Supply chain management Argumentative
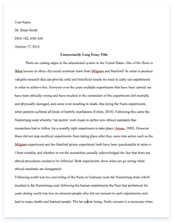
- Pages: 154
- Word count: 38389
- Category: Management Supply Supply Chain Management
A limited time offer! Get a custom sample essay written according to your requirements urgent 3h delivery guaranteed
Order NowFundamentals of Supply Chain Management
Download free eBooks at bookboon.com
2
Fundamentals of Supply Chain Management
3
Fundamentals of Supply Chain Management
Introduction
8
1.1
Why Supply Chain Management
8
1.2
Defining supply chains
9
1.2
Customer Orientation
11
1.3
Defining Supply Chain Management
13
1.3
Development Trends
16
2
Global Supply Chain Operations
17
2.1
Global Business Environment
17
2.2
Strategic Challenges
19
2.3
How Global Supply Chains Responded
2.4
Current Trends in Global SCM
3
Supply Chain Design and Planning
3.1
Supply Chain Configuration
3.3
Extent of Vertical Integration
3.4
Outsourcing and Offshoring
34
3.5
Please click the advert
Location Decisions
39
360°
thinking
.
360°
thinking
23
.
27
30
30
32
360°
thinking
.
Discover the truth at www.deloitte.ca/careers
Š Deloitte & Touche LLP and affiliated entities.
Discover the truth at www.deloitte.ca/careers
Š Deloitte & Touche LLP and affiliated entities.
Download free eBooks at bookboon.com
Š Deloitte & Touche LLP and affiliated entities.
Discover the truth4at www.deloitte.ca/careers
Š Deloitte & Touche LLP and affiliated entities.
D
Fundamentals of Supply Chain Management
Contents
3.6
Capacity Planning
42
3.7
Bullwhip Effect
44
4
Lean Supply Management
50
4.1
Origins of the Lean Manufacturing
50
4.2
Lean Supply Principles
51
4.3
Focusing on Cost-to-Serve
56
4.4
Drivers for Lean Supply Chain
57
4.5
Lean Process Mapping Tools
60
5
Agile Supply Management
70
5.1
The Need for Agility
70
5.2
Agile Supply Chain Concept
71
5.3
Agile Supply Chain Framework
74
5.4
Competing on Responsiveness
77
5.5
Getting It Right from Within.
80
6
Purchasing and Supplier Selection
83
6.1
Strategic Role of Purchasing
83
6.2
Purchasing Portfolio
85
6.3
Supplier Selection
88
6.4
Tools for Supplier Selection
89
6.5
Towards Knowledge Based Sourcing
91
Please click the advert
Increase your impact with MSM Executive Education
For almost 60 years Maastricht School of Management has been enhancing the management capacity of professionals and organizations around the world through state-of-the-art management education. Our broad range of Open Enrollment Executive Programs offers you a unique interactive, stimulating and multicultural learning experience.
Be prepared for tomorrowâs management challenges and apply today. For more information, visit www.msm.nl or contact us at +31 43 38 70 808 or via [email protected]
the globally networked management school
For more information, visit www.msm.nl or contact us at +31 43 38 70 808 or via [email protected]
Download free eBooks at bookboon.com
18-08-11 15:13
Executive Education-170×115-B2.indd 1
5
Fundamentals of Supply Chain Management
Contents
7
Relationship and Integration
94
7.1
Supply Relationship Defined
94
7.2
Close Partnership
95
7.3
Strategic Alliance
98
7.4
Relationship Dilemma
99
7.5
Supply Chain Integration
103
8
The Future Challenges
105
8.1
Creating Customer Centric Supply Chain
105
8.2
Managing Supply Networks
107
8.3
Watch the Dynamics
109
9
References
112
Please click the advert
See the light!
The sooner you realize we are right,
the sooner your life will get better!
A bit over the top? Yes we know!
We are just that sure that we can make your
media activities more effective.
Get âBookboonâs Free Media Adviceâ
Email [email protected]
Download free eBooks at bookboon.com
6
Fundamentals of Supply Chain Management
Preface
Preface
I feel honoured to have this opportunity to write a book about the fundamental of supply chain management for the BookBoon.com Ltd and Ventus Publishing ApS. The chosen topic represents my attempt to respond to the growing demand for better understanding of supply chain management from managers, academics and graduate students alike. This book is based upon my 15 years of teaching experience gained through working in 6 different countries around world. Most of my courses on supply chain management were targeted at the master and executive levels, from which I have learned and enjoyed as much as my students do. The most important lesson I learned is that supply chain management is a dynamic and evolving subject. It is not a subject that just needs to be taught, but the one needs to be constantly developed. To certain extent, this book will hopefully contribute to such a development. Due to the constraints in the number of pages, this book will primarily focus on the fundamental principles of supply chain management. It will cover all the key conceptual areas with short business cases, but is limited in scope on management skill coaching. The book is particularly suitable for those readers who may have come across the subject anecdotally but have never studied it systematically.
In order to continuously improve my book, I would appreciate any suggestions and comments. Please do not hesitate to get in touch with me through: [email protected].
Dr. Dawei Lu
April, 2011
Download free eBooks at bookboon.com
7
Fundamentals of Supply Chain Management
Introduction
1 Introduction
1.1 Why Supply Chain Management
A supply chain is basically a group of independent organisations connected together through the products and services that they separately and/or jointly add value on in order to deliver them to the end consumer. It is very much an extended concept of an organisation which adds value to its products or services and delivers them to its customers. But what is the benefit of understanding the value adding from the supply chain perspective? Why managing supply chain is becoming necessary and important to todayâs business success? These are some of the fundamental questions that must be first addressed before discussing the âhow toâ questions.
Over the last three decades, the concept and theory of business management have undergone profound changes and development. Many old ways of doing business have been challenged and many new ideas and approaches have been created, among them are business process re-engineering, strategic management, lean thinking, agile manufacturing, balanced scorecard, blue ocean strategy, ⌠just to name a few. Supply chain management is undoubtedly one of those new and well grown management approaches emerged and rapidly developed across all industries around the world. The earliest appearance of the term âsupply chain managementâ as we know it today published in recognisable media and literatures can be traced back to the early 1980s. More precisely, it first appeared in a Financial Times article written by Oliver and Webber in 1982 describing the range of activities performed by the organization in procuring and managing supplies. However the early publications of supply chain management in the 1980s were mainly focused on purchasing activities and cost reduction related activities. The major development and the significant increases of publications in the areas of supply chain integration and supplier-buyer relationship came in 1990s when
the concept as we know it today was gradually established.
It is therefore clear that supply chain management is not one of the legacy academic subjects existed for hundreds or thousands of years, but rather a young and even nascent subject. It is only recently that business world started making use of this concept. So, the question is âWhy now?â A convincing answer to this question is that our business environment has changed, which includes globalisation, more severe competition, heightened customer expectation, technological impact and geopolitical factors and so on. Under such a renewed business environment, an organisation focused management approach is no longer adequate to deliver the required competitiveness. Managers must therefore understand that their businesses are only part of the supply chains that they participated and it is the supply chain that wins or loses the competition.
Thus, the arena of competition is moving from âorganisation against organisationâ to âsupply chain against supply chainâ. The survival of any business today is no longer solely dependent on its own ability to compete but rather on the ability to cooperate within the supply chain. The seemingly independent relation between the organisations within the supply chain becomes ever more interdependent. You âsink or swim with the supply chain.â It is for this reason that gives rise to the need for supply chain management.
Download free eBooks at bookboon.com
8
Fundamentals of Supply Chain Management
Introduction
Consequently, aspiring to become an excellent business simply through an entirely inward looking management approach can be very illusive. Whatâs more practical and indeed more assured way of better managing a business is
to managing it along with the supply chain through appropriate strategic positioning, adequate structural configuration, collaboration, integration and leadership. The paramount importance of doing so does not derive from the theories or reasoning, rather it is withstood by the business performance improvement and market measured customer results. It is the tangible benefits and success that it delivers makes the subject important.
Supply chain management is also pervasive and ubiquitous. One can hardly find any aspect of business that has nothing to do with supply chain management. Take an example of quality management â a very important part of todayâs business management, and ask yourself a question: can you manage and improve the quality standard of your product or service measured by the end-consumer without managing the suppliers and buyers in the supply chain at all? Of course not. Business value creation is always a collective contribution from the whole involved supply chain.
1.2 Defining supply chains
Ploughing through the plethora of literatures, one will come to realise that there are as many different definitions as many of those who cared to write about it. However, a broad conceptual consensus on the notion of Supply Chain (SC) and Supply Chain Management (SCM) is beyond anybodyâs reasonable doubt. Based on that, the author would like to offer his definition of SC here and SCM in the next section.
In this definition, there are a number of key characteristics that have been used to portrait a supply chain. First, a supply chain is formed and can only be formed if there are more than one participating companies. Second, the participating companies within a supply chain normally do not belong to the same business ownership, and hence there is a legal independence in between. Third, those companies are inter-connected on the common commitment to add value to the steam of material flow that run through the supply chain. This material flow, to each company, comes in as the transformed inputs and goes out as the value added outputs.
Intuitively, one can imagine a supply chain as something resembles a âchainâ,
in which the âlinksâ are the participating companies that are inter-connected in the value adding process (see figure 1). The link on the upstream side of the material flow is the supplierâs supplier; and on the downstream side of the material flow is the customer. There is usually an OEM â Original Equipment Manufacturer in between. The OBM sometimes is represented by OBM â Original Brand Manufacturer, or sometimes simply the âfocal company.â
Download free eBooks at bookboon.com
9
Fundamentals of Supply Chain Management
Introduction
Figure 1. The basic Supply Chain model
At the end of a supply chain is the product and/or service that are created by the supply chain for the end consumer. Thus, the fundamental reason of a supply chainâs existence is hinged on to serving the end-consumer in the market place. The degree of how well a supply chain can serve their consumer ultimately defines its competitive edge in the market place. It is understandable that in real-world a supply chain is much more complex than the one depicted in Figure1. It is not really a âchainâ, rather it is more like a ânetworkâ, when you consider that there are usually multiple suppliers and multiple customers for each participating companies in the chain. There are also possible nested chains within the chains. For example an engine manufacturing supply chain is a nested supply chain within the connected automobile supply chain. Depend on how would like to see the supply chain, there are similar but different names you may like to call the supply chain. If you view a supply chain as basically a chain of value adding activities, you may like to call it âValue Chainâ; if you perceive a supply chain as continuous demands originated from the consumer and stretched to upstream suppliers, you may like to call the supply chain the
âDemand Chainâ. Since the business connections between organisations are pervasive, how could one draw a boundary of a supply chain? In order to answer this question, one needs to understand the four intrinsic flows of a supply chain. Material Flow: All manufacturing supply chains have material flows from the raw materials at the beginning of the supply chain to the finished products at the end of the supply chain. A furniture-making supply chain will have the wood cut down from forest at the beginning of its supply chain and home furniture at the end of supply chain. The continuous flow of wood been transformed through the chain and end up to furniture ties the whole supply chain together and defines its clear boundary. A furniture supply chain can never be confused with a chocolate manufacturing supply chain because the material flows in between are clearly different and never will they cross with each other.
Download free eBooks at bookboon.com
10
Fundamentals of Supply Chain Management
Introduction
Information Flow: All supply chain s have and make use of information flows. Throughout a supply chain there are multitude of information flows such as demand information flow, forecasting information flow, production and scheduling information flows, and design and NPI information flows. Unlike the material flow the information can run both directions, towards upstream and downstream alike. Interestingly most of them are unique to the specific supply chain. The information of womanâs fashion clothing has no value to a motorbike supply chain. Any supply chain will have its own set of information flows that are vital to its existence which are often jealously protected against those of other supply chains. Finance Flow: All supply chain have finance flow. It is basically the money flow or the blood stream of a supply chain. Without it, a supply chain will surely demise. However, for any supply chain, there is only one single source of such finance flow â
the en-consumer. This understanding of single source of finance has led to a concept of âsingle entityâ perspective of a supply chain, which is a very useful foundation for supply chain integration and collaboration. The distribution and sharing of this single financial resource fairly across a supply chain will allow for the better alignment between the contribution and reward for the participating companies.
Commercial flow: All supply chain represents a transactional commercial flow. This means that the material flow that run through the supply chain changes its ownership from one company to another, from supplier to buyer. The transactional process of buying and selling shifts the material flowâs ownership from the supplier to the buyer repeatedly until the end of the supply chain â the end-consumer. This transactional commercial flow will only take place in a supply chain where there are more than one companies. On the other hand, if it is with an organisation there will be material flow, but no ownership change, and hence no commercial flow.
The four flows described above not only better explain the function of the supply chain, but also define it more rigorously. They represent four major areas of concerns and research activities in the supply chain management, which covers most of the known issues in the published literatures.
1.2 Customer Orientation
Having understood the supply chain model, one may ask âIs the end-consumer a part of the supply chain?â Most people will say âYesâ, because consumer give the demand information; consumer provide the financial reward and so on. But the author will argue that strictly speaking the end-consumer is NOT part of the supply chain; the supply chain only extend from the very raw material suppliers to the retailer (if thatâs the last link in the supply chain before the end-consumer). There are number of fundamental reasons to support this argument. 1) First, all supply chain supplies, and every member of the supply chain supplies; but the consumer DONâT, it demands instead of supply. The fundamental function of a supply chain is to supply; and the consumer is the recipient of the supply, but not a part of the supply. Supply chainâs existence is based on the existence of the demand from the consumer. Supply
chain treats consumer as the object which it serves. If a supply chain contains the consumer within itself, then it will have no object to serve and no recipient to take the supply; and it will lose its purpose of existence.
Download free eBooks at bookboon.com
11
Fundamentals of Supply Chain Management
Introduction
2) Second, a supply chain adds value to the product (or transformed inputs), but the consumer DONâT. Consumer consumes the product and depletes its market value. Used goods are always cheaper than the new ones. A supply chain and every member in it have the irrefutable duty to add values to the material flow, and they must learn how to improve the business and its management; but consumers will never need to do that. Their job is to use the money to vote which supply chain best satisfy their demand. 3) Third, a supply chain is always specialised and a consumer is always general. A computer manufacturing supply chain only produces computers, whilst a consumer will have to buy food, clothing, and automobile as well as computers. Due to the extremely divers nature of consumerâs purchasing, to put the consumer as part of a supply chain will not be helpful in understanding the nature of a supply chain and may cause considerable confusion theoretically and logically.
Based on these three fundamental differences between the nature of supply chain and that of the consumer, it is more appropriate and less confusion if we separate the consumer away from the concept of the supply chain. This definition of supply chain without consumer will not deprive the immense benefits that consumer may contribute to the supply chain. How the end-consumer plays this pivotal role in the existence and the management of supply chain is the core notion of supply chain management.
The end-consumer to a supply chain is perhaps the most important factor of all as far as its management is concerned. Everything a supply chain does is driven by the needs and wants of the end-consumer. The contents of SCM are populated with the approaches, activities as well as the strategies that are aiming at delivering the products and services to satisfy the end-consumer. Therefore, it is safe to say that the SCM should be and has always been a customer centred management.
Please click the advert
This reflects the typical characteristic of supply chainâs customer orientation.
GOT-THE-ENERGY-TO-LEAD.COM
We believe that energy suppliers should be renewable, too. We are therefore looking for enthusiastic new colleagues with plenty of ideas who want to join RWE in changing the world. Visit us online to ďŹnd out what we are offering and how we are working together to ensure the energy of the future.
Download free eBooks at bookboon.com
12
Fundamentals of Supply Chain Management
Introduction
Not only the end-consumer serves as the ultimate objective, it also provides vital information and practical assistance to the decision making in the process of supply chain management. The end-consumers needs and wants, where they are, how many they are and how much they can afford and etc. give the supply chain manager some very precise guidance as how to achieve market responsiveness.
It is therefore beyond the shadow of doubt that supply chain and its management have always been, still are, and will certainly continue to be customer oriented. This customer orientation gives the fundamental reason and purpose of its existence. It also ensures that supply chain management has to be a system perspective based management approach that engages every participating member of the supply chain to align to the customer orientation.
1.3 Defining Supply Chain Management
Defining the supply chain management can be both dead easy and extremely difficult. It is dead easy because it is so widely known and widely practiced in almost all businesses. There is hardly a need to teach the âA, B, Câ again. It is also extremely difficult because the definition must capture all what supply chain management in practice has reached far and wide. As an attempt, the author proffers the following definition:
This definition squared out the nagging confusion between organisational business management and supply chain management. Rarely any aspect of organisational business management is not related to or influenced by the external firms in the supply chain. Thus the best way to manage the business is to take into consideration and engage with the external organisations in the decision making in order to achieve the ultimate business objectives â that means supply chain management.
In other words, trying to identify a set of supply chain management activities that is not or nothing to do with any known business management activities would futile. The inception of the supply chain management concept did not create a new set of functional activities that has never been carried out before. What it created is a new way of understanding on how the business activities might be better carried out.
The supply chain management defined as such has already elevated the modern business management concept from the organisational focused domain to the supply chain focused system giving rise to more effectiveness in achieving the strategic objectives. Todayâs competition is no longer seen as the
company against the company but the supply chain against the supply chain. Supply chain management is therefore a new perspective towards the old activities.
Download free eBooks at bookboon.com
13
Fundamentals of Supply Chain Management
Introduction
This definition effectively explains why supply chain management can be done in such vastly diverse ways; why apparently completely different management activities can often be called supply chain management; why the same traditional management function is now been entitled as supply chain management; and so on. The answer is simply that because we start view the management issues and taking actions from the supply chain perspective. This definition certainly gives the supply chain management concept a ubiquitous and pervasive nature. But, that does not mean that there is nothing uniquely identifiable on its own. One can still identify some practically very useful conceptual components of the supply chain management. Any supply chain management practice and activities is captured by the three conceptual components: Supply Chain Configuration; Supply Chain Relationship; and Supply Chain Coordination.
Figure 2. Supply Chain Management conceptual model
⢠Supply Chain Configuration is about how a supply chain is constructed from all its participating firms. This includes how big is the supply base for OEM (original equipment manufacturer); how wide or narrow is the extent of vertical integration (which is the single ownership of consecutive activities along the supply chain); how much of the OEMâs operations are outsourced; how the downstream distribution channel is designed; and so on. It is also known as supply chain architecture. The decision on supply chain
configuration is strategic and at a higher level.
⢠Supply Chain Relationship is about inter-firm relationships across the supply chain albeit the key focus of relationship is often around the OEM and its first tier suppliers and first tier customers and the relationship in between. The type and level of the relationship is determined by the contents of inter-organisational exchanges. The relationship is likely to be âarmâs lengthâ if they only exchanged the volume and price of the transaction; on the other hand, the relationship would be regarded as close partnership if the parties exchanged their vision, investment planning, NPI process and detailed financial information. The decision on supply chain relationship is both strategic and operational.
Download free eBooks at bookboon.com
14
Fundamentals of Supply Chain Management
Introduction
⢠Supply Chain Coordination refers mainly to the inter-firm operational coordination within a supply chain. It involves the coordination of continuous material flows from the suppliers to the buyers and through to the end-consumer in a preferably JIM manner. Inventory management throughout the supply chain could be a key focal point for the coordination. Production capacity, forecasting, manufacturing scheduling, even customer services will all constitute the main contents of the coordination activities in the supply chain. The decision on the supply chain coordination tends to be operational. There is, however, one thing in common amongst the three key supply chain management focuses. That is they all deal with the external organisation in the same supply chain, which makes the concept more supply chain rather than organisationally internal. These concepts also tell us that supply chain management involves managerial decision making across strategic, tactic and operational levels â the pervasiveness. One may notice
that all the major Operations Management text books will include a chapter or two on supply chain management, but that does not necessarily make the subject purely operational.
30 FR
da EE
ys
tria
l!
SMS from your computer
…Sync’d with your Android phone & number
Please click the advert
Go to
BrowserTexting.com
and start texting from
your computer!
…
BrowserTexting
Download free eBooks at bookboon.com
15
Fundamentals of Supply Chain Management
Global Supply Chain Operations
1.3 Development Trends
Another difficulty in understanding and defining supply chain and supply chain management is that it is never stand still and the subject has been continuously evolving since its inception in the early 1980s. The continuous development is partly propelled by the changes of overall business environment and heightened competitions in the global market place. But partly it is influenced by the new understanding of the supply chain that they participate. There are number of early development trends that can be observed evidently.
1) From functional to process perspective. Business management used to see and take action on the functional silos in the business. It was understandable that naturally the function is what seen to be the delivery part of the business. But, today with supply chain management concept managers can see their problems more from the process perspective, understanding that functions can only make sense if it is perceived from a supply chain process perspective.
2) From operational to strategic viewpoint. At early years of applying supply chain management concept, managers tends to see it as another operational tactics that will help to reduce operational cost, such as purchasing function improvement and optimising the logistics operations. But, gradually more and more managers realised that the effective changes can only be achieved if the operational issues are addressed from the supply chain wide strategic viewpoint. Operational excellence can only be manifested through its strategic fit. 3) From single enterprise to extended enterprise. Enterprise management is now arguably displaced by the supply chain management, where the supply chain is by definition the extended enterprise. The long established enterprise centred management thinking was based on that the competition was raged between the organisations, thus it becomes obsolete as the competitions are now predominantly between the supply chains. Management thinking over the extended enterprise produces a great deal ideas that single enterprise alone cannot.
4) From transactional to relationship based engagement. Business engagement between firms in the past was predominantly transaction based and cost
driven. The merit of any purchasing and procurement of externally sourced materials and services was judged by the transactional measures such as price, volume and delivery terms. But whatâs now more of the practices in working with external organisations within the supply chain is so called relationship based engagement. This relationship approach does not abandon the transactional activities but put its decision baking on much wider consideration of knowledge exchange, long-term commitment, incentives and reward.
5) From local to regional, and from regional to global. Connections of supply network have over the last two decades grown from local to regional and to global. Hardly any major enterprise and supply chains is not connected to some part of the world. You need to get out before you can get up. This trend is spurred by the lower cost of labour and materials in many parts of the world, as well as first mover advantages in setting up global market presence.
