Safety Precaution About Bench Fitting Shop
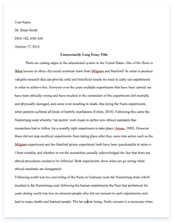
- Pages: 25
- Word count: 6084
- Category: Safety
A limited time offer! Get a custom sample essay written according to your requirements urgent 3h delivery guaranteed
Order NowBy the end of this unit each apprentice will be able to:
• State the function of common workshop tools and equipment and the safety precautions to be observed when using this equipment
• Measure and mark out metal work exercises
• Produce metal work exercises by cutting, drilling, tapping and screw threading
• Drill out and replace pop rivets as part of a metal work exercise
• Re-tap damaged threads on a vehicle component i.e. studs or stud holes
2.0 Introduction
In engineering you are usually concerned with a number of parts or components fitting together to make an assembly, so you must control the sizes of the parts to make sure they assemble correctly and will function as the designer intended. Even if you are only purchasing a bar stock you need to know that any unmachined surfaces are suitable sized for your application. In all theses cases the control of size and the assembly of components can be done with the help of a limits and fits standard of some kind.
What is a fit in Engineering Terms?
Imagine that you have drilled and reamed a hole 20mm in diameter in a piece of metal 14mm thick .
You are now going to machine a diameter on the end of a 30mm bar. If the machined diameter has to pass easily through the hole you could make it, say, 16mm.
There would be a gap, or technically clearance, between the diameter of the hole and the shaft. Alternatively you might want the shaft to be a tight fit in the hole and machine the shaft slightly larger than the hole –the method of determining the actual size will be discussed later! In this case you would need to force the shaft into the hole. The hole and shaft diameters interfere with each other. Notice that it was suggested carrying the fit by varying the size of the shaft. Because the hole is the fixed size this system is based on the hole and is known as a hole basis. The hole in our example could just as easily be a slot, groove, gap or similar internal feature whilst the shaft could be a tongue, tenon or similar external feature.
You could, however, decide on a shaft size and vary the hole sizes to give various fits. This would be known as a shaft basis. A particular base is a shaft having the same basic size throughout, which is designed to carry various parts required to assemble a shaft with different fits. Such
variations in fit required by bearings, couplings, collars sliding members or other parts would involve expensive machining of the shaft in order to vary its diameter and to adjust the bore of each part to give the required fit.
3.0 S I System
A set of units known as the metric system is used internationally by most nations. It was introduced by the French National Assembly late in the sixteenth century and was adopted by Ireland in the early 1970s. One of the main characteristics of the system is its decimal nature; therefore, the conversion between smaller and larger units is made by moving the decimal point to the left of right. The SI system of units (Systeme International d’Unites), developed from the metric system, and has been defined and recommended as the system of choice for scientific use worldwide. The primary units in the SI system which are of interest to the motor mechanic are as follows: QUANTITYUNITSYMBOL
Length Meterm
MassKilogramkg
Capacity Litrel
TemperatureDegree CelsiusoC
TemperatureDegree KelvinK
TimeSeconds
ForceNewtonN
Heat Joulej
Power Wattw
4.0 Derived Units
Derived units are those which can be expressed in terms of the primary units so as to provide more units to work with. There is a primary unit for length, but not for area or volume, however, it is possible to derive units for area and volume from the primary units. Any area is measured as the products of two lengths. It can be said that an area has the “dimensions” of (length) x (breadth) and so is measured in squared units. Area = length x breadth and if the length of each of these is given in meters, then, area = m x m = m2 so the derived unit for area is the square meter which is written m2. Another derived unit is that of volume which is expressed in cubic meters written as m3Volume = length x breadth x height; m x m x m = m3 so the derived unit for volume is the cubic meter which is written m3. Some of the more commonly used derived units are given in the table below. QUANTITYUNITSYMBOL
AreaSquare Meterm2
Volume Cubic Meterm3
Pressure Newton perN/m2
Square Meter
5.0 Basic Drawing Theory
What follows are some background notes and basic instructions on creating appropriate drawings, for different situations. Read the notes and use these to help complete the activities later in the element.
