Supply Chain Mapping
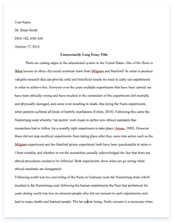
- Pages: 7
- Word count: 1628
- Category: Management
A limited time offer! Get a custom sample essay written according to your requirements urgent 3h delivery guaranteed
Order NowSupply chain mapping is an analytical tool used in process management and strategic SCM. It is a conceptual map which clearly identifies critical parties or players in the supply chain and relationships between them. It also represents the flow of materials, cash and information throughout the chain. It can identify bottlenecks, suppliers, logistics coordination, potential competitors, opportunities, overlaps and duplication of effort and resource. A strategic supply chain map is created first which represents overall company strategy depending upon company’s value, goals. After that process map is completed by an organization. A complete map can be used to evaluate and monitor the effectiveness and efficiency of the process. Many organizations and companies are using the supply chain mapping as an important tool to assess risk before making any strategic decision in supply chain.
Purpose of this Map, Problem and Usefulness of Map
I am working in a real estate rental and construction company. It has over 35300 suites in 225 properties across 5 provinces in Canada. Mission of our company is to serve and provide our Resident Members (RM) with quality rental communities. The above mission statements govern the decisions and policies of our company makes and determine the way we treat each other, our associates, our resident members and our communities. We are providing repair and replacement services within 72 hours. To provide multi dimensional services to the RM as quick as possible the supply chain management department is working efficiently. It contributed to our company’s ability to compete and differentiate itself from others in the real estate market and placed our company among top five companies. It appeared from the performance evaluation analysis for the year 2012 that it took much time and money towards repair and maintenance of Heating Ventilation and Air-conditioning (HVAC) system especially in Edmonton area in Alberta province. Most of the time taken by the contractors to search and collect spares and the cost of services also charged much higher.
Through a management decision a Preventative Maintenance (PM) department was established in 2013 to reduce the use of contractors by June 2014. From July 2014 PM department took over all repair jobs. To facilitate quick repair they forwarded a list of inventories to all sites with a request to order and maintain those inventories at all times. In September 2014, the finance department informed the management that the yearly repair and maintenance budget in Edmonton area is exhausted and requested additional budget for remaining three months of the year. The purpose of this supply chain process mapping was to clearly identify critical parties/players in the supply chain, relationships between them, flow of materials, bottlenecks, review the decision taken for change, logistics coordination, opportunities, overlaps and duplication of effort and resource. At the end to identify the support for further decision making.
The supply chain process mapping was created, reviewed and analysed. Analysis shows that all 17 areas were requested to order and maintain excessive inventories, lack of detail plan by the PM dept and unrealistic supply chain coordination in this area has contributed to this problem. Salaries of 7 members of PM team, their tools and cost of vehicles added overhead cost. Management decision to establish a PM department was found justified but implementation was not done correctly. There was no monitoring system in place and supply chain management department was not consulted. Details of analyses are presented with facts and figures. Recommendations are made to redesign logistics supply and work process of PM dept which will reduce time and cost of repair and maintenance of HVAC system.
The Supply Chain Process Map of Our Company
(Represent 1 out of 17 areas in Edmonton)
It is stated before that my company has 226 properties in 5 provinces across Canada. Two or more properties are grouped together depending upon their size and location. Each site has a unique name, maintains inventories and a maintenance team. Few sites are grouped together called area and placed under one area leader. In Edmonton there are 17 areas with 17 area leaders. There is a large company warehouse located in Edmonton works directly under the direction of Supply Chain Management (SCM) department at head office in Calgary. Figure -1 below represents the typical supply chain process of map only one area out of 17 areas in Edmonton. Warehouse receives inventories from companies (process A and path D) and wholesalers contracted by SCM dept. Site orders required inventories through area leader (process E) and receives inventories on site delivered by warehouse staffs. The inventories are used by the onsite maintenance team for day to day routine maintenance.