The trends of supply chain development are not always positive and encouraging. There is now enough evidence to support that supply chain risks are now continuously growing to the level that is higher than ever before; and supply chain integration still remains as the major management shortfall across all industrial sectors (PRTM Global supply chain trends report 2010-12). The task of managing and improving supply chain performances across all industrial sectors is only becoming tougher, not easier. This calls for deeper and more thorough understanding of the challenges supply chains are facing. Download free eBooks at bookboon.com
16
Fundamentals of Supply Chain Management
Supply Chain Design and Planning
2 Global Supply Chain Operations
2.1 Global Business Environment
To date, our world market is dominated mostly by many well established global brands. Over the last three decades, there have been a steady trend of global market convergence â the tendency that indigenous markets start converge on a set of similar products or services across the world. The end-result of the global market convergence is that companies have succeeded on their products or services now have the whole wide world to embrace for their marketing as well as sourcing. The rationale of global market convergence lies partially in the irreversible growth of global mass media including Internet, TVs, radios, news papers and movies, through which our planet has become truly a small global village. Everybody knows what everybody else is doing, and everyone wants the same thing if it is perceived any good. It also lies in the rise of emerging economic powers led by BRICs (Brazil, Russia, India and China), which has significantly improved the living standard and the affordability of millions if not billions of people. For organizations and their supply chains, the logic of going global is also clearly recognizable from economic perspective. They are merely seeking growth opportunities by expanding their markets to wherever there are more potentials for profitmaking; and to wherever resources are cheaper in order to reduce the overall supply chain costs. Inter-organizational collaborations in technological frontier and market presences in the predominantly non-homogeneous markets can also be the strong drivers behind the scene.
One can also observe from a more theoretical perspective that the trends of globalization from Adam Smithâs law of âdivision of labourâ. A global supply chain is destined to be stronger than a local supply chain because it takes the advantage of the International Division of Labour. Surely, the specialization and cooperation in the global scenario yields higher level of economy than that of any local supply chains. Thus the growth of global supply chain tends to give rise to the need for more coordination between the specialized activities along the supply chain in the global scale. As the newly appointed Harvard Business School dean professor Nitin Nohria said âIf the 20th century is Americanâs century, then the 21st century is definitely going to be the global century.â The shift of economic and political powers around world is all too visible and has become much more
dynamic and complex. But, one thing is certain that there will be significantly and increasingly more participation of diverse industries from all around the world into the global supply chain network; hence bringing in the influences from many emerging economies around the world. Their roles in the globally stretched network of multinational supply chains are going to be pivotal and will lead towards a profoundly changed competitive landscape.
Download free eBooks at bookboon.com
17
Fundamentals of Supply Chain Management
Supply Chain Design and Planning
In such a global stage there are a number of key characteristics that global supply chains must recognize before they can steer through:
⢠Borderless: National borders are no longer the limits for supply chain development in terms of sourcing, marketing, manufacturing and delivering. This borderless phenomenon is much beyond the visible material flows of the globalised supply chain. It is equally strongly manifested in terms of invisible dimensions of global development such as brands, services, technological collaboration and financing. Evidently, the national borders are far less constrictive than they used to be. Arguable this is perhaps the result of technology development, regional and bilateral trade agreements, and the facilitation or world organizations such as WTO, WB, GATT, OECD, OPEC and so on.
⢠Cyber-connected: The global business environment is no longer a cluster of many indigenous independent local markets, but rather it emerged as an inter-connected single market through predominantly and growingly important cyber connections. For this reason, the inter-connection of our global business environment is almost âinvisibleâ, spontaneous and less controllable and surely irreversible. Globally stretched multinational supply chains would not be possible or even comprehensible without
cybertechnology allowing large amounts of data to be transferred incredibly quickly and reliably. ⢠Deregulated: Trade barriers around the world has been demolished or at least significantly lowered. Economic and free-trade zones around the world have promoted open and fair competition and created, albeit never perfect, a level playing field on the global stage. Deregulation simplifies and removes the rules and regulations that constrain the operation of market forces. It has targeted more at the international trading and aiming for stimulating global economic growth. The typical deregulated regions are European Union, North America Free Trade Agreement zone; Associations of Southeast Asian Nations group and so on. Deregulation reduces government control over how business is done thus moving towards laissez-fair and free market system.
⢠Environmental Consciousness: Last decade has witnessed the growing concerns on the negative impact of business and economic development on the natural environment. The global movement towards green and more eco sustainable business strategies plays an important role in todayâs global supply chain development. This is also driven by the actions of lawmakers and regulatory agencies, such as the Environmental Protection Agency (EPA). Governments of leading economies are increasingly involved in promoting greening activities in business, and formalize more legislation and regulation to place upon firms in the future. Carbon footprint is now a key performance measure of the sustainability for many global supply chains.
⢠Social Responsibility: Along with that is a wider socio-economic impact. Fair trade and business ethics become increasingly the key measures on businessâs social responsibility, and the key factors for business decision making. Social pressure strikes at the heart of a companyâs brand in the mind of the consumer. A significant group of consumers have begun making their purchasing decisions based on the supply chainâs ethical standard and social responsibility. Global corporate citizenship and social responsibility forms yet another important business environmental factor that can make or break a business.
Download free eBooks at bookboon.com
18
Fundamentals of Supply Chain Management
Supply Chain Design and Planning
2.2 Strategic Challenges
Under such a changing global business environment, what are the new strategic and operational challenges? At a macro level, there are at least five key strategic challenges that will have the long term and overall impact on the architecture as well the management process of the global supply chains. Those strategic challenges tend to be interrelated intricately and dynamically with one another. The magnitude of those challenges varies from industry to industry; and from time to time. Market dimension
Continuing demand volatility across the world market has hampered many supply chainsâ ability to manage the responsiveness effectively. Demand fluctuation at the consumer market level poses a serious challenge to the assets configuration of supply chain, capacity synchronisation, and lead-time management. More often than not it triggers the âbullwhip effectâ throughout the supply chain resulting in higher operating cost and unsatisfactory delivery of products and services. The root causes of the demand volatility in the global market are usually unpredictable and even less controllable. Economic climate plays a key role in overall consumer demand. The recent worldwide economic downturn has made many global supply chains over-capacitated, at least for a considerable period of time. Geo-political instability around the world has also contributed to the market volatility to certain industries. Technology development and product innovation constantly creates as well as destroys the markets often in a speed much faster than the supply chain can possibly adapt. Emerging economies around the world are aggressively churning out products and services that rival the incumbent supply chains in terms of quality and price, which lead to huge swings of market sentiment.
Please click the advert
Who is your target group?
And how can we reach them?
At Bookboon, you can segment the exact right
audience for your advertising campaign.
Our eBooks offer in-book advertising spot to reach
the right candidate.
Contact us to hear more
[email protected]
Download free eBooks at bookboon.com
19
Fundamentals of Supply Chain Management
Supply Chain Design and Planning
Recent research shows that customer loyalty has significantly decreased over the last decade, adding to the concerns of market volatility. The development of internet based distribution channels and other mobile marketing medias has made it incredibly easier for consumers to switch their usual brands. Many products are becoming more and more commoditized, with multiple competitors offering very similar features. With increased market transparency, many B2B and end customers simply shop for the lowest price, overlooking their loyalty to particular suppliers or products. A lack of robust forecasting and planning tools may have contributed to the problem, as companies and their suppliers frequently find themselves scrambling to meet unexpected changes in demand.
Technology dimension
Technology and the level of the sophistication in applying the technology for competitive advantages have long been recognised as the key strategic
challenges in supply chain management. This is even more so, when we are now talking about the supply chain development in a global stage. The key strategic challenges in the technological dimension are threefold. The first is the development lead-time challenge. The lead-time from innovative ideas to testing, prototyping, manufacturing, and marketing has been significantly shortened. This is partially due to the much widened global collaboration on technological development and subsequent commercialisation and dissemination. The globally evolved technology development systems have created a new breed of elite group as the world technology leaders across different industries. They capture the first mover advantages and made the entry barriers for new comers almost impossible to overtake. No doubt, there is a strategic challenge that global supply chain must create an ever ready architecture that can quickly embrace the new ideas and capitalise it in the market place. The second challenge comes from its disruptive power. Harvard Business School professor Clayton Christensen published his book The Innovatorâs Dilemma in May 1997, in which he expounded on what he defined as the disruptive technology. The basic message he tried to put across was that when new technologies causes great firms to fail, managers face the dilemma. Evidently, not all new technologies are sustaining to business, often they are competency-destroying. The product or service developed through applying new innovative technologies may not be so much appreciated by the consumers. Consumers often are often not so eager to buy the ideas. They may not be so convinced that the value the technology created or the costs it added in. If you wait for other companies to test the market first, then you run a high risk of losing the first mover advantage and losing the market leadership. Thatâs the dilemma and thatâs the challenge. The third challenge lies in the supply chain network. The innovative ideas and new technologies usually emerge from a supplier or a contractor in the supply chain network. To convince the whole supply chain of the value adding or cost reduction is not guaranteed. Each supplier and contractor will have its own value stream and will make technology adoption decisions based on the needs of its own customers. Innovative ideas that come up from subcontractors may be stifled due to the supply chainâs inability to coordinate value contribution between individual members and the whole supply chain. The cost and profit structures in the value network can also limit the attractiveness of an
innovation. If profit margins are low, the emphasis will be on cost cutting across proven technologies, rather than taking the risk of the new technologies.
Download free eBooks at bookboon.com
20
Fundamentals of Supply Chain Management
Supply Chain Design and Planning
Finally from the technology evolution perspective, technology destroys as readily as it creates. The development of digital photography has literally destroyed the photo film manufacturing industries including many well known brands; LCD and Plasma technology also smashed the TV Tube (traditional screen component) manufacturing industry overnight. This increased risk of technology disruption at the industrial scale is lot more formidable than the innovative dilemma Prof Christenson was talking about in his book. Nevertheless, there are some helpful supply chain strategies that can better prepare them for the eventuality.
Resource dimension
From resource based perspective, global supply chain development is both motivated by dinging new resources around world and by make better use of its own already acquired resources to yield economic outputs. It comes as no surprises that one of the key strategic challenges in global supply chain development is about resource deployment. The term resource in this context means any strategically important resources, including financial resource, workforce resource, intellectual resource, natural material resources, infrastructure and asset related resources, and so forth. Stretching supply chainsâ downstream tentacles around the world opens the door for making good (more efficient) use of internal resources, i.e. the same level of resources can now be used to satisfy much wider and bigger market in terms of volume, variety, quality and functions. However the internal resource or competence
based strategy will also face more severe challenges on the global stage than in its own local or regional market. The challenges are not necessarily just from the indigenous market, but more likely they come from equally competitive incumbent multinationals and possible emerging ones alike. Also more menacingly the internal based advantages can evaporate anytime when global business
Please click the advert
environment subjects fundamental changes.
THE BEST MASTER
IN THE NETHERLANDS
Download free eBooks at bookboon.com
21
Fundamentals of Supply Chain Management
Supply Chain Design and Planning
Stretching the sourcing-end (supply side) of supply chain to the global market is a great strategy to acquire scarce resources, or any resources at a much lowered cost. The productivity and operational efficiency oriented strategy is often no match to the procurement focused strategy in measures of reducing the total supply chain cost. No wonder many multinationals are actively debating on sourcing their workforce, materials and energy from overseas locations in order to significantly reduce the operation cost, which will then lead to more competitive market offerings. This resource sourcing strategy has been the prime drive for the surge of off-shoring and outsourcing activities all over the world. However many longterm and short-term impacts of outsourcing and off-shoring are difficult to be fully understood from the outset, if at all possible. Thus it forms a key strategic challenge in global supply chain development. Time dimension
Most of the key global supply chain challenges are time related, and it appears to be that they are becoming even more time related than ever before. Given that everything else is equal; the differences on time could make or break a supply chain. When the new market opportunity emerges it is usually the one who gets into the market first reaps the biggest advantages. Competitions on many new electronic consumer products is largely about who developed it first and become the industry leader. From the internal supply chain perspective, the cost and core competences are all largely measured against time. Inventory cost increase, if the materials do not move on quick enough; supply chain responsiveness is can be significantly influenced by the lead-time and throughput time. Indeed, one of the key supply chain management subject areas is about agility and responsiveness. That is basically defined as how fast the supply chain can respond to the unexpected and often quite sudden changes in market demand. Understandably, in the increasingly fast moving global market place, developing and implementing an agile supply chain strategy makes sense. However, the tough challenges are usually not on making the decisions as to whether should the supply chain be agile or not. They are more on balancing the âcost to serveâ. In order to maintain a nimble footed business model, the supply chain may have to upgrade its facilities with investment, having higher than usual production and service capacities, or having high level of inventories. Then the question is would the resultant agility pay for the heightened supply chain costs. There is no fixed answer to this question, and it remains as a key challenge to supply chain managers. The time measures on many operational issues have also been the major challenges for supply chain managers. Customer lead-time, i.e. from customer order to product delivery, is one of those challenges. Toyota claims that they can produce a customer specified vehicle with a fortnight â the shortest lead-time in the auto industry. This adds huge value to the supply chain in terms of customer satisfaction, cost reduction, efficiency and productivity. But it could be a huge challenge, when the customers are all over the world and the productions sites and distribution logistics facilities are not well established. All the challenges in the three dimensions are, of course, interrelated and even interdependent with each other. A supply chain strategist must have a sound
system view to understand the intricate relations of all factors in the whole supply chain and over the projection of long-term. Those strategic challenges have undoubtedly given rise to the risk level of global supply chain development. It came as little surprise that the supply chain risk management, which will be discussed later in this book, is now one of the hot topics discussed in the academia and business circle alike.
Download free eBooks at bookboon.com
22
Fundamentals of Supply Chain Management
Supply Chain Design and Planning
2.3 How Global Supply Chains Responded
Knowing the challenges is one thing perhaps to begin with, but learning about how to face up to the challenges is quite another. Despite the plethora of literatures on supply chain management, there are still no universally agreed âone size fit allâ recipes for managers to prescribe in order to survive the challenges. Academic and empirical studies show there are at least five common approaches that supply chains have survived the global challenges. Collaboration
âIf you cannot beat them, you better join them.â A great deal of global supply chain management activities are not necessarily about competing against one another, rather it is more about collaboration and partnering. Inter-firm collaboration in supply chain management context is simply defined as working together to achieve a common goal. The content of collaboration varies from project to project and from business to business. It may be a research and development collaboration which is aiming perhaps for a technological advancement or a new product design; or it could be a logistics operational collaboration where the aim is to reduce logistics lead-time and cost; it could also be marketing collaboration where the aim is to penetrate the market and increase sales. So, the collaboration is
usually mentioned when there is an area or a project the activities of the collaboration can be associated with. The parties that involved in the collaboration are often referred to as the partners or collaborative partners. There are a number of obvious reasons why collaboration is one of the most favourite supply chain management approaches. ⢠Sharing resources: collaboration between two firms helps to share the complementary resources between them, thus avoiding unnecessary duplication of the costly resources such as capital-intensive equipment, service and maintenance facilities, and distribution networks and so on. Information, knowledge and intellectual resources are also very common resources that are shared during the collaboration. ⢠Achieve synergy: collaboration of the two partnering firms will usually result in what is called âsynergy.â Synergy, in general, may be defined as two or more things functioning together to produce a result not independently obtainable. That is, if elements A and B are combined, the result is greater than the expected arithmetic sum A+B. In the context business collaboration or partnering, synergy is about creating additional business value that neither can achieve individually. ⢠Risk sharing: a properly constructed collaboration can help to mitigate the companyâs market and supply risk significantly for both parties. Risk is the negative but uncertain impact on business, which is normally beyond control. By collaborating on investment and marketing, the negative impact of the supply chain risks can be borne by both parties and thus shared and halved.
⢠Innovation: collaboration in technology development and R&D partnering is particularly effective way to advance their competitive advantages through innovation in the technological frontier. The logic behind is perhaps that when people from different business working to gather, they start blend their knowhow and experience together, sparkling new innovative ideas. In most of innovation training programmes one can always recognise one of steps of generating innovative ideas is to have brain storming across a multifunctional team.
Download free eBooks at bookboon.com
23
Fundamentals of Supply Chain Management
Supply Chain Design and Planning
Supply chain integration
The nature of a supply chain is that it is usually a network which consists of a number of participating firms as its member. For a global supply chain the network stretches many parts of the world, and the participating member firms of the network can be an independent company in any country around the world. Supply chains are therefore voluntarily formed âorganisationsâ with fickle loyalties and often antagonistic relations in between the member firms. Communication and visibility along the supply chain are usually poor. In other words, supply chains are not born integrated. Supply chain integration therefore can be defined as the close internal and external coordination across the supply chain operations and processes under the shared vision and value amongst the participating members. Usually, a well integrated supply chain will exhibit high visibility, lower inventory, high capacity utilisation, short lead-time, and high product quality (low defect rate). Therefore, managing supply chain integration has become one of the most common supply chain management approaches that can stand up to the global challenges. However, there is no supply chain that is strictly 100% integrated, nor any one that is strictly 0% integrated. It is about how much the supply chain is integrated from a focal companyâs point of view. To illustrate this degree of difference in supply chain integration, Frohlich and Westbrook (2001) suggested a concept of âArc of Integrationâ (Figure 3). A wider arc represents a higher degree of integration which covers larger extent of the supply chain, and a narrow one for a smaller extent. The issue about supply integration is particularly important when the supply chain is formed by the members around the globe.
Figure 3. Arc of integration (Source: Frohlich and Westbrook, 2001)
Download free eBooks at bookboon.com
24
Fundamentals of Supply Chain Management
Supply Chain Design and Planning
Divergent product portfolio
A conventional wisdom says that âdonât put all your eggs in one basket.â It also makes sense in formulating a global supply chain development strategy. Translated into business management terminology, the wisdom is very similar to the âdivergent product portfolioâ strategy. Then it may make even more sense when the global market becomes the stage for the supply chain. Two key characteristics of global market are volatility and diversity. Develop divergent product portfolio will make the supply chain more capable of satisfying the divergent demand of the world market. Many leading multinational organisations have already been the firm believer of this strategy. They have developed a wide range of product or even business sector portfolio to cater for the market needs. Virgin Group, General Electric, British Aerospace are just some well know examples. The divergent product portfolio strategy can also significantly mitigate the market risks that brought forth by the nature of global market volatility. If one product is not doing well, the supply chain can still be stabilised by others that do well. The shock of one single market at a particular time will not derail the overall business. In a long run, occasional market
Please click the advert
instabilities will ease off with each other. So, the divergent portfolio works like a shock absorber and risk mitigating tool.
With us you can
shape the future.
Every single day.
For more information go to:
www.eon-career.com
Your energy shapes the future.
Download free eBooks at bookboon.com
25
Fundamentals of Supply Chain Management
Supply Chain Design and Planning
Develop the âblue ocean strategyâ
Instead of going for the âhead-onâ competition in the already contested âred seaâ a much more effective approach is to create a new market place in the âblue oceanâ, which makes the competition irrelevant. This is an innovative strategic approach developed by Prof. Cham Kim and Renee Mauborgne in 2005, and published in their joint authored book âBlue Ocean Strategyâ. In the book, the authors contend that while most companies compete within such red oceans, this strategy is increasingly unlikely to create profitable growth in the future. Based on a study of 150 strategic moves in many globally active supply chains over the last thirty years, Kim and Mauborgne argue that developing the âblue ocean strategyâ (as they coined it) has already been proven an effective response to the global challenges for many supply chains. Tomorrowâs leading supply chains will succeed not by battling competitors, but by creating âblue oceanâ of uncontested market space that is ripe for growth. They have proved that one can face up to the challenges most effectively without actually doing so. Creating new market space is actually a lot easier than you think if you know how.
Pursuing world class excellence:
To weather the global challenges and to achieve long lasting business success often calls for one fundamental feat and that feat is world class excellence. Almost all known world leading supply chains in all industrial sectors have somehow demonstrated that they have just been excellent in a multitude of performance measures. The world class excellence defines the
highest business performance at a global level that stand the test of time. Only the very few leading edge organisations around the world truly deserve this title. But the title is not just a title. It is the fitness status that ultimately separates the business winners from losers.
To become a world class supply chain one need to excel in four dimensions. The first dimension is the operational excellence. All world class supply chain must have optimised operations measured in productivity, efficiency, cost effectiveness, quality, high standard of customer service and customer satisfaction. The second dimension is the strategic fit. All world class supply chains must also ensure that excellent operations fit to the supply chainâs strategic objective and stakeholderâs interests; and the internal resources fit to the external market needs. The third dimension is the capability to adapt. Would class supply chains must be dynamic and able to adapt into to new business environment in order to sustain the success. The fourth dimension is the unique voice. All world class supply chains needs to develop its own unique signature practices that render positive market results. Such internally unique practice coupled with positive market result is called unique voice. This dimension goes beyond benchmarking on best-practices; it creates best-practices (Lu 2011).
Download free eBooks at bookboon.com
26
Fundamentals of Supply Chain Management
Supply Chain Design and Planning
2.4 Current Trends in Global SCM
Many reliable management researches and surveys conducted in recent years have come to a broad consensus that some significant development trends are shaping and moving todayâs global supply chains. The following trends are mainly based on and adapted from the PRTM 2010 Survey results with the authorâs own interpretation and analysis to facilitate student learning.
Trend 1: Supply chain volatility and market uncertainty is on the rise. Research survey shows that continued demand volatility in most of global markets is a major concern to the executives of supply chains. Significantly more than any other challenges to supply chain flexibility, more than 74% of the surveyed respondents ticked the demand volatility and poor forecasting accuracy as the increasing major challenges to supply chain flexibility. Apparently, few companies have strategies in place for managing volatility in the years ahead let along implementing it. The lack of flexibility to cope with the demand change is increasingly a management shortfall. In the path of economic recovery, this shortfall could well be the trigger for bullwhip effect. The fast development of cyber market and mobile media has given rise to the market visibility leading to high level of market transparency. B2B customers and consumers have found it a lot easier to shop for alternative lower price or better value. The switching cost is evaporated rapidly, and so is the customer loyalty, which adds salt to the injury. The only known approaches to deal with the trend of increased volatility are improving forecasting accuracy and planning for flexible capacity throughout the supply chain. Best performing companies tends to improve supply chain responsiveness through improving visibilities across all supply chain partners. On the downstream side, companies are now focusing more on deepening collaboration with key customers to reduce unanticipated changes. Trend 2: Market growth depends increasingly on global customers and supplier networks The research survey has shown a positive growing trend in international customers and international suppliers in more international locations. As a result, more than 85% of companies expect the complexity of their supply chains to grow significantly at least for the coming year. The immediate implication of this trend is that the supply chain will have to produce higher number of products or variants to fulfil the customer expectations, albeit this may vary slightly for different geographical regions. In the main, the pattern of global supply chain is going to be more complex in terms of new customer locations, market diversity, product variants, and demand volatility. On the supply side, the trends indicated that a more dynamic supply networks stretching far and wide globally. Managing those suppliers, developing them and integrating them
become more a critical challenge than ever before. Nearly 30% of respondents expect the in-house manufacturing facilities will decline and to be replaced by outsourced and off-shored international contractors. Similarly nearly 30% of respondents expected a decline in the number of strategic suppliers to the OEM (original equipment manufacturer) in order to achieve more closely integrate the supply chain for higher collaborated value adding. This will result in more consolidated supply base. This is more evident in North America and Europe, but significantly less so in Asia where expansion of supply network is more of the case.