Graphical Methods
• Freehand sketches –these are usually straight line pencil drawings.
• Drawing using instruments and stencils.
• Airbrush techniques,
• Computer aided design – the use of graphics programs and CAD (Computer Aided Design).
Block Diagrams and Flow Diagrams
Check BS 5070.
Block diagrams show schemes for completing tasks and flow diagrams might show the direction hydraulic fluid runs in a brake system, or the direction of coolant in a an engine.
Schematic Diagrams
These show the layout of the circuit using approved symbols.
Circuit Diagrams
This includes circuit diagrams using approved symbols, but also may show diagrams with full size components. A printed circuit board may be drawn full size or even larger than full size with the actual components in place. The design of computer parts or printed circuit boards require large scale drawings as the final components are very small and 1:1 scale drawings would be inadequate, or even impossible to draw. Circuit diagrams are drawn for pneumatic, hydraulic, electronic and electrical systems.
Detailed Drawings
Fully dimensioned drawings, sometimes to a very large scale, They may include tolerances and machining limits.
Assembly Drawings
This includes orthographic first and third angle, isometric and oblique line drawings. Perspective views of a complete assembly.
6.0 Orthographic Drawing
There are two types of orthographic drawing; these are called first angle projection and third angle projection. Both drawing types show three views of an object: a plan
a side or end view
and a front view
The layout of the views is difference in first and third angle projections.
When we look at an object we see in three dimensions, we see light and shade, colors and shadows. Making an orthographic drawing of an object means taking the outlines of an object. The simplest objects to consider are a cube and a ball or sphere.
When drawn, because this is a cube and all the sides are the same, the front view, end view, and plan will all look like this:
The front view, end view and plane of a ball or sphere will look like a circle. Check this for yourself! In first angle projection the layout is:
In third angle projection the layout is:
The first angle projection was most common in Britain. The third angle projection is more common in Europe and the USA, this has now been adopted in the UK.
Oblique Views
These drawings show one side of an object in its true shape. Other areas are drawn using lines at 45 o to the lines of the side shown in true shape, the cube at the beginning of the section shows an oblique type drawing. The lines which leave the side shown in true shape or scale should be half their true length. Advantages: Lines on the true shape can be measured and drawn to scale. Disadvantages: Does not give as realistic or comprehensive idea of the item as other drawing methods, for example perspective views (see later)
Paper with 45 o angles lines is available to put under you sketching paper as a guideline.
Isometric Projection
Whereas oblique drawing shows one face or one side in true scale, isometric begins at one point. Vertical lines remain vertical, but other lines are drawn at 30 o to the horizontal.
All the lengths remain to scale and a cube shape will become: The lines should all be to scale and the angles 30o
The advantage of this method is that the lines are to scale, but the disadvantage is the object may look ‘larger than real size’ to the eye. Paper with a grid of 30 o angle lines is available to draw isometric projects.
Perspective Drawings
These are views of an object or objects from a vanishing point. Sometimes two vanishing points are used, the drawings are called two point perspective drawings. The vertical line nearest the viewer is the only line drawn to scale. These drawings are most useful when working out how parts are assembled… A one point perspective of a box:
7.0 Scale
It is not always possible to draw objects to their actual size. You can draw around your hand on an A4 piece of paper and this will be life size and the scale 1:1. there an item is too large to draw in real size you can reduce the size, a scale of 1:2 will produce a half real size drawing of the object, a scale of 1:10 will mean the drawing is one tenth the size of the real item. Sometimes it is necessary to enlarge items, for example circuit boards may be drawn at a scale larger than real size. The scale 2:1 Means the drawing will be twice the size of the original item. Below are some examples of different scales.
