oil, Gas and HSD were kept as the base and energy charges were decided. The bills are made accordingly. With the increase or decrease in prices the rates are automatically adjusted with the same ratio. This work is efficiently being performed by finance department. Bills for the raw material are also prepared and paid according to the contracts deeds.
INFORMATION SYSTEM
Information is one of the most important corporate assets but, to unlock real value you need to ensure that it can be easily retrieved, managed and shared. The IT system recently installed at KAPCO fulfils the requirements. More than 120 officers / engineers have been provided with the network computers and are connected with each other through a server installed at a central place. The most modern computer aided maintenance management and stock control system has also been installed and made accessible for all the users. The documents and other forms of information can be scanned and converted to electronic form. From any workstation, user can retrieve documents rapidly, review or annotate them, communicate to other people for comments or approval and incorporate the information into other popular business applications.
EXECUTIVE SUMMARY
Until 1996, Government of Pakistan had monopoly over power generation and transmission all over the country. Government ran this business through State owned “Water and Power Development Authority” (WAPDA). In 1996, the then Government decided to privatize WAPDA in different stages. because of excessive in-efficiencies in the operation of WAPDA’s and to encourage in-ward investment into Pakistan. Kot Addu Power Company came into existence in June 1996 when the Government privatize its 26 % shares to National Power England through open bidding with an option to purchase another 10 %. This 10 % was purchased by National Power England. Therefore, in June 1996 a new company named “Kot Addu Power Company” came into existence. The power complex is spread over 280 acres of land. It has three independent blocks and each block has machines of different make where different technology is used. Production department operates the plant and maintenance department is responsible for up keep of the plant through preventive maintenance, trouble shooting and major / minor overhauling after predetermined period.
Forecasting of the company is entirely dependent upon the forecasting received from WAPDA. Mainly forecasting is done for various maintenance operations. Forecasting is also done for the provision of raw material supplies i.e. Furnace Oil, High Speed Diesel and Spare Parts for the plant machinery. The company maintains an inventory of 21 days for Furnace Oil and High Speed Diesel. It also maintain a huge inventory of spare parts. A fairly good Supply Chain Management System exists within the organization. The company’s basic business is to produce required amount of power according to the customer demand with No liquidated damages. The company believes in quality by maintaining high efficiency level of its operations. There are no ISO 9000 certification obtained by the company. The company is shifting its existing manual information system to modernized information technology based system in which approximately 120 new computers along with a server had already been installed. In this report a detailed analysis of various operations management procedures has been carried out. This analysis provides an opportunity to look into the organizational functioning of KAPCO deeply.
ACKNOWLEDGEMENT
To start with, I with my all humility convey, my sincere thanks to GOD the ALMIGHTY for having granting me the Wisdom and energies to complete this assignments with in the stipulated time. In the process of the preparation of report I required lot of guidance and directions. I could receive these from highly learned, experienced and most elegant personality Dr. Hayat M. Awan. Let me admit openly that without his dedicated guidance, most useful advises and wholehearted assistance the task was uphill. I have learnt a lot and added to my experience during this process. I extend my deep gratitude and most sincere thanks to him. I also extend very sincere thanks to the following executives of KAPCO who have really provided me with the most useful information about the project. Mr. Nisar Asim Ex. General Manager
Mr. Amjad Ali Sheikh Resident Engineer (Opeartions)
Mr. Muhammad Yasin Manager Human Resources
I am also thankful to all others who assisted me in completion of this report. Author
Preface
To become an expert in any field, only theoretical knowledge does not provide a concrete base. This is a unique approach of business education that provides an opportunity to the students to observe daily life business practices and problems. Operations Management is one of the core subject of MBA Program that gives us an idea as to how the various aspect of operations are dealt in the different organizations. Therefore, the study of this subject is incomplete without observing the applications in the real working environment. During the process of study, I made a couple of visits to meet with the executives of KAPCO. A formal questionnaire was prepared before the discussions were made with the General Manager of the Organization and Resident Engineer (Operations). A very informative, exhaustive and valuable material has been collected during the discussion with experts. All this prove to be an effective source of learning.