Download free eBooks at bookboon.com
27
Fundamentals of Supply Chain Management
Supply Chain Design and Planning
Trend 3: Towards more cost-optimised supply chain configurations Survey respondents seemed confident that they will be able to deliver substantial gross margin improvements over the next couple of years. However the gains will not come from price increases, but from reductions of end-to-end supply chain costs. Globalising supply chain operations and outsourcing specific functions are viewed as critical for controlling costs. It came as no surprise that outsourcing is on the rise across many industrial sectors around the world. Companies are taking advantages of lower costs in emerging markets and increasing their flexibility of their own supply chain. The functions that will see the greatest increase in outsourcing are product development, supply chain planning and shared services. However, globalisation does not seem to have reduced process and management costs. In fact those hidden costs could be on the rise when supply chain becomes more global if not careful. Leading companies understand the impact of those hidden costs and are taking aggressive steps to identify and manage them. Many are embracing new concepts like Total Supply Chain Cost Engineering, an integral approach to calculating and managing total cost across all supply
chain functions and interfaces. Rigorous cost optimisation across the end-to-end supply chain â from order management, sourcing, and manufacturing to logistics and transportation â are critical for success.
Please click the advert
Do your employees receive
the right training?
Bookboon offers an eLibrairy with a wide range of
Soft Skill training & Microsoft Office books to keep
your staff up to date at all times.
Contact us to hear more
[email protected]
Download free eBooks at bookboon.com
28
Fundamentals of Supply Chain Management
Supply Chain Design and Planning
Trend 4: Risk management involves end-to-end supply chain
To date, risk has become an increasingly critical management challenge across the global supply chains. According to the research survey participants, new demands from their customers have played a key role in this development. Dealing with cost pressures of their own, many customers have increased their efforts in asset management and have started shifting supply chain risks, such as inventory holding risks, upstream to their suppliers. This approach, however, merely shifts risks from one part of the supply chain to another but not reduces it for the whole supply chain. In fact, between 65% and 75% respondents believe that supply chain risks can only be most effectively mitigated by the end-to-end supply chain approaches. These end-to-end supply chain practices include advanced inventory management,
joint production and material resource planning, improved delivery to customers and so forth. Leading companies are taking an end-to-end approach in managing risk at each node of the supply chain. To keep the supply chain as lean as possible, they are taking a more active role in demand planning, which ensures they order only the amount of material needed to fill firm orders. Firms are also limiting the complexity of products that receive late-stage customisation. Leading companies mitigate inventory-related risks by shifting the responsibility for holding inventory to their suppliers and, furthermore, by making sure finished product is shipped immediately to customers after production. Trend 5: More emphasis on supply chain integration and empowerment Little can be achieved without appropriate management approaches that truly integrated across all functions throughout the supply chain and empowered them to take bold action. However, approximately 30% mention the lack of integration between supply chain functions like product development and manufacturing. Integrated supply chain management across all key functions still seen to be a myth, with many procurement and manufacturing executives making silo optimisation decisions. Nearly one-fourth of survey respondents point to their organisationsâ inability to make concerted actions and coordinated planning to respond to the external challenges. This could be a surprise to many that would believe after so much has been talked by so many for so long on the supply chain integration, little has been achieved in practice. Whilst almost all the survey participating companies have supply chain department, many of them failed to empower their supply chain managers to take leading roles in business transformation. Leading companies understand that breakthrough improvements are not possible unless the decisions made are optimal for all supply chain functions. For this reason, they have already taken steps to integrate and empower their supply chain as a single resource under one joint responsibility. These firms are making sure the organisation has a strong end-to-end optimization, and are integrating supply chain partners up and downstream.
Download free eBooks at bookboon.com
29
Fundamentals of Supply Chain Management
Supply Chain Design and Planning
3 Supply Chain Design and Planning
One of the important issues in supply chain management is to design and plan out the overall architecture of the supply chain network and the value adding flows that go through it. This means that managers should step back and looks at the supply chain as a whole and formulates strategies and processes that maximise the total supply chain value-adding and minimises the total supply chain costs. The key contents of such architecture design and planning include configuration, extent of vertical integration, strategic outsourcing, location decisions, capacity planning, and dealing with bullwhip effect. There are also other aspects of the design and planning such as relationship posture which will be covered in a separated chapter.
3.1 Supply Chain Configuration
Supply chain configuration represents how the participating company members of the chain are connected with each other to deliver the product or service to the end customer. To an OEM, how many suppliers it uses, how the suppliers are grouped or categorised or tiered, where do they geographically located, the ownership and independence of the suppliers, the choice of distribution channels are all the configuration issues for the supply chain. The fact is that companies do have the choice to configure their supply chains in the way they believe are most appropriate and beneficial. However there is no single âbestâ configuration for all supply chains. It all depends on the industry sectors, market environment, stages of product cycle and so on.
The evolution of global multinationalsâ network could be an interesting example to understand the relevance of supply chain configuration. In the pre-second World War era of 1930s and 1940s, the mostly European multinational companies including Unilever, Royal Dutch/Shell, ICI, and
Philips were the pioneers of âglobal supply chainâ development and created their tentacles such as subsidiaries all over the continent. Each national subsidiary was permitted a high degree of operational independence from the parent company; understanding its own product development, manufacturing and marketing. It is a semidetached âlooseâ configuration. This âhands-off â approach was a response to the conditions at the time when international transport and communication were slow, costly and unreliable; and the national markets were highly differentiated.
During the 1950s and 1960s, the world appears to be dominated mostly by the American multinationals, including GM, Ford, IBM, Coca-Cola, Caterpillar, Procter & Gamble. The configuration of those multinationals with their wholly owned subsidiaries took an evolved form. Although the subsidiaries were operated with high degree of autonomy from the parent company, the US based parent companies occupies a dominant position in terms of strategic guidance and resource support. It was partly because at that time the US was the largest and most affluent market in the world. The US base acted as the source of new products and process technology. The primary competitive advantage of the subsidiaries was the ability to utilise the resource.
Download free eBooks at bookboon.com
30
Fundamentals of Supply Chain Management
Supply Chain Design and Planning
The 1970s and 1980s saw the Japanese challenges all over the world. Her multinationals like Toyota, Honda, Matsushita, NEC, and Sony completed a long journey from exporting to globalisation and established a concrete market bases. A distinguished configuration feature of the Japanese multinationals was their pursuit of global strategies from the centralised domestic bases. While overseas subsidiaries were initially for sales, distribution, and customer support. By building plants of unprecedented
scale to service growing world demand Japanese companies were able to exploit substantial scale and experience advantage.
Supply chain configuration can also be observed from the network relationship perspective. When the OEM forms its supply network through tiered suppliers and tiered distributor with medium and long term stability, it can be called the âStable Network.â When the OEM does not have many of those long term tiered suppliers and customers, but instead uses dynamic and mostly short term suppliers and distributors to achieve high level of operational flexibility and strategic agility, it can be called the âDynamic Network.â The two broad types of network configuration can be illustrated in figure x.
In comparison, the tiered stable network has more control over its suppliers and distributorsâ operations than the dynamic network. An unexpected misunderstanding in the dynamic network may result in unrecoverable product defects. Along with it, there is higher risk in operational cost control and quality standard. However, the dynamic network is much more flexible than stable network in that it can quickly form a new network in the supply market to cater for the changed demand both in volume and in variety. It also has a better ability to upgrade technology and foster innovative processes. Which network configuration is better? It all depends on the objectives and desired characteristics of the network in the business context.
Download free eBooks at bookboon.com
31
Fundamentals of Supply Chain Management
Supply Chain Design and Planning
3.3 Extent of Vertical Integration
Much of the supply chain design is determined by the extent of vertical integration. Vertical integration is defined as the single ownership of
consecutive activities along the supply chain. It must not be confused with the concept of supply chain integration. A well integrated supply chain may not have a large extent of vertical integration (see definition of supply chain integration in section 2.3). If an OEM does not have ownership of its suppliers and customers, it is regarded as having a narrow span of vertical integration. On the other hand if it owns a number of tiers of suppliers and customers, it is regarded as having a large extent of vertical integration. Obviously it could also be a forward integrated one or backward integrated one as shown in figure 4.
Please click the advert
Figure 4. The extent of vertical integration
www.job.oticon.dk
Download free eBooks at bookboon.com
32
Fundamentals of Supply Chain Management
Supply Chain Design and Planning
In 1930s, Ford Motor Corporation created vastly vertically integrated automobile manufacturing empire the industry had even seen before or since. Instead of using independent suppliers and contractors to provide the materials and components for the Model T (one of Fordâs famous passenger car), Ford choose to produce them by itself through creating extended Ford owned manufacturing suppliers and taking over some small and medium sized suppliers. It also bought steel mills to produce steels which goes into many parts of the automobile; and glass mills which made window screens for the cars. Ford also bought large pieces of land in Brazil and Southeast Asian countries to grow rubber trees that eventually supplied the rubber materials for making tyres. In the end Ford can proclaim that it did not really need
any suppliers and everything built into his Model T is made by Ford. That story becomes the classical case of what today we call the vertical integration. Obviously, the choice of such large extent of vertical integration of Ford Corporation was for a purpose not by an accident. Historian and academics believe, the purpose then was to exercise control, capture the profitability from the suppliers in the upstream of the supply chain, and obviously the market dominance. Such strategic configuration appeared to have fitted very well to the then business environment, when market demand in volume looked to be permanent, and low price was the definitive market winner. Fordâs sale reached peak. However, large extent of vertical integration has its own weaknesses. It was very rigid in its asset deployment, product line modification and introduction, no flexibility in responding to demand changes (due to fixed production capacity). As Henry Ford once said âOur customers can have any coloured cars they want, so long as itâs black.â This was a statement that acknowledged the systemâs rigidity and inflexibility. In the same period, but on the contrary, the second largest American automobile company GM was pursuing a very different strategy on the extent of vertical integration. Under the leadership of Alfred Sloan (then CEO of GM), GM pursued a âfull-line productsâ strategy that aiming to produce a variety of models from small economical version to large luxury models; some models for family use other for business. To illustrate his strategy, Sloan once put it: âWe will build cars for every purse and purpose.â This is a statement of customer oriented supply chain flexibility. GM saw the market was changing; people will not be satisfied with one model or one colour. They demand variety, upgraded new versions and customisation.
To maintain and further develop the companyâs flexibility and dynamism, GM not only had chosen to use the independent suppliers for many of its materials and components, it even created so called strategic profit unit within the vertically integrated part of the supply chain in order to maintain the drive for competitiveness. GM has never followed Ford to go anywhere near the complete vertical integration. The relatively small extent of vertical integration had given GM the competitive advantage in satisfying the customerâs needs for variety. Soon GMâs sale surpassed Ford and became
the worldâs biggest auto-maker in term of volume. Its world leading position was kept until 2007 when Toyota took over became the biggest volume producer in the world.
The above cases show that a supply chainâs extent of vertical integration has always had profound impact on its development. To large extent a companyâs strategy, operation and performance will depend on the right design of the supply chain configuration. Nevertheless, depending on the nature of industry, product lifecycle and competitive environment, the architecture design of supply chain can vary significantly. Generally speaking, process based industry such as oil industry and chemical industry tends to be more vertically integrated; and the technology intensive electronics industry tends to be less vertically integrated.
Download free eBooks at bookboon.com
33
Fundamentals of Supply Chain Management
Supply Chain Design and Planning
3.4 Outsourcing and Offshoring
On the opposite direction of vertical integration is vertical disintegration where the supply chain comprises of many independent participating members and the OEM does not have a large extent of vertically integrated consecutive operations. In fact for a vertically disintegrated supply chain, considerable part of the OEMâs operations are outsourced to the independent external suppliers in order to achieve maximised value adding and minimised total cost for the supply chain. Hence, like the vertical integration, outsourcing is also a supply chain architecture design issue. Outsourcing or strategic outsourcing is commonly known as the âmake-or-buyâ decision. Organisations may want to contract some of its in-house operations such as design, manufacturing and marketing to its external suppliers. Most often such decisions to âbuyâ the operation instead of âmakeâ itself is aiming at
a reduced cost. If a Chinese organisation can produce the same components at a fraction of the usual cost, it will surely attract many OEMs to outsource the production of the components to it. But it is also possible, that if some companies, say in India, may have much better capability of developing the state-of-the-art IT software it makes sense to outsource the software development operations to them in order to gain the supply chain value adding. The decision and processes of moving any strategically significant operations out to the external suppliers is called outsourcing.
There are two points to clarify from the definition. First, outsourcing is not just a decision of make or buy, but also a process that including indentifying the potential suppliers, contractual negotiation, regular evaluation and review of the outsourced operation. Second, not all operations that carried out by the external suppliers are suitable to be classified as outsourcing; only the strategically significant operations can be classified as outsourcing. For example, to a manufacturing supply chain, outsourcing some key components manufacturing operations is strategically significant; but the external catering service supply used by the same company is not. Thatâs why outsourcing is often interchangeably called strategic outsourcing.
Apart from maximising the value adding and minimising the total cost discussed above, outsourcing has many other potential benefits which could form the prime motive for the decision makers: ⢠Focus on and further developing the core competences
⢠Further differentiated competitive edge
⢠Increasing business flexibility, thus supply chain flexibility ⢠Improved supply chain responsiveness
⢠Raise the entry barrier through focused investment
⢠Enhanced ROI or ROE through downsizing the fixed asset
Download free eBooks at bookboon.com
34
Fundamentals of Supply Chain Management
Supply Chain Design and Planning
Case examples of outsourcing are all around us. Dell is a computer manufacture. In order to develop its strategic competitiveness in customised product configuration, assemble to order, and distribution channel transformation, it decided to put its strategic emphasis on product design and downstream services. To this end they decided to outsource most of its manufacturing operations to Taiwan but retain the design and also vertically integrated downstream channels. Another example is the Benetton Group which is a leading edge garment supply chain in the world. It has the presence in over 120 countries. Its core business is fashion apparel. But, 80% of its manufacturing operation is outsourced to thousands of independent small manufactures. This helped the Benetton group to reduce its manufacturing cost, synchronise the supply chain capacity with the fluctuated market demand, and alleviate the bullwhip effects. From an OEM perspective the supply chain is less vertically integrated if more operations are outsourced. Similarly, less outsourcing means higher level of vertical integration. Across most of the manufacturing industries around world, the recent decades have seen a clearly increased level of outsourced activities, and thus the reduced extent of vertical integration for most of the supply chains. This is largely due to the continuous growth of global market volatility which drives the supply chains to become more flexible and agile, and the less vertically integrated supply chain offers precisely that flexibility. Another closely related concept in supply chain architecture design is called âoffshoringâ. Offshoring is defined as moving the on-shore operations to offshore locations in order to take the advantages of local resources, and to reduce operating cost or create market presence. However offshoring does not necessarily mean outsourcing, especially when the ownership of the off-shored operation remains unchanged. There has been no outsourcing taken place. The inter-connection of the two concepts can be illustrated in figure 5.
Please click the advert
Is your recruitment website
still missing a piece?
Bookboon can optimize your current traffic. By
offering our free eBooks in your look and feel, we
build a qualitative database of potential candidates.
Contact us to hear more
[email protected]
Download free eBooks at bookboon.com
35
Fundamentals of Supply Chain Management
Supply Chain Design and Planning
Figure 5. Outsourcing vs. off-shoring
The types of outsourcing business can be broadly observed in three categories. ⢠Business process outsourcing (BPO)
— Marketing / call centre outsourcing
— R & D process outsourcing
— Engineering process outsourcing (EPO)
— HR and recruitment process outsourcing
— Knowledge process outsourcing (KPO)
⢠Business function outsourcing
— Financial auditing
— IT services
— Logistics services
⢠Facility and man power outsourcing
— Capital equipment leasing
— Free length experts hiring
Outsourcing is relatively simple to understand as a concept, but is difficult to implement in practice. The debate surrounding the outsourcing decisions can be lengthy and complicated. The decision often will involve many factors from all levels of management and are intricately inter-related. It is therefore recommended that managers should set up and follow an appropriate process to make the outsourcing decisions and execute the decisions. Here is a set of common steps of outsourcing processes:
Download free eBooks at bookboon.com
36
Fundamentals of Supply Chain Management
Supply Chain Design and Planning
1) Understand competitive environment
2) Clarify the strategic objectives and processes
3) Analysing the market needs
4) Identify internal resources and competencies
5) Make or buy decision making
6) Identifying strategic suppliers
7) Deciding on the relationships
8) Performance evaluation and reviewing
To give managers some hands-on support in outsourcing decision making. Many tools have been developed by the academics and practitioners alike. They are very useful to get the managers started to create tools or frameworks that tailored to their own business cases. Those tools clarify the decision criteria, visualise the decision progress, communicate the ideas, and document the decisions process. Two of those tools are shown in Figure 6 and Figure 7.
Figure 6. The logic decision tool for out sourcing (adopted from Nigel Slack 2005)
Download free eBooks at bookboon.com
37
Fundamentals of Supply Chain Management
Supply Chain Design and Planning
Figure 7. the matrix decision tool for outsourcing (from Abbetti 1997)
Turning a challenge into a learning curve.
Just another day at the office for a high performer.
Please click the advert
Accenture Boot Camp â your toughest test yet
Choose Accenture for a career where the variety of opportunities and challenges allows you to make a difference every day. A place where you can develop your potential and grow professionally, working alongside talented colleagues. The only place where you can learn from our unrivalled experience, while helping our global clients achieve high performance. If this is your idea of a typical working day, then Accenture is the place to be.
It all starts at Boot Camp. Itâs 48 hours
that will stimulate your mind and
enhance your career prospects. Youâll
spend time with other students, top
Accenture Consultants and special
guests. An inspirational two days
packed with intellectual challenges
and activities designed to let you
discover what it really means to be a
high performer in business. We canât
tell you everything about Boot Camp,
but expect a fast-paced, exhilarating
and intense learning experience.
It could be your toughest test yet,
which is exactly what will make it
your biggest opportunity.
Find out more and apply online.
Visit accenture.com/bootcamp
Download free eBooks at bookboon.com
38
Fundamentals of Supply Chain Management
Supply Chain Design and Planning
Nevertheless, outsourcing like many other management activities is not without any risks. Far from it, the biggest concern of outsourcing is perhaps the risk that it brings about.
⢠Negative impact on companyâs personnel
⢠Loss control over key strategic design task, sub-system or component, resulting in negative impact on the companyâs competitiveness.
⢠Could creating tomorrowâs competition
⢠Risk of severe business disruption due to failed supply from single sourced suppliers ⢠Tactical, short term approach to outsourcing may inhibits continuous improvement and long term investment
⢠Intellectual property right risks
⢠Foreign currency exchange risk if involves overseas suppliers Therefore, an outsourcing decision and its executions must be regularly reviewed and assessed against those risks strategically. The review is essential because the changing business environment could easily make the originally right
decision no longer justifiable. When the capital or financial circumstance changes like the one in the economic downturn, the outsourcing decision may have to be revised accordingly. Internal development of technologies and technical competences could also affect the outsourcing decisions.
3.5 Location Decisions
The choice of geographical locations for supply chain operations is another important decision area for supply chain design and planning. Location decision is about the geographical positioning of the supply chain functions (such as assembly and distribution). It is normally done for the purpose of better serving the customers and further reducing the operational cost in the supply chain. Clearly, not all the locations are suitable for the supply chain operations. But one thing is assured that when changing a location, many business-related factors change along with it. That makes the location change a powerful management instrument. Without doubt, a location decision will have profound impact on labour cost, material cost, taxation, currency exposure, financial and legal regulations and so on. These will further lead toward the significant changes in business outcomes, supply chain performance, and even environmental consequences. It is important to understand that the operational considerations for the location decisions are not enough for the supply chain location design. Operational considerations for choosing a location are still valid and useful, but they are mainly the measures of the operations costs from many different dimensions. The operational location design, for example will take into account of multiple factors on the supply side of operations as well as on the demand side of operations as shown in figure 8.
Download free eBooks at bookboon.com
39
Fundamentals of Supply Chain Management
Supply Chain Design and Planning
Figure 8. factors influence the operational location decisions.
However the location design for the whole supply chain will mainly consider two aspects of the whole supply chain. The single operationâs location decision has to be made in conjunction with the other operationsâ locations decisions. In other words it is the combined effect of all locations together that matters for the supply chain. It has been well documented that the total supply chain cost consists broadly two components: the physical cost and market cost (as shown in figure 9).
Figure 9. Supply chain total cost
The physical cost measures the supply chain operational efficiency as a whole. It looks at all the involved cost that are necessary for the supply chain to transform the raw materials to the end products for the consumer. It includes the production cost, logistics cost, material cost, labour cost, taxation cost, energy cost and so on. The market cost looks at all the loss or cost incurred by the inappropriate supply chain market mediation. If a supply chain failed to produce the products that are the right quantity for the market at the season, delivered to the right location where customers find it convenient to access to, with right quality and functions that they expect, at the right prices that they are willing to pay for, the supply chain will make loss either on unsold products or unsatisfied customers. measured by the product delivery process (PDP) cost in general.
Download free eBooks at bookboon.com
40
Fundamentals of Supply Chain Management
Supply Chain Design and Planning
The locations decision for the supply chain, therefore, will have profound impact on both components of the supply chain cost, which in turn give rise
to its importance in the supply chain design and planning. However, in practice, due to the complexity of many factors involved, making a decision could be difficult; or rather to justify the merit of one decision over another could be very tricky. To facilitate managers to make such decision, I would suggest to use the common weighted scoring method as shown in figure 10.
Figure 10. the weighted scoring method. (source: Slack et.al. 2006)
Step 1
Identifying the criteria which will be used to evaluate the various locations. Obviously, the criteria what are chosen must serve the strategic intention of the decision maker, and depend on the specific circumstances surrounding the location.