Scale rules are special rulers which have a selection of different scales. A reading of 1 on the 1:10 scale ruler will have been adjusted to give one tenth of the original value, 1 centimeter on the object will become 1 millimeter on the drawings
Dimensioning Drawings
Drawings are dimensioned using fine lines with neat arrows on each end of the line
Dimensions are written above the line or to the left of the line.
Small lines are used as projection lines and leave the drawing with a gap of about 2mm between the drawing and the line. Where circular items are dimensioned diameter is given the symbol The radius of an item is given the symbol R. These symbols are paced in front of the dimensions. Centre lines of objects are marked by dotted lines consisting of long dashes and short dashes.
An example of a rivet, end view:
Hidden detail is a term used in engineering drawings to indicate the lines of something behind what the eye sees. Takes two boxes balanced one on the other –from the side the view may be. From above the view will be a solid outline of the box on top. The box is below is not visible and should be represented by a short fine dashed line. The hidden detail in the above drawing has been show by a grey line.
8.0 Sections
Many objects cannot be fully represented by third angle projection drawing without the addition of one or more sections to the drawing. If you draw a children’s plastic ball, one which consists of a layer of plastic with air inside, the end view, plane and front view are all circles.
On the right is an n exaggerated view of what a section through the ball might look like. The engineer has shaded the material to show this view is a section. The arrows indicate where the section has been taken and which direction the section looks. It is useful to think of a section as what you will see if you cut across the line the arrows form. On small items all dimension will be given millimetres, on larger items the dimension may be in metres. The actual units will be stated in the drawing key, or information box, normally found at the bottom of the drawing, whenever you look at any drawing it is very important to read the key first, before you being to work out what the drawing represents.
9.0 Circuit Diagrams
These represent electrical or electronic components. The symbols for these components are included in many up to date books and accepted British or European Standard documents. Some companies and businesses use their own set of symbols. If this is the case then they will supple these to manufacturers, when they supply their drawings. Circuit diagrams often begin as sketches. The formal circuit diagram, also known as a schematic diagram. This circuit diagram shows straight lines and accepted symbols. There are no details to show where the components are found in the torch. No dimensions are given, so you do not know how long the electrical leads need to be. A sketch of a section through a torch or plan is needed to show where the components are located and distances, sometimes manufacturers supply photographs, for example where manuals are written for maintenance.
10.0 Block Diagrams and Flow Diagrams
These diagrams use rectangular or square boxes to represent processes in a manufacturing system. No decisions are involved. For example: producing full boxes of cereal.
This is a simplified version of a very complex factory process, three items are made and assembled.
Flow Diagrams
These show the direction fluids move, for example water in a central heating system, or compressed air lines in factories, hydraulic fluids in brakes. Simple sketches are used with arrows to show the direction of fluid flow. They are important where valves are installed in equipment as the diagrams will show where the valves should be place and when valves are designed to prevent fluids flowing backwards, the direction they should be placed.
11.0 Hydraulics and Pneumatics
These systems use fluids (either liquids or gases) to transmit forces from one place to another. Pneumatic systems use compressed air and the example most easily accessible to you is the equipment at garages used to fill tyres with air. Compressed air is also used in industry to operate machinery. Compressed air used to operate machinery is particularly useful in environments where there is a danger that electrical sparks might cause explosions or fires, for example mines. In power hydraulic systems the fluid is usually pressured oil, for example mechanical diggers. Other hydraulic systems include central heating, water supply and pumps. The systems use drawings similar to circuit diagrams in electrical and electronic diagrams, but with a different set of symbols used to represent valves, cylinders and other components. For example a directional control valve (this will stop the fluid flowing backwards) is represented by the following symbol
A push button switch may be represented by the following symbol
Drawings for these systems have to be logical, some understanding of OR AND GATES may be necessary to construct and check drawings for a pneumatic and hydraulic system.
12.0 Questions on the Background Notes
1.Explain the difference between a block diagram and a flow diagram
2.Which types of engineering information can be represented by circuit diagrams?
4.What information does drawing quantitative information give?
5.Draw the layout of the first angle projection and third angle projection.