There are contractors and services providers contracted by head office (process C) for major repair of Heating Ventilation and Air-conditioning (HVAC), roofing, carpeting, plumbing, electrical etc. Area leaders are requesting contractors and service providers through head office when the job can’t be done by onsite maintenance team. Head office selects suitable contractors and issues purchase order to them. Bills are raised by the contractors on completion of job. Head office pays the bill once confirmation is received from the area leaders. Management, SCM department, Warehouse, PM department, area leaders, HVAC contractors and the sites are the key players in the supply chain. Their functions are decision making, ordering, purchasing, financing, service providing, inventory management and operation. The first supply chain mapping created is shown below (figure 1).
The appendix 1 shows that in the year 2012 head office paid total CAD 855400.00 to the HVAC contractors of Edmonton area where CAD 200200.00 was paid for spares and 655200.00 for labour and services. It was considered very expensive and management decided to create own Preventative Maintenance (PM) department by 2013. In the year 2013 a group of technician were hired and a PM department was established in Edmonton. They started work in a limited scale side by side with the HVAC contractor. The next supply chain process map created at figure-2 below shows that there is a PM department In Edmonton. They are providing services to the sites with the request of area leaders (line G).
It has no interaction with warehouse and depends on site for the parts. For HVAC repair and maintenance there is no contract made (Highlighted in yellow). But contractors were called to support PM department time to time. The cost of repair, inventories and wage of PM dept members in 2013 were CAD 1150000.00 (Appendix 2). The cost was found justified to the management. In August 2014, the finance department informed the management that the yearly repair and maintenance budget in Edmonton area is exhausted and requested additional budget for remaining three months of the year. The breakdown of total expenditures of 1550500.00 CAD for 9 months is shown in appendix 3. Supply chain process mapping created as shown below. (Figure 2)
Analysis of the Situation Under the Above Supply Chain Process Map (Figure 2) A team of 7 members with a supervisor were hired to establish the PM dept. All required tool and transports were purchased in 2013. An unused facility was converted as PM office and there was no cost for the facilities other then utility bills. The PM department prepared a list of inventories and forwarded to all 17 sites with a request to maintain the suggested stock level. All the 17 sites in Edmonton ordered the parts and arrived on site within a month. Breakdown of expenditure for inventories, repair and salaries of 7 PM members presented by finance dept are shown in Appendix 2. Details of analyses and findings are as follows:
a. The cost hiring contractor was saved but salaries and benefit of 7 PM members added
b. Cost of 4 vehicles and tools are added but it will come in assets c. Operating costs for vehicle and utilities are added
d. All 17 areas are stocking 90% same inventories which are 4 time more than the parts used by contractors in year 2012 (appendix 1 and 3 )
e. Lead time for the 80 % parts included in the inventory are maximum 7 days.
f. Lead time for the 20% spares are maximum 20 days
g. Holding of extra inventory has added overhead cost
h. Some inventories may remain unused and become obsolete
i. PM team needs to wait for the onsite maintenance to issue parts
j. Few
sites did not order parts as per list
k. Supply chain management department was not consulted at any stage and while preparing the inventory list
l. Preventative maintenance for the boiler room has been done very well than any time before.
Recommendation
From the studies and analysis it appears that following decision and corrective measures may be taken to save cost and make the PM department profitable:
a. PM department may be given an extra store to maintain first moving spares for 15 days and for critical parts 30 days on the basis of average consumption for all sites.
b. All inventories from the sites may be shifted to PM department.
c. PM dept may be allowed to order and receive parts from warehouse.
d. Being a valued customer company may take steps to return over stock to the suppliers.
e. PM dept may be allowed to purchase parts from store in urgent case.
f. The inventory requirement of PM dept may be reviewed every six months.
g. PM dept may allocate parts against the requisition for repair order.
h. Management may monitor the activities of PM time to time.
i. SCM may be consulted before making such decision
j. A supply chain process map as recommended is shown below.(Figure 3)
List of Figures
1. Original Supply Chain Map of an area
2. Supply Chain Process Map of an area with PM Department
3. Recommended Supply Chain Map of an area