The Wake
Please click the advert
the only emission we want to leave behind
.QYURGGF ‘PIKPGU /GFKWOURGGF ‘PIKPGU 6WTDQEJCTIGTU 2TQRGNNGTU 2TQRWNUKQP 2CEMCIGU 2TKOG5GTX 6JG FGUKIP QH GEQHTKGPFN[ OCTKPG RQYGT CPF RTQRWNUKQP UQNWVKQPU KU ETWEKCN HQT /#0 &KGUGN
6WTDQ
2QYGT EQORGVGPEKGU CTG QHHGTGF YKVJ VJG YQTNFoU NCTIGUV GPIKPG RTQITCOOG s JCXKPI QWVRWVU URCPPKPI HTQO VQ M9 RGT GPIKPG )GV WR HTQPV
(KPF QWV OQTG CV YYYOCPFKGUGNVWTDQEQO
Download free eBooks at bookboon.com
41
Fundamentals of Supply Chain Management
Supply Chain Design and Planning
Step 2
Establish the relative importance of each criterion through discussion and brain storming. Then assign the weighting factors to each of them. The total sum of the weighting scores must equal to 100, thus the scores will conveniently represent the proportion of the weight in term of percentage.
Step 3
Rate each of the alternative locations against the criteria based on a defined scale. The scale could be between 1 to 9 or 0 to 100, where 1 or 0 represent the worst possible score and 9 or 100 the best. The scoring is normally subjective and hence it is more reliable if a group of people join the scoring together. Step 4
Multiply the weighting allocated to each criterion by the score in each location. Then for each location the overall score becomes the sum of (score for each criterion x weight for each criterion). The highest overall scored location is regarded as the most appropriate one.
3.6 Capacity Planning
Business capacity planning is a big subject on its own. What I am going to talk about is the capacity related planning issues for supply chain architecture design. If one observes the supply chain from the spectrum of capacities of each and every participating members, then an usually uneven capacity âlandscapeâ emerges. The question then is that which form of the landscape is the most beautiful one for the supply chain. The answer to this question surely cannot come from one companyâs capacity planning, as the landscape is formed along with others. This means supply chain capacity planning differs from organisational capacity planning in that it is coordinated endeavour.
One can consider a single column supply chain with n (number) participating
members. Each member has a known capacity Ci. Then a relevant question here would be âwhat is the capacity of the whole supply chain?â The answer to this question is undoubtedly âthe minimum of all the known capacities Ci.â
Download free eBooks at bookboon.com
42
Fundamentals of Supply Chain Management
Supply Chain Design and Planning
One can imagine a supply chain as a piece of water pipe with different diameters at different sections. The overall flow of the pipe, which represents the total capacity of the supply chain, depends on the smallest diameter section. In the situation of networked tiered supply chain structure, the overall capacity of the supply chain becomes the double layered minimum. For each tier i the overall capacity is ; and the whole supply chainâs capacity becomes.
This capacity modelling analysis reveals a capacity bottleneck problem. Thus, to resolve the supply chain capacity planning problem, the key is to identify and open up the capacity bottleneck. To work on the other links of the supply chain, which do not form the bottleneck, is unnecessary and futile as it will not affect the total capacity of the supply chain. However, when one bottleneck capacity has been increased, logically the next smallest capacity link will become the bottleneck instead; and it will then become the focus of capacity management subsequently. There are already well established theories on the bottleneck problems, called âthe theory of constraintâ. In supply chain management, not only the capacity planning can apply the theory of constraint, so does the quality management, technology management, lead-time management, because every part of supply chain do have bottlenecks big or small in theory at least. To carry out the capacity planning in real-world supply chain, however, one needs to deal with it in three levels. The first is the companyâs internal capacity planning and
management, which could be understood as the internal supply chain capacity management. The second level is the companyâs external capacity coordination and synchronisation with the other members of the same supply chain, which can also be understood as the supply chainâs internal capacity planning. The third level is the supply chainâs capacity responsiveness to the market demand changes, which can be understood as the capacity synchronisation between the supply chain and the customer demand. At the level 1
Managers will have to manage the company internal capacity synchronisation to achieve the capacity planning objectives. This is because the desired capacity for the supply chain will eventually to be executed and implemented by each and every individual participating member of the supply chain. Thus for an organisation to achieve supply chain capacity planning, it must also be able to manage and synchronise the organisational internal capacities. This simply means that each functional silo will need to be coordinated with each other to avoid bottlenecks or over-capacity throughout. This also means to make use of the safety inventories, manage smaller batch sizes and keep synchronised flows of materials.
Download free eBooks at bookboon.com
43
Fundamentals of Supply Chain Management
Supply Chain Design and Planning
At the level 2
The key to achieved optimised capacity for a supply chain lies in its external synchronisation. The need for synchronise the capacities of each participating member is very simple. It is to reduce and eliminate the waste incurred by the redundant capacities and to eliminate possible risks of short supply due to the bottlenecks. However, when it comes to actually achieving these supply chain wide capacity synchronisation, difficulties cannot be underestimated. First, a truly synchronised capacity can only be
achieved when the involving members are strategically aligned and operationally integrated with each other. Second, to achieve a synchronised capacity for the supply chain, the participating organisation may have to re-structure its assets and even make some capital investment; without a committed long term close partnership, such capital investment and asset re-deployment is unlikely to be achieved swiftly. Third, capacity synchronisation can only be a result of matured, culturally embedded and technically compatible operating systems across the supply chain. At the level 3
The whole supply chainâs capacity must be synchronised with the market demand changes, and market demand change is often unknown or uncertain. Forecasting has long been used to assist the planning of the supply chainâs capacity but with limited successes. The credential of the analytical forecasting methods has not lived to its promises. As the result forecasting is either lucky or wrong. Thus supply chain managers must resort to other more effective means of managing capacity synchronisation and ultimately the supply chain responsiveness. Last two decades have seen some encouraging progress in achieving high level of supply chain responsiveness. Today, supply chains are more active in creating and developing flexible capacity and flexible structure through outsourcing, vertical disintegration, virtual networks, and sharing and pooling resources, to name just a few. But so far there is no single silver bullet discovered in this respect. The ways that industries manage their own capacity and responsiveness varies significantly.
3.7 Bullwhip Effect
Capacity synchronisation has another major beneficial effect. It helps to alleviate the Bullwhip Effects in the supply chain, and the bullwhip effect is a very common phenomenon which has many negative impacts on the supply chain performances. Understanding the bullwhip effect is therefore essential to the supply chain design and planning.
Download free eBooks at bookboon.com
44
Fundamentals of Supply Chain Management
Supply Chain Design and Planning
Bullwhip effect is also known as Forrester Effect as Jay Forrester (1961) showed that this was so by modelling supply chain mathematically and he called it industrial dynamics. What happened basically is that when the small demand ripple in the market place is felt by the retailer at the end of the supply chain, the retailer will then start adjusting their orders to the wholesalers, and the wholesaler in turn will adjust its orders to the distributer, and the distributer to the factory. One would imagine when the factory receives the orders, it will have the equally small changes. Unfortunately, it could not be farther from the truth. The small ripples have been significantly amplified stage by stage towards the upstream of the supply chain. When it reaches the factory or components manufacture the magnitude of fluctuation becomes unrecognisable. Figure 11 shows such changes.
Period 1
Period 2
Period 3
Retail Sales
+10%
-10%
+10%
Distribution Orders from Retail
+17%
-21%
+32%
Factory Orders from Distributor
+30%
-40%
+48%
Manufacturing Orders from
Factory
+45%
-66%
+80%
Factory output
+39%
-60%
+72
Figure 11, Example of bullwhip effect
Such phenomenon has been observed repeatedly and reliably through all types of supply chains. It is therefore appropriate to generalise it and theorise
it as a universal âeffectâ model, through which analysis and simulations can be applied. Basically, the bullwhip effect has three key characteristics. The first is oscillation. The demand, orders or inventories move up and down in an alternative pattern. The second is amplification. The magnitude of the alteration and fluctuation increases as it travels to the upstream end of the supply chain. The third is phase lag. The cycle of peaks and troughs of one stage also tends to lag behind the one in the previous stage. Those characteristics can be clearly demonstrated by a supply chain simulation game.
The Beer Game
To illustrate the bullwhip effect in the supply chain dynamics, MIT Sloan School of Management created a so called Beer Distribution Game or just Beer Game. The Beer Game is the most widely played game in business schools around the world. Many modified versions have also been developed and used extensively, but the one shown in this book is the original version. Despite the variation of the games played around world, the key features and the learning points remain largely the same.
Download free eBooks at bookboon.com
45
Fundamentals of Supply Chain Management
Supply Chain Design and Planning
The game is a role playing simulation of a supply chain originally developed by Jay Forrester in the late 1950s to introduce students of the concept of system dynamics and its management. The game is played on a board portraying a typical supply chain (figure 12). The supply chain distributes beers and has four sectors: retailer, wholesaler, distributor, and factory. One or two persons manage each sector. A deck of cards represents customer demand. Each week, customers demand beers from the retailer; the retailer fills the order out of inventory. The retailer in turn orders beer from the wholesaler, who
ships the requested beer from the wholesale stocks. Likewise the wholesaler orders and receives beer from the distributor, who in turn orders and receives beer from the factory, and the factory produces beer. At each stage there are order processing and shipping delays. Each link in the supply chain has the same structure.
Brain power
Please click the advert
By 2020, wind could provide one-tenth of our planetâs
electricity needs. Already today, SKFâs innovative knowhow is crucial to running a large proportion of the worldâs wind turbines.
Up to 25 % of the generating costs relate to maintenance. These can be reduced dramatically thanks to our systems for on-line condition monitoring and automatic
lubrication. We help make it more economical to create
cleaner, cheaper energy out of thin air.
By sharing our experience, expertise, and creativity,
industries can boost performance beyond expectations.
Therefore we need the best employees who can
meet this challenge!
The Power of Knowledge Engineering
Plug into The Power of Knowledge Engineering.
Visit us at www.skf.com/knowledge
Download free eBooks at bookboon.com
46
Fundamentals of Supply Chain Management
Supply Chain Design and Planning
Figure 12. The beer game board
The playersâ objective is to minimize the total cost for their company. Inventory holding costs are usually set to $0.50 per case per week, and stock out costs (costs for having a backlog of unfilled orders) are $1.00 per case per week. The task facing each player is a typical example of the stock management problem. Players must keep their inventory as low as possible while avoiding backlogs. To fulfil the incoming orders the inventory has to be depleted, so the players must place replenishment orders in order to adjust their inventory to a desired level. There is a delay between placing and receiving orders, just like in real-world business case, creating unfilled orders. There are also shipping delays that even the supplier despatched the goods it will take time to arrive, which is often the case in real-world. This results in the inability to adjust the inventory level quick enough to avoid the backlogs.
Clearly, the game is far simpler than any real supply chain. There are no random events â no machine breakdowns, and transport problems, or strikes. There are no capacity constraints or financial limitations. Above all the structure of the supply chain is visible to all, which is rarely the case in real life. Players can readily inspect the board to see how much inventory is in the transit or held by their teammates. The game is typically played with a very simple pattern of customer demand. Starting from 4 cases per week for the first few weeks and then jumped to 8 cases per week and stays there until the end. Despite the apparent simplicity of the game, people do extremely poorly. For most of the first time player average costs are typically an astonishing 10 times greater than optimum. Figure x shows the typical results of the game. In all cases customer orders are essentially constant except for the small step increase near the start. In all cases the response of the supply chain is unstable. The oscillation, amplification and phase lag observed in real supply chains are clearly visible in the displayed result. In the period of 20-25 weeks, the average amplification ratio of factory production relative to customer order is a factor of 4.
Download free eBooks at bookboon.com
47
Fundamentals of Supply Chain Management
Supply Chain Design and Planning
Figure 13. Typical results of the Beer Game (Sterman, 2001).
Most interesting, the patterns of behaviour generated in the game are remarkably similar. Starting with the retailer, in the 20 weeks or so, inventories decline throughout the supply chain, and most players developed a backlog of unfilled orders (negative net inventory). In response, a wave of orders moves through the chain, growing larger at each stage. Eventually, factory production surges, and inventories throughout the supply chain start to rise. But inventory does not stabilize at the cost-minimising level near zero. Instead, inventory significantly overshoots. Players responded by slashing orders, often cutting them to zero for extended periods. Inventory eventually peaks and start decline again. These behaviours are all the more remarkable because there is no oscillation in customer demand. The oscillation arises as the consequence of the players activities. Although plays are free to place orders in any way they wish, the vast majority behave in a remarkably uniformed fashion.
The causes of the bullwhip effect are systemic. They are a combination of structured delays both in order processing and shipping, over ordering and ignoring the incoming good in the pipeline, under ordering and failing to see the build-up of downstream demand, panic and over react, lack of coordination, poor forecasting and so on. In real-world supply chain operations, there will be even more factors that worsening the bullwhip effect, such as batching, facility breakdown, poor maintenance, inappropriate scheduling and communication, poor capacity coordination, market disruptions and many more.
Download free eBooks at bookboon.com
48
Fundamentals of Supply Chain Management
Supply Chain Design and Planning
How to alleviate the bullwhip effect? There is no single cure-all recipe. But there are some commonly agreeable countermeasures to the bullwhip effect:
â˘
Improve information sharing through EDI (electronic data interchange), POS (point of sale systems), and web-based IS (information systems).
⢠Reducing batch ordering
⢠Coordinating capacity and production planning
⢠Apply appropriate safety stocks to insulate the oscillation ⢠Reducing inventory level through JIT (just in time), VMI (vendor managed inventory), QR (quick response). All those approaches must be executed cohesively in an integrated manor. A bullwhip effect proof supply chain will also call for a very high degree of inter-organisational collaboration by which systematic coordination in capacity planning,
Please click the advert
inventory management, cost-to-serve, lead-time reduction and responsiveness can be effectively achieved.
Download free eBooks at bookboon.com
49
Fundamentals of Supply Chain Management
Lean Supply Management
4 Lean Supply Management
4.1 Origins of the Lean Manufacturing
Over the span of circa 40 years time, from the beginning of 1950s to the end of 1980s, Toyota led Japanese automotive industry created a unique production / manufacturing system, which brought the industry from the ruins of the 2nd World War to the biggest automobile exporter in the world. That system was known as the Toyota Production System (TPS), now more commonly known as lean manufacturing. The term âleanâ was first coined in a large scale research programme called IMVP (International Motor Vehicle Programme) initiated by MIT (Massachusetts Institute of Technology). The primary concern of the programme was the unanticipated yet strong competitive advantages of Japanese automotive industry over that of Americanâs and Europeanâs. The key findings of the programme have been published in many books and articles. One of them is a bestseller book entitled âThe Machine that Changed the Worldâ, in which the term âleanâ is defined as we know it today.
Lean manufacturing is a comprehensive production management system developed in Toyota originally but later gradually refined and improved by many scholars and practitioners around world. There are two major features of lean manufacturing that distinguishes it from mass production are: first, increased efficiency through the reduction of waste and error; and second, reduced carrying cost of inventories achieved by manufacturing in small âbatchesâ. The key ingredient to success of the system is Japanâs highly skilled workforce. The overriding concept of the lean system is about doing more with less â a philosophy for identifying and removing waste across the whole business activities. It is also about adding value for the customer and for the business and it is customer driven. Lean manufacturing was not designed and implemented overnight. It took long years of relentless drive, continuous improvement, trial-and-error, and gradually perfected a system that works best. Compared with the mass production system, lean manufacturing centres management improvement on people especially the operators on the shopfloor. Whether it is quality circle or total preventive maintenance, it is the actively participating workforce that makes them
work. Lean Manufacturing focus on the add value from demand. The whole production system is basically pulled from the demand rather than entirely depend on forecasting based scheduled production. Product customisation and increased scope of customer choices are the direct results. Lean manufacturing develop and make use of employeeâs intellectual assets. Everyone is encouraged to make improvement suggestions and even have the power to stop the assembly line if they see something wrong. High commitment, hard working, well educated workforce and loyalty to the company become part of the organisational culture.
Lean manufacturing emphasises the optimisation across organisations and supply bases not just the functional silos. It promotes close partnership relations with the first tier suppliers and other strategic partners in the distribution channel. It created the tiered supply base structure. The waste between the organisations, often ignored in the past, has been identified as key improvement area. The modular design of the automobile has been master minded to fit to the tiered supply structure. All in all, the lean system has also transformed the supply chain management which we call the âlean supply managementâ. This is precisely I am going to discuss in this chapter.
Download free eBooks at bookboon.com
50
Fundamentals of Supply Chain Management
Lean Supply Management
4.2 Lean Supply Principles
To understand whatâs unique about lean supply and how it works, one must first examine the supply chain practice in mass production, knowing the whole lean manufacturing system was originally evolved from inherited mass production system. In the mass production supply system, the mass producer buys its basic components from a large supply base. The supplier number will normally reach 5000 to 8000, bearing in mind that a modern automobile will
have more than 20,000 basic components built into it. As shown in Figure 14 the mass supply structure is very flat. The mass producer takes on the assembly of the whole vehicle as well as many subsystems and modules. Thus the level of outsourcing is relatively low.
Figure 14. Mass supply chain structure.
The mass producer will design the parts to be made by the suppliers. The process is basically a sequence of one-step-a-time from design, bid, prototype, check, contract and make. With this system, when it comes to find and select the supplier, the cost will always come first. Whosever can make the same part at a lower price will win the bid. This will often lead to a scenario that the suppliers will quote a low price to win the bid and then expecting to raise the price through the annual price adjustment. Suppliers will hardly share any information with the buyer other than the volume and price. The consequence of the mass supply system is far from beneficial. Supplier brought into the production too late that even the suppliers have better ideas on the design; it would be too late to change. Perhaps the buyer never intended to make use of the suppliersâ know-how on the design of the vehicle anyway. Intense cost pressure from the buyer to suppliers are detrimental that the buyer often play-off the suppliers making them reluctant to share production information. This also made it impossible for the buyer to estimate the true cost of making the parts. When the supplier has improved its production efficiency there is no incentive to merge the learning curve (to share the saving). All these resulted in high parts cost and unsatisfactory quality.
Over the years the Japanese developed a set of completely different practices â the lean supply system (Figure 15). They can be summarised in 10 lean supply principles that are in stark contrast with what the mass supply system was about.
Download free eBooks at bookboon.com
51
Fundamentals of Supply Chain Management
Lean Supply Management
360°
thinking
Please click the advert
Figure 15. Lean supply chain structure.
360°
thinking
.
.
360°
thinking
.
Discover the truth at www.deloitte.ca/careers
Š Deloitte & Touche LLP and affiliated entities.
Discover the truth at www.deloitte.ca/careers
Š Deloitte & Touche LLP and affiliated entities.
Download free eBooks at bookboon.com
Š Deloitte & Touche LLP and affiliated entities.
52
Discover the truth at www.deloitte.ca/careers
Š Deloitte & Touche LLP and affiliated entities.
D
Fundamentals of Supply Chain Management
Lean Supply Management
1) Supply from a smaller 1st-tier supply base: As shown in figure 15 the lean producer also use large number of suppliers, but it manages them in a tiered structure. The suppliers directly supply the buyer is called the first tier supplier. It is this group of first tier suppliers that the lean producer now deals with directly and gets all the supply of subsystems and modules and components from. Hence the first tier suppliers group is called the supply base. The number of suppliers in the supply base for the lean structure is about 200 to 300. It is significantly lower than what mass supply system used to have. Using small supply base is a distinct supply chain configuration the all lean supply chains have in common. This structure change has led to a raft of supply chain behaviour changes that really deliver the advantages. 2) Develop appropriate usually close partnership: by using a much smaller supply base, the lean producer can manage to spare more time and other resources to interact with each and every one of the first tier suppliers. This has made it possible for the operational relationship between the buyer and the suppliers to become close. As will be discussed in the Chapter 7, the close and highly engaging relationships are usually defined by the contents of the exchanges in between. The close partnership will typically entail the shared vision and mission, joint design and development of new products, strategically collaborated capital investment planning, capacity synchronisation, coordination on JIT delivery and inventory optimisation. The contractual terms for the suppliers are normally from medium to long term. The communication and engagement are at multiple levels in both formal and
informal regularity. 3) Supplier selection based on performance: when the lean producer selects its suppliers, price is no longer the only criterion, nor the most important criterion like what mass producer will do. Lean producers will base its ranking and selection on a number of higher level performance focused criteria, such as quality standard, R&D capability, delivery reliability, management system and standard, commitment and relationship. Price will also be considered as one of the criteria, but it will always be referenced to the value that the company can offer. Details of supplier selection will be discussed in Chapter 6. Once selected as the suppliers, the lean producer will treat them as the âfamily memberâ and an open and trust culture will be enforced.
4) Single or dual sourcing only: Lean producer tends to prefer the âsingle sourcingâ or âdual sourcingâ strategy, not âmultiple sourcingâ. Single sourcing means the lean produce will source the product (with unique SKU) from only one supplier. This means there is no back-up suppliers and no duplicated suppliers for the same product. Compare with the multiple sourcing strategy, single sourcing has a number of key advantages. It consolidates the volume to one supplier so that the unit cost can be minimised; the supplier will reap the benefit of economy of scale. It provides the convenience and focus when research and product development is required; to deal with two different companies for the same product design could raise unnecessary complications. It helps to develop close partnership; to contract the product to a single supplier is, in itself, a clear statement of trust and partnership initiation. However, there are also a number of risk factors involved in the single sourcing strategy. The risk of supply breakdown for whatever the causes could be an issue; lack of competition may promote complacency.
Download free eBooks at bookboon.com
53
Fundamentals of Supply Chain Management
Lean Supply Management
5) âMarket price minusâ rather than âSupplier cost plusâ: Lean supply chain deals with the pricing issue very differently. In mass supply system, the supplied component price is normally determined by the unit cost of making the component by the supplier plus the profit margin that the supplier needs to make. That is whatâs called âsupplier cost plus (margin)â. The problem with this approach is that the supplierâs cost model is accepted without questioning. The uncompetitive supplier cost could slip into the supply chain and compromises the supply chain competitiveness. Lean producer use the âmarket price minusâ approach. It first determine the market price of the supplied component through market research and benchmarking; then take away (minus) the agreed reasonable profit margin that the supplier need to make on each unit; whatâs left is the âtarget costâ. If the target cost is lower than supplierâs actual cost, the buyer and the supplier will then work together to lower the cost to meet the target cost. In this way, both the market price and the profit margin for the supplier are secured. This also means that all the pricing in the supply chain are market acceptable, thus secures the product success.