6.What angle does: aisometric projection use?
ban oblique view use?
7. Which of the two drawing types named in question 6 can be used to scale dimensions from?
8.Complete the following box showing drawing sizes and their different scales.
9.On which sides of the dimension lines are the actual dimensions placed?
10.aWhat does R mean when place in front of a dimension?
bwhat symbol is used to represent diameter?
11.What type of line represents:
Ahidden detail?
Ba centre line?
Draw the correct lines next to the questions.
12. How would you know that part of a drawing had been drawing in section?
13.0 Screw Thread Cutting
Aims and Objectives
Learning Outcome:
By the end of this unit each apprentice will be able to:
• Describe the hazards and most appropriate safety procedures required when drilling mild steel. • Drill holes in mild steel plate. Cut internal threads in the holes to accommodate manufactured bolts of various sizes. • Produce external threads cut on round bar to accommodate manufactured nuts of various sizes. • Repair internal and external threads
• Removal of broken or damaged studs
14.0 Cutting and Repairing Threads
Using a thread pitch gauge
1. Preparation and safety
Objective
• Identify the common types, length, diameter, grade, and thread pitch of threaded fasteners.
Safety check
• Never use a bolt that has been over-tightened. Its tensile strength is very low and it could break. • Use the correct tool to tighten or loosen bolts, otherwise you could break them. • Make sure that you understand and observe all legislative and personal safety procedures when carrying out the following tasks. If you are unsure of what these are, ask your supervisor.
Points to note
• Fasteners are used to secure components or pieces of components together. There are two main types of fasteners: inch and metric. They are not compatible.
• Bolts are identified in four ways:
o Length
o Diameter
o Thread Pitch
o Tensile Strength
• A bolt’s length is the distance from under the head of the bolt to the far end of the thread. Inch bolts can come in sizes such as 1 1⁄4″, 3 1⁄2″, etc. Metric bolt sizes might be 25mm, 40mm, etc.
• The bolt diameter is the thickness of the bolt shank. This will be 1⁄4″ or 1⁄2″, etc if it is an inch bolt, or 6mm, 8mm, 10mm, etc if it is a metric bolt.
• Fine threads can achieve a greater tightening force than coarse threads.
• Coarse threads are used in softer materials because they have a greater grip on the material.
• The measurement of thread pitch for UNC and UNF bolts is described in the number of threads-per-inch (TPI).
• A UNF bolt may measure 1⁄2″ x 3″ x 20. That is, the bolt is 3″ long, has a shank diameter of 1⁄2″ and the threaded area has 20 threads in every inch of thread. A UNC bolt that measures 1⁄2″ x 3″ x 13 will have the same dimensions but have only 13 threads for every inch of thread.
• The length and shank diameter of metric bolts is measured in the same way as UNF and UNC bolts but the measurements are in millimeters, rather than in inches or fractions of an inch. The difference lies in how the thread pitch is measured. Metric bolts define their pitch by the distance between each thread. There are still fine and coarse threads but this time the bolt dimension may be 6mm x 40mm x 1.0 or 1.25 in the case of a fine thread. A coarse threaded bolt of a similar size will have the dimensions of 6mm x 40mm x 1.75 or 2.0.
• The suitability of a bolt for an application is determined by its tensile strength and its yield strength. The tensile strength is defined as the maximum stretching stress a bolt can withstand without breaking. The yield strength is the maximum stress a bolt can withstand and still return to its original form.
• There are two standards of bolt grading in use. The Society of Automotive Engineers (SAE) and the American National Standards Institute (ANSI) apply the ANSI standard. This grading applies to the strength of the bolt. The second is the International Standards Organization (ISO) grading for tensile strength and yield strength of the bolt.
• A bolt graded by the ANSI standard is identified by the number of lines arranged around the head of the bolt. The minimum value of tensile strength is defined as 2. A bolt of this value has no lines on it’s on its head.
o 0 lines = Grade 2 tensile strength
o 3 lines = Grade 5
o 5 lines = Grade 7
o 6 lines = Grade 8
• A high grade-value = a high tensile value.
• The ISO standard uses two numbers on the head of the bolt. The first number indicates the tensile strength; the second number signifies the yield strength.
• If a bolt is marked 8.8, it has a tensile strength of 800 MegaPascals (MPa) and a yield strength value of 640 MPa, 80% of its tensile strength. A marking of 10.9 indicates a tensile value of 1000 MPa with a yield strength of 900 MPa, 90% of its tensile strength.
o 4 = 400 MPa
o 5 = 500 MPa
o 8 = 800 MPa
o 10 = 1000 MPa
o .5 = 50%
o .6 = 60%
o .7 = 70%, etc.
• Always use a bolt suitable for the application. If a bolt with too high tensile strength is used and not tightened to its designed value, it may fail. That is because high tensile bolts have less resistance to fatigue than bolts with a lower tensile value.
2: Step-by-step instruction
1. Choose a pitch gauge: To determine the thread pitch of a particular fastener, you need to use a thread pitch gauge.
2. Check gauge markings: Open out the pitch gauge set and examine the markings on the toothed blades. The markings will be either in inch units or in metric units. The numbers stamped on the toothed blade of an inch gauge set indicate the number of threads per inch of thread length. For example: 16 threads to the inch. Look at the numbers on the blade of a Metric pitch gauge set. The numbers indicate the width between each thread in millimeters. For example: a thread pitch of 1.5 millimeters.
3. Measure a known size: Choose a fastener of a size you know. Say, 3/8inch U-N-C bolt. Using your inch gauge set, select each blade and hold the toothed edge against the thread of the bolt. Continue trying the blades until you find one that matches exactly the thread on your bolt. Check the number on the blade; it should read 16. That is, 16 threads per inch.
4. Measure an unknown size: Now choose a fastener whose size you do not know. If it is a metric bolt, select the metric thread pitch gauge. Repeat the procedure with the blades against the thread of the bolt, until you find a perfect match. Check the number on the blade; it will tell you the thread pitch of this fastener in millimeters.
5. Correctly store gauge: When you have finished, be sure to fold all of the blades back into their casing before putting the gauge set away. This is to protect the blade teeth from damage.
15.0 Repairing an external thread
1. Preparation and safety
Objective
• Use a die to repair damaged threads in an automotive component.
Safety check
• Use safety eyewear when using cutting equipment.
• Do not run your fingers down a newly cut thread. It has many sharp edges that will cut your fingers and small metal particles will start an infection in the cut.
• Make sure that you understand and observe all legislative and personal safety procedures when carrying out the following tasks. If you are unsure of what these are, ask your supervisor.
Points to note
• A die is a metalworking tool used to repair or cut new outside threads on fasteners.
• The die is installed in a tool called a “die stock”. It gives the leverage to turn the die over the new thread. The diestock locates the die in place using thumbscrews that match indentations in the outer edge of the die.
• The die has a top and a bottom. The bottom has tapered threads to guide the thread into the die.
• Use a thread cutting compound with the die. It will keep the cutting edge of the die sharp, allowing it to be used many times.
• If cutting a new thread on a bolt or stud, make sure the top of the shank is square. This will help lead the die teeth squarely onto the shank.
• Make sure the die is square to the shaft of the stud or bolt at the start of the thread cutting process.
• When cutting or repairing a thread, once the die has started to cut, turn the die about a quarter of a turn then back off. Cut another quarter of the thread and back off again. Continue until the thread has been cut. This action clears the cutting teeth of any scrap and gives a better finish.
• Once the thread has been cut and the die removed, clean the new thread with a wire brush. This will remove any sharp edges and any left over scrap from the new thread.
• Do not use a wrench to tighten the die locating thumbscrews.
16.0 Repairing an internal thread
1. Preparation and safety
Objective
• Use a tap to repair damaged threads in an automotive component.