6) Early and close engagement with suppliers for NPI: In mass supply system, the new product introduction is solely designed by the mass producer â the buyer; and the supplierâs job is simply to make it according to the blueprint given; the supplier has no involvement in the design stage. Lean supply system choose to identify its suppliers first and then get them involved in the design and planning stage for the new product introduction. This way the suppliers will have plenty opportunities to contribute their expertise to the design and by working with the engineers from the buyer innovation and new ideas can be generated much more effectively. The engineers from the supplier may work in the buyerâs site as the âresidential engineerâ as if they are the same company. In this way, many later stage production and engineering problems can be eliminated in the earliest design stage. It is an important part of supply chain collaboration and integration. 7) Synchronised flexible capacity: In the lean supply system, the assigned capacity for both suppliers and buyers are not permanently
fixed, because a fixed capacity will either be over-capacitated when the demand is low; or it will be under-capacitated when the demand is high. More importantly the capacities of the supplier and buyers throughout the supply chain should ideally be synchronised to achieve the optimum supply chain efficiency. Lean supply system build on a largely synchronised flexible capacity. The key is to have the flexible capacity at each link of the supply chain. This capacity flexibility means having the ability to rapidly increase or decrease production levels, or to shift production capacity quickly from one products or service to another. Such flexibility is achieved through flexible plants, processes, and workers, as well as through strategies that use the capacity of other organisations. 8) Just-in-time delivery: JIT is a well known lean approach. It represents the key philosophy and characteristic of lean manufacturing and lean supply chain. JIT is an approach to material control based on the view that a process should operate only when a customer signals a need for more parts from that process. When a process is operated in the JIT way, goods are produced and delivered just-in-time to be sold. This principle applies to the entire lean supply chain. Parts are produced and delivered just-in-time to be built into the subassemblies. Throughout the supply network, the trigger to start work is governed by demand from the customer. A lean supply chain can be conceived as a chain of customers, with each link coordinated with its neighbours by JIT signals. The whole supply chain is triggered by the demand from the end-consumer in the market place. This system of flowing materials and good through the supply network is characteristic of a pull system. Parts are pulled through the chain in response to demand from the end-consumer.
Download free eBooks at bookboon.com
54
Fundamentals of Supply Chain Management
Lean Supply Management
9) Incentive and reward alignment: Lean supply chain pays great attention on the alignment with the suppliers through incentive and reward. The objective of the lean producer as the buyer is not to take piece of profit from the supplier, but to work with the supply to get the cost down so that together they build a stronger supply chain. The contributions that suppliers made to the cost reduction will be rewarded and incentivised. The typical practice is that when the supplier made x amount of saving through efficiency improvement, 50% of which will be retained by the supplier rather than become the cost cutting of the component to the buyer. Contributions on better design and quality improvement will be rewarded with more businesses. This approach not only aligns the value adding to the reward, but also significantly boosts the suppliersâ motivation and commitment in creating a competitive supply chain. 10)Willingness to share a substantial part of its proprietary information: Lean supply chain also represents a culture of mutual trust loyalty at least and usually within the supply chain. Suppliers are willing to share substantial amount of proprietary information with the buyer. This openness and trust not only makes the supply chain much more visible, thus easy to coordinate, but more importantly it creates synergy between the parties. The value of information increases when it is shared and made use of more widely.
Please click the advert
Increase your impact with MSM Executive Education
For almost 60 years Maastricht School of Management has been enhancing the management capacity of professionals and organizations around the world through state-of-the-art management education. Our broad range of Open Enrollment Executive Programs offers you a unique interactive, stimulating and multicultural learning experience.
Be prepared for tomorrowâs management challenges and apply today. For more information, visit www.msm.nl or contact us at +31 43 38 70 808 or via [email protected]
the globally networked management school
For more information, visit www.msm.nl or contact us at +31 43 38 70 808 or via [email protected]
Download free eBooks at bookboon.com
18-08-11 15:13
Executive Education-170×115-B2.indd 1
55
Fundamentals of Supply Chain Management
Lean Supply Management
4.3 Focusing on Cost-to-Serve
To think lean supply chain is just a cost cutting supply chain would have miss the significance of the lean by miles. It would become a âmeanâ supply chain if that is the case. Although, cost and efficiency appears always on the top agenda when it come to make a process leaner, but the subtle yet fundamental difference between low cost and lean supply chain can never be ignored. A slight misunderstanding of the concept could have a long lasting detrimental consequence in supply chain performance. In a lean supply chain, a cost-cutting idea can only be acceptable if it passes the âcost-to-serveâ test. In other words, the focus of lean is not on the cost but on the cost-to-serve.
Organisations have been applying lean concepts to corporate logistics systems and the wider domain of supply chain management ever since Toyota demonstrated its undisputable leadership position in production management. However, as so often occurs when new concepts are applied to supply chain thinking, people can start to have unreasonable expectations about the actual benefits. The cause of such unreasonable expectation appears always stemmed from the misconception of the original terms and ideas.
The fundamental concept of lean is identifying and eliminating waste in the material, processes, time and information, and adding value perceived from the eyes of consumer. Thus waste is the one to be cut across the management spectrum, not necessarily the cost. When a cost is identified as the waste, which does not seem to have added any value, it should be rightly slashed. The key issue here, therefore, is to looking for the cost that adds no value. If the cost that does add value to the supply chain has been cut, value has been cut with it. There is little justification why should value adding cost is to be cut. Toyotaâs three original criteria for value adding activities are: 1) There must be physical changes
2) It must be concerned by the customer
3) It must be right first time
Wasteful activities are therefore defined as non-value adding activities. This is where the concept of âserveâ kicks in. If the activity adds the value and the value is perceived by the customer, the activity âservesâ the customer. Therefore an appropriate translation of the lean principles in terms of attitude towards the cost should be that to identify and eliminating the non-value adding or non- âservingâ activities. Thus, a measure for how wasteful is a cost or a cost incurring activity can be defined by whatâs known as âcost-to-serveâ.
Download free eBooks at bookboon.com
56
Fundamentals of Supply Chain Management
Lean Supply Management
With this measure, one can compare activities to see which one adds more value and which one is more of a waste. When the âtotal cost involvedâ remains unchanged, the more âCustomer perceived value and serviceâ received the lower the âcostto-serveâ, and vice versa. So, the lean approach is not
cost cutting but cost-to-serve cutting, which clarifies the opening confusion in this section. Furthermore, the purpose of lean approach can, therefore, be interpreted as to minimise the level of cost-to-serve.
This lean concept based on cost-to-serve can explain why some supply chains achieve low cost by ensuring customers are not over-serviced, while others achieved much leaner supply chain by investing more into the operation.
4.4 Drivers for Lean Supply Chain
What makes a supply chain lean? Research and literatures have pointed to six key drivers that will lead to a lean supply chain. Driver 1: Waste Reduction
Elimination of waste is one of the key tenets of lean manufacturing. In the broadest sense, waste can be found from all aspect of business activities. It can take the form of time, inventory, redundant process and defects. Supply chain members must work together to identify and eliminate all those possible wasteful and non-value adding elements in order to become lean. This elimination of waste will have a direct and visible consequence, which is the reduction of cost to the supply chain. When the cost reduced, assuming the output of the supply chain remains the same, the supply chain efficiency improves and cost-to-serve reduces. It is crucial that waste must be assessed from supply chain perspective not from a companyâs own individual perspective. For example, a company may move the inventory responsibility to the supplier in order to reduce its own the inventory holding cost. This may seem to be a âwasteâ or cost reduction activity. However, from a supply chain perspective, the inventory holding cost has not be eliminated but merely been moved from one section of the supply chain to another.
The emphasis, as discussed in the previous section, must be on the waste but not the cost. Cost cutting, if it becomes the driver, can be very misleading and confusion. A preoccupation of cost cutting often leads to conflict of interest between the parties of the supply chain; and increase the supply chain total costs whilst trying to reduce the cost in an isolated local section. More importantly, the most sinister waste often lies in between the suppliers and buyers and not covered in anybodyâs boundaries. The waste of
supply chain resources by not getting the suppliers involved in the early stages of product development is often not identifiable by either side. It is therefore highly recommended that supply chain should have joint, if not integrated, approach toward waste reduction. Collaborative policies and jointly formed multifunctional teams are much more effective in identifying the waste lurking in the gaps of the supply chain. Download free eBooks at bookboon.com
57
Fundamentals of Supply Chain Management
Lean Supply Management
Driver 2: Demand Management
Managing demand is by far one of most important frontier that supply chains compete in the market place, and there is always significant room for improvement. In fact, the performance of the supply chain viewed by the end-consumer is largely hinged on how the consumer demand is managed, fulfilled and satisfied. The status quo of the demand management in supply chains today show it is not just a matter of a good will or customer minded attitude. It is now a measure of supply chain capability which is often facilitated by sophisticated POS (point of sale) data communication system. Demand management thus will be enhanced or constrained by the companiesâ material resource management systems which may or may not be compatible throughout the supply chain.
How well firms manage the demand and demand related information such as forecasting and market signals is also reflected in how they view and manage their collaboration with buyers and suppliers. Real-time collaboration and responses are highly desirable but hardly evident in most of supply chains. Collaboration, not just for demand management, must begin with managementâs understanding and acceptance of the concept, followed by a communicated commitment throughout the managers as well as the workforce. Regular meetings and reviews between the partners should be hardwired into the
processes. Documentation, such as supplierâs manual, could be a great building block.
Please click the advert
See the light!
The sooner you realize we are right,
the sooner your life will get better!
A bit over the top? Yes we know!
We are just that sure that we can make your
media activities more effective.
Get âBookboonâs Free Media Adviceâ
Email [email protected]
Download free eBooks at bookboon.com
58
Fundamentals of Supply Chain Management
Lean Supply Management
Driver 3: Process Standardization
Process standardization enables the continuous flow to run through the company and the supply chain, which represents another tenet of lean supply chain. Flow means the uninterrupted movement of a product or service through the system to the customer. Major inhibitors of flow are work in queue, batch processing, and transportation. These roadblocks slow the time from product or service initiation to delivery, and increase the material and work in process carrying cost. The process flow concept helps to see and understand the value stream of the production and the supply chain. It also represents a shift from the vertical organisational structure and functional silos to a horizontal connectivity of processes in a stream of value. This value stream process linked the business activities to the need of
customers. This means managing the supply chain process flow means focusing on system efficiency rather than activity efficiency. Flow is best enabled when material and processes are standardized across the supply chain to reduce the complexity. But the standardized processes can only be achieved through wide range of close collaborations between the members of the supply chain. The typical processes to be standardized are planning and production. It helps the supply chain up and downstream to have thorough understanding of the process involved. Products and material standardization can help to share the subcomponents across the product lines, which will lead to volume advantages, consistency and operational cost savings.
Driver 4: Engaging People
Lean manufacturing differs significantly from production systems in its people engagement. To implement lean process and develop a lean supply chain, managers must start with engaging people. This means the lean campaign is not just a brilliant idea of the CEO, nor it is the job of executive board, it is task that everyone in the organisation must get involved, especially the operators and engineers in the operational frontier on the shopfloor. The improvement ideas and innovative changes are often come directly from the people who do the job. This also means that ownership of the lean campaign is in the hand of every employee not just a small group of senior managers. Engaging people is a near miracle drive for the lean transformation.
⢠First, by engaging everyone in the company, you have dug into the goldmine of intellectual assets of people. Their knowledge and expertise have been mobilised to contribute to the value adding activities. ⢠Second, engaging people is the best way to motivate them. People are the only active force in the business. How powerful this force is depends almost entirely how well they are motivated for the common courses of the supply chain.
⢠Third, engaging people is the only practical way to change the organisational culture; culture is can only be carried and displayed by people. A lean supply chain can be built to last if and only if it is created with the embedded culture.
Download free eBooks at bookboon.com
59
Fundamentals of Supply Chain Management
Lean Supply Management
Driver 5: Collaboration
Lean philosophy promotes working together and collaboration. Lean supply chain thrives on collaboration. Collaboration can take place between organisations within the supply chain or across different supply chains. Collaboration often results in shred resources leading to high level of economy of scope; it also significantly reduces the business risks for the partners by sharing it and jointly averting it; it promotes technological advancement and innovative product and service development. The power of collaboration has undoubtedly been recognised in all lean enterprises. How to initiate collaboration from the lean supply chain context? It must start with the top level strategic intention from both or all sides. This intention is obviously based on the stakeholderâs interest and the potential benefits that the collaboration may generate. Initial proposal and executive level contact to draw a broad plan and review all the involved factors; then further collaborative areas or projects can then be put into details; finally the implementation and trial programme can be launched. However this is what normally called the top-down approach. Many collaboration is created from bottom-up approaches. In this approach, practice and experience in working together in the past will have laid a good foundation; managers then build on that to expand the scope of activity and formalise the collaboration through institutionalising the processes.
Driver 6: Continuous improvement
Lean philosophy believes the journey to improve will never end. If better is possible good is not enough. It does not need to be a quantum leap; any small steps of changes toward better operations will be encouraged. Toyota
Production System itself was not designed and created by somebody overnight, but rather an ultimate result from long years of gradually, step by step changes through the continuous improvement processes. A continuous improvement process is an ongoing effort to improve products, services or processes. These efforts seek the âincrementalâ improvement at a time and over time; it also embrace the âbreakthroughâ improvement as and when it occurs. Some successful implementations of the continuous improvement have been known as âKaizenâ, which is basically the Japanese word for continuous improvement. The key features of Kaizen are: ⢠Improvements are based on many, small changes rather than one radical changes ⢠Ideas of changes are often come from the workers at the operational front ⢠Small improvements do not usually require any capital investment or major change of process ⢠All employees are engaged to participate to seek the ways to improve their own performance ⢠It encourages the workers to take the ownership of their performance
4.5 Lean Process Mapping Tools
Lean approach, unlike many other âflavour of the monthâ, has been extremely enduring. After three decades of worldwide preaching and application, lean movement is still going strong. In todayâs business management world, lean method is still the most popular one across the world. Over more than 70% of organisations have, to various extents, exercised lean. One of the reasons why lean is so widely applied and continues to be the most favourable method is that it has a set of practical tools that can be readily applied in almost all business circumstances.
Download free eBooks at bookboon.com
60
Fundamentals of Supply Chain Management
Lean Supply Management
The tools created originally by the Toyota production systems are called
âlean process mapping toolsâ. The purposes of those tools are to visualise the material flows in the production lines and in the supply chains; to see where the waste is. They help to pull together the lean thinking principles and facilitate the discussion and communication, and help to identify the bottleneck and prioritise the remedial actions. There are quite many widely used tools that can directly support lean supply chain management. Most of the figures of the tools are sourced from the article âGoing leanâ by Peter Hines and David Taylor (2000).
⢠Value Stream Mapping
⢠Time Based Process Mapping
⢠Process activities mapping
⢠Supply chain response matrix
⢠Logistics pipeline map
⢠Production variety funnel
⢠Quality filter mapping
⢠Demand amplification mapping
Please click the advert
⢠Value adding time profile
GOT-THE-ENERGY-TO-LEAD.COM
We believe that energy suppliers should be renewable, too. We are therefore looking for enthusiastic new colleagues with plenty of ideas who want to join RWE in changing the world. Visit us online to ďŹnd out what we are offering and how we are working together to ensure the energy of the future.
Download free eBooks at bookboon.com
61
Fundamentals of Supply Chain Management
Lean Supply Management
The value stream mapping tool as shown in figure 16 is designed to map out the value adding and wastage from the supplier to customer, including logistics, purchasing, order fulfilment, production processes.
Figure 16. Value stream mapping tool (source: syque.com)
Time-based process mapping tool is a simply âwalk throughâ tool to identify and map out the activity time (suppose to be value adding) and waste time (non-value adding) in every steps that the material has gone through, as shown in Figure 17.
Download free eBooks at bookboon.com
62
Fundamentals of Supply Chain Management
Lean Supply Management
Figure 17. Time-based process mapping
The process activity mapping tool maps out the four different activities: operation, transport, inspection and storage that the materials have to go through. Keys are assigned to each activity types to help visualisation. Plan flow diagram can also be added to optimise the flow.
30 FR
da EE
ys
tria
l!
SMS from your computer
…Sync’d with your Android phone & number
Please click the advert
Go to
BrowserTexting.com
and start texting from
your computer!
…
BrowserTexting
Download free eBooks at bookboon.com
63
Fundamentals of Supply Chain Management
Lean Supply Management
Figure 18. Process activity mapping
Supply chain response matrix is used to evaluate the inventory and lead times incurred by a supply chain in maintaining a given level of customer service. It is used to identify large sects of time and inventory and allows managers to assess the need to hold the inventory.
Download free eBooks at bookboon.com
64
Fundamentals of Supply Chain Management
Lean Supply Management
Figure 19. Supply chain response matrix.
Logistics pipeline map is a compliment to the supply chain response matrix. It shows the accumulation of process time on the horizontal axis and of inventory levels on the vertical axis. It shows exactly where the inventory and time accumulate within each operation (see figure 20).
Download free eBooks at bookboon.com
65
Fundamentals of Supply Chain Management
Lean Supply Management
Figure 20. logistics pipeline map
Production variety funnel is a visual mapping technique that plots the number of product variety at each stage of the manufacturing process. This technique is used to identify the point at which a generic product becomes either increasingly or totally customer specific.
Download free eBooks at bookboon.com
66
Fundamentals of Supply Chain Management
Lean Supply Management
Figure 21. Product variety funnel.
Please click the advert
Who is your target group?
And how can we reach them?
At Bookboon, you can segment the exact right
audience for your advertising campaign.
Our eBooks offer in-book advertising spot to reach
the right candidate.
Contact us to hear more
[email protected]
Download free eBooks at bookboon.com
67
Fundamentals of Supply Chain Management
Lean Supply Management
Quality filter mapping is a tool designed to identify quality problems in the order fulfilment process or the wider supply chain. The map shows where three different types of quality defects occur in the value stream.
Figure 22. Quality filter mapping.
Demand amplification mapping is a graph of quantity against time, showing the batch sizes of a product at various stages of the production process. This may be plotted with a company or along the supply chain. It also can be used to show inventory holdings at various stages long the supply chain.
Download free eBooks at bookboon.com
68
Fundamentals of Supply Chain Management
Lean Supply Management
Figure 23. Demand amplification mapping.
Value adding time profile plots the accumulation of both value adding and non value adding costs against the time. It is an excellent tool for looking at time compression or mapping out where money is being wasted.
Figure 24. Value adding time profile.
Download free eBooks at bookboon.com
69
Fundamentals of Supply Chain Management
Agile Supply Management
5 Agile Supply Management
5.1 The Need for Agility
Having understood the impact and the undisputable success of the lean philosophy applied in many organisations world over. Can we come to a conclusion that the next milestone, after the craft production and mass production, is going to be the lean production? To answer this question, one needs to first establish whether the lean approach can fit to all business environments now and in the future. Researches and literatures so far appear to believe the otherwise. The critical argument here is that the lean system was developed from a forecasting based volume production industrial sector where the market differentiator is reliability and cost, and today large part of our global market is variety dominated and the differentiator is speed and responsiveness. Hence, lean probably is not a cure-all approach after all. The new breed of enterprises such as Zara, Dell, Cisco and Li & Fung are certainly demonstrating apparently different success models when it come to responding to customers in a fast-moving environment, where life
cycles are short and variety reigns. The winners in this environment are those that can respond quickly and efficiently. This renewed competitive
Please click the advert
arena calls for more nimble businesses and more agile supply chains.
THE BEST MASTER
IN THE NETHERLANDS
Download free eBooks at bookboon.com
70
Fundamentals of Supply Chain Management
Agile Supply Management
Apparently, the focus in an agile supply chain is on being fast and also on being smart in how you aligning with the increasingly demanding customers. But the tenet is still that supply chains are driven by the end-consumers in the dynamic market places. The need for supply chain agility ultimately comes from the consumer. However, the customer behaviours could be driven by uncertainties caused possibly by the world oil prices, terrorism-related demand change or by the impact new technological advancement. The unpredictability is not so much the result of one customer ad hoc behaviour; it is combined effect of an uncertain world rippling up and down the supply chain. Often the longer the supply chain the more complexity and increased risk of bullwhip effect. In industries such as fashion and consumer technology, the plethora of products seem to increase exponentially while in the same time the product life cycles in the market are getting shorter. It will come as no surprise that the dominant buying behaviour of customers in an agile supply chain operated environment is that of demanding quick response. The known business models of make-to-order or assemble-to-order are critical for catering such demand. Hewlett-Packard has long adopted the
practice of postponing the final assembly of its printers until the exact market demand in terms of product configurations are known. Thus what it produced are almost guaranteed to be sold and not over production or redundant finished goods inventories are created. Similarly, Dell Computer is a master at assemble to order, and often the assembly were carried out during the distribution and delivery process, so that the customer can have their bespoke computer delivered in just a few days. And for Dell, the generic components in the up part of the supply chain were produced by the make-to-forecast model where efficiency and low cost can be achieved; the assemble-to-order at the final sector of the supply chain delivers the speed and responsiveness.
5.2 Agile Supply Chain Concept
Agility is a supply chain-wide capability that embraces organisational structures, value chain configurations, information systems, logistics processes and in particular mindset and culture. A key characteristic of an agile supply chain is flexibility, which should be interpreted from two side of supply chain. From the inside of supply chain, such flexibility means configurations and structures are not fixed. They may transform quickly as the needs arises. From outside, i.e. from market and consumer perspective, the supply chain must deliver timely products and services; and deliver them at the beginning of the usually short profit widows; often to be innovative and to be the market leader. Thus âagile supply chainâ is essentially a practical approach to managing supply networks and developing flexible capabilities to satisfy the fast changing customer demand. It is about moving and transforming a supply chain that is structured around the focal company and its product categories to the one that is centred on end-consumers and their requirement. As the Chairman of Li and Fung Group â the largest export trader in Hong Kong, says that one of the key features of his approach is to organise for customer, not on country units that may end up competing against each other. The capabilities of an agile supply chain is created and measured from the âoutside inâ as opposed to pushing product offerings into the market â the âinside outâ. The strategic focus of an agile supply chain is a relentless pursuit of customer value in every part of its fabric. The operational planning of agile supply chain is focused on
the capabilities for responsiveness and constantly in anticipation of unpredictable sudden changes in demand. Such capability building and customer attention cannot be achieved without a cost. Typically, in order to ensure availability, extra production and service capacity need to be reserved; this will incur additional cost of over capacity. However, when the strategic positioning of the supply chain is rightly set, the gains from the agility are worth the effort and cost. This actually raised an important question. In which business circumstances that the agile supply chain is worthwhile?
Download free eBooks at bookboon.com
71
Fundamentals of Supply Chain Management
Agile Supply Management
To answer this question, we may do some comparative observations between lean and agile by looking at some most common variables in supply chain management. First, we can make observation on the volume and variety of the product that supply chain produces. As shown in Figure 25, lean works best for high volume, low variety and more predictable operating environment; whilst agility is needed in less predictable environment where the demand for variety and choice is a dominant feature.
Figure 25, Volume and variety observation.
We can also make observation from some specific characteristics of demand and supply. As shown in Figure 26 the supply characteristics in lead-time can be long or short; whilst the predictability of market demand can be categorised into either predictable or unpredictable. It then become intuitive that in the case of long supply lead-time with predictable customer demand, the plan and execution style of lean model works the best; while in the case of short supply lead-time with unpredictable demand, the Agile responsiveness works
the best.
Download free eBooks at bookboon.com
72
Fundamentals of Supply Chain Management
Agile Supply Management
Figure 26. Demand characteristics observation
More comprehensively, Mason-Jones et al. (1999) developed a comparative analysis between lean and agile by observing a whole host of supply chain attributes as shown in Table 1. This list clearly mapped out two distinctively different attributive profiles for both lean and agile supply chain to home in.
Table 1. Comparison of lean supply with agile supply
Distinguishing Attributes
Lean Supply
Agile Supply
Typical products
Commodities
Fashion goods
Market place demand
Predictable
Volatile
Product variety
Low
High
Product life cycle
Long
Short
Customer drivers
Cost
Availability
Profit margin
Low
High
Dominant cost
Physical cost
Marketability cost
Stock-out penalties
Long-term contractual
Immediate and volatile
Purchasing policy
Buy materials
Assign capacity
Information enrichment
Highly desirable
Obligatory
Forecasting mechanism
Algorithmic
consultative
Download free eBooks at bookboon.com
73
Fundamentals of Supply Chain Management
Agile Supply Management
5.3 Agile Supply Chain Framework
The comparison of lean and agile, have certainly helped to make some intuitive sense about the concept of the agile supply chain. But it would be more useful if some theoretical underpinning of the agile supply chain model can be provided. Professor Alan Harrison of Cranfield University proposed a
framework (Harrison, 1999) for agile supply chain, which was perhaps the earliest theoretical attempt to the framework. The four key components of the framework can be interpreted as follows.
Figure 27. Agile supply chain framework (adopted from Harrison 2005)
Agile supply chain is about virtual integration
Agility implies that the supply chain is able to respond to the changes in the local market requirements and much of these can perhaps be the opportunities. To do this, agile supply chain must be able to leverage skills, assets and other resources across the divisional units in the local region in which they operate. This means they need to establish the shared goals and communicate them across the supply chain and work toward them jointly in harmony. The bound between organisations created by the shared goals does not necessarily vertical where the ownership consolidates. In fact, typically, it creates the virtual integration â the vertical integration without being so. Virtual integration is characterised by informal and flexible and dynamic relationships between the divisional units and different sectors of the supply chain. The governance of such integration explicitly does not get involved with initiatives that are specific to an individual business. It does not centrally control the supply chain operations, but rather it supports and facilitates larger or overall supply chain initiatives from which many parts of the supply chain can and should benefit. The virtual integration also provides senior management with a method for supporting and steering direction on most important direction. As the structure and processes have been kept minimum in the virtual integration, and individual unit involvement remains fully empowered, the supply chain becomes more agile and responsive.
Download free eBooks at bookboon.com
74
Fundamentals of Supply Chain Management
Agile Supply Management
Agile supply chain relies on market sensitivity
Market sensitivity means that the supply chainâs internal measures, whatever it may be, are sourced directly from and linked closely with the external market that the supply chain is operated in. All too often, we see performance measures and business assessment are based on the data, information from with the internal operation and mostly generated within the supply chain. This will most probably misguide the management and drive the supply chain away from its ultimate objective of serving the market.
What a truly agile supply chain do in terms of performance measure and operational improvement is to set up a very high level of market sensitivity. Such market sensitivity has two implications. First is to the internal performance measure. Every measure must be immediately or ultimately linked to the consumers in the market place. This means linking internal customers and external customers all to the ultimate end-consumers. To do this, a causal map from what really customer care about to every operation the business delivers must be meticulously drawn out. Second, is to quick responsiveness. How quick can a supply chain respond to the market change is a primary measure for the agility of the supply chain. Its attainment is largely dependent on how closely the supply chain is able to sense the sudden changes of the market behaviour. Zara is able to have the market sensitivity because they created process of online market feedback from their stores through PDF units. Dell is able to have their market sensitivity by creating a web-based distribution and service
Please click the advert
channel.
With us you can
shape the future.
Every single day.
For more information go to:
www.eon-career.com
Your energy shapes the future.
Download free eBooks at bookboon.com
75
Fundamentals of Supply Chain Management
Agile Supply Management
Agile supply chain needs improved process integration
Agile supply chain will require higher level of integration between internal operational processes, such as sales, forecasting, production planning, sourcing, and delivery. The logic behind is straight forward. When sales operation sensed any change of market trends it will trigger a chain reaction of responsive or corrective changes through many other operations in the supply chain. How fast the supply chain can react to the market change is dependent on the speed of changes in many other internal processes. Thus, it makes sense that the internal processes must be integrated and perform as if they a one entity. There are number of things that the supply chain managers can do to make difference. First, forecast by market not by business units. The forecast generated by business units often show huge variance and inconsistency. What an agile supply chain can do is to create a so-called market lead team which will be responsible to all the forecasting required by the supply chain and the business units wherein. Second, set out to create a capability of coordinating the three prime sectors source-make-deliver. It is all too easy to assume the ERM system will look after everything. The matter of fact is that they donât. Third, managers must link forecasting to improvement goals. This is so because the forecasting is a process that can take the market sentiment and give indications as which directions the market is moving to. Business improvement will only make sense when it responses to the changing directions of the market. Agile supply chain is often dynamic network based
Looking at the agile supply chainâs architecture, managers need to clarify how the participating members of the agile supply chains are best connected with each other. As discussed in Chapter 3 the supply chain configuration can be divided broadly into two types of networks: stable network and dynamic network. The stable network is a normal form of supply chain configuration where the suppliers and buyers are formed in tiers along the supply chain. The suppliersâ involvement in the supply chain is more or less fixed. The operational guidelines are formalised with the OEM. The technical role and competence positioning in the supply chain is also predefined. The style of operation of this type of network is mainly mechanical in nature that is displayed in its physical functions. However, the dynamic network is preferred by the agile supply chain and it has a set of very different characterises. In the dynamic network, the ties between suppliers and buyers, and amongst the suppliers themselves, are much looser than that of stable network. Short term contract or virtual relations are more often the case. Some even strategically important functions such as product design and marketing can be undertaken by independent organisations at a short term basis. Market forces rather than formalised structure are the means by which the parties are bonded together. The network relies on more sophisticated information systems with high level of information disclosure between the parties, whereby instant switch of connection can be easily established if required by the sudden change of market. For those reasons, the dynamic network is undoubtedly a more superior form of networking for agile operations.
Download free eBooks at bookboon.com
76
Fundamentals of Supply Chain Management
Agile Supply Management
5.4 Competing on Responsiveness
Ultimately, the validity of the agile model is to be tested, not by a formula, but by the competition in the market place. The market place to test agile supply chain is presumed to be volatile and fast changing in nature. The top measure for the fitness of a supply chain is responsiveness. Typically high responsiveness cannot be achieved for minimal cost. Customers and suppliers have to make a choice. The trade-off can be tough at times. For any agile supply chain there is always an incremental cost associated with servicing the changing demand. For those genuinely need urgent service will pay a premium. If the customerâs demand is not urgent, they perhaps can wait or chose alternative cheaper version which is often offered by lean supply chains.
The unique value proposition of agile supply chains is that they can respond rapidly and with high priority in unpredictable supply and demand conditions. To do this sometimes means holding spare or redundant capacity to cope with the sudden surges in the pipeline. That is part of the cost the agile supply chain has to pay. Zara has two very large distribution centres at La Coruna and Zaragoza in Spain which sometimes may only be 50% utilised. This is not an oversight on the capacity management, but a deliberated strategy. Zara management know the cost of redundancy, but they also know the benefit and indeed the necessity of having transient capacity available to support their rapid fire replenishment business model. The levels of responsiveness a supply chain can deliver do make significant difference in terms of winning the market share. In the immediate aftermath of Hurricane Katrina, which swept through the US state of Louisiana in September 2005, one of the most affected companies was a major oil company, which lost all of its computing equipment in its service centres. The company contacted Hewlett Packard, its regular hardware supplier, with a priority request to replace 1,000 specially configured PCs as quickly as possible. HP got back a few days later with a commitment to deliver the replacements by Christmas. This was not the answer that the company wanted to hear, so it called Dell which had not previously been a preferred supplier and asked the same question. Back came the answer almost immediately: âIs Monday Okey?â Dell got the business won a new major customer.
It is quite telling that the supply chain that can respond quickly wins. How to create the structured supply chain responsiveness? The most commonly used strategy is called postponement, or delayed configuration. Postponement is not just an operational trick, it requires the supply chain to configure in a particular way which may or may not be so obvious at the first sight. To illustrate the concept of postponement, we must first understand the concept of âorder decoupling pointâ in supply chain.
Download free eBooks at bookboon.com
77
Fundamentals of Supply Chain Management
Agile Supply Management
As shown in figure 28 the order decoupling point determines how far the customer orders will enter into the supply chain. It is the point (marked by the inverted triangle in the figure) beyond which the customer specific order is no longer visible to the supply chain. Different supply chains have different design for where the order decoupling point sits. For a supply chain that is mainly ship-to-stock, the decoupling point tends to be very much at the downstream end of the supply chain; while for the supply chain that is mainly make-to-order, the decoupling point is usually at the manufacturing stage in the middle part of supply chain. It is therefore clear that on the downstream side of the decoupling point the supply chain operating model is customer âpullâ â responding to demand changes. On the upstream side of the decoupling point the supply chain is operating in a âpushâ mode, where one the generic components are produced based on amalgamated forecast and schedule.
Figure 28. Supply chain order de-coupling point
The postponement strategy is aiming to achieve market responsiveness in terms of producing the right variety and right product portfolio at the right
quantity, but do it efficiently at a mass production price. To achieve this, the order decoupling point is postponed to a later, or as later as possible, stage close to product delivery. The resultant supply chain will have most part its operation under scheduled generic components manufacturing, which is based on the aggregated demand and in a volume production mode leading to low cost and high efficiency. Reflecting what we have leant about the lean supply, understandably this part of supply chain (before the decoupling point) is predominantly lean. Then at the end of this lean section, there will be a stockpile of the inventory of those generic components called strategic inventory.
Download free eBooks at bookboon.com
78
Fundamentals of Supply Chain Management
Agile Supply Management
Figure 29. Postponement strategy (source: Christopher, 2005)
After the strategic inventory, the orders from customers are visible to the supply chain, and the supply chain operation is focused on configuring (assembling to order) the products to satisfy the demand. Because it is driven by the demand, this part of the supply chain is primarily agile.
Please click the advert
Do your employees receive
the right training?
Bookboon offers an eLibrairy with a wide range of
Soft Skill training & Microsoft Office books to keep
your staff up to date at all times.
Contact us to hear more
[email protected]
Download free eBooks at bookboon.com
79
Fundamentals of Supply Chain Management
Agile Supply Management
The critical design point of postponement strategy is based on the understanding of the market. When operated in an uncertain and volatile market environment the actual customer demand on the variety of products is largely uncertain, unpredictable or volatile. The supply chain could make all the possible variety of products in sufficient volume to stock in order to satisfy the unknown demand, but the redundant products cost will be too high and supply chain marketability would be too poor. Instead, the supply chain could reconfigure the material flows and make a more predicable volume of generic components ready at the strategic inventory point, but postpone the product configurations to the very last stage when the demand is a lot clearer and the specific volumes of each variety become more predictable. In this way, not only the specific customer demand can be fulfilled very quickly because all the generic components are ready and only need to be assembled to the required configurations, also there will be no redundant finished products because the volume is produced in such a short span before delivery that it is matched to the exact demand.
5.5 Getting It Right from Within.
To develop the agile capability for your supply chain, you must start from within. There number of things the organisations in the supply chain need to get it right before they can become competitive in the agility dominated operating environment. This may include organisational structure change, process reengineering, cultivating appropriate culture, developing KPI, and investing in IT system. The top level executives commitment and direct involvement is the transformation is critical. It may also down to the right
style of leadership.
Structure Change
As mentioned earlier, agile supply chain differs from the lean one from its structure to say the least. The structure change required for developing an agile supply chain applies to two aspects. One is the supply chain architecture; another is the organisational internal structure. It has to be said here that we assume business and supply chain strategies have been and will be developed appropriately to support the structure decision making. For the supply chain structure, it all about the organisations external connections and how the whole supply chain is networked together. The first consideration is the extent of vertical integration. For an agile supply chain, the broad guidance is to have small or narrow span of vertical integration. This will give the supply chain a great deal of flexibility without feeling bogged down by the fixed assets. The second aspect to consider might be the outsourcing alternatives. To have a network of capable suppliers that can take outsourcing contracts from you, will materially improve the agility of the supply chain. The other one to consider is the location of the suppliers. Long distance and poor infrastructure will certain impede the supply chainâs fast reaction and thus need to be pruned in the network. From the organisational internal structure point of view, agile supply chain also demands some structure changes. Some historically centralised operation may need to be decentralised to cut the bureaucracy and respond to local conditions. Multi-divisional structure may be advisable to concentrate on the product, service, and geographical area and allowing units to adapt to local needs. Agile operations would also prefer more flat structures not tall hierarchies. High degree of empowerment and less formal rules are also positive factors to the agile structure.
Download free eBooks at bookboon.com
80
Fundamentals of Supply Chain Management
Agile Supply Management
Process Change
In the agile supply chain, processes are still necessary, but they are fewer by definition. Any process slows down the response time should be considered for reengineering. It is likely that some process short-cuts are necessary for the agile operation and the level of operational risks may rise. But the top priority is still the responsiveness, so long as the safety is not compromised. Ways may be found to by-pass the regulations and opportunistic flair could play a role in achieving unanticipated profit. However, this does not mean to create any expansive purchasing or costly deliveries. Quite the contrary, the process that drive and support agile supply chain are often the unique combinations of standard or modular process which is the key to containing the cost while delivering the service to unexpected demand. The postponement process discussed in the previous section is a widely applied process to achieve higher agility. It is also important that the business processes are aligned through the supply chain. Thus a coordinated process development for agile response is essential.
IT Systems
Agile supply chains are best underpinned by an ERP system similar to those used in other supply chain types. An array of additional applications designed to optimise the agile capabilities including process alignment and joint forecasting and planning. Zaraâs achievement of remarkable responsiveness was due no small measure of its IT systems. The centralised design teams for manâs ware, womanâs ware and childrenâs ware are hardwired with the retail stores around the world. Using on-line market information the teams will be able to change or creating new designs quickly ahead of the competition. Anecdotally, if as few as three people have come to the store and asked something that Zara donât have. Zaraâs design team will take it on and design it for them.
Nevertheless, investing in applications does not necessarily mean investing in large lump of capital equipment. In fact, investing in hardware may even hinder the agility development. Hardware is generally rigid and
non-transferable between markets, once invested it will only depreciate, and it depreciates much faster when new updated equipment are coming onto the market. Renting or buying the service without taking the ownership of the hardware appears to be a better choice for agile supply chains.
Download free eBooks at bookboon.com
81
Fundamentals of Supply Chain Management
Agile Supply Management
Key Performance Indicators
Agile supply chain will also need a set of its own unique key performance indicators (KPI). The commonly used KPI in predominantly lean supply chain operating environment will not fit and often misguide the management. On top of the most frequently used KPI for agile supply chains are:
⢠Design to market time
⢠Customer satisfaction and delight
⢠Production throughput
⢠Delivery lead-time
⢠Product availability in the market
⢠Capacity synchronisation and optimisation
⢠Cost-to-serve
⢠Frequency of product up-grading
⢠Service innovation and flexibility
Fundamentally the KPI for agile supply chain is the market responsiveness in terms of speed product range and service quality. But the detailed KPI for a specific organisation, however, must be aligned with its top level business strategies
Please click the advert
and related with the industry sector and product categories.
www.job.oticon.dk
Download free eBooks at bookboon.com
82
Fundamentals of Supply Chain Management
Purchasing and Supplier Selection
6 Purchasing and Supplier Selection
6.1 Strategic Role of Purchasing
Purchasing function has a strategically indispensible role to play in supply chain management. It covers the sourcing end of supply chain management interfacing with the delivery end of the suppliers. ⢠The classical definition of purchasing is: to obtain materials and/or services of the right quality in the right quantity from the right source, deliver them to the right place at the right price. ⢠The composite definition of purchasing is: the process undertaken by the organisational unit which, either as a function or as part of an integrated supply chain, is responsible for procuring supplies of materials and services of the right quality, quantity, time and price, and the management of the suppliers, thereby contributing to the competitive advantages of the achievement of the corporate strategy. Purchasing management thus, by definition, supports and implements the supply chain management strategies. It is one of, or maybe the most important, delivery arms of supply chain management. Often it directly delivers the cost saving, quality improvement and fulfils the supplier relationships. Purchasing functionâs critical role can also be illustrated from a simplified income statement:
Total sales
=
ÂŁ10,000,000
Purchased Service / materials
=
ÂŁ7,000,000
Salaries
=
ÂŁ2,000,000
Overheads
=
ÂŁ500,000
Profit
=
ÂŁ500,000
Suppose this is a companyâs profit-loss account for the current year, and the shareholders demand the CEO to deliver double the profit in the next year. What can the CEO do with regards to those factors associated with the account? Well, assume everything else remains equal, doubling the total sales will eventually double the profit. It is equivalent to create two companies. But the problem with this approach is that the sales volume is often constrained by the market. If the product cycle has passed the maturity and started to decline, to maintain the amount of sale would be
difficult let alone to double it. Or, the company could reduce the salary by 25%, which could make ÂŁ500,000 saving for the bottom line. Common sense tells that it is not feasible, and the CEO would not agree as his 25% cut would be biggest of all. Another alternative is to get rid of all the overheads costs, which also makes ÂŁ500,000 saving. However, this is almost impossible to do practically, nor agreeable theoretically.
Download free eBooks at bookboon.com
83
Fundamentals of Supply Chain Management
Purchasing and Supplier Selection
Whatâs left is to curtail the buyer-in goods and service by 7% which will make $500,000 savings for the bottom line. Now, just 7% cut in purchasing would result in 100% increase of profit. This is no doubt a very effective approach as the effort appears to be small and the gain is amazingly high. It is apparently the only viable and convincing choice there is to it. Who is going to do that for the company? It is the purchasing function. This is why purchasing function is distinctly so important to the companyâs profit level. It is the companyâs profit leveraging point, whereby a small input can generate large output. No wonder we see many OEMs often try to enforce the supplied material cost reduction by 4-5% year on year, albeit, this may not be the best approach from the contemporary supply chain best-practice perspective. The operational processes of purchasing function can be represented by the diagram shown in Figure x. It basically intermediates the companyâs internal operations with the suppliers, ensuring the right suppliers are found and engaged in a process of supply and delivering the required materials, components and services that best suit the internal operations.
Figure 30. Operational purchasing activities (adopted from Slack, 1998)
These are just the visible parts of purchasing function. Beyond these processes, there might more important high level strategic decisions to be made for the purchasing, through the purchasing and by the purchasing. Typically, make-or-buy decisions, supply base rationalisation, supplier development and etc..
Download free eBooks at bookboon.com
84
Fundamentals of Supply Chain Management
Purchasing and Supplier Selection
6.2 Purchasing Portfolio
âWhat is the best way to managing purchasing?â âWhat is the best strategy for purchasing and supply?â Many practitioners and academics have asking these questions in past and still today. In fact, there were no shortages of answers to these questions in the plethora of literatures even in the early years. But few stood the test of time for its applicability and universality. Then there came Dr.Peter Kraljic from McKinsey who claimed that there is no single best way existed for managing purchasing in all circumstances. He then published a paper entitled âPurchasing Must Become Supply Managementâ in Harvard Business Review in September 1983, and proposed the very well known Kraljic Purchasing Portfolio model (see figure x). This model had since then been widely cited and referenced across the world in all types of management literatures. There are now many modified versions by many scholars which have contributed and further developed the application of this model.
Please click the advert
Is your recruitment website
still missing a piece?
Bookboon can optimize your current traffic. By
offering our free eBooks in your look and feel, we
build a qualitative database of potential candidates.
Contact us to hear more
[email protected]
Download free eBooks at bookboon.com
85
Fundamentals of Supply Chain Management
Purchasing and Supplier Selection
Figure 31. Kraljic purchasing portfolio matrix
Dr. Kraljicâs answer to the question can be paraphrased as that although there is no single best way, but if we know which product category we are purchasing, there would be a best way to do the purchasing for this product category. He looked in two dimensions to categorise all the purchased products. One is the supply risk of the product from the market; two is the financial impact of the purchased material. Thus a four categories matrix emerged presenting four different types of purchased product.
Leverage products
Leverage products are those you buy from your supplier that will have significant impact on the finance of your own final product, but it is relatively easy to buy from the supply market, hence low market risk. For example, wood is a leveraged product for a wood furniture manufacture to purchase. This is because that most of the furniture they do are made of wood. A large portion of the cost come from wood price and the furniture prices are dependent on the wood cost in the market place. However, unless it is rare wood which they hardly use, the supply of wood is plentiful and there is very low risk of short supply.
For such leverage products, Kraljic proposes a purchasing strategy of competitive bidding. Understandably, competitive bidding will only work if there is more than one supplier. The low supply risk factor of leverage products supports this strategy. Alternative suppliers are in this case available and substitution of supplier is possible. The buyer can then benefit on the lower price and cost advantages. It is important to understand that the buyer need to do so, because the high financial impact the leveraged products.
Download free eBooks at bookboon.com
86
Fundamentals of Supply Chain Management
Purchasing and Supplier Selection
Routine Products
Routine products are those materials that have very little financial impact on the buyerâs own products and also there are plenty to choose from in the market place. Examples of these products or materials are small fixtures, pant, and standard components like springs and nuts. They donât cost much in comparison to the total cost of your own products. The market availability for those materials is very high and there is no risk of supply. For the routine products, Kraljic proposed a purchasing strategy of system contracting plus e-commerce solutions, because these products have large varieties and high logistics complexity and often labour intensive in handling. The sophisticated computer based system ordering suits well with the nature of the products. Although the alternative sources of supply are available, bidding is not recommended. This is because the low cost nature of the materials made the bidding unnecessary; and the variety complexity of the materials will make the bidding unaffordable. Strategic Products
Strategic products are those components have high level of financial impact to your final product. They are very expansive to develop and manufacture,
and often involve high technology contents. They are not usually available in the market place, thus high supply risk. The buyer will need to contract for the manufacturing rather than pay for the delivery. The examples of these products are engines for automobile and compressor for the refrigerator. For the strategic products, Kraljic proposed a purchasing strategy of performance based partnership. That is to create a partnership relation with the supplier and work together to develop and manufacture the components. The proposal is obviously for good reasons. This type of components usually is not make to stock it at lease needs to be ordered to the specific requirement, often the components will have to be designed and developed together with the supplier. Hence, strictly speaking, it is no longer the purchasing of products, but rather purchasing of the developing and manufacturing capabilities from the suppliers. Thatâs why âperformance basedâ is necessary, because it is about the capability. Bottleneck products
Bottleneck products are those components that may or may not cost too much in comparison with the total material cost, but they must have them and they are very difficult to get hold of. The supply risk for those components is high, and the availability of the components is not guaranteed. For example, the small amount of precious metal required for the exhaust purification system is a typical bottleneck material. Without it, the automobile will not pass the environmental standard and will not be allowed on the road. There are only very few supply in the world that have the blessing of the natural resource for those precious metal. Demand is much higher than supply. For such bottleneck products, Kraljic recommended a purchasing strategy of securing supply plus searching for alternatives. You must secure your current supply because you have no choice, you must have it; you need to search for alternatives because the constant risk of cut-throat. The alternatives include radical new designs which may use different materials that are not short of supply. This is the relationship setting that the supplier has the up-hand; buyers will have to take some diversions.
Download free eBooks at bookboon.com
87
Fundamentals of Supply Chain Management
Purchasing and Supplier Selection
6.3 Supplier Selection
One of the mission critical tasks of purchasing function is to identify and select the suppliers. This is particularly true when we talk about of strategic components and bottleneck components. In both of these categories, suppliers are by no means ascertained. The quality of the suppliers and the righteousness of their selection will have direct implications on the supply chainâs long-term competitiveness. The processes of going about selecting suppliers can be suggested as follows, but by no means comprehensive and universal. The processes to go about selecting the suppliers are as follows. ⢠Set up Selection criteria
⢠Initial contact
⢠Formal evaluation
⢠Price quotation
⢠Financial data
⢠Reference checking
⢠Supplier visit
⢠Audits, assessments or surveys
⢠Initiation test
Turning a challenge into a learning curve.
Just another day at the office for a high performer.
Please click the advert
Accenture Boot Camp â your toughest test yet
Choose Accenture for a career where the variety of opportunities and challenges allows you to make a difference every day. A place where you can develop your potential and grow professionally, working alongside talented colleagues. The only place where you can learn from our unrivalled
experience, while helping our global clients achieve high performance. If this is your idea of a typical working day, then Accenture is the place to be.
It all starts at Boot Camp. Itâs 48 hours
that will stimulate your mind and
enhance your career prospects. Youâll
spend time with other students, top
Accenture Consultants and special
guests. An inspirational two days
packed with intellectual challenges
and activities designed to let you
discover what it really means to be a
high performer in business. We canât
tell you everything about Boot Camp,
but expect a fast-paced, exhilarating
and intense learning experience.
It could be your toughest test yet,
which is exactly what will make it
your biggest opportunity.
Find out more and apply online.
Visit accenture.com/bootcamp
Download free eBooks at bookboon.com
88
Fundamentals of Supply Chain Management
Purchasing and Supplier Selection
Apparently, these processes are mainly around setting and taking measures
against the criteria. However, there are three significantly different approaches toward supplier selection. The first is based on the product that the supplier can deliver. This approach will normally check the product prototype to see if the quality and technical specifications can be met and the delivery terms are satisfactory. The second is based on the capability that the supplier displays. It typical checks whether the supplier has the design and development capability, strategic investment in technology and skills, and up to scratch management. This capability approach is often used for long-term supplier selection and can be done well before the idea of component is taking shape. The third is the combination of product and capability selection. It applies to when a strategically important new part is to be outsourced to a new supplier. Not only the supplier must comply with all the product specific requirements but also should have the capability of making future generation of the products in the long run, so as to sustain the supply chain development. Some frequently used criteria for capability filtering are as follows. Assessment criteria on the supplierâs capability:
⢠Total quality management policy
⢠BS 5750/ ISO 9000 certification or equivalent
⢠Implementing latest techniques e.g. JIT, EDI
⢠In-house design capability
⢠Ability to supply locally or world-wide as appropriate
⢠Consistent delivery performance, service standards and product quality ⢠Attitude on total acquisition cost
⢠Willingness to change, flexible attitude of management and workforce ⢠Favourable long term investment plan
6.4 Tools for Supplier Selection
To facilitate the process of supplier selection, quantitative tools are beneficial. They can make the selection process more rationale; they serve as the platform for meaningful discussion or debate; they provide traceable documents; they form the factual contents for decision-making. Three basic quantitative tools are introduced here for managers to get started on creating their own tools for their own industry and products. The first one
is called the âcategorical methodâ as shown in figure 32. You define the selection criteria first, for example quality, delivery and service; then you make three category judgements: good (+), unsatisfactory (-), and neutral (0) against the criteria for each supplier; finally you sum up the judgement into a total score for each supplier; the highest one will be selected. This method is very simple to apply but is rather subjective. Hence, it is recommended to form a multi-functional team to make collective judgements in order to limit the bias from individuals.
Download free eBooks at bookboon.com
89
Fundamentals of Supply Chain Management
Purchasing and Supplier Selection
Performance Characteristics
Supplier
Quality
Delivery
Service
Total
A
Good (+)
Unsatisfactory (-)
Neutral (0)
0
B
Neutral (0)
Good (+)
Good (+)
++
C
Neutral (0)
Unsatisfactory (-)
Neutral (0)
–
Figure 32. Categorical method
The second method is called the âcost ratio methodâ as shown in figure 33. Similarly you set up the required criteria against the alternative suppliers. Whatâs different from the categorical method is that it is not entirely based on the peopleâs subjective judgement. It makes use of some available data on the quality performance; service standard and delivery reliability for instance. With those historically collected data, you will be able to establish the corresponding cost ratios for each criterion in term of how much the penalty cost needs to be added. The original quoted unit prices from different suppliers will then be adjusted to generate the net-adjusted costs. It then becomes clear that if the supplier selection is based on the original quoted unit price, then the supplier C should be
selected because its cost is the lowest. However, if the supplier selection process takes into account of the suppliers historical performances in the three areas and use the net-adjusted cost, the lowest cost supplier is A not C. The little homework of considering the cost ratio has made very different choice in the selection.
Quality
Supplier
Cost
Ratio (%)
Delivery
Cost
Ratio (%)
Service
Cost
Ratio (%)
Total
Penalty
Ratio (%)
Quoted
Price/
Unit (ÂŁ)
Net
Adjuste
d Cost
(ÂŁ)
A
2
2
1
5
16.00
16.80
B
5
4
2
11
15.40
17.01
C
7
3
5
15
15.00
17.25
Figure 33. Cost ratio method
Download free eBooks at bookboon.com
90
Fundamentals of Supply Chain Management
Purchasing and Supplier Selection
The problem with the two methods is that all the criteria are treated equally in the selection process. This is not really true in real-world business. People have preferences toward different criteria for various reasons. In some circumstances, quality is more important than delivery, and in other situations the delivery is more than quality. The third method takes care of these preferences by assigning a weight to each criterion. It is called the âlinear-average methodâ as shown in figure 34. The weight is a score that reflects the relative importance of the criterion. The sum of all the weight scores is normally 100. Whatever the judgement score multiplied by the weight become the adjusted judgement score; and then add all the adjusted scores together to generate the total selection score for the supplier. It should be noted that the weight can also be applied to the cost ratio method, or any other method. In the end, the most appropriate supplier selection tool perhaps is the combination of some of those methods.
Selection
Weight
Criteria
Supplier A
Supplier B
Supplier C
Score
Total
Score
Total
Score
Total
Quality
52
8
416
5
260
6
312
Delivery
26
3
78
8
208
3
78
Service
22
5
110
8
176
5
110
Total
604
500
644
Figure 34. Linear -Averaging Method
6.5 Towards Knowledge Based Sourcing
Purchasing practice and theory never stops developing. It really is a dynamic and evolving subject in both theory and practice. Looking back at the recent three decades of purchasing development, an evolution pattern starts emerge. Depend how one would like to take out of it; the pattern may be presented in different ways. Here we frame the evolution pattern into two perspectives, each of which has four key stages. The first perspective is on the operational focuses and the second perspective is mainly on the characteristics changes.
The operational focus perspective classifies the purchasing function into four stages: ⢠Stage one can be called âProduct centred purchasingâ. The operation is basically concentrated exclusively upon the purchasing of the tangible products and its outcomes on the overall businesses. It is usually measured in the five rights (right price, right time, right quantity, right quality and from the right sources).
Download free eBooks at bookboon.com
91
Fundamentals of Supply Chain Management
Purchasing and Supplier Selection
⢠Stage two can be called âProcess centred purchasingâ. It is predominantly process focused operation. It moves beyond the direct outcomes of the purchasing activities and into the processes through which the outcomes are delivered. This means that the managers realised that the processes are the enablers, and often the controllers of the purchasing outcomes.
⢠Stage three can be called âRelational purchasingâ. The focus of the operation is not just on the process but also on the inter-organisational relationships. The relationship has been taken on as the key management instrument to enhance the product quality and technological advances; it also had massive positive impact on the supplier integration and development.
⢠Stage four can be called âPerformance centred purchasingâ. It focuses on the optimum business performances as a whole and managing the purchasing functionâs contributions to the overall business performances. In this way, the purchasing function has been strategically connected to the businessâs ultimate objectives and delivery. It is a system approach.
The characteristics focus perspective classifies the purchasing function into four stages: ⢠Stage one is âpassiveâ in character. In this stage the purchasing can be defined as lack of strategic directions and is mainly reactive to operational requirements. High proportion of purchasing managerâs time is on routine operations with low visibility to the supply chain. The supplier selection is based on price and availability only.
⢠Stage two is âindependentâ in character. In this stage the purchasing may have adopted the latest technology and process, but may have not got the strategy that aligned with the competition. Links between purchasing and technical disciplines may have been established; performance based on cost reduction; top management recognises the importance of professional development and the opportunities in purchasing contributing to profitability.
⢠Stage three is âsupportiveâ in character. Purchasing starts to support firmâs competitive strategy by adopting purchasing techniques and products which strengthen the firmâs competitive position. Suppliers are considered as key competitive resource. The supply market, products evolution and suppliers capabilities are continuously monitored and analysed.
⢠Stage four is âintegrativeâ in character. In this stage purchasing strategy fully integrates with firmâs purchasing function. Multifunctional
teams and cross functional training of purchasing professional begin to take hold. Open and close communication with other functional departments is hard wired into the processes. Purchasing is measured in terms of its contribution to the overall success of the firm. It is interesting to notice that the four stages in both perspectives can be broadly matched with little obvious impediment. However, it will take a more rigorous approach to declare the theoretical match and to create a new stage model for the purchasing development. The discussion presented here merely opens the scope of discussion and hopefully stimulate further thinking and debate.
Download free eBooks at bookboon.com
92
Fundamentals of Supply Chain Management
Purchasing and Supplier Selection
But there is no doubt that the purchasing function has now become a much more sophisticated process and has much wider and deeper impact to the business performance. It is moving away from the short-term towards long-term; from a function to processes; from transactional to relational; from cost saving to performance enhancing. The picture of purchasing in the future perhaps can be described as the knowledge-based purchasing, which is built on the knowledge about whole business objectives and stakeholdersâ interest, the knowledge about the suppliers and their capabilities and potential, the knowledge about the people and their emotion towards relationship and culture; and the knowledge about technology up-taking.
The Wake
Please click the advert
the only emission we want to leave behind
.QYURGGF ‘PIKPGU /GFKWOURGGF ‘PIKPGU 6WTDQEJCTIGTU 2TQRGNNGTU 2TQRWNUKQP 2CEMCIGU 2TKOG5GTX 6JG FGUKIP QH GEQHTKGPFN[ OCTKPG RQYGT CPF RTQRWNUKQP UQNWVKQPU KU ETWEKCN HQT /#0 &KGUGN
6WTDQ
2QYGT EQORGVGPEKGU CTG QHHGTGF YKVJ VJG YQTNFoU NCTIGUV GPIKPG RTQITCOOG s JCXKPI QWVRWVU URCPPKPI HTQO VQ M9 RGT GPIKPG )GV WR HTQPV
(KPF QWV OQTG CV YYYOCPFKGUGNVWTDQEQO
Download free eBooks at bookboon.com
93
Fundamentals of Supply Chain Management
Relationship and Integration
7 Relationship and Integration
7.1 Supply Relationship Defined
Supply relationship can be defined as the cross organisational interaction and exchange between the participating members of the supply chain. This means that the relationship is between organisations not individual people within the same supply chain where the material flows defines the boundary. However for the inter-organisational interaction that falls outside of the main streams of the material flows, then it may not be called collaborative relationship or partnership relation, but may not be the supply relationship. Supply relationship can be either on the upstream side with the suppliers or on the downstream side with the buyers. If the relationship is solely observed between one supply and one buyer, it is also called dyadic relationship.
One of the most common organisational relationships is whatâs called the partnership relation. A partnership is defined as a specific relationship arrangement where parties agree to cooperate to advance their mutual
interests. Since humans are social beings partnerships between individuals, businesses, organisations, and varied combinations thereof, have always been commonplace. In the most frequent instance, a partnership is formed between two or more businesses in which partners cooperated to achieve and share business advancement and profits or losses. In supply chain management, relationship between the participating members is in fact more a dimension rather than an element. This means that supply relationship cannot be understood as something that you either have it or you donât; instead it is a dimension from which various different relationship postures can be identified, such as armâs length relation; shortterm contractual relationship, long-term partnership relation and so on. It is almost like a variable that may take different values under different circumstances. Then the question is how, in practice, one might measure the âvalueâ of relationship? This is a difficult question. Amongst many known attempts, a relatively more convincing one is that if a relationship is a form of interaction and exchange, then a specific relationship can be measured by the contents of the exchange.
Download free eBooks at bookboon.com
94
Fundamentals of Supply Chain Management
Relationship and Integration
Since relationship is ultimately about exchange, and hence, so long as we know what has been exchanged in between we should be able to pigeonhole it to a specific type. For example, if the buyer and supplier have only exchanged on the price and volume of the goods, we can very safely assess that they are having an armâs length relationship; on the other hand if the two companies have been exchange their vision, mission and value, have joint design and product development and coordinated production and so on, one can safely assess that the relationship between them is close and highly engaging.
7.2 Close Partnership
The traditional supplier-buyer relationship has been limited to almost single point contact of purchasing officer on the buyer side and the sales person on the supplier side. The purchasing decision is largely based on the unit price. Information sharing is very limited if not at all in existence. The relationship tends to be antagonistic and adversarial. The close partnership relation with suppliers was first practiced in the Toyota led Japanese automotive industry. It had profound influence on Western assemblers and is now a dominant school of thought in supply relationships. The basic practices of the Japanese close partnership with suppliers involve many aspects of supply chain management. ⢠First they reduced their supplier basis and form tiered supply network structure. As a result, the buyer can then focus much smaller number of 1st-tier suppliers; more time and other resources can be focused on them to develop much closer relationships.
⢠They use long term contract with their suppliers. Not only the long-term contract stabilises the contractual relationship, but also psychologically it is a statement of trust and good-will intention which seldom fail to entice a higher level of commitment.
⢠Single sourcing is preferred to dual sourcing or multiple sourcing, taking advantage of volume consolidation, coupled with greater subcontracting to suppliers. This shift has seen the vertical disintegration of the industry.
⢠They get the suppliers involved earlier in the new product introduction process. Suppliers can then contributing their expertise to design and engineering of the new products, adding substantial value to the supply chain. Some of the suppliersâ designers and engineers may reside in the premises of the assembler, creating much closer relationship.
⢠They move away from price based purchasing towards quality-driven purchasing. Putting tremendous amount of effort in working with the suppliers closely to achieve the âzero-defectâ target as part of their TQM campaign.
⢠They developed the JIT production system, which require close integration of suppliers and buyers production system. Supplierâs capacity is synchronised with the buyerâs; and the production scheduling is coordinated to ensure smooth flow of materials and low or no inventories along the processes.
Download free eBooks at bookboon.com
95
Fundamentals of Supply Chain Management
Relationship and Integration
The current emphasis on the close relational exchange represents a departure from the former transactional focus widely practiced in the Western industries, which is characterised by the short-term gains and limited communications and no collaboration. The close relationship is concerned with long-term partnerships and long-term gains for the whole supply chain. It is a shared destiny relationship with suppliers. It is often developed incrementally between the buyer and supper over time. Research suggests that the concept of trust and commitment are pivotal to the relationshipâs success. Trust is defined as âthe willingness to rely on an exchange partner in whom one has confidence. It is thought to be the binding force in most productive buyer-supplier relationships.
Lamming (1993) proposed a nine factors model to summarise the key success factors of the close partnership between supplier and buyer, which could be helpful as a benchmark for supply relationship development. 1) The nature of competition
⢠Global operation and local presence
⢠Based upon contributions to product technology
⢠Combination of Organic growth, merger and acquisition
⢠Dependent upon alliance/collaboration
2) Basis of sourcing decision
⢠Small supply base
⢠Supplier selection not just on bid price
⢠Single and dual sourcing
⢠Re-sourcing as a last resort
⢠Earlier involvement of established suppliers
3) Role of information exchange
⢠True transparency: cost etc.
⢠Two-ways: discussion of cost and volumes
⢠Technical and commercial information exchange
⢠Kanban system for production deliveries
4) Management of capacity
⢠Synchronised capacity
⢠Flexibility to operate with fluctuations
5) Delivery practice
⢠Just-in-time delivery
⢠Local, distance and international JIT
Download free eBooks at bookboon.com
96
Fundamentals of Supply Chain Management
Relationship and Integration
6) Dealing with price changes
⢠Price reductions based on cost reductions
⢠Joint efforts form a key part of information exchange in lean supply ⢠There is a combination of working pressure and co-operation, coupled with transparency in costing 7) Attitude to quality
⢠Supplier vetting system become redundant
⢠Mutual agreement on quality targets
⢠Continual interaction and Kaizen
⢠Perfect quality as a goal (such as 6Ď, and zero-defects) 8) Role of R&D
⢠Integrated assembler and supplier
⢠Long-term development of components system
9) Level of pressure
⢠Very high for both customer and supplier
⢠Self-imposed
⢠Not culturally specific
Brain power
Please click the advert
By 2020, wind could provide one-tenth of our planetâs
electricity needs. Already today, SKFâs innovative knowhow is crucial to running a large proportion of the worldâs wind turbines.
Up to 25 % of the generating costs relate to maintenance. These can be reduced dramatically thanks to our systems for on-line condition monitoring and automatic
lubrication. We help make it more economical to create
cleaner, cheaper energy out of thin air.
By sharing our experience, expertise, and creativity,
industries can boost performance beyond expectations.
Therefore we need the best employees who can
meet this challenge!
The Power of Knowledge Engineering
Plug into The Power of Knowledge Engineering.
Visit us at www.skf.com/knowledge
Download free eBooks at bookboon.com
97
Fundamentals of Supply Chain Management
Relationship and Integration
7.3 Strategic Alliance
Strategic alliance is defined as an informal or formal arrangement between two or more companies with a common business objective. They are seen as a manifestation of inter-organisational cooperative strategies that entails pooling of skills and resources by the alliance partners in order to achieve one or more goals linked to the strategic objectives of the cooperating firms. They usually will take one of the three structural types: ⢠Horizontal alliance: that is between companies on the same level of different supply chains, which is also referred to as inter-channel alliances.
⢠Vertical alliance: that is between the firms on the different levels of the same supply chain, which also referred to as the intra-channel alliances.
⢠Lateral alliance: that is developed between the client company and logistics service provider firms. Those logistics providers usually will serve many different supply chains and thus they are often seen from any supply chain as the âlateralâ rather than internal.
Companies embarked on the business of strategic alliances do so for many reasons: ⢠Sharing complementary resources
⢠Sharing market risks
⢠Achieve economy of scale and economy of scope
⢠Joint development and collaboration
⢠Create value through synergy as the partners achieve mutually benefit gains that neither would be able to achieve individually
⢠Cost saving and customer value adding
Strategic alliances between businesses usually do not start by the âlove at the first sightâ. They must be contemplated and planned dispassionately, and they call for a continuous process of initiation and development. Statistics show that 70% of newly created strategic alliances decease within one year of operation. This may not be as alarming as it sounds. Alliances, perhaps, are supposed to be so. Strategic alliance is fundamentally informal to start
with and will certainly enjoy a cosy but flexible relationship. It is perfectly alright for the parties to decease the alliance without costing them an arm or leg if the experience is not what was expected.
Download free eBooks at bookboon.com
98
Fundamentals of Supply Chain Management
Relationship and Integration
Figure 35. Continuous processes of alliance development
As illustrated in the diagram, the starting point is the matching of the strategic intent of both parties, which is based on their careful analysis and decisions in respect to the strategic choice and supply chain configuration at a high level. The strategic intention of alliance can only become the reality when the agreed alliance is implemented and put to practice. But the implementation is usually facilitated, affected, or constrained by many factors (the 4 Cs, in the model) including the whether the two parties have compatible goals, cooperative culture, complementary skills and commensurate risks. If all goes well the alliance is expected to produce some positive result through synergy; and they are usually evaluated on the value-adding, efficiency and effectiveness, cost, and shred risks. The evaluated results of the alliance will then be reviewed to see if they have met both partiesâ strategic intentions. That completes the cycle of alliance development model. It is anticipated that continuing success of the alliance will rely on the continuing process of those described steps.
7.4 Relationship Dilemma
Why close partnership is so great? We ask this question because the validity of the close partnership appears to have not been challenged, and most of the times it has been pursued as a best practice almost religiously. Most of supply chain relationship literatures appear to be in the same vein;
practitioner world zealously follow the close partnership as the principal developed from the lean supply chain model. The resultant phenomenon is that we all choose to practice the close partnership without questioning its merit in all circumstances, and that could be dangerous. Here, we are going to investigate the three relationship dilemmas in order to have more thorough understanding of the issue.
Download free eBooks at bookboon.com
99
Fundamentals of Supply Chain Management
Relationship and Integration
Dilemma No.1
Relationship could often run into a dilemma between cooperation of and non-cooperation. The well known prisonerâs dilemma game (figure x)vividly illustrates this phenomenon. Two suspects are arrested by the police. The police have insufficient evidence for a conviction, and, having separated the prisoners, visit each of them to offer the same deal. If one testifies for the prosecution against the other (defects) and the other remains silent (cooperates), the defector goes free and the silent accomplice receives the full one-year sentence. If both remain silent, both prisoners are sentenced to only one month in jail for a minor charge. If each betrays the other, each receives a three-month sentence. Each prisoner must choose to betray the other or to remain silent. Each one is assured that the other would not know about the betrayal before the end of the investigation. How should the prisoners act?
Figure 36. Prisonerâs dilemma
The prisonerâs dilemma is a fundamental problem in game theory that demonstrates why two people might not cooperate even if it is in both their best interests to do so. In this game, as in most game theory, the only
concern of each individual player (prisoner) is maximizing his or her own payoff, without any concern for the other playerâs payoff. The unique equilibrium for this game is that the rational choice leads the two players to both play defect, even though each playerâs individual reward would be greater if they both played cooperatively. This scenario of dilemma does sound very familiar in supplier buyer relationship. The trust may leave the business vulnerable to the onslaught of betrayal; but the betrayal will surely destroy the collaboration, thatâs the dilemma. Dilemma No.2
Relationship-based supply chain collaboration and integration often run into the dilemma between positive gains and negative constraint from the same loyalty and closeness of the relationship. A well-developed, high-involvement supplier buyer relationship is at the heart of a supply chainâs survival and is the basis of its growth and development. This is because the close relationship cultivates a culture of trust, creates synergy in collaboration and ensures operational efficiency.
Download free eBooks at bookboon.com
100
Fundamentals of Supply Chain Management
Relationship and Integration
But the high-involvement relationship also ties the company into its current ways of operating and restricts its capacity to change. The close partnerships are designed to be got rid of very easily. Trusted commitment is for the long-term. Cut short of close relationship unilaterally could be seen as a moral betrayal, and losing face is even harder to accept. Supplier buyer close relationship is, therefore for a company, both a powerful driver for development and the cage that imprisons it. The existing close relationship with the buyer, and the psychological commitment to it, could be a major constraint for the supply chain to engage with better suppliers when opportunities arise. Dilemma No.3
Relationship development will always have the dilemma between the level of commitment or cost on relationship and the level of benefit gained from the close partnership. The commitment and cost is the investment the company has to make in order to get closer with its supplier, which include all the activities and expenditures associated with it; and the benefit is everything and anything that contribute to the stakeholdersâ interests. Shown in figure 37, the benefit-gain (indicated by the blue line) from the supplier buyer relationship increases when the relationship gets closer, this is proven by numerous business cases. However, when the relationship gets too close, the gain of benefits may not continue to rise proportionally (the blue line dips a little at the end).
Nevertheless, the cost including all the invested commitment, time and money increase all the way when the relationship gets closer. The high level of engagement in all sorts of activities incurs costs (as shown by the green line). Combining the benefit curve and cost curve together, i.e. take the costs away from the benefit we arrive at a economics model for relationships. This model shown by the orange line depicted the cost and benefit dilemma in determining the level of engagement or the closeness of supplier and buyer relationship. Three key rules can be derived from the model: ⢠The closer the more cost; are you prepare to pay or commit to the relationship? ⢠Over certain level of closeness the cost will surpass the benefit, and become uneconomical; never over-kill; enthusiasm must be tamed by reason.
⢠There always be an optimum level of closeness in the economic zone, where the effectiveness (benefit over cost) is at its highest.
Download free eBooks at bookboon.com
101
Fundamentals of Supply Chain Management
Relationship and Integration
Please click the advert
Figure 37. Relationship dilemma on cost and benefit
Download free eBooks at bookboon.com
102
Fundamentals of Supply Chain Management
Relationship and Integration
7.5 Supply Chain Integration
Close relationship between the members of the supply chain is an indispensible part of the supply chain integration, and supply chain integration is an indispensible part of business success. I firm needs to develop effective coordination within and beyond its boundaries in order to maximise the potential for converting competitive advantage into profitability. That basically is what supply chain integration is all about. Conceptually, supply chain integration means that the legally independent participating firms coordinate seamlessly together as if they one company in order to achieve the common goal. An integrated supply chain will coordinate the order fulfilment to match actual consumption at the end of the supply chain, and synchronise the suppliersâ production to ensure the timely delivery of the products to the right place at the right time and with the right price. Wal-Mart, for instance, shares point-of-sales data including sales and stocking data with its key suppliers. Tracking daily sales enables the suppliers to differentiate popular from slow-moving items and to respond quickly either to replenish or to discontinue the items in retail stores. Tight coordination between Wal-Mart and its key suppliers dramatically increases product availability and reduces inventory costs. The figure 38 shows a framework of supply chain integration. It looks at the product flow that goes through a typical supply chain, which has the manufacturer as the
focal company in the middle, involving two tiers of suppliers upstream and two tiers of customers downstream. On top of everything else, the information flow through the supply chain is the essential infrastructure for the integration. The contents of the integration are managed through 8 dimensions. ⢠Customer relationship management
⢠Customer service management
⢠Demand management
⢠Order fulfilment
⢠Manufacturing flow management
⢠Supplier relationship management
⢠Product development and commercialisation
⢠Returns management
Download free eBooks at bookboon.com
103
Fundamentals of Supply Chain Management
Relationship and Integration
Figure 38. Supply chain integration framework
Coordination among independent firms, such as raw-material suppliers, manufacturers, distributors, third-party logistics providers and retailers, is the key to attaining the flexibility necessary to enable them to progressively improve supply chain processes in response to rapidly changing market conditions. Poor coordination among the chain members can cause dysfunctional operational performance. Some of the negative consequences of poor coordination include inventory costs, longer delivery times, higher transportation costs, higher levels of loss and damage, and lowered customer service. Since the supply chain members are largely independent, the changes that occur in any of them are likely to affect the performance of the others and the supply chain as a whole. The performance of the supply chain thus is
always the âintegratedâ performance, with or without management influence, i.e. the supply chain is inter-linked one way or the other albeit very complex. However, to improve the overall supply chain performance to a desired level, a coordinated effort must be taken. A coordinated action not only has proven useful, but perhaps is the only effective approach to mitigate demand variability and excess inventories in the process.
If supply chain integration is about the process of planning, executing and controlling the interdependence of activities carried out by different supply chain members or business units in order to create value for the end consumer, then supply chain management is basically managing the supply chain integration. Download free eBooks at bookboon.com
104
Fundamentals of Supply Chain Management
The Future Challenges
8 The Future Challenges
Whatâs the future holds for supply chain management? The future of supply chain management is the future of the business management when there will be no business that is not part of a supply chain. The paradigm of business management will soon be converged to the paradigm of supply chain management. To precisely fortune-tell the future of supply chains is meaningless. But whatâs useful is to identify and explore some challenges that we better prepare ourselves for. Three key challenges have been identified and discussed here.
8.1 Creating Customer Centric Supply Chain
The first challenge that the supply chain managers are facing is to transform the supply chains from supplier-centric to customer-centric. Traditionally, supply chains have been developed from factory outwards so that the companyâs business model may be continued without major change. The management emphasis was on how to ensure the production process could be
most efficiently run and products could be most cost effectively distributed. The marketing is to find the customer that fit to the products rather than to make the products that fit to the market. In todayâs highly competitive global market place, the market favours whichever the supply chain that satisfies them best. The strategic aim of the supply chains must be on the higher levels of customer responsiveness. Thus the agility rather than the cost becomes the key diver. The supply chains must be designed to get the customer on the driving seat. Coordination and operational integration of the supply chain members must be significantly strengthened to counterbalance the increased volatility of market behaviour. It is anticipated that there will be a culture change towards the 21st Century supply chain management. This change, which is already underway, is expected to transform the business model from supplier centric to customer centric. The customer centricity idea represents a renewed paradigm that will have profound implications through every aspect of supply chain management. Research shows that close connectivity to customer will significantly improve supply chain effectiveness and market performance.
Traditionally, this task of customer connection is left to only small part of the supply chain. Dealers and service/repair shops have most information about the consumer, with OEMs and suppliers having the least. However, in futureâs supply chain, more information is shared across the network. With online communities, embedded systems, connected online configuration and ordering the future supply chain will have more information about consumers than ever before. More importantly, it will have better intelligent analytics to synthesize and use the information. Across industries, demand planning with customers in the centre will become a standard process for synchronizing supply and demand. Customer centricity also will play a pivotal role in customer collaboration on product innovation. Already more and more supply chains support customer product configuration and specification, and collaborate extensively with customers on product design. While many models of organizational effectiveness can be used for transforming the organisation, one that has persisted is the McKinsey 7S framework. Developed in the early 1980s by Tom Peters and Robert Waterman, two consultants working at the McKinsey & Company consulting firm, the basic
premise of the model is that there are seven internal aspects of an organization that need to be aligned if it is to be successful. Download free eBooks at bookboon.com
105
Fundamentals of Supply Chain Management
The Future Challenges
Three of those are what they call the âHardâ elements and four are âSoftâ ones. The âhardâ elements are easier to define or identify. The management can directly influence them. These are strategy statements; organization charts and reporting lines; and formal processes and IT systems. The âsoftâ elements, on the other hand, can be more difficult to describe, and are less tangible and more influenced by culture. However, these soft elements are as important as the hard elements if the organization is going to be successful.
360°
thinking
Please click the advert
.
360°
thinking
.
360°
thinking
.
Discover the truth at www.deloitte.ca/careers
Š Deloitte & Touche LLP and affiliated entities.
Discover the truth at www.deloitte.ca/careers
Š Deloitte & Touche LLP and affiliated entities.
Download free eBooks at bookboon.com
Š Deloitte & Touche LLP and affiliated entities.
106
Discover the truth at www.deloitte.ca/careers
Š Deloitte & Touche LLP and affiliated entities.
D
Fundamentals of Supply Chain Management
The Future Challenges
Letâs look at each of the elements specifically to see how a customer-centric supply chain can be achieved: ⢠Strategy: from the top of the organisation a customer oriented strategy must be drawn and put to be communicated throughout the organisation. The strategy must include how the organisation should align its strategy with the suppliers and customers to have the visibility and responsiveness to the end-consumersâ demand.
⢠Structure: For the organisation, horizontal dynamic structure that aligned to products and market segment is more preferred that the vertical hierarchical reporting lines; for the supply chain, networked flexible structure with small span of vertical integration is more responsive to the customer demand. ⢠Systems: the procedures and daily activities must be in tune with market sentiment; customer complaints and request must be dealt
with by a fixed routine procedure systematically; a joint forecasting and new product introduction process should be established collaboratively across the supply chain. ⢠Shared value: customer service and customer value must be enshrined in the core organisational value; it should become the culture and second nature for people to act on anything relate to the customer and endconsumer at the highest priority. ⢠Style: the leadership style adopted must fit the culture of customer orientation and customer-centric. The leaders and management team should âwalk the talkâ and become the role model in caring about the customer.
⢠Staff: the employee and their capabilities are the assets of the organisation. People are the only active force in caring and serving the customer. The change of organisational performance is almost entirely dependent on the changes of peopleâs understanding, knowledge and attitude. ⢠Skills: the quality of the products, the level of customer satisfaction, rely on the skills of the workforce, which in turn determines the organisationâs and supply chainâs competences in delivering the products and services.
8.2 Managing Supply Networks
The second challenge is to take on the whole supply network and manage it as an integrated entity. Managers see the only legitimate platform for them to exercise control is their own organisation, beyond which is the supply chain they participated. This limited scope of business management is to be and has already been challenged. Companies will not stand alone in the competition. Like it or not the competition will only be waged with supply chain against supply chain. The survival of the supply chain is the survival of the organisations in it.
Download free eBooks at bookboon.com
107
Fundamentals of Supply Chain Management
The Future Challenges
Therefore the new competitive paradigm place the firm in the middle of an interdependent network â a confederation of mutually complementary competencies and capabilities â which competes as an integrated supply chain against other supply chains. To manage in such a radically revised competitive structure clearly requires different skills and competencies than those used in the traditional structure. To achieve future global market leadership in the networked competitive environment necessitates a network focused management model and the associated management processes. One of the key cognitive characteristics of any network is its configurative structure, which specifies how a supply chain is constructed in terms of its flow model. Such network structure dimension determines how big the supply base is; how wide the extent of vertical integration is; how much its level of outsourcing is; where the suppliers are located; how close the dyadic relationships are; what the channels of connection for the network are; and etc.. As it happens, globalisation has, amongst many other forces, propelled some unprecedented shifts in network structure and configuration. Evidences from numerous surveys and case studies show that more and more leading edge enterprises are outsourcing more strategically important functions and vertically disintegrating the supply chain to geographically, economically and culturally remote destinations.
Such a momentum has inevitably given rise to some new challenges in reshaping the network management. Business strategies formulation must be carried out collectively with the network members. A significantly higher level of joint strategic development is required in order for the network to be truly effective. Another challenge is for the networks to break free from the often adversarial nature of buyer-supplier relationships. There is now a growing realisation that co-operation between network partners usually leads to improved performance generally. The result of the improved performance needs to be shared between the members of the network to achieve whatâs called âwin-winâ. Developing the shared information system for the network management is another challenge. Forecasting information, capacity information, and production information can all be collectively managed to
reduce the inventory levels and achieve shorter lead-time and JIT delivery. Throughout the supply the material flows are gradually to be displaced by the information flow. Whilst the supply network becomes leaner in terms of less redundant materials in the process, the investment in the information systems and its management gets increasingly higher. Coordinating the IT system compatibility, software upgrading, maintenance and service could be resource hungry. However the gain in the much more coordinated operation and supply chain responsiveness is understood to be worth the cost. As supply network complexity and uncertainty becomes ever more persistent the challenges also ripple out to the supply chain risk management. This is particularly true when supply chains become more reliant on virtual networks. The emerging future model of risk management for supply chains cannot be a scheme of buying an insurance policy; nor would it be an experience of gambling. Companies that aspire for the supply chain leadership position in the future will be those who mitigate the risk by building various forms of reserves, including inventory, capacity, redundant suppliers, but in the meantime maintaining a competitive strength in business efficiency and responsiveness. Managers thus must keep a vigilant eye on the trade-off between the risk and the cost of building a reserve to mitigate it. With so many related risks and risk-mitigation approaches to consider, it is suggested that managers must do two things when they begin to construct a supply network risk management strategy. First, they must create a shared organisationwide understanding of supply-chain risk. Then they must determine how to adapt general risk-mitigation approaches to the circumstances of their particular company.
Download free eBooks at bookboon.com
108
Fundamentals of Supply Chain Management
The Future Challenges
8.3 Watch the Dynamics
The third challenge is how to survive the dynamics of the never ending supply chain evolution. The future of supply chain will face unprecedented dynamics in terms of structural dynamics, technological dynamics, and relationship dynamics, to say the least.
Structural dynamics
From a system dynamics point of view, the flow structure of a supply chain is a typical dynamic system with lows and stock; there are feedbacks and delays. From managerial experience perspective, it is even more so; there are fluctuations of demand, overproduction, high inventory, capacity miss-match, backlogs of unfulfilled orders, delayed delivery and so on. The trouble is that the supply structure is growingly more complex, and market volatility is set to increase too. There is little doubt the dynamic behaviour of a supply chain is only to be exacerbated. A number of factors are at play, which is continuously contributing to the increased structural dynamics. ⢠The first factor is that business around the world is becoming more specialised, and they become so rightly for their competitive advantages, utilisation of resources and returns on investment. This trend is leading to more inter-connections of the specialised operation in the supply chain networks. Specialisation gives rise to the need of coordination in between. Thus increase the complexity of the system and more triggers for dynamic changes.
⢠The geographical expansion of supply chains around world also exacerbates the dynamic behaviour, as the delays in logistics and visibilities are worsened. It has also brought in the unstable factors such as different legal and financial systems, cultural and religious conflicts, indigenous market related ethical issues. ⢠The rapid growing environmental concerns around world have already started to reshape the supply chains. Not only the resourcing strategies, but also the production and logistics processes have felt the significant impact. Carbon footprint has become the KPI for many supply chains across industries, which they never heard of in just few years back. Consequently, the structure of the supply chains will have to change. Technological dynamics
Innovation and technology advancement have been great news for the business and the consumers alike in most cases. But the changeover to new technologies can be a very painful process as it induces series of dynamic changes to the supply chains. All too often the disruptive technology advancement decease the existing operating model and invalidates the existing markets. The changing dynamics that have been enforced upon the supply chain can be observed from number of directions:
⢠Sudden change of competition landscape when the new technology advancement has helped the competitors to update their offering to the market.
Download free eBooks at bookboon.com
109
Fundamentals of Supply Chain Management
The Future Challenges
⢠The manufacture may be forced to switch the suppliers due to the desperate need of the new technology in the supply base in order to keep competitive.
⢠Sudden arise of the new investment requirement due to the pressure to upgrade the equipments and facilities to cater the new technology.
⢠Unfolding a significant skill gap in the workforce due to the unpreparedness of the technology. Relationship dynamics
Many people believe the operating core of supply chain management is that of relationships with the suppliers and buyers including the end consumers. Hence, the external business relationship management for a company has become the centre piece of todayâs and arguably the futureâs supply chain management. However the conceptual alignment of this concept in the academic as well as the practitionersâ circles has always been a quagmire, as there are many apparently conflicting approaches towards managing the relationships.
Please click the advert
Increase your impact with MSM Executive Education
For almost 60 years Maastricht School of Management has been enhancing the management capacity of professionals and organizations around the world through state-of-the-art management education. Our broad range of Open Enrollment Executive Programs offers you a unique interactive, stimulating and multicultural learning experience.
Be prepared for tomorrowâs management challenges and apply today. For more information, visit www.msm.nl or contact us at +31 43 38 70 808 or via [email protected]
the globally networked management school
For more information, visit www.msm.nl or contact us at +31 43 38 70 808 or via [email protected]
Download free eBooks at bookboon.com
18-08-11 15:13
Executive Education-170×115-B2.indd 1
110
Fundamentals of Supply Chain Management
The Future Challenges
It is now emerging, that no single existing relationship model so far can possibly serve all business needs because of the underlying dynamism. There are basically two key dynamisms in the relationship management, one is the portfolio dynamism and the other is longitudinal dynamism. The portfolio dynamism addresses a portfolio different relationship approaches that fit to a corresponding portfolio of business models. Thus, in often times, business
will need to harness with a number of different supply chain relationships to different suppliers based on product categories, market segmentations, development strategies, and financial circumstances and so on. The longitudinal dynamism addresses the changing relationship posture along the time continuum. In this way the relationship management becomes a powerful instrument to achieve the supply chain responsiveness and supply chain agility. It is anticipated that the future supply relationship management will hinge on a combined approach that addresses both the portfolio and longitudinal dynamisms. How to survive the supply chain dynamics?
The Triple-A supply chain model proposed by Professor Hau Lee (2007) from Stanford University is a useful blueprint to survive the supply chain dynamics.
⢠The triple-A stands for Agility, Adaptability and Alignment. A supply chain must be agile enough in order to respond quickly to the dynamics of demand fluctuations and sudden changes of supply. The agility is a supply chain capability that handles the unexpected external disruptions smoothly and cost effectively. It enables the supply chain to survive the impact of the external dynamics and be able to recover from any initial shocks.
⢠Adaptability differs from the agility in that it deals with more long-term and fundamental changes in the overall external environment, which is often irreversible. Adaptability calls for organisation and its supply chain to embark on major strategic changes in technology, market positioning, radical skill upgrading and competence shift. It helps the supply chain to survive the long waves of external dynamics. ⢠Alignment is a supply chain capability that coordinates and balances the interests of all members. It addresses the supply chainâs internal dynamics and ensures the supply chain to remain as a stable and cohesive whole. It also means to align all the complimentary resources and optimise the operational effectiveness and relationship to deliver the competitive advantage.
Download free eBooks at bookboon.com
111
Fundamentals of Supply Chain Management
References
9 References
Christopher, M 2005, Logistics and supply chain management â creating value-adding networks, 3dt Ed. FT Prentice Hall, London.
Fisher, M 1997, âWhat is the right supply chain for your product?â, Harvard Business Review, March/April. Frohlich, MT and Westbrook, R 2001, âArcs of integration: an international study of supply chain strategiesâ, Journal of Operations Management, Vol. 19, pp. 185-200.
Gattorna, J 2006, Living supply chains â how to mobilize the enterprise around delivering what your customers want, FT Prentice Hall, London.
Harrison, A &Van Hoek, R 2011, Logistics management and strategy â competing through the supply chain, 4th Ed. FT Prentice Hall, London.
Harrison, A, Christopher, M & Van Hoek, R 1999, âCreating the agile supply chainâ, School of Management Working Paper, Cranfield University, Cranfield.
Hines, P & Taylor, D 2000, Going lean. Lean Enterprise Research Centre, Cardiff Business School, Cardiff, UK. Kim, WC, Mauborgne R. 2005, Blue Ocean Strategy. Harvard Business School Press: Boston. Lamming, R 1993, Beyond Partnership, Hemel Hempstead: Prentice Hall. Lee, HL 2006, âThe triple-A supply chainâ, Harvard business review on supply chain management, page 87-116. Harvard Business School Press, New York.
Lu, D 2011, In Pursuit of World Class Excellence, Ventus Publishing Aps, Frederiksberg, Denmark. Slack, N Johnston, S 2006, Operations Management, 5th Edition, Prentice Hall, London
112