Safety check
• Use safety eyewear when using cutting equipment.
• The teeth of a tap are sharp. Be careful when handling the tap so that you do not injure yourself.
• Make sure that you understand and observe all legislative and personal safety procedures when carrying out the following tasks. If you are unsure of what these are, ask your supervisor.
Points to note
• There are three different types of thread taps: starting, intermediate and finishing.
• A starting tap has a well tapered end, which is why it is sometimes called a “taper” tap. This allows the tap gradually to cut deeper threads as it passes through the job. It can be used to cut a thread in work that has a thin enough section to allow the tap to pass through it. It is also used to perform the first cut in a blind hole.
• An intermediate or second tap is used for the second cut in a blind hole. It has fewer tapers than a tapered tap, which allows the threads at the bottom of the hole to be more complete.
• A finishing, bottoming or plug tap is designed to cut the final thread into a blind hole. It has almost no taper, so the threads it cuts extend to the bottom of the hole.
• Use a thread cutting compound with the thread tap. It will keep the cutting edge of the tap sharp, allowing it to be used many times.
• When cutting a new thread into a hole, make sure the tap is square to the work piece. This will help lead the teeth to cut squarely onto the shank.
• When cutting or repairing a thread, once the tap has started to cut, turn it about a quarter of a turn then back off, then cut another quarter thread and back off again. Continue until the thread has been cut. This action clears the cutting teeth of any scrap and gives a better finish.
• Once the thread has been cut and the tap removed, clean the new thread with an air duster.
• Do not use an impact wrench on the tap.
• Practice on a scrap component before attempting a real one.
Part 2: Step-by-step instruction
1. Choose the correct tap: Choose the correct size and type of tap you need to repair the thread, either in Metric or Inch.
2. Determine the thread size: Determine the thread size of the screw that should fit the damaged hole. Use a thread pitch gauge to confirm the size.
3. Select corresponding tap: Select the corresponding tap size and type: either a taper, intermediate or bottoming tap.
4. Fit the tap to the tap wrench: Select either a T-handle wrench or a hand-held tap wrench, and fit the square end of the tap shank into the chuck on the wrench then tighten the chuck.
5. Apply thread cutting compound: Apply a small amount of thread cutting compound to the cutting teeth of the tap. Position the tap in the damaged hole, making sure that it’s square to the hole and not at an angle.
6. Rotate the tap clockwise: Slowly and carefully turn the tap wrench in a clockwise direction into the damaged hole. You will feel the tap removing the metal from inside the hole, making the thread. Continue to turn the tap until it has bottomed in the hole or has passed all the way through.
7. Remove the tap counterclockwise: To remove the tap, turn the wrench counter-clockwise up and out of the hole. Clean any filings or particles from the cutting threads and the flute of the tap before you remove it from the wrench.
8. Clean out the hole and test it: Clean out any filings or particles from the hole you have just repaired. You can then test the repair by using the correct size screw or bolt and tightening it by hand. Sometimes you’ll find the damage was so severe that the tap wrench procedure fails to fix the problem. If this happens refer the job to your superviso
17.0 Remove and Replace a Stud
1. Preparation and safety
Objective
• Remove and replace a stud with a jam and drive nut or a stud remover.
Safety check
• Do not apply too much force to old and corroded studs. They may break if too much force is applied to them.
• Make sure that you understand and observe all legislative and personal safety procedures when carrying out the following tasks. If you are unsure of what these are, ask your supervisor.
Points to note
• Studs can be removed and refitted using two different methods:
o Jam and drive nut
o Stud remover
• The jam and drive nut method is used when the stud is re-used because it does not damage the stud.
• Stud removers are used to remove damaged studs when jam and drive nuts cannot perform the task.
• The most common type of stud remover consists of a frame with two holes and a knurled offset movable set of jaws.
• The holes are two different sizes. When you slide the stud remover over the stud, select the hole that allows the jaw to have the best purchase.
• Measure the exposed length of the existing stud before removal.
• After the stud has been removed, compare it to the new one. They should be the same thread and pitch.
• When fitting the new stud, apply the correct thread coating compound. It may be thread locking compound or an anti-rusting agent.
2: Step-by-step instruction
1. Use penetrating fluid: If the stud is rusted in place, soak the base of the stud threads with penetrating fluid to remove the corrosion and make it easier to take out. If possible, let the penetrating fluid soak in overnight.
2. Measure the old stud: Before working on the old stud, measure its exposed portion to verify the new stud is the same size. Note the measurement.
3. Install the ‘drive’ nut: Find two nuts with the same size and thread as the old stud, and thread one of these all the way down to the bottom of the stud. This will be the ‘drive’ nut.
4. Install the ‘jam’ nut: Thread the second nut all the way down until it sits on top of the drive nut. This second nut will be the ‘jam’ nut.
5. Tighten the ‘jam’ nut: Secure an open-end wrench to the bottom “drive” nut and hold it in position. Then tighten the “jam” nut against the “drive nut” with a box or open-end wrench. The jam nut will now prevent the drive nut from moving.
6. Turn the ‘drive’ nut: Use the open-end wrench to turn the bottom drive nut counter-clockwise. The drive nut applies the turning force to the stud and forces it to unscrew.
7. Remove the stud: Continue to rotate the drive nut until the stud comes out.
8. Attach the stud remover: If jam and drive nuts don’t budge the stud, you can use a stud remover. Slide the stud remover over the old stud and seat it flush with the surface of the component. Turn the jaws in a counter clockwise direction until the stud is held tight.
9. Turn counterclockwise: Fit a wrench onto the stud remover and turn the wrench in a counter-clockwise direction. The stud remover will grip the stud and turn it. Continue to rotate the stud, using the wrench, until the stud comes out.
10. Inspect for damage: Once you’ve removed the old stud, inspect the internal thread of the hole for any damage
18.0 Using a screw extractor
1. Preparation and safety
Objective
• Use a screw extractor to remove a broken stud or screw.
Safety check
• Always wear eye protection when drilling and removing a broken stud or bolt.
• Make sure that you understand and observe all legislative and personal safety procedures when carrying out the following tasks. If you are unsure of what these are, ask your supervisor.
Points to note
• Fasteners can fail for many reasons: over-tightening, over-stressing, fatigue and old age are all possible causes.
• If the fastener is broken near the surface, a screw extractor will be needed to remove it.
• Screw extractors are available in two common types: One has reverse threads and the other has straight flutes.
• The fastener needs to be drilled before the screw extractor can be inserted.
• Always drill to the size recommended by the screw extractor instructions. If you are unsure of the correct size, ask your supervisor.
• If a fastener is rusted into place, use a penetrating fluid on the threads and allow it time to work before attempting to loosen it.
• Sometimes the fastener can be made easier to remove by the application of heat to the surrounding area. Ask your supervisor to demonstrate this to you.
• When fitting a replacement stud, apply the recommended coating to the thread. It may be thread locking or anti-seize compound. Follow the manufacturer’s instructions on the application and use of the compound.
• Use a jam and drive nut to fit the replacement stud.
2: Step-by-step instruction
1. Select the correct tools for the job: Open your screw extractor set and study the instructions, which should be enclosed. Identify and select the correct size drill and screw extractor for the job.
2. Mark the exact center: With a center punch, mark the exact center of the broken screw to get the power drill started.
3. Drill a hole: Drill a hole through the center of the bolt. Drill only to the depth specified in your screw extractor instructions.
4. Select the correct size: Make sure you use the correct screw extractor – that is, the one that matches the drill bit you used.
5. Turn extractor counterclockwise: Because the screw extractor has reverse threads, you will need to remember to turn it counter-clockwise.
6. Use a tap wrench: Use a tap wrench and turn the screw extractor into the hole. The reverse threads will force the extractor into the hole until the broken bolt or stud is forced to turn. Continue turning until the stud is